Overview
Carbide Flat Strip refer to flat ferrous alloy steel precursors containing chemically complex carbides that transform upon heat treatment into materials of very high hardness used in demanding wear- and abrasion-resistant applications. Narrow tolerance low roughness carbide alloy strip stock ensures consistent performance in operation.
Key types of carbide materials available as annealed flat strip precursors are:
- Tungsten carbide alloys
- Chromium carbides
- Vanadium carbides
- Tantalum carbides
- Silicon carbides
These strips serve as feedstock for fabricating hawk circular saws, slitters, industrial knives, shear and perforator blades resisting extreme mechanical stresses.
Types of Carbide Flat Strip Materials
Various chemically complex metal carbides significantly strengthen traditional tool steel grades when present as fine uniform dispersoids:
Tungsten Carbides
Tungsten carbide crystals have hardness values exceeding 2500 HV conferring impressive abrasion resistance through a variety of mechanisms:
- Physical shielding effect
- Load bearing support
- Fracture resistance
Tungsten typically appears in 6-12% concentrations within specialized hot work tool steel matrices alongside other strengthening carbides.
Benefits
- Hardness capability over 65 HRC
- High toughness
- Thermal shock stability
Limitations
- Difficulty machining requiring EDM
- Brittle failure modes
Chromium Carbides
Alloying elements like chromium combine with migratory carbon forming very hard abrasion-resistant chromium carbides (Cr23C6). Dispersed interlaced chromium carbides bolster abrasion resistance through composite strengthening mechanisms.
Benefits
- Less expensive alloying addition than tungsten
- Corrosion resistance
Limitations
- Less hardness capability than tungsten carbide grades
Vanadium Carbides
Microalloying ferrous tool steel compositions with 0.5-2% vanadium facilitates prolific formation of fine vanadium carbide precipitates (VC) upon proper heat treatment further enhancing wear resistance.
Benefits
- Cost-effective strengthening
- Improved fatigue resistance
Limitations
- Lower hardness than tungsten/chromium carbides
- Brittleness with excessive levels
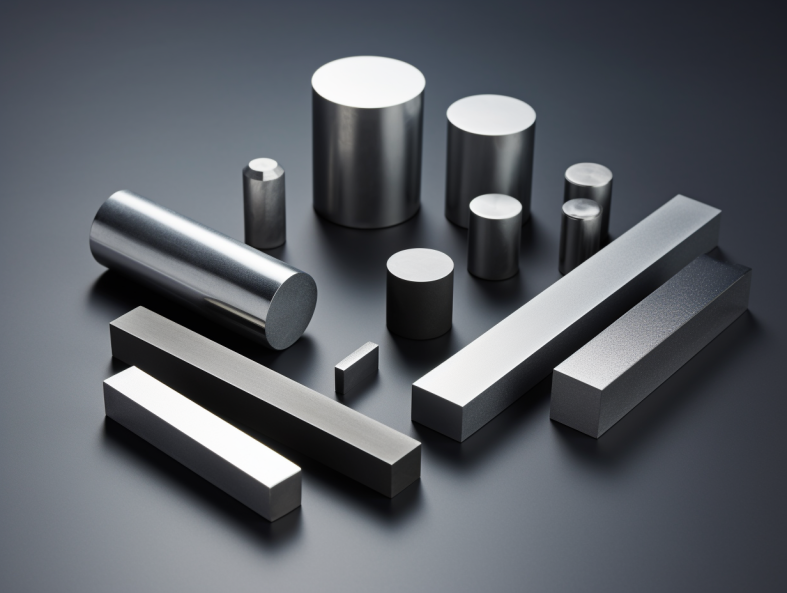
Production Methods
Common techniques for fabricating tailored carbide alloy strip include:
Casting
- Vacuum induction melting forms desired chemistry
- Followed by hot rolling into strip
Powder Metallurgy
- Blended elemental/prealloy powders
- Compacted into green preforms
- Hot consolidated into fully dense strip
Comparison Criteria
Parameter | Cast Strip | P/M Strip |
---|---|---|
Homogeneity | Moderate | ✅ Excellent |
Inclusions | Possible | Eliminated |
Alloy Flexibility | Limited | ✅ Broad customization |
Cost Economics | Lower initial costs | ✅ Higher production rate |
Powder metallurgy consolidation from blended nanoscale powders ensures optimum homogeneity and cleanliness necessary for reliable consistent carbide performance.
Key Properties
Critical considerations in quality Carbide Flat Strip include:
Surface Finish
Strict surface roughness tolerances on strip assure precision interface dimensions and shearing action facilitating clean tearing/cutting minimizing jagged or burred edges.
Parameter | Typical Range |
---|---|
Average Roughness (Ra) | 0.4 – 0.7 μm |
RMS Roughness (Rq) | 0.6 – 1.0 μm |
Dimensional Tolerances
Maintaining narrow width, thickness, flatness and squareness tolerances of Carbide Flat Strip is vital allowing precision assembly of slitters, industrial knives and related tooling systems. Tolerances down to ±0.025 mm on dimensions assure reliability.
Chemistry
Controlling compositions within 0.25 wt% ensures consistent as-quenched post-heat treat hardness and toughness linked to fractional percentages of strengthening carbides:
Alloy | Wt% Range |
---|---|
Tungsten | 5 – 8% |
Carbon | 0.7 – 1.4% |
Chromium | 3 – 6% |
Vanadium | 0.8 – 1.5% |
Deviations beyond these thresholds risks inadequate transformational hardening or excessive brittleness.
Testing and Verification
Multiple quality checks validate performance:
Microstructure Confirmation
Micrographs should indicate uniform distribution of strengthening carbides in suitable matrices. Image analysis determines phase fractions.
Hardness Mapping
Rockwell or Vickers micro/macro hardness indent mapping across entire strip surface identifies any deviations indicating inadequate carbide formation or non-uniform chemistry.
Machinability Assessments
Test machining trials assess grindability, cutting forces generated, achievable surface finish, tool wear rates and burr formation tendencies before full production.
Heat Treatment Response Tests
Measuring before and after hardness on sample strips verifies attainment of specified hardness above 60 HRC following quench and tempering validates process.
Applications and Use Cases
Exceptional hardness rendered through heat-induced microstructural transformations of various metal carbide dispersions make these materials uniquely suited for:
Industrial Slitter and Cutter Blades
- Paper, polymer, textile manufacturing
- Tight thickness tolerances prevent jamming
- Carbides withstand highly abrasive media
Circular Saw Blades
- Carbide grades enhance durability, metal removal rates and lifetimes
Food Processing Equipment
- Slicers, dicers, perforators
- Carbides resist abrasive bone fragments
Glass Cutting Machinery
- Scoring hardness without microfractures
High Speed Steel Cutting Tools
- Drills, endmills, tool bits
Standards and Specifications
Application-specific standards help define product performance needs:
Standard | Purpose |
---|---|
ASTM A681 | Standard for tool steel strip |
AMS 6681 | Aerospace grade tool steel strip |
AISI/SAE 52100 | Ball bearing steel |
DIN 1.2510 | Alloy tool steel standard |
Customers and producers align composition, surface finish, tolerance and hardness requirements per final operating conditions through specialty grade development.
Cost Analysis
Carbide Flat Strip pricing depends heavily on:
1. Carbide Types and Compositions
- Tungsten and tantalum grades are more expensive than chromium or vanadium carbide alloys
2. Size Requirements
- Economies of scale apply for longer strips or high annual volume forecast
3. Lead Times
- Rush or expedited deliveries draw premiums
4. Testing Extensiveness
- More rigorous validation procedures increase cost
Grade | Pricing Estimate |
---|---|
T2 High Speed Steel | $7 – $15 per kg |
M2 Tool Steel | $12 – $25 per kg |
Custom Tungsten Carbide | $30 – $60 per kg |
Purchasers should balance needs versus budget in developing custom Carbide Flat Strip requirements.
Advantages and Challenges
Benefits
- Excellent wear and abrasion resistance
- Customizable carbide compositions and ratios
- Dimensional precision from powder metallurgy
- Heat treatable to over 65 HRC hardness
Limitations
- Higher cost than standard tool steels
- Brittle failure modes still possible
- Complex to fully characterize performance
- Secondary machining difficulties
Comparing to Alternatives
Parameter | Carbide Strip | Ceramic Media | Diamond Coatings |
---|---|---|---|
Abrasion Resistance | Excellent | Best | Best |
Toughness | Good | Poor | Good |
Thermal Shock Resistance | Good | Poor | Excellent |
Cost | Medium | High | Highest |
FAQs
Q: What carbide strip hardness levels are typical for industrial slitter blades?
A: Target hardness after heat treatment for precision slitters processing polymers, paper and textiles usually lies between 62-65 HRC conferring an optimum balance of wear performance and fracture resistance from transformed carbides.
Q: What thickness precision is important for circular saw carbide blades?
A: Deviations above ±0.05 mm between carbide strips assembled into stacks can cause runout issues deteriorating cutting accuracy and increasing risks of fracturing, cracking or tooth loss in operation.
Q: Why is composition control vital for custom tungsten or tantalum carbide alloys?
A: Precise alloying percentages directly impact resultant carbide volume fractions formed during quenching. Excess amounts risk brittleness while inadequate levels reduce abrasion resistance. Each grade has optimized ratios.
Q: What post-processing method increases toughness of hardened carbide steel?
A: Cryogenic treatment applying subzero temperatures after standard tempering allows transition of retained austenite to martensite increasing wear resistance by 25-30% while also improving fracture toughness and flexibility by transforming the microstructure.