Carbide rectangular blanks and squares are versatile workpiece materials used for machining complex parts and tooling. This guide provides a comprehensive look at carbide blank properties, grades, sizes, tolerances, applications, suppliers, and advantages/disadvantages.
Overview of Carbide Rectangular Blanks/Squares
- Carbide blank rectangles and squares are unmachined carbide workpieces
- Provide starting shape for machining complex carbide parts
- Available in various carbide grades and sizes
- Tighter tolerances than cast or forged stock
- Used to machine dies, cutting tool blanks, wear parts, components
- Allows optimized carbide grain orientation for application
Carbide blanks enable machining intricate parts from precise carbide shapes.
Grades of Carbide Blanks
Carbide blanks are available in these common grades:
Carbide Blank Grades
Grade | Description | Main Uses |
---|---|---|
C2/C3 | Straight tungsten carbide | General purpose machining, forming/punching |
C5 | Cobalt-enriched carbide | Wear parts, cutting tools |
C6 | Fine grain carbide | Cutting tools, drawing dies |
C10 | High cobalt carbide | Severe wear parts |
C12 | Nano-grain carbide | Precision cutting tools |
The grade is selected based on required hardness, toughness, and wear needs.
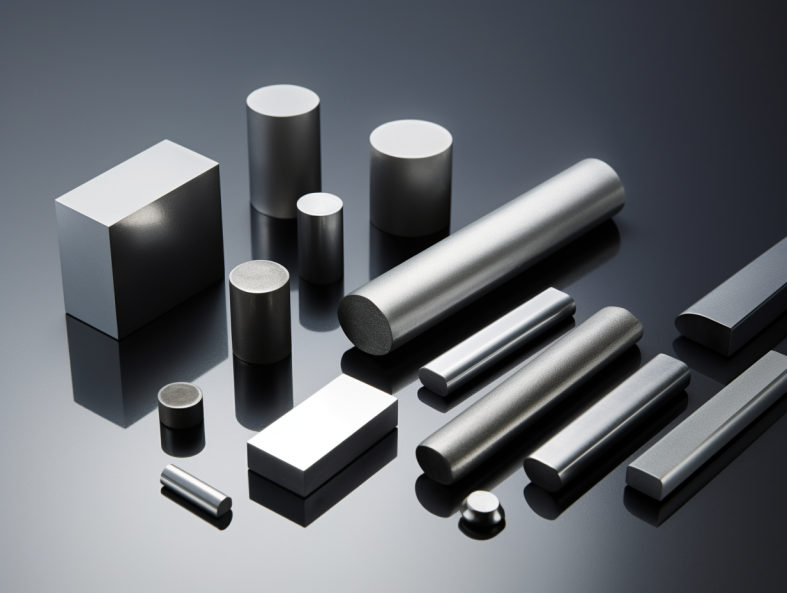
Blank Sizes and Tolerances
Blanks are produced in standardized sizes with tight tolerances:
Blank Sizes
- Thickness: 0.5″ to 4″ typically
- Width: 0.5″ to 8″ typically
- Length: 0.5″ to 16″ typically
- Custom lengths/widths possible
Tolerances
- Thickness tolerance: +/- 0.001″ to 0.005″
- Width/Length tolerance: +/- 0.001″ to 0.010″
- Squareness tolerance: 0.001″ to 0.002″ per inch
- Custom tolerances available
Precise sizing allows optimizing raw material usage in machining.
Applications of Carbide Blanks
- Cutting tool blanks – drills, end mills, reamers, burrs
- Injection molding components – cores, cavities, components
- Metal forming/punching dies – draw, blanking, extrusion dies
- Wear parts – nozzles, pump/valve components, plungers
- Precision parts – gears, cams, fixtures, spacers
Carbide blanks enable optimized grain alignment for the application.
Suppliers and Pricing
Leading carbide blank manufacturers include:
Carbide Blank Suppliers
Supplier | Description |
---|---|
Kennametal | Global carbide supplier. Grades include C2, C5, C6. |
Mitsubishi Materials | Broad carbide blanks line. Grades from C2 to C12. |
Ceratizit | C2 through C10 and nano-grain grades. |
Tunco Manufacturing | Wide range of common to custom blank sizes. |
Midwest Carbide | Specializes in smaller quantity orders. |
Pricing
Price varies based on blank grade, size, tolerances and quantity:
- C2 blanks: $8 – $12 per inch3
- C5 blanks: $10 – $15 per inch3
- C10/C12 blanks: $15 – $30 per inch3
- Tighter tolerances command premium pricing
Contact suppliers directly for volume discounts.
Pros and Cons of Carbide Blanks
Advantages | Disadvantages |
---|---|
Tighter tolerances than cast/forged stock | Higher cost than carbide plate/bar |
Optimized carbide grain alignment | Limited sizes may increase waste |
Uniform properties and workability | Higher machining time than standard shapes |
Reduces machining scrap and steps | Longer lead times for custom sizes |
Wide range of grades and sizes | Difficult to machine complex internal features |
Carbide blanks provide precision starting material despite some limitations.
Carbide Blanks vs. Plate and Bar
Parameter | Carbide Blanks | Carbide Plate/Bar |
---|---|---|
Tolerances | Very tight – 0.001-0.005″ | Wider tolerances – 0.010-0.020″ |
Price | Higher per in3 | Lower per in3 due to shape |
Lead time | Longer for custom sizes | Shorter for standard sizes |
Grain structure | Can align to forces | Random orientation |
Machining | Requires finishing all surfaces | Half or more surfaces finished |
Scrap rate | Lower scrap potential | Higher scrap rates |
Carbide blanks offer precision but at higher raw material cost.
FAQ
What are carbide blanks used for?
Carbide blanks provide precision starting material for machining cutting tools, dies, molds, wear parts that require optimized carbide grain alignment.
What grade of carbide is best for cutting tools?
Fine grain grades like C6 and nano-grain grades like C12 offer the best combination of hardness, strength and edge sharpness for cutting tools.
What tolerance can carbide blanks be manufactured to?
Standard carbide blank tolerances are +/- 0.001″ to 0.005″. Precision tolerances down to +/- 0.0005″ are possible for critical applications.
How are carbide blanks made?
Carbide blanks are produced via powder metallurgy methods. Carbide powder is pressed and sintered into net shape or near-net shape blanks.
What is the difference between carbide plate and blanks?
Carbide plate starts as cast plate stock sliced to size. Blanks are pressed/sintered to finished blank dimensions. Blanks offer tighter tolerances and aligned grain.
Carbide rectangular blanks provide a precision foundation for machined carbide components.
Conclusion
Carbide rectangular blanks offer an advantageous starting point for machining critical carbide parts and tooling. Tight dimensional tolerances and optimized carbide grain alignment reduce scrap and improve performance. Major global suppliers provide standard and custom blank sizes in grades engineered for wear resistance, toughness, and hardness. While costlier than plate or bar stock, carbide blanks allow optimizing raw material usage and properties. Their precision enables lighter and stronger designs across industries like aerospace, automotive, and general engineering. Carbide blanks will continue seeing strong demand as technology pushes boundaries further.