Carbide inserts are the unsung heroes of precision machining, enabling manufacturers to create high-quality parts across industries. Whether you’re a machinist, engineer, or someone curious about metal cutting tools, this guide will demystify carbide inserts for you. Let’s explore their composition, types, properties, applications, and much more in a highly detailed, engaging, and conversational manner.
What Are Carbide Inserts?
Carbide inserts are small, precision-crafted tools used in machining operations to cut, shape, and refine materials. These inserts, typically made from tungsten carbide powder, deliver durability and efficiency when machining hard materials like steel, cast iron, and alloys. Think of them as the sharp teeth on the edge of a powerful tool, designed to stay sharp under immense pressure.
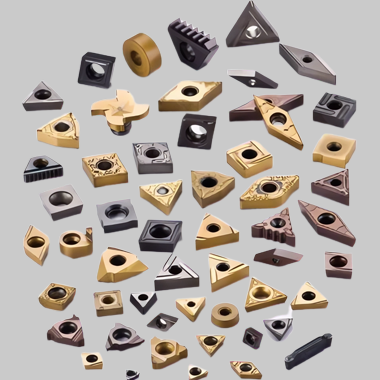
Types of Carbide Inserts and Their Uses
Carbide inserts come in different shapes, grades, and coatings to cater to specific machining needs. Below is a table showcasing the types of carbide inserts and their typical applications.
Type | Description | Applications |
---|---|---|
Turning Inserts | Designed for precision in lathe operations. Often triangular, square, or diamond-shaped. | Turning, contouring, and profiling operations. |
Milling Inserts | Inserts used in milling cutters to remove material efficiently. | Slotting, face milling, and surface finishing. |
Drilling Inserts | Highly durable inserts that ensure precision in drilling holes. | Creating holes in hard metals. |
Brazed Inserts | Fixed to tools and offer excellent performance at a lower cost. | General-purpose machining. |
Grooving Inserts | Specially designed for grooving and threading operations. | Creating grooves, slots, and threads. |
Parting Inserts | Optimized for parting-off operations with clean cuts. | Separating workpieces from stock material. |
Threading Inserts | Precise inserts for creating threads on materials. | Internal and external threading. |
Coated Inserts | Inserts coated with TiN, TiCN, or Al2O3 for extended tool life. | High-speed machining, heat-resistant applications. |
Ceramic Inserts | Non-carbide but often paired for specialized machining with enhanced wear resistance. | High-temperature machining of hardened materials. |
Diamond-Tipped Inserts | Tipped with polycrystalline diamond for unparalleled cutting precision and longevity. | Machining non-ferrous materials and composites. |
Raw Materials and Composition of Carbide Inserts
Carbide inserts are primarily composed of tungsten carbide, a compound formed from tungsten and carbon. Here’s a breakdown of their typical raw materials and composition:
Component | Role | Percentage (Typical) |
---|---|---|
Tungsten Carbide (WC) | Provides hardness and wear resistance. | 70-97% |
Cobalt (Co) | Acts as a binder to hold the carbide grains together. | 3-20% |
Titanium Carbide (TiC) | Enhances heat resistance and toughness. | 0-10% |
Tantalum Carbide (TaC) | Improves high-temperature stability. | 0-5% |
The exact mix depends on the insert’s intended application, balancing hardness, toughness, and resistance to thermal and mechanical wear.
Production Process Flow of Carbide Inserts
Ever wondered how these tiny marvels are made? The process is intricate and ensures every insert meets exacting standards.
- Powder Preparation
Tungsten carbide, cobalt, and other additives are mixed into a fine powder. - Compaction
The powder is pressed into a mold to form the desired insert shape using high pressure. - Sintering
The compacted shapes are heated to high temperatures (around 1400°C) to bind the particles, creating a solid, dense material. - Grinding and Shaping
The sintered inserts are ground into precise geometries using diamond-tipped tools. - Coating
Depending on the application, inserts may be coated with materials like titanium nitride or aluminum oxide. - Inspection and Packaging
Each insert undergoes rigorous quality control to ensure dimensional accuracy and performance before being shipped.
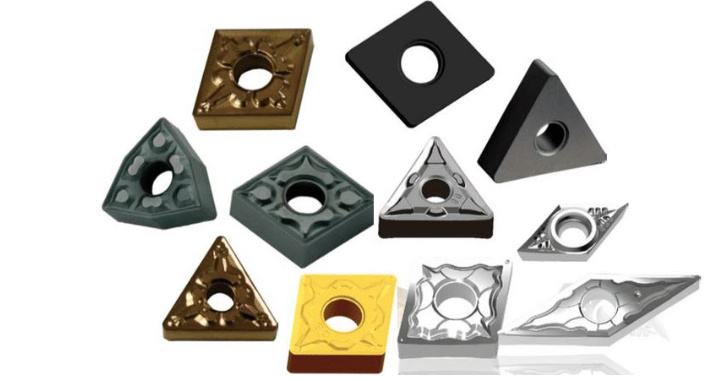
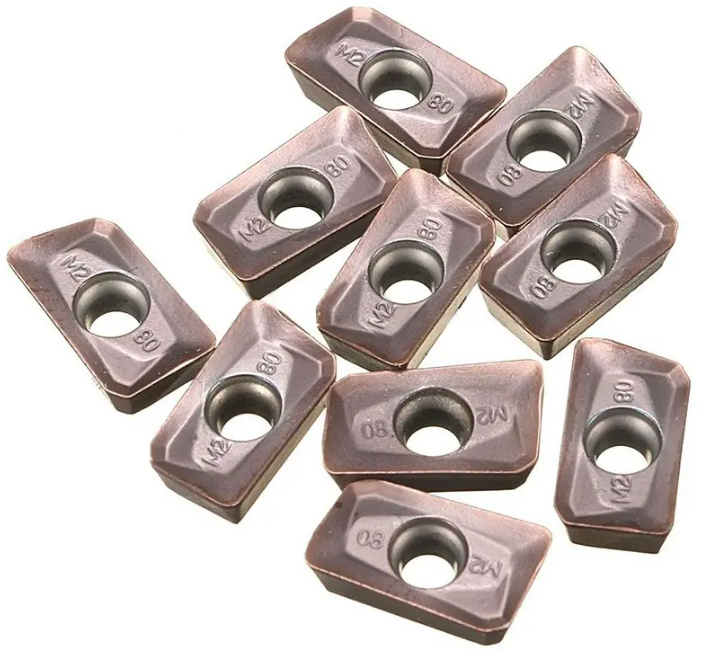
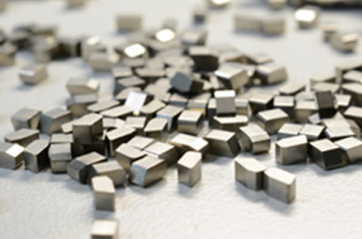
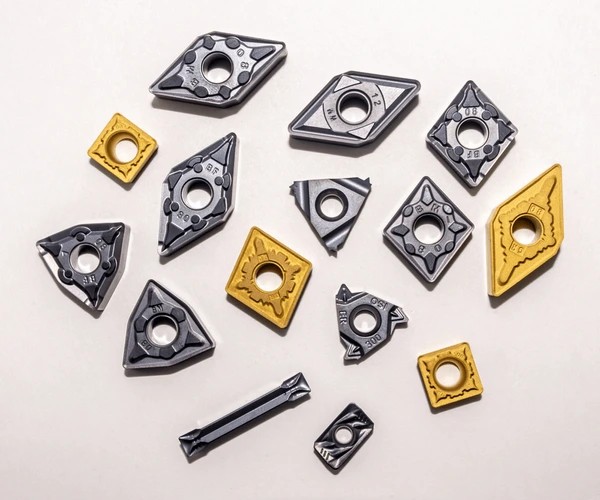
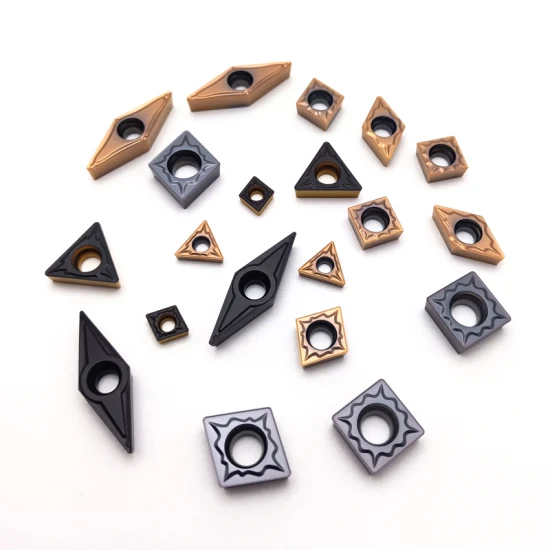
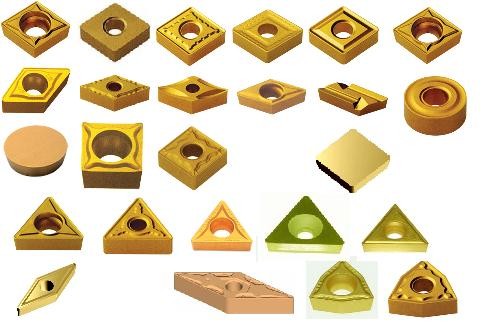
Applications of Carbide Inserts
Carbide inserts are indispensable across numerous industries. Here’s a table highlighting their applications:
Industry | Application | Example Tasks |
---|---|---|
Automotive | Precision machining of engine parts. | Crankshafts, camshafts, gears. |
Aerospace | Machining lightweight, heat-resistant materials. | Aircraft components, turbine blades. |
Manufacturing | General metalworking and fabrication. | Tools, molds, and industrial machinery. |
Oil and Gas | Machining corrosion-resistant materials for harsh environments. | Valves, pipelines, drilling equipment. |
Medical | Creating high-precision medical instruments. | Implants, surgical tools. |
Material Properties of Carbide Inserts
Carbide inserts must balance hardness, toughness, and wear resistance. Here’s an overview of their material properties:
Property | Description | Typical Value |
---|---|---|
Hardness | Resistance to deformation. | 1,500-2,200 HV |
Compressive Strength | Ability to withstand compressive loads. | 4,000 MPa |
Fracture Toughness | Ability to resist crack propagation. | 8-14 MPa·m½ |
Density | Mass per unit volume. | 13-15 g/cm³ |
Thermal Conductivity | Ability to conduct heat. | 70-100 W/mK |
How to Select the Right Carbide Insert
Selecting the right insert can feel overwhelming, but it’s all about balancing your machining needs. Consider these factors:
Factor | Description | Example Selection |
---|---|---|
Material Type | What are you machining—steel, aluminum, or something else? | Steel: Coated inserts. |
Operation Type | Are you turning, milling, drilling, or threading? | Threading: Threading inserts. |
Speed and Feed Rate | High speeds need durable inserts with heat-resistant coatings. | High-speed: TiAlN-coated. |
Tool Life | Prioritize longevity or cost-efficiency? | Longer tool life: Cermet. |
Advantages and Limitations of Carbide Inserts
Advantages | Limitations |
---|---|
Exceptional hardness and wear resistance. | Can be brittle under high impact. |
Versatile for various materials and applications. | Higher initial cost compared to HSS tools. |
Enhanced precision and surface finish. | Requires specific machining conditions. |
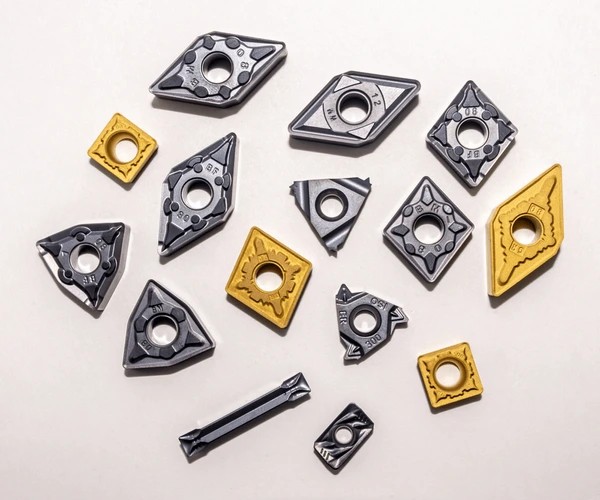
Suppliers and Pricing of Carbide Inserts
Supplier | Location | Pricing (Per Insert) |
---|---|---|
Sandvik Coromant | Global | $10-$50 |
Kennametal | Global | $8-$40 |
Mitsubishi Materials | Japan | $12-$45 |
Iscar | Israel | $15-$60 |
Seco Tools | Sweden | $10-$55 |
FAQs
Question | Answer |
---|---|
What materials can carbide inserts cut? | They are ideal for machining metals like steel, stainless steel, cast iron, and non-ferrous alloys. |
How long do carbide inserts last? | Lifespan varies depending on usage, but high-quality inserts typically last longer than HSS tools due to superior wear resistance. |
Can carbide inserts be resharpened? | No, they are disposable. Instead of resharpening, you replace the insert. |
What coatings are available for carbide inserts? | Common coatings include TiN (titanium nitride), TiCN (titanium carbonitride), and Al2O3 (aluminum oxide) for improved wear resistance and heat dissipation. |