Overview of Carbide Block Die Blanks
Carbide block die blanks are blocks of tungsten carbide that can be machined into custom shapes to create dies and other industrial tooling. Carbide offers high hardness, wear resistance, compressive strength, and chemical stability, making it an ideal material for forming and stamping tools, extrusion dies, drawing dies, and more.
Key details about carbide block die blanks:
- Made from tungsten carbide with cobalt binder
- Available in a range of carbide grades and grain sizes
- Offer high hardness (~90 HRA) and resistance to abrasion/erosion
- Withstand high compressive stress without distortion
- Maintain strength and edge sharpness at high temperatures
- Can be precision machined into complex die and tool shapes
- Require diamond grinding/EDM to shape – resistant to conventional machining
- Used for manufacturing dies for metal forming, stamping, wire drawing, extrusions, etc.
- Also used to make pelletizer dies, trim dies, bearing races, and other tooling
- Enables long production runs with minimal die wear or maintenance
- Higher initial cost but longer lifespan than steel tooling
Types of Carbide Block Die Blanks
There are several types of carbide grades and binder contents used for die blank blocks:
Carbide Grade | Description |
---|---|
Straight Grade | Most common general purpose grade, 8-12% cobalt binder |
Micrograin | Very fine 1-3 micron grain size, optimal hardness |
Submicron | Ultrafine submicron grains for smoother finishes |
Coarse Grain | Larger grains with higher fracture resistance |
Medium/Fine Grain | Balanced grain size, lower cost option |
Binder Content | Description |
---|---|
6% | Minimum binder, highest hardness, more brittle |
8-12% | Standard binder content, optimal combination of hardness and toughness |
15%+ | High binder for increased fracture resistance |
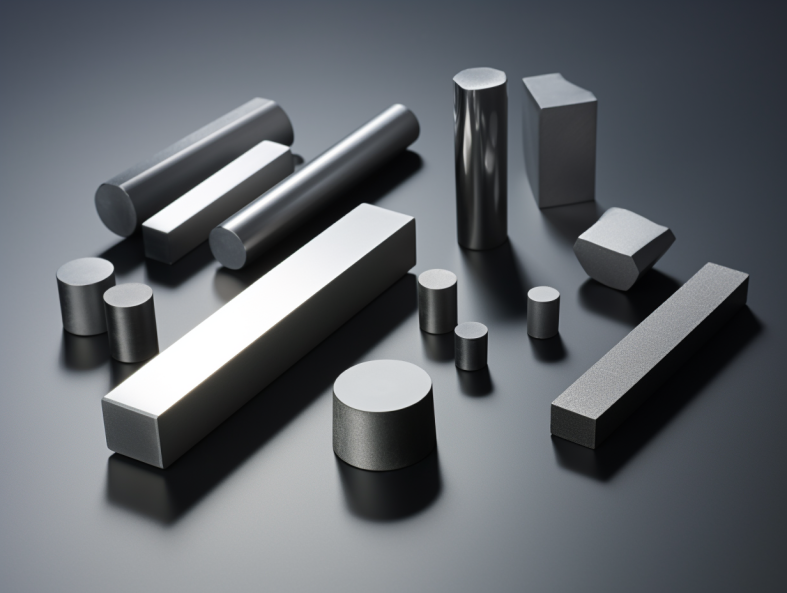
Applications and Uses of Carbide Block Die Blanks
Carbide block die blanks have many uses across manufacturing:
Application | Uses |
---|---|
Metal forming | Punch/stamping dies, draw dies, bending dies |
Wire drawing | Carbide drawing dies with precise hole dimensions |
Extrusion | Complex extrusion dies for metals and plastics |
Pelletizing | Pelletizer dies for making plastic and pharmaceutical pellets |
Automotive | Trim/piercing dies, bearing races, custom automotive tooling |
Electronics | Leadframe trim/punch dies, semiconductor wafer handling |
Medical | Tablet punch dies, surgical blades, dental drills |
Aerospace | Aircraft riveting dies, turbine blade formed dies |
Military/Defense | Ammunition forming dies, armor panel dies |
Specifications of Carbide Block Die Blanks
Key specifications for carbide block die blanks:
Parameter | Details |
---|---|
Dimensions | Thicknesses from 1/4” to over 6”, diameters up to 30”+ |
Tolerances | Custom tolerances down to +/- 0.0005” |
Surface Finish | Up to 4 Ra microinch, some down to 2 Ra |
Hardness | Up to 90+ HRA depending on grade |
Transverse Rupture Strength | 500,000 – 600,000 psi |
Density | 14.95 g/cm2 |
Thermal Conductivity | 60 W/m-K |
Maximum Service Temperature | 1000°C / 1800°F |
Thermal Expansion Coefficient | 5.2 x 10-6/K |
Electrical Resistivity | 25-50 x 10-6 Ω-cm |
Standard grades meeting ISO specification and M grade ultrafine submicron carbides are common. Custom requirements can also be met.
Suppliers of Carbide Block Die Blanks
Top suppliers of carbide block die blanks include:
Supplier | Description |
---|---|
Kennametal | Global leader, grades include KC850, KC925, KC994 |
Mitsubishi Materials | Top grades are AC2000, AC2500, AC3000 |
Ceratizit | High precision Swiss carbides, MAXICARB grades |
Kyocera SGS | Japanese brand, wide thickness range |
Midwest Carbide | Broad selection of dies and tool blanks |
Global Tungsten | Tungsten and carbide supplier, precision machining |
Eagle Alloys | Large inventory of barstock and blocks |
Scientific Cutting Tools | Custom fabricated blanks, quick delivery |
Carbide blocks are priced based on size, grade, and order quantity. Small blanks can range $150-$500 each while large 30”+ blocks for progressive dies can cost over $5000 each. High precision submicron grades carry a premium.
Installation, Operation, and Maintenance
- Carbide dies and tooling require precision machining on CNC mills with diamond wheels
- All machining stresses must be minimized to prevent microfractures
- Critical dimensions should be finish ground to final tolerance
- Pieces require lapping/honing and edge blending for optimal performance
- Careful handling is imperative – carbide is brittle and can chip if struck
- Dies should be secured in holders/fixtures with even clamping force
- Dies must be sharpened periodically to restore sharp cutting edges
- No aggressive chemicals should come into contact with carbide parts
- Dies should be inspected periodically for wear, cracks, or edge rounding
- Damaged parts may need welding repair or replacement if reuse is not possible
Proper installation, operation, and maintenance helps maximize carbide die life and performance. Partnering with experienced carbide machinists is key.
How to Choose a Carbide Die Blank Supplier
Key factors in choosing a carbide block supplier:
- Range of grades and binder content options
- Consistent quality standards and ISO certification
- Dimensional accuracy and surface finish capabilities
- Custom fabrication and value-added services
- Experience with required applications
- Competitive and transparent pricing
- Lead times and inventory availability
- Customer service and technical expertise
- Domestic availability or imports/logistics services
Work with sales reps to understand capabilities and get product samples before purchasing large quantities. Check references and shop drawings/quality control. Choose reliable partners able to deliver throughout the life of production contracts.
Advantages and Limitations of Carbide Block Die Blanks
Advantages:
- Extreme hardness for long die life
- Resists abrasion, deformation, and thermal stress
- Maintains sharp cutting edges at high temperatures
- Enables large production runs with minimal maintenance
- Consistent dimensions over hundreds of thousands of cycles
- Smooth surface finish quality on extruded/drawn parts
- Withstands high compressive loads without distortion
- Chemical inertness protects against corrosion
- Can be precision machined into complex shapes
Limitations:
- Brittle with lower fracture resistance than steel
- Difficult to conventionally machine requiring diamond grinding
- Higher initial cost than fabricated steel tooling
- Production lot minimum orders on many grades
- Low supply chain availability of premium ultrafine grain sizes
- Lead times can be longer than steel depending on supplier
- Repairing/reforming damaged areas is often not possible
Carbide Grades Comparison
Grade | Hardness | Fracture Resistance | Wear Resistance | Cost |
---|---|---|---|---|
Straight Grade | Medium | Medium | Medium | Low |
Micrograin | High | Low | High | Medium |
Submicron | Very High | Very Low | Very High | High |
Coarse Grain | Medium | High | Medium | Low |
- Straight grade provides the optimal balance of properties at the lowest cost
- Micrograin offers maximum abrasion resistance for long run tools
- Submicron is best for very high precision finishing applications
- Coarse grain sacrifices some wear resistance for improved toughness
There are always tradeoffs – work closely with suppliers to match the carbide grade to the specific production needs. Getting sample blanks for testing is recommended.
Carbide vs. Steel for Die Blanks
Parameter | Carbide | Steel |
---|---|---|
Hardness | Up to 90+ HRA | Max 50 HRC |
Wear Resistance | Extremely High | Moderate |
Toughness | Brittle | Much Higher |
Machining | Very Difficult | Readily Machinable |
Typical Die Life | 100,000+ hits | <50,000 hits |
Initial Cost | Expensive | Lower Cost |
Lead Time | Weeks | Days to Week |
Typical Applications | High Production, Fine Features | Short Runs, Basic Features |
Carbide blank advantages really emerge in high volume production situations where the increase in die life offsets the higher initial cost. The hardness enables small delicate features and fine finishes. Steel is preferable for short production runs where cost and flexibility is paramount.
Carbide Die Blank Grades FAQ
Q: What is the most commonly used carbide grade for die blanks?
A: Straight grades with 8-12% cobalt binder offer the best all-around properties for most applications. KC850 and KC925 from Kennametal are popular.
Q: When does it make sense to use more expensive premium grades?
A: Micrograin and submicron grades excel in high precision finishing applications like wire drawing or plastic extrusion. The additional cost pays off in very long die life.
Q: What is the hardest grade available?
A: Carbide can be made with less than 6% cobalt for maximum hardness over 90 HRA. However, at this end of the spectrum toughness and EDM machinability suffer, making shaping complex dies difficult. 8-10% binder offers the ideal hardness/toughness balance.
Q: Can carbide be repaired or reformed once damaged?
A: Unfortunately no – once chipped or cracked the die area is permanently weakened. Some welding or epoxy repairs are possible but high pressure use is not recommended afterwards. Damaged carbide dies are generally discarded and replaced.
Q: Should surface coatings like TiN be applied to carbide dies?
A: Coatings do little to enhance the inherent wear resistance of quality carbide grades. However, they can provide lubricity benefits for non-ferrous wires and help release sticky materials. Any coating thickness impact on tolerances must be considered.
Conclusion
Carbide block die blanks enable manufacturing of durable, high precision dies for demanding metalworking applications. Their extreme hardness and wear resistance allows large production runs exceeding 100,000 hits with minimal maintenance compared to steel tooling. However, the high cost means carbide is most advantageous when high volumes justify the investment. Understanding the properties of various carbide grades is the key to selecting optimal materials based on required tolerances, production runs, and part finish requirements. Proper handling, machining, sharpening, and implementation by experienced operators helps maximize the working life of carbide dies.