Introduction
Definition of Carbide Die Blanks
Carbide die blanks are specialized tools used in various industries for shaping and forming materials. These blanks are made from a combination of tungsten carbide and cobalt, which gives them exceptional hardness and durability. The main purpose of carbide die blanks is to create precise and intricate shapes in materials such as metal, plastic, and wood. They are commonly used in manufacturing processes such as stamping, forging, extrusion, and cutting. The high wear resistance of carbide die blanks allows them to withstand the intense pressure and friction involved in these processes, ensuring a longer tool life and improved productivity. With their superior strength and precision, carbide die blanks have become an essential component in the production of a wide range of products, from automotive parts to electronic components.
Importance of Carbide Die Blanks
Carbide die blanks play a crucial role in various industries, including manufacturing, automotive, and aerospace. These high-performance tools are essential for precision cutting, shaping, and forming of materials such as metal, plastic, and wood. The importance of carbide die blanks lies in their exceptional hardness, wear resistance, and thermal stability, which enable them to withstand extreme operating conditions and deliver consistent and accurate results. With their superior durability and longevity, carbide die blanks significantly improve productivity, reduce downtime, and ensure high-quality end products. Whether it’s for stamping, punching, or extrusion applications, the use of carbide die blanks is indispensable for achieving efficient and cost-effective manufacturing processes.
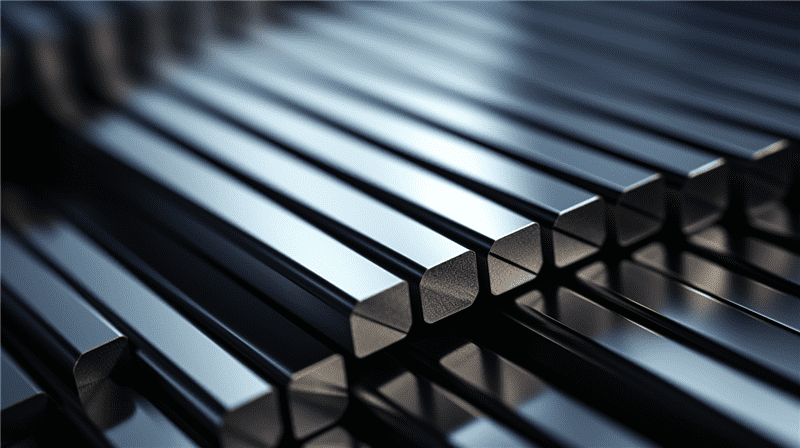
Applications of Carbide Die Blanks
Carbide die blanks find extensive applications in various industries due to their exceptional hardness and wear resistance. One of the key applications of carbide die blanks is in the manufacturing of metal components, such as fasteners, bolts, and screws. The high hardness of carbide die blanks allows them to withstand the extreme pressures and temperatures involved in metal forming processes. Additionally, carbide die blanks are widely used in the production of wire and cable, where they provide precise and consistent shaping of the materials. Other applications of carbide die blanks include the production of ceramics, plastics, and glass, where they enable the creation of intricate shapes and designs. Overall, the versatility and durability of carbide die blanks make them indispensable in various industries for achieving high-quality and precise manufacturing processes.
Composition of Carbide Die Blanks
Tungsten Carbide
Tungsten Carbide is a versatile and highly durable material widely used in various industries. It is known for its exceptional hardness and resistance to wear and corrosion. In the context of carbide die blanks, Tungsten Carbide is the preferred material due to its superior strength and toughness. Carbide die blanks made from Tungsten Carbide offer excellent precision and longevity, making them ideal for applications that require high levels of accuracy and durability. Whether it is for stamping, punching, or forming operations, Tungsten Carbide carbide die blanks provide reliable performance and consistent results. With their exceptional hardness and resistance to wear, they can withstand the most demanding manufacturing processes, ensuring the production of high-quality components. In summary, Tungsten Carbide is a crucial material in the production of carbide die blanks, enabling the manufacturing industry to achieve precise and efficient results.
Cobalt
Cobalt is a crucial element in the production of carbide die blanks. It is widely used as a binder material in the manufacturing process. The addition of cobalt enhances the hardness and strength of the carbide, making it suitable for various applications in industries such as automotive, aerospace, and manufacturing. The high melting point and resistance to wear and corrosion make cobalt an ideal choice for carbide die blanks, ensuring their durability and longevity. With the increasing demand for high-quality carbide die blanks, the importance of cobalt in their production cannot be overstated.
Other Additives
Carbide die blanks are essential components in various industries, especially in the manufacturing sector. These blanks are made from high-quality carbide materials, which provide exceptional hardness and wear resistance. They are commonly used in the production of precision tools and components, such as cutting tools, punches, and dies. Additionally, carbide die blanks are known for their excellent thermal conductivity, allowing for efficient heat dissipation during machining operations. With the addition of other additives, such as cobalt or titanium, the properties of carbide die blanks can be further enhanced, resulting in improved performance and longevity. The use of carbide die blanks with other additives has become increasingly popular due to their ability to withstand high temperatures and resist wear, making them an ideal choice for demanding applications in industries like aerospace, automotive, and medical.
Manufacturing Process
Powder Metallurgy
Powder metallurgy is a manufacturing process that involves the production of metal parts by compacting and sintering metal powders. It is widely used in the production of carbide die blanks, which are essential components in various industries. Carbide die blanks are made from a mixture of tungsten carbide and cobalt powders, which are pressed into a die cavity and then sintered at high temperatures. The resulting carbide die blanks have excellent hardness, wear resistance, and dimensional stability, making them ideal for applications that require high precision and durability. With the advancements in powder metallurgy techniques, carbide die blanks are now available in a wide range of sizes, shapes, and compositions, allowing manufacturers to meet the specific requirements of different industries. The use of carbide die blanks in industries such as automotive, aerospace, and manufacturing has significantly improved the efficiency and quality of various processes, making them an indispensable tool in modern manufacturing.
Compaction
Compaction is a critical process in the production of carbide die blanks. It involves the compression of powdered tungsten carbide and other materials into a die cavity to form a compacted shape. This process is essential for achieving the desired density and strength of the carbide die blanks. Compaction is typically performed using hydraulic presses or mechanical presses, which apply high pressure to the powder mixture. The compacted shape is then sintered at high temperatures to further enhance its strength and durability. Overall, the compaction process plays a crucial role in ensuring the quality and performance of carbide die blanks.
Sintering
Sintering is a crucial process in the production of carbide die blanks. It involves heating the powdered carbide material at high temperatures, typically in a controlled atmosphere, to facilitate the bonding of particles. During sintering, the carbide particles undergo a process called diffusion, where they merge and form a solid mass. This results in a dense and strong carbide structure with excellent wear resistance and hardness. The sintering process also helps to eliminate any residual porosity in the carbide material, ensuring its mechanical integrity and dimensional stability. Overall, sintering plays a vital role in transforming carbide powder into high-quality die blanks that are capable of withstanding the demanding conditions of various manufacturing applications.
Properties of Carbide Die Blanks
Hardness
Carbide die blanks are known for their exceptional hardness. This characteristic makes them ideal for applications where high wear resistance and durability are required. With a hardness rating that surpasses that of steel, carbide die blanks can withstand heavy loads and extreme temperatures without deforming or losing their shape. This hardness also allows for precise and accurate machining, ensuring consistent and reliable performance. Whether used in the automotive, aerospace, or manufacturing industries, carbide die blanks offer unmatched hardness that enhances the performance and longevity of various tools and components.
Wear Resistance
Carbide die blanks are known for their exceptional wear resistance, making them ideal for applications where durability is crucial. The high hardness and toughness of carbide materials allow these die blanks to withstand the extreme conditions of heavy-duty operations. Whether it’s in the automotive, aerospace, or manufacturing industry, carbide die blanks provide long-lasting performance and reliable results. With their resistance to wear, these die blanks minimize the need for frequent replacements, reducing downtime and increasing productivity. Additionally, the wear resistance of carbide die blanks ensures consistent and precise shaping of materials, resulting in high-quality finished products. Overall, the superior wear resistance of carbide die blanks makes them a valuable asset in various industries, where reliability and longevity are paramount.
Heat Resistance
Carbide die blanks are known for their exceptional heat resistance properties. They are specifically designed to withstand high temperatures without losing their structural integrity or performance. This makes them ideal for applications that involve intense heat and pressure, such as metal forming and shaping processes. The heat resistance of carbide die blanks ensures that they can maintain their shape and hardness even under extreme conditions, resulting in longer tool life and improved productivity. Additionally, their ability to resist thermal deformation and wear makes them a reliable choice for demanding industries where precision and durability are paramount.
Advantages of Carbide Die Blanks
Longevity
Carbide die blanks are known for their exceptional longevity. These high-quality tools are specifically designed to withstand the demands of heavy-duty industrial applications. With their superior hardness and resistance to wear, carbide die blanks can maintain their sharpness and precision for extended periods of time. This longevity not only ensures consistent and reliable performance but also helps to minimize downtime and increase productivity. Whether used in metal stamping, wire drawing, or other manufacturing processes, carbide die blanks are a reliable choice for businesses looking for durable and long-lasting tooling solutions.
High Precision
Carbide die blanks are widely used in various industries due to their exceptional hardness and wear resistance. In the field of high precision manufacturing, these die blanks play a crucial role in achieving accurate and consistent results. The superior strength and durability of carbide make it an ideal material for creating dies that can withstand the high pressures and stresses involved in precision machining. Additionally, carbide die blanks offer excellent dimensional stability, ensuring that the final products meet the strictest tolerances. With their outstanding performance and reliability, carbide die blanks have become the preferred choice for manufacturers seeking to achieve the highest level of precision in their operations.
Cost-effectiveness
Carbide die blanks offer a significant advantage in terms of cost-effectiveness. These versatile tools are known for their long lifespan and high durability, making them a cost-effective choice for various industries. The superior hardness of carbide die blanks allows for increased productivity and reduced downtime, resulting in cost savings. Additionally, the precision and accuracy of carbide die blanks contribute to improved efficiency and quality in manufacturing processes. With their ability to withstand high temperatures and resist wear and tear, carbide die blanks prove to be a wise investment for businesses looking to optimize their operations and minimize expenses.
Applications of Carbide Die Blanks
Metal Stamping
Metal stamping is a widely used manufacturing process in which metal sheets are formed into desired shapes using a die and a press. It is commonly used in industries such as automotive, aerospace, and electronics. Carbide die blanks play a crucial role in metal stamping as they are used to create the dies that shape the metal sheets. These die blanks are made from a high-quality carbide material, which provides excellent hardness and wear resistance. With their superior strength and durability, carbide die blanks ensure precise and consistent metal stamping operations, resulting in high-quality finished products. Whether it’s producing intricate automotive components or precise electronic parts, carbide die blanks are essential for achieving accurate and efficient metal stamping processes.
Wire Drawing
In the wire drawing process, carbide die blanks play a crucial role. These die blanks are specially designed to withstand the high pressure and friction involved in drawing wires of various diameters. Made from high-quality carbide materials, they offer exceptional hardness and wear resistance, ensuring a longer lifespan compared to traditional die materials. The precise shape and dimensions of the carbide die blanks contribute to the accuracy and consistency of the wire drawing process, resulting in smooth and uniform wire products. With their excellent heat resistance and durability, carbide die blanks are the preferred choice for wire drawing applications in industries such as automotive, aerospace, and electronics.
Cold Heading
Cold heading is a manufacturing process used to shape metal into specific forms. It involves the use of carbide die blanks, which are hardened and durable tools designed to withstand the high pressures and forces involved in the cold heading process. These die blanks are made from a special type of carbide material that is known for its toughness and wear resistance. During cold heading, the metal is placed between the die blanks and subjected to a series of blows or compressions to shape it into the desired form. This process is commonly used in industries such as automotive, aerospace, and construction to produce a wide range of components, including bolts, screws, and fasteners. The use of carbide die blanks in cold heading ensures accurate and precise shaping of the metal, resulting in high-quality and reliable products.