Introduction
Definition of Carbide Blanks Square
Carbide blanks square refers to a type of carbide material that is shaped in a square form. These blanks are commonly used in various industrial applications, such as cutting tools, drills, and milling machines. The square shape of carbide blanks allows for precise and accurate machining, making them ideal for creating intricate shapes and designs. Additionally, carbide blanks square offer excellent hardness and wear resistance, ensuring long-lasting performance and durability. With their superior properties, carbide blanks square have become a popular choice among manufacturers and engineers for achieving high-quality and efficient machining processes.
Uses of Carbide Blanks Square
Carbide blanks square is a versatile material that finds numerous applications in various industries. One of the primary uses of carbide blanks square is in the manufacturing of cutting tools. Due to its exceptional hardness and wear resistance, carbide blanks square is ideal for producing high-quality cutting edges that can withstand the rigors of machining operations. Additionally, carbide blanks square is also used in the production of molds and dies, where its superior strength and durability ensure precise and long-lasting results. Furthermore, carbide blanks square is employed in the aerospace and automotive industries for fabricating components that require high strength and resistance to extreme conditions. Overall, the uses of carbide blanks square are vast and essential in enhancing productivity and efficiency in various industrial sectors.
Importance of Carbide Blanks Square
Carbide blanks square plays a crucial role in various industries, especially in the manufacturing sector. The importance of carbide blanks square lies in its ability to provide precise and accurate cutting edges. With its exceptional hardness and wear resistance, carbide blanks square ensures longer tool life and improved productivity. It allows for high-speed machining and reduces the need for frequent tool changes, resulting in cost savings and increased efficiency. Moreover, carbide blanks square offers excellent dimensional stability, ensuring consistent and reliable performance. Overall, the use of carbide blanks square is essential for achieving superior quality and precision in machining operations.
Properties of Carbide Blanks Square
Hardness
The hardness of carbide blanks square is a crucial factor to consider when choosing the right material for various applications. Carbide blanks square are known for their exceptional hardness, which allows them to withstand high temperatures, heavy loads, and abrasive environments. This hardness is achieved through a combination of the carbide material and the manufacturing process, resulting in a durable and long-lasting product. With their high hardness, carbide blanks square are widely used in industries such as automotive, aerospace, and machining, where strength and wear resistance are essential. Whether it’s for cutting tools, molds, or wear parts, carbide blanks square offer superior hardness that ensures optimal performance and longevity.
Wear Resistance
Carbide blanks square are known for their exceptional wear resistance. This remarkable characteristic makes them ideal for various applications where durability and longevity are crucial. The high hardness of carbide blanks square ensures that they can withstand abrasive wear, impact, and high temperatures, making them suitable for use in cutting tools, dies, and wear parts. Additionally, the wear resistance of carbide blanks square contributes to improved productivity and reduced downtime, as they require less frequent replacement compared to other materials. Overall, the wear resistance of carbide blanks square makes them a reliable choice for industries that demand high-performance materials.
Heat Resistance
Carbide blanks square are known for their exceptional heat resistance. This property makes them highly suitable for applications that involve high temperatures and thermal stress. The unique composition of carbide blanks square allows them to maintain their structural integrity even under extreme heat conditions. This heat resistance ensures that the carbide blanks square can withstand prolonged exposure to heat without deforming or losing their hardness. As a result, they are widely used in industries such as aerospace, automotive, and manufacturing, where heat resistance is a critical requirement. The outstanding heat resistance of carbide blanks square contributes to their long lifespan and reliability in demanding environments.
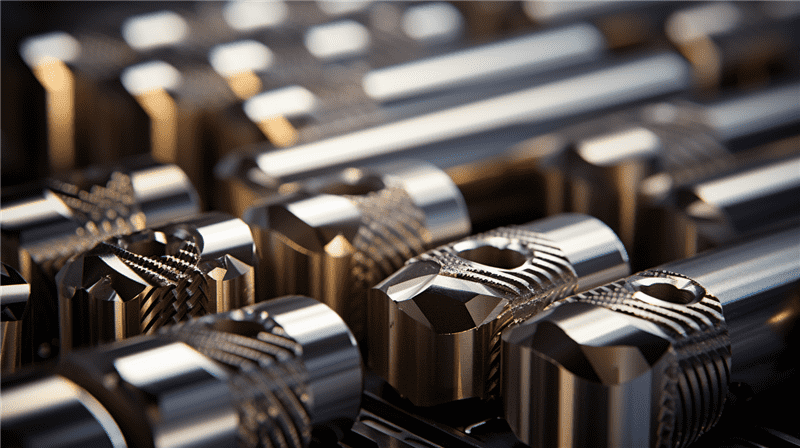
Manufacturing Process
Selection of Raw Materials
When it comes to the selection of raw materials for carbide blanks square, there are several factors to consider. The first factor is the purity of the raw material. It is important to choose a raw material that has a high level of purity to ensure the quality and performance of the carbide blanks square. Additionally, the particle size of the raw material is another important consideration. The particle size should be uniform to achieve consistent results. Furthermore, the composition of the raw material should be carefully evaluated to ensure it meets the specific requirements of the carbide blanks square. By carefully selecting the raw materials, manufacturers can produce high-quality carbide blanks square that meet the needs of various applications.
Mixing and Blending
Mixing and blending are crucial processes in the production of carbide blanks square. These processes involve combining different materials, such as tungsten carbide powder and cobalt binder, in precise proportions to create a homogeneous mixture. The mixture is then subjected to intense blending to ensure uniform distribution of the materials. This step is essential for achieving the desired properties and quality of the carbide blanks square. Additionally, the mixing and blending processes also play a significant role in controlling the grain size and structure of the carbide, which further influences the performance of the final product. Overall, proper mixing and blending techniques are vital for producing high-quality carbide blanks square with consistent properties and performance.
Compacting and Shaping
Carbide blanks square is a crucial process in the manufacturing of various industrial components. During the compacting and shaping stage, the carbide blanks are formed into the desired square shape, ensuring precision and accuracy in the final product. This process involves applying high pressure to the carbide material, which helps in achieving the required density and strength. Additionally, shaping the carbide blanks into a square shape allows for easy integration into different machinery and equipment. The compacting and shaping process plays a vital role in ensuring the overall quality and performance of the carbide blanks square.
Applications
Metalworking
Metalworking is a versatile and essential process in the manufacturing industry. One aspect of metalworking that is particularly important is the production of carbide blanks square. Carbide blanks square are precision-cut pieces of carbide material that are used in various applications, such as tooling, machining, and wear-resistant parts. These blanks are known for their high hardness, strength, and resistance to wear, making them ideal for demanding metalworking tasks. With their exceptional properties, carbide blanks square play a crucial role in achieving precise and efficient metalworking results.
Woodworking
Woodworking is a versatile and rewarding craft that involves shaping and manipulating wood to create beautiful and functional objects. One essential tool in woodworking is the carbide blanks square. This tool is used to ensure precise angles and measurements when cutting and joining wood pieces. The carbide blanks square is made of high-quality carbide, which provides durability and accuracy. Whether you are a professional woodworker or a hobbyist, having a carbide blanks square in your toolkit is essential for achieving precise and professional-looking results in your woodworking projects.
Plastic Molding
Plastic molding is a widely used manufacturing process that involves shaping plastic materials into various forms and products. It is a versatile technique that allows for the creation of complex shapes and designs with high precision and consistency. In the context of carbide blanks square, plastic molding plays a crucial role in the production of components and parts that require strength, durability, and dimensional accuracy. By using plastic molding techniques, manufacturers can efficiently produce carbide blanks square with consistent quality and performance. This process offers numerous advantages, including cost-effectiveness, design flexibility, and the ability to produce large quantities of carbide blanks square in a relatively short period of time. Plastic molding has revolutionized the manufacturing industry and continues to be an integral part of the production process for carbide blanks square and various other products.
Advantages of Carbide Blanks Square
Long Tool Life
The carbide blanks square offers exceptional tool life, especially in applications where high-speed cutting and extreme wear resistance are required. With its superior hardness and toughness, the carbide blanks square can withstand the most demanding machining operations, ensuring long-lasting performance and reduced downtime. Its advanced composition and precise manufacturing process result in a highly uniform and stable tool, delivering consistent and reliable results. Whether it’s milling, drilling, or turning, the carbide blanks square provides exceptional cutting performance, allowing for faster and more efficient machining processes. With its long tool life, manufacturers can achieve higher productivity and cost savings in the long run.
High Cutting Speed
Carbide blanks square are known for their exceptional performance in various machining applications. One of their key advantages is their ability to achieve high cutting speeds. With their superior hardness and heat resistance, carbide blanks square can withstand the intense forces and temperatures generated during high-speed cutting operations. This allows for faster material removal and increased productivity. Additionally, the high cutting speed of carbide blanks square results in improved surface finish and reduced tool wear, making them a preferred choice for precision machining tasks. Whether it’s milling, turning, or drilling, carbide blanks square deliver outstanding results when it comes to achieving high cutting speeds.
Improved Surface Finish
The use of carbide blanks square has led to an improved surface finish in various industries. Carbide blanks square are known for their high hardness and wear resistance, which allows for a smoother cutting and shaping process. This results in a finer and more precise surface finish on the workpiece. Additionally, the use of carbide blanks square reduces the occurrence of burrs and other surface defects, further enhancing the overall surface quality. With their exceptional performance and durability, carbide blanks square have become an essential tool for achieving superior surface finishes in manufacturing and machining applications.
Conclusion
Summary of Key Points
The carbide blanks square is a crucial component in various industrial applications. It is known for its exceptional hardness and durability, making it ideal for cutting and shaping operations. These square-shaped carbide blanks are manufactured using high-quality tungsten carbide material, ensuring excellent performance and longevity. They are widely used in the production of cutting tools, such as drills, end mills, and reamers, as well as in the manufacturing of wear-resistant parts, such as punches and dies. The precise dimensions and square shape of these carbide blanks allow for accurate and efficient machining processes. Overall, the carbide blanks square is an essential material that plays a vital role in enhancing productivity and precision in various industries.
Future Developments
In the realm of carbide blanks square, future developments hold great promise. Researchers and engineers are continuously working towards enhancing the performance and durability of these cutting-edge materials. Advancements in manufacturing techniques and material compositions are expected to result in carbide blanks that offer even higher precision and longer tool life. Additionally, efforts are being made to develop carbide blanks with improved resistance to wear and corrosion, further expanding their applications in various industries. As technology continues to evolve, it is anticipated that carbide blanks square will play a pivotal role in shaping the future of cutting and machining processes.
Final Thoughts
In conclusion, carbide blanks square are an essential component in various industries. Their durability, hardness, and resistance to wear make them ideal for applications that require precision and reliability. Whether used in cutting tools, molds, or wear parts, carbide blanks square deliver exceptional performance and contribute to the overall efficiency and productivity of the manufacturing process. With their superior properties, these carbide blanks square are sure to continue playing a crucial role in shaping the future of numerous industries.