Carbide buttons are small yet mighty components that play a critical role in industries like mining, drilling, and machining. Their exceptional hardness, wear resistance, and durability make them indispensable in tools and machinery that face extreme conditions. In this article, we’ll dive deep into the world of carbide buttons, exploring their materials, production process, applications, and more. Whether you’re a buyer, engineer, or just a curious reader, we’ll simplify the technical jargon and help you make informed decisions.
What Are Carbide Buttons?
Carbide buttons are compact, high-strength components made from cemented carbide—a composite material primarily consisting of tungsten carbide (WC) particles bound together by a metal binder, usually cobalt or nickel. Their unique properties make them ideal for cutting, drilling, and abrasion-resistant applications.
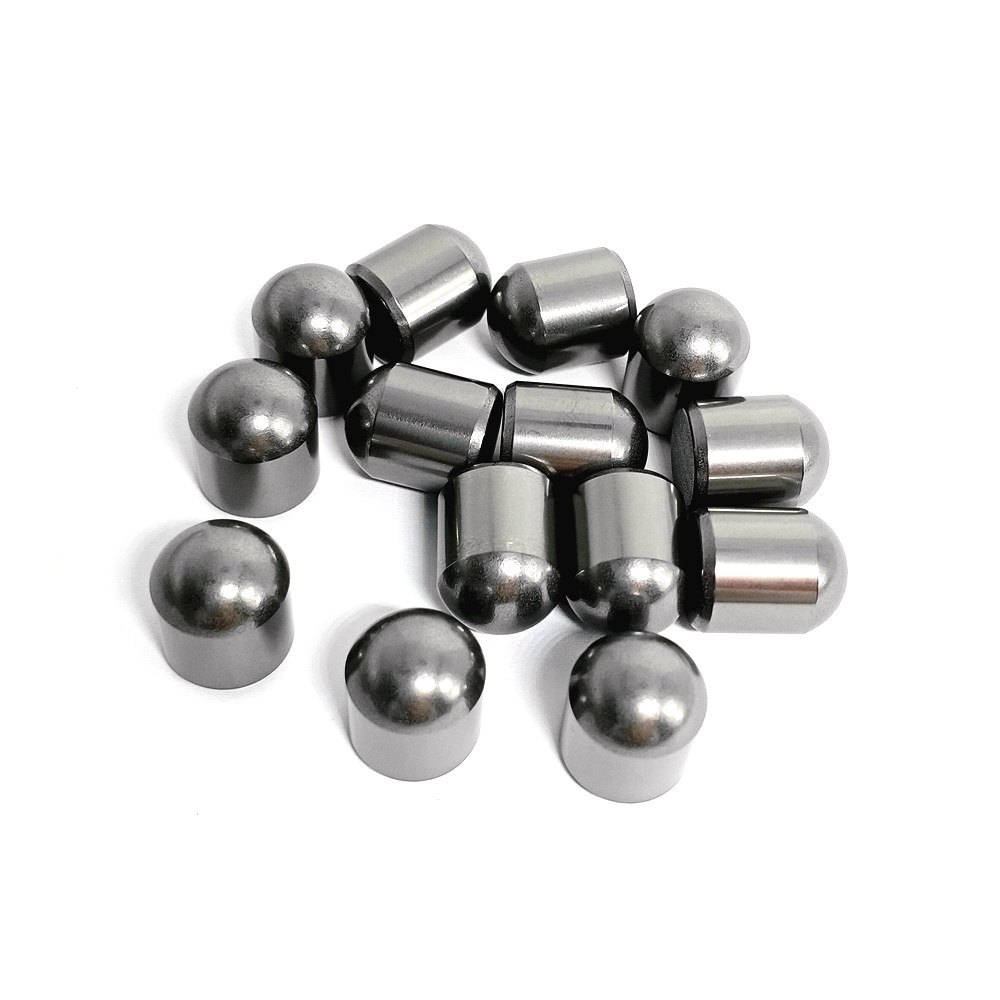
Types of Carbide Buttons
Here’s a detailed breakdown of carbide button types, categorized by shape, functionality, and industrial application:
Type | Description | Applications |
---|---|---|
Spherical Buttons | Round-shaped, offer excellent resistance to abrasion and wear. | Mining, deep drilling, rock excavation. |
Conical Buttons | Cone-shaped for better penetration in hard materials. | Hard rock drilling, deep well exploration. |
Flat Buttons | Feature a flat surface, used for grinding and stabilization. | Tool stabilization, boring applications. |
Chisel Buttons | Sharp edge for precision cutting. | Precision machining, fine cutting. |
Parabolic Buttons | Dome-shaped for general-purpose use in moderate drilling conditions. | Coal mining, road construction. |
Tapered Buttons | Designed for gradual penetration in various materials. | Tunneling, drilling in mixed material conditions. |
Ballistic Buttons | Aggressive cutting angle for high-speed drilling. | High-impact drilling, fast-cutting applications. |
Double Dome Buttons | Two rounded surfaces for increased wear resistance. | Tough environments requiring extended tool life. |
Insert Buttons | Customizable shapes for specialized applications. | Industrial-grade drilling tools. |
Multi-Edge Buttons | Provide multiple cutting edges for prolonged use. | Heavy-duty applications like oil and gas drilling. |
Raw Materials and Composition Analysis of Carbide Buttons
Carbide buttons owe their remarkable properties to their carefully engineered composition.
Common Materials Used in Carbide Buttons
- Tungsten Carbide (WC): The primary material, known for its extreme hardness and wear resistance.
- Cobalt (Co): Acts as a binder, providing toughness and resistance to cracking.
- Nickel (Ni): Used as an alternative binder for corrosion-resistant applications.
- Metal Powders: Enhance specific properties like hardness or strength.
Composition and Properties of Carbide Buttons
Material | Percentage (%) | Role | Effect on Performance |
---|---|---|---|
Tungsten Carbide (WC) | 70-97% | Provides hardness and wear resistance. | High durability and resistance to deformation. |
Cobalt Binder (Co) | 3-30% | Enhances toughness and reduces brittleness. | Improved impact resistance and ductility. |
Nickel Binder (Ni) | 2-5% | Corrosion resistance. | Suitable for environments with high moisture. |
Additives (e.g., TaC) | 1-3% | Adjust grain size and toughness. | Customizable properties for specific applications. |
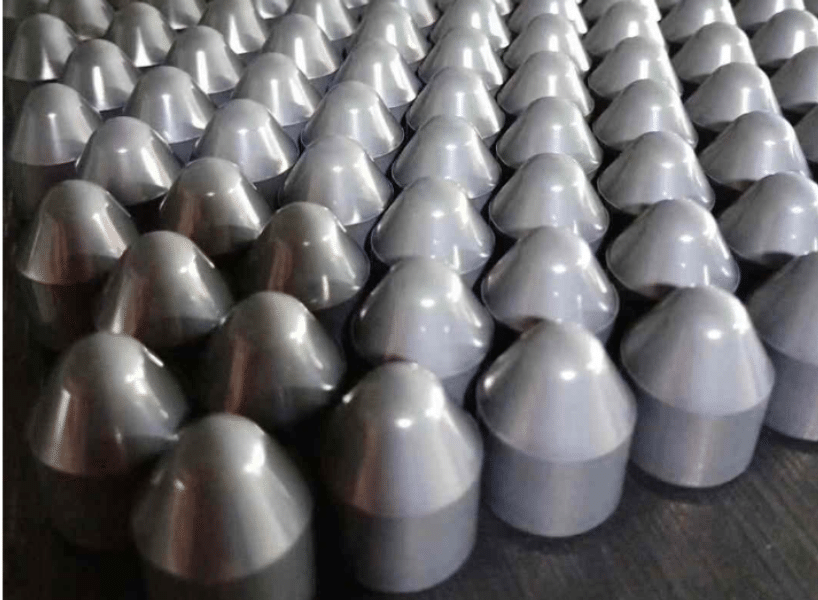
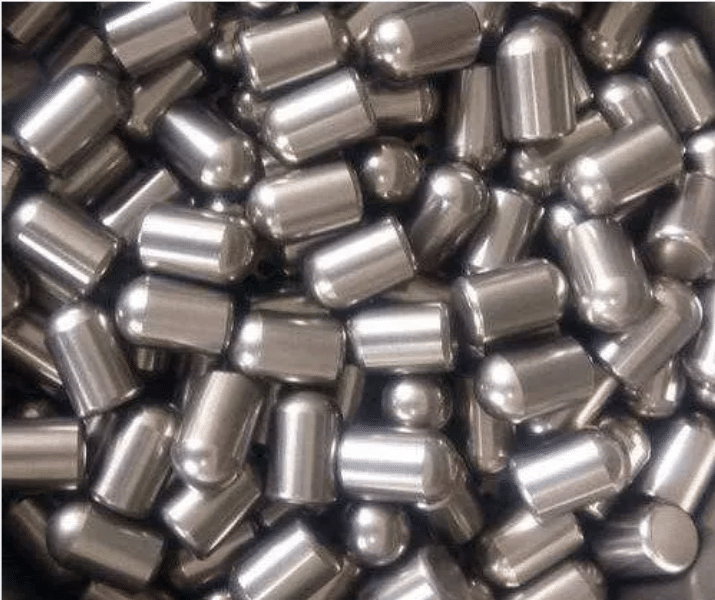
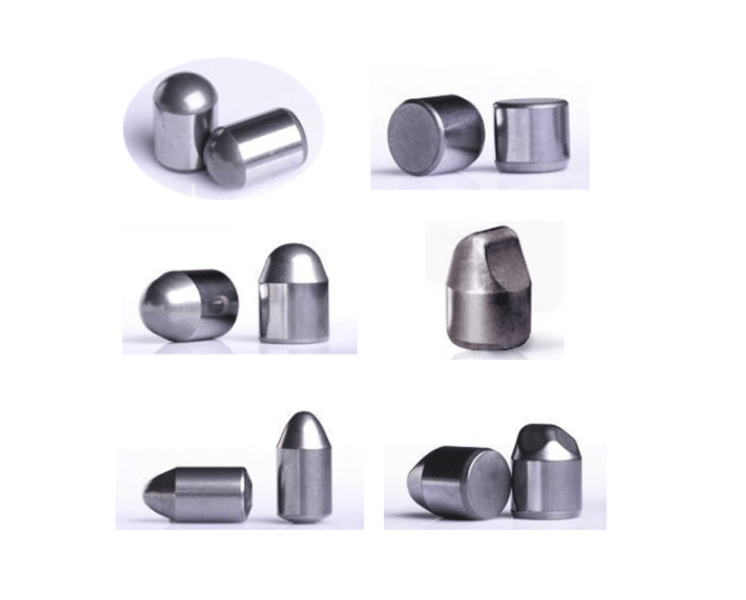
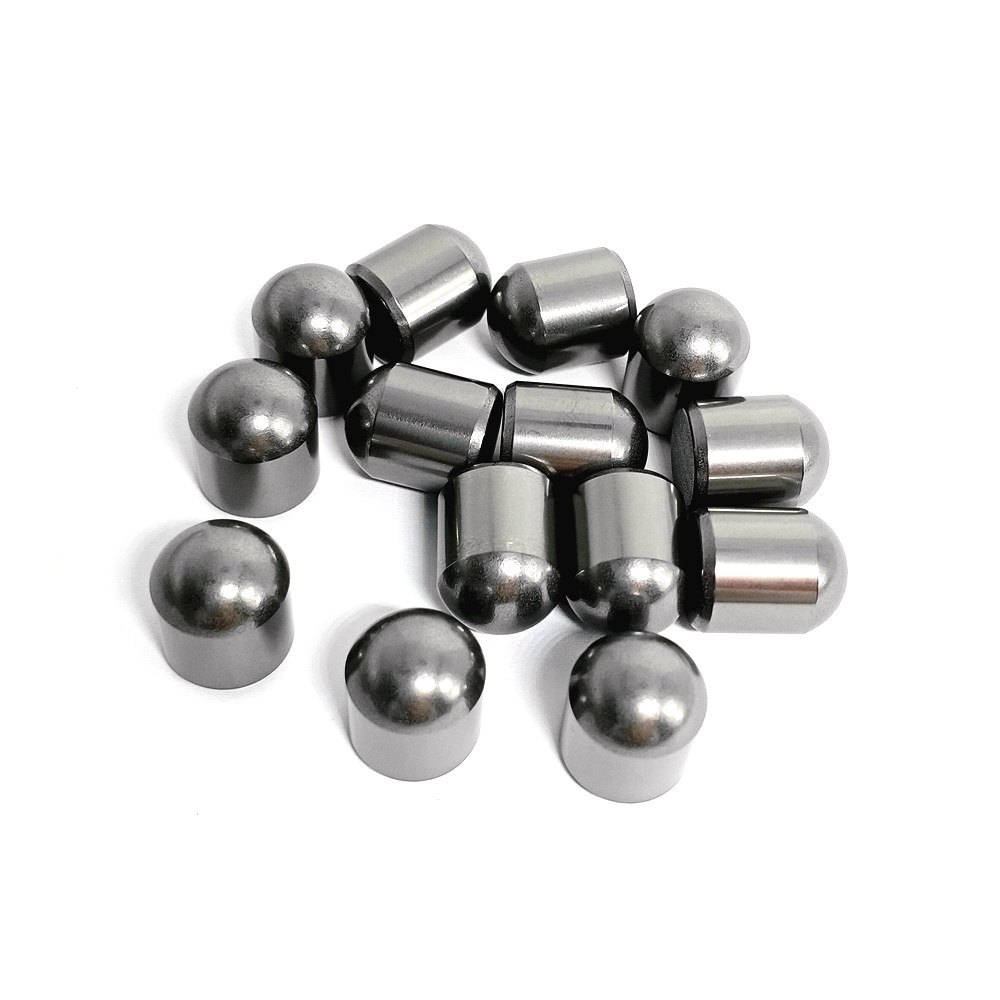
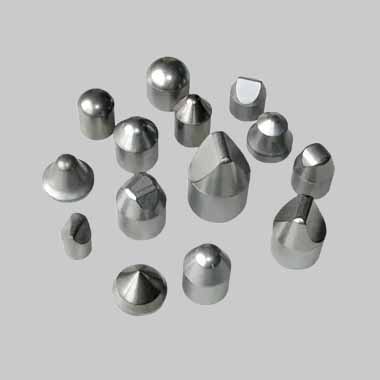
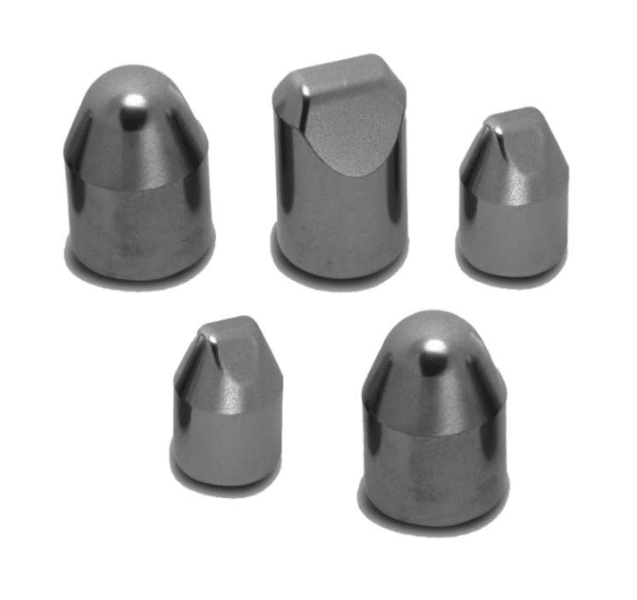
Applications of Carbide Buttons
Carbide buttons find uses across various sectors. Let’s outline their applications based on industry:
Industry | Application |
---|---|
Mining | Rock drilling, coal mining, and mineral extraction. |
Oil and Gas | Exploration drilling and well construction. |
Construction | Road cutting, tunneling, and demolition. |
Precision Machining | Cutting tools for metals and composites. |
Defense | Armored components and military-grade tools. |
Aerospace | High-performance cutting and abrasion-resistant parts. |
Production Process Flow of Carbide Buttons
- Powder Preparation: Tungsten carbide powder is mixed with cobalt or nickel binders.
- Pressing: The mixture is pressed into desired shapes under high pressure.
- Sintering: Components are heated to high temperatures in a controlled environment to bond the particles.
- Finishing: Post-sintering processes like grinding and polishing ensure precision.
- Quality Control: Rigorous testing for hardness, density, and dimensions.
Material Properties of Carbide Buttons
Property | Range | Significance |
---|---|---|
Hardness (HRA) | 87-93 | Determines wear resistance. |
Density (g/cm³) | 14.5-15.5 | Affects strength and impact resistance. |
Compressive Strength (MPa) | 2000-3500 | Resistance to crushing forces. |
Fracture Toughness (MPa·m1/2) | 8-15 | Ensures crack resistance under stress. |
Thermal Conductivity (W/m·K) | 50-100 | Heat dissipation during high-speed applications. |
Specifications, Sizes, Shapes, and Standards
Parameter | Options |
---|---|
Shape | Spherical, conical, flat, chisel, parabolic. |
Size | 8mm, 10mm, 12mm, 16mm, 20mm, etc. |
Standards | ISO, ANSI, GB/T, DIN. |
Hardness, Strength, and Wear Resistance
Characteristic | Details |
---|---|
Hardness (HRA) | Up to 93 for premium models. |
Wear Resistance | Excellent for abrasive conditions. |
Impact Strength | Optimized for high-pressure applications. |
Suppliers and Pricing Details
Supplier Name | Location | Price Range (USD) |
---|---|---|
Carbide Solutions Inc. | USA | $5-15 per piece. |
Tungsten Experts | Germany | $10-20 per piece. |
DrillTech Industries | China | $3-10 per piece. |
How to Select the Right Carbide Button
Factor | Details |
---|---|
Application Environment | Choose based on material hardness and abrasiveness. |
Button Shape | Match shape to specific drilling requirements. |
Binder Content | Higher cobalt for toughness, nickel for corrosion resistance. |
Cost vs. Performance | Balance initial cost with expected tool life. |
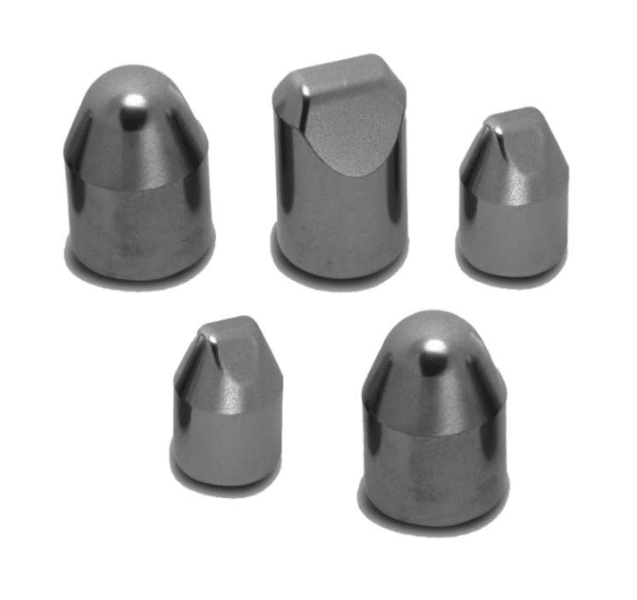
Advantages and Limitations of Carbide Buttons
Advantages | Limitations |
---|---|
Exceptional hardness and durability. | High initial cost. |
Resistance to extreme temperatures. | Brittleness in some configurations. |
Versatility in applications. | Requires precise handling during installation. |
FAQs
Question | Answer |
---|---|
What are carbide buttons used for? | They are primarily used in drilling, cutting, and abrasion-resistant applications in industries like mining, oil, and gas. |
How are carbide buttons made? | They are produced using a powder metallurgy process, including pressing, sintering, and finishing. |
What’s the hardest carbide button material? | Tungsten carbide with high cobalt content offers the highest hardness and wear resistance. |
How do I choose the right carbide button? | Consider application requirements, material hardness, and environmental conditions like moisture and temperature. |