Introduction
Definition of Carbide Blanks
Carbide blanks are specially designed pieces of carbide material that serve as the starting point for the manufacturing of various cutting tools. These blanks are made from a combination of tungsten carbide and cobalt, which results in a strong and durable material. The purpose of carbide blanks is to provide a solid foundation for the creation of cutting tools such as drills, end mills, and inserts. By starting with a carbide blank, manufacturers can ensure that the final cutting tool will have the necessary hardness, wear resistance, and toughness to effectively perform its intended function. Carbide blanks are essential components in the production of high-quality cutting tools used in industries such as automotive, aerospace, and manufacturing.
Importance of Carbide Blanks
Carbide blanks play a crucial role in various industries, especially in manufacturing and engineering. These high-quality materials are widely used for their exceptional hardness, durability, and resistance to wear and corrosion. The importance of carbide blanks lies in their ability to provide precision and reliability in the production of cutting tools, dies, and molds. With their superior performance and long lifespan, carbide blanks enable manufacturers to achieve high productivity and cost-effectiveness. Moreover, their excellent heat resistance makes them suitable for use in high-temperature applications. Overall, the use of carbide blanks is essential for ensuring the efficiency and quality of various industrial processes.
Applications of Carbide Blanks
Carbide blanks are versatile materials that find applications in various industries. One of the key applications of carbide blanks is in the manufacturing of cutting tools. Due to their high hardness and wear resistance, carbide blanks are ideal for producing durable and efficient cutting tools used in metalworking, woodworking, and other machining processes. Additionally, carbide blanks are also used in the production of wear parts, such as nozzles, dies, and punches, due to their ability to withstand high temperatures and extreme conditions. Furthermore, carbide blanks are utilized in the production of precision instruments and components, where their exceptional strength and dimensional stability are crucial. Overall, the applications of carbide blanks are diverse and essential in various industries, contributing to improved productivity and performance.
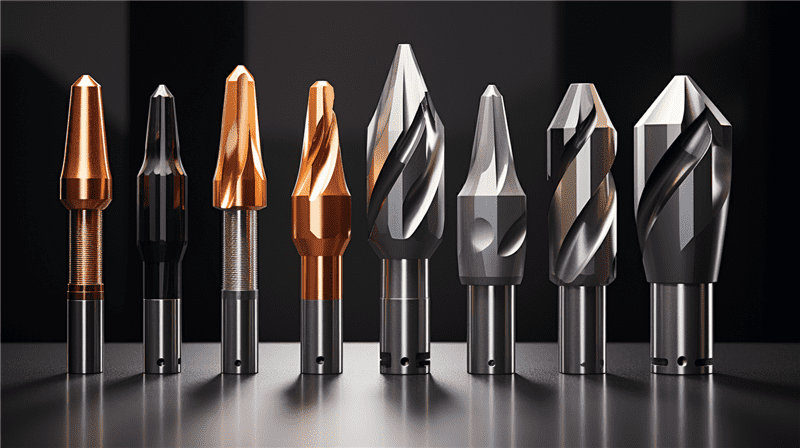
Types of Carbide Blanks
Solid Carbide Blanks
Solid carbide blanks are essential components in the manufacturing of cutting tools. These blanks are made from high-quality carbide materials, which provide excellent hardness and wear resistance. The precise dimensions and superior quality of solid carbide blanks make them ideal for applications that require high precision and durability. Manufacturers of solid carbide blanks utilize advanced production techniques to ensure consistent quality and performance. With their exceptional strength and durability, solid carbide blanks play a crucial role in the production of high-performance cutting tools used in various industries such as automotive, aerospace, and machining. Whether it’s for drilling, milling, or turning, solid carbide blanks are the go-to choice for professionals seeking reliable and efficient cutting solutions.
Brazed Carbide Blanks
Brazed carbide blanks are an essential component in the manufacturing industry, particularly in the field of cutting and machining. These blanks are made from a combination of tungsten carbide and a metal binder, resulting in a strong and durable material that can withstand high temperatures and heavy loads. The brazing process ensures a secure bond between the carbide and the binder, creating a seamless and reliable tool for various applications. Whether it’s for drilling, milling, or turning, brazed carbide blanks provide exceptional performance and precision, making them the preferred choice for many manufacturers around the world.
Indexable Carbide Blanks
Indexable carbide blanks are an essential component in the manufacturing industry. These blanks are made from high-quality carbide materials, which provide superior strength and durability. They are widely used in various applications, including metalworking, woodworking, and automotive industries. Indexable carbide blanks offer the advantage of replaceable cutting edges, which allow for easy and cost-effective tool maintenance. With their excellent wear resistance and cutting performance, these carbide blanks enable precision machining and improve productivity. Manufacturers of carbide blanks ensure strict quality control to deliver reliable and consistent products to meet the diverse needs of their customers. Whether it’s for milling, turning, or drilling operations, indexable carbide blanks play a crucial role in achieving high-quality results and optimizing production processes.
Carbide blanks manufacturers:Manufacturing Process
Selection of Raw Materials
The selection of raw materials is a crucial step in the manufacturing process of carbide blanks. The quality and properties of the raw materials directly impact the performance and durability of the final product. Manufacturers carefully choose materials that possess high hardness, strength, and resistance to wear and corrosion. Tungsten carbide, cobalt, and other alloying elements are commonly used in the production of carbide blanks. These materials are selected for their excellent mechanical properties and ability to withstand extreme conditions. By carefully selecting the raw materials, carbide blanks manufacturers ensure that their products meet the highest standards of quality and performance.
Mixing and Blending
Mixing and blending are essential processes in the manufacturing of carbide blanks. These processes involve combining different materials to create a homogeneous mixture that will be used to form the blanks. The proper mixing and blending of the materials is crucial to ensure the quality and consistency of the final product. Various techniques, such as mechanical mixing and blending, are employed to achieve the desired results. The ratio of the materials, the duration of the mixing process, and the speed of the blending equipment are carefully controlled to achieve optimal results. By effectively mixing and blending the materials, carbide blanks manufacturers can produce high-quality products that meet the specific requirements of their customers.
Compacting and Shaping
Compacting and shaping processes are crucial steps in the manufacturing of carbide blanks. These processes involve compressing and molding the carbide powder into the desired shape and size. The compacting process uses high pressure to ensure the powder particles are tightly packed together, resulting in a dense and uniform structure. The shaping process then further refines the shape and dimensions of the carbide blanks, using techniques such as pressing, extrusion, or injection molding. These processes play a vital role in determining the final quality and performance of the carbide blanks, ensuring they meet the exact specifications required by manufacturers in various industries.
Quality Control
Inspection of Raw Materials
The inspection of raw materials is a critical step in the manufacturing process of carbide blanks. It ensures that the materials used meet the required quality standards and specifications. During the inspection, various tests and measurements are conducted to assess the composition, hardness, and dimensional accuracy of the raw materials. This helps in identifying any defects or impurities that may affect the final product’s performance and durability. Additionally, the inspection process includes verifying the supplier’s certifications and documentation to ensure the authenticity and traceability of the raw materials. By conducting thorough inspections of the raw materials, carbide blanks manufacturers can maintain consistent quality and reliability in their products.
Testing of Physical Properties
Testing of physical properties is a crucial step in the manufacturing process of carbide blanks. It involves assessing various characteristics such as hardness, toughness, density, and thermal conductivity. These tests ensure that the carbide blanks meet the required standards and are suitable for their intended applications. The physical properties of carbide blanks play a significant role in determining their performance and durability. By conducting thorough testing, manufacturers can guarantee the quality and reliability of their products, providing customers with confidence in their purchase.
Dimensional Inspection
Dimensional inspection is a crucial step in the manufacturing process of carbide blanks. It ensures that the carbide blanks meet the required specifications and tolerances. During dimensional inspection, various measurements and tests are conducted to verify the accuracy and precision of the carbide blanks’ dimensions. This includes checking the length, width, thickness, and other critical dimensions. Any deviations from the specified dimensions are carefully analyzed and addressed to maintain the quality and performance of the carbide blanks. The dimensional inspection process plays a vital role in ensuring the consistency and reliability of the carbide blanks manufactured by carbide blanks manufacturers.
Advantages of Carbide Blanks
High Hardness and Wear Resistance
Carbide blanks manufacturers are known for their ability to produce high hardness and wear resistance materials. These manufacturers use advanced technologies and processes to create carbide blanks that are capable of withstanding extreme conditions and heavy usage. The high hardness of carbide blanks makes them ideal for applications in industries such as automotive, aerospace, and manufacturing. Additionally, their exceptional wear resistance ensures that carbide blanks have a longer lifespan compared to other materials. With their superior properties, carbide blanks manufactured by reputable manufacturers are highly sought after by various industries for their durability and reliability.
Excellent Heat Resistance
Carbide blanks manufacturers are known for their excellent heat resistance. This key characteristic sets them apart from other materials used in various industries. The ability of carbide blanks to withstand high temperatures without losing their shape or strength makes them highly desirable for applications where heat resistance is crucial. Whether it’s in the automotive, aerospace, or manufacturing sector, carbide blanks manufacturers play a significant role in providing durable and reliable components that can withstand extreme heat conditions. With their exceptional heat resistance properties, carbide blanks manufacturers continue to be the preferred choice for industries that demand superior performance in challenging environments.
Long Tool Life
Carbide blanks manufacturers play a crucial role in ensuring long tool life. With their expertise in producing high-quality carbide blanks, these manufacturers provide the foundation for durable and reliable cutting tools. The use of carbide blanks in tool manufacturing significantly enhances the tool’s resistance to wear and extends its lifespan. By using carbide blanks manufactured by reputable companies, tool users can benefit from tools that maintain their sharpness and cutting performance for longer periods. This not only reduces the frequency of tool replacements but also increases productivity and cost-effectiveness in various industries such as automotive, aerospace, and machining. Overall, the contribution of carbide blanks manufacturers in achieving long tool life cannot be overstated, making them essential partners for tool manufacturers and end-users alike.
Conclusion
Summary of Key Points
Carbide blanks manufacturers play a crucial role in the production of high-quality cutting tools. These manufacturers are responsible for producing carbide blanks, which are the raw materials used in the manufacturing process. The quality of carbide blanks directly impacts the performance and durability of cutting tools. Therefore, it is important to choose a reliable and reputable carbide blanks manufacturer. When selecting a manufacturer, factors such as quality control, production capacity, and technical expertise should be considered. Additionally, it is essential to ensure that the manufacturer adheres to industry standards and regulations to guarantee the consistency and reliability of the carbide blanks produced. By partnering with a trusted carbide blanks manufacturer, businesses can enhance their cutting tool production and deliver superior products to their customers.
Future Trends in Carbide Blanks
Carbide blanks manufacturers are constantly striving to stay ahead of the game by keeping up with the future trends in the industry. As technology continues to advance, the demand for carbide blanks is expected to increase. One of the key future trends in carbide blanks is the development of new materials and coatings that enhance the performance and durability of the blanks. Manufacturers are also focusing on improving the precision and accuracy of their carbide blanks to meet the growing demands of various industries. Additionally, there is a growing emphasis on sustainability, with manufacturers exploring eco-friendly production processes and materials. Overall, the future of carbide blanks looks promising, with manufacturers investing in research and development to meet the evolving needs of the market.
Closing Remarks
In conclusion, the carbide blanks manufacturers play a crucial role in the manufacturing industry. Their expertise and precision in producing high-quality carbide blanks are essential for various applications, such as cutting tools, wear parts, and molds. The continuous advancements in technology and the constant drive for innovation have enabled these manufacturers to meet the ever-growing demands of the market. With their commitment to excellence and customer satisfaction, carbide blanks manufacturers are poised to continue contributing to the success and growth of numerous industries.