Introduction
Definition of Carbide Blank
A carbide blank refers to a type of material used in various industrial applications. It is a hard and durable substance made from a combination of carbon and metal, typically tungsten or titanium. Carbide blanks are commonly used in the manufacturing of cutting tools, such as drills and end mills, due to their high hardness and wear resistance. They are also used in the production of wear parts, such as bearings and seals, where their toughness and corrosion resistance are highly valued. Overall, carbide blanks play a crucial role in enhancing the performance and longevity of various industrial components.
Uses of Carbide Blank
Carbide blank is a versatile material with a wide range of uses in various industries. One of the primary uses of carbide blank is in the manufacturing of cutting tools, such as drills, end mills, and inserts. The hardness and durability of carbide blank make it ideal for applications that require high-speed machining and precision cutting. Additionally, carbide blank is also used in the production of wear parts, such as nozzles, dies, and punches, due to its resistance to wear and corrosion. Furthermore, carbide blank finds applications in the automotive industry for the production of engine components, brake pads, and clutch plates. Its high thermal conductivity and resistance to heat make it a suitable material for these demanding applications. Overall, the uses of carbide blank are extensive, making it an essential material in various manufacturing processes.
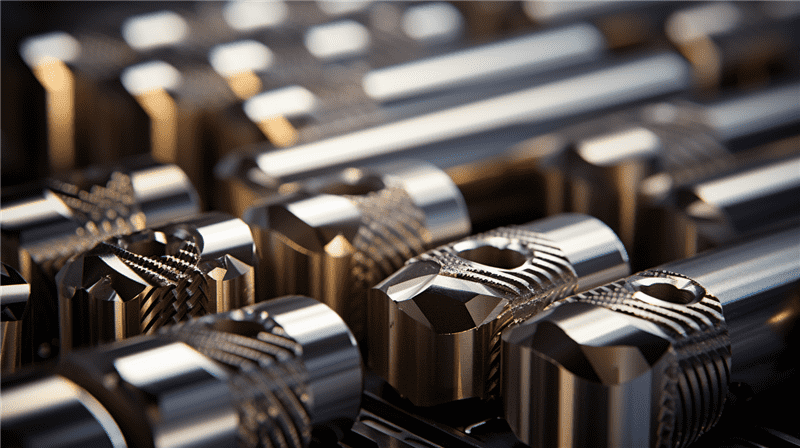
Importance of Carbide Blank in Manufacturing
Carbide blank plays a crucial role in the manufacturing industry. It is a versatile material that is widely used in various applications, such as cutting tools, molds, and wear parts. The importance of carbide blank lies in its exceptional hardness and resistance to wear, which allows for longer tool life and improved productivity. Additionally, carbide blank offers high thermal stability, ensuring consistent performance even in high-temperature environments. Its superior strength and durability make it an ideal choice for demanding manufacturing processes. Overall, the use of carbide blank in manufacturing is essential for achieving precision, efficiency, and cost-effectiveness.
Properties of Carbide Blank
Hardness
Carbide blanks are known for their exceptional hardness. This hardness is a result of the material’s unique composition and manufacturing process. With a high level of carbon and other alloying elements, carbide blanks exhibit a superior resistance to wear, abrasion, and deformation. This makes them ideal for applications that require high levels of hardness and durability, such as cutting tools, molds, and wear parts. Additionally, the hardness of carbide blanks allows for precise machining and shaping, ensuring accurate and consistent results. Overall, the hardness of carbide blanks is a key factor in their widespread use across various industries.
Wear Resistance
Carbide blanks are known for their exceptional wear resistance. This property makes them highly suitable for applications where materials are subjected to intense friction, abrasion, or erosion. The unique combination of hardness and toughness exhibited by carbide blanks allows them to withstand harsh conditions and maintain their performance over an extended period of time. Whether it is in the manufacturing of cutting tools, dies, or wear parts, carbide blanks have proven to be a reliable choice for industries that require superior wear resistance.
Heat Resistance
Carbide blanks are known for their exceptional heat resistance properties. They can withstand high temperatures without losing their hardness or strength. This makes them ideal for applications that involve intense heat, such as cutting tools, molds, and dies. The heat resistance of carbide blanks is due to the unique combination of tungsten carbide and cobalt, which gives them excellent thermal stability. Additionally, carbide blanks have low thermal expansion, allowing them to maintain their shape and dimensional accuracy even under extreme temperature fluctuations. Overall, the heat resistance of carbide blanks makes them a reliable and durable choice for various industrial applications.
Types of Carbide Blank
Solid Carbide Blank
A solid carbide blank is a high-performance cutting tool material used in various industries, including automotive, aerospace, and manufacturing. It is made from a combination of tungsten carbide and cobalt, which gives it exceptional hardness, strength, and wear resistance. Solid carbide blanks are commonly used to produce drills, end mills, reamers, and other cutting tools. They offer superior performance and longer tool life compared to traditional tool materials. With their excellent heat resistance and ability to withstand high cutting speeds, solid carbide blanks are essential for achieving precision and efficiency in machining operations.
Brazed Carbide Blank
A brazed carbide blank is a type of cutting tool that is made by brazing a carbide insert onto a steel body. The carbide insert provides the cutting edge, while the steel body provides the strength and support. This combination of materials results in a durable and long-lasting tool that is capable of withstanding high temperatures and heavy-duty cutting applications. Brazed carbide blanks are commonly used in industries such as manufacturing, automotive, and aerospace, where precision and efficiency are crucial. With their superior hardness and wear resistance, brazed carbide blanks offer improved cutting performance and extended tool life compared to traditional steel tools.
Indexable Carbide Blank
An indexable carbide blank is a type of cutting tool used in machining operations. It is made from carbide, a highly durable and heat-resistant material. The indexable design of the blank allows for multiple cutting edges, which can be rotated or replaced when they become worn or damaged. This makes indexable carbide blanks a cost-effective option for manufacturers, as they can prolong the tool’s lifespan and reduce the need for frequent replacements. Additionally, the carbide material provides excellent cutting performance and precision, making indexable carbide blanks suitable for a wide range of machining applications.
Manufacturing Process of Carbide Blank
Powder Metallurgy
Carbide blank is a crucial component in the field of powder metallurgy. Powder metallurgy is a manufacturing process that involves the production of parts and components using fine metal powders. In this process, the carbide blank plays a vital role as it serves as the starting material for the production of various carbide-based products. The carbide blank is made by compacting and sintering metal powders, resulting in a solid and durable material. With its high strength, wear resistance, and thermal stability, the carbide blank is widely used in industries such as automotive, aerospace, and cutting tool manufacturing.
Sintering
Sintering is a crucial process in the production of carbide blanks. It involves heating the compacted carbide powder to a high temperature, typically in a controlled atmosphere. During sintering, the powder particles bond together, resulting in a solid and dense carbide material. This process helps to enhance the mechanical properties of the carbide blank, such as hardness and strength. Additionally, sintering also aids in eliminating any residual porosity, ensuring the carbide blank achieves the desired dimensional accuracy and surface finish. Overall, sintering plays a vital role in the manufacturing of high-quality carbide blanks.
Grinding and Finishing
Grinding and finishing are crucial processes in the production of carbide blanks. After the carbide blanks are formed, they undergo grinding to achieve the desired shape and dimensions. This process involves the use of abrasive materials to remove excess material and refine the surface of the carbide blanks. Finishing, on the other hand, focuses on enhancing the surface quality and appearance of the carbide blanks. It involves smoothing out any rough edges or imperfections and applying a final coating or polish to achieve a uniform and glossy finish. Both grinding and finishing play a significant role in ensuring the overall quality and performance of carbide blanks.
Applications of Carbide Blank
Cutting Tools
Carbide blanks are an essential component in the manufacturing of cutting tools. These blanks are made from a combination of tungsten carbide and cobalt, which gives them exceptional hardness and wear resistance. Cutting tools made from carbide blanks are known for their superior performance and durability. They are capable of withstanding high temperatures and heavy loads, making them ideal for various cutting applications. Additionally, carbide blanks can be precision-ground to achieve the desired cutting edge geometry, ensuring precise and efficient cutting. Overall, carbide blanks play a crucial role in the production of high-quality cutting tools that are widely used in industries such as automotive, aerospace, and metalworking.
Milling Tools
Carbide blanks are an essential component of milling tools. These blanks are made from high-quality carbide material, which offers exceptional hardness and durability. When used in milling tools, carbide blanks provide superior cutting performance, allowing for precise and efficient machining operations. The use of carbide blanks in milling tools also helps to extend tool life, reducing the need for frequent replacements. With their excellent heat resistance and wear resistance, carbide blanks are the preferred choice for professionals in various industries, including automotive, aerospace, and manufacturing. Whether it’s for roughing or finishing operations, carbide blanks in milling tools deliver consistent and reliable results, making them indispensable in the field of machining.
Drilling Tools
Carbide blank is a crucial material used in the manufacturing of drilling tools. Known for its exceptional hardness and wear resistance, carbide blank is the preferred choice for creating durable and long-lasting drilling tools. The use of carbide blank in drilling tools ensures high precision and efficiency, allowing for smooth and accurate drilling operations. With its superior strength and toughness, carbide blank can withstand the extreme forces and temperatures encountered during drilling, making it an indispensable component in the drilling industry.
Advantages and Disadvantages of Carbide Blank
Advantages
Carbide blanks offer several advantages in various applications. Firstly, they have exceptional hardness, making them highly resistant to wear and abrasion. This makes carbide blanks ideal for use in cutting tools, such as drills and end mills, where durability is crucial. Additionally, carbide blanks have excellent thermal stability, allowing them to withstand high temperatures without deformation. This makes them suitable for use in high-speed machining applications. Furthermore, carbide blanks have superior strength, allowing them to maintain their shape and sharpness for extended periods of use. Overall, the advantages of carbide blanks make them a popular choice in industries such as manufacturing, automotive, and aerospace.
Disadvantages
One of the main disadvantages of carbide blanks is their high cost. Carbide is a specialized material that requires complex manufacturing processes, leading to higher production costs. Additionally, carbide blanks are more brittle compared to other materials, making them prone to cracking or breaking under certain conditions. Another drawback is that carbide blanks have limited versatility, as they are primarily used in specific applications such as cutting tools and wear-resistant parts. Finally, carbide blanks require careful handling and maintenance to ensure their longevity and performance, which can be time-consuming and costly for users.
Comparison with Other Materials
Carbide blanks are widely used in various industries due to their exceptional hardness and durability. When compared to other materials, carbide blanks offer superior performance and longevity. The high hardness of carbide blanks allows them to withstand heavy loads and resist wear, making them ideal for applications that require high precision and toughness. Additionally, carbide blanks have excellent heat resistance, ensuring their stability and reliability even in extreme temperature conditions. With their exceptional properties, carbide blanks outperform other materials in terms of strength, toughness, and overall performance, making them the preferred choice for many industrial applications.