Imagine a world where metalworking grinds to a halt. Drills snap, blades dull, and dies crumble under pressure. Thankfully, this dystopian scenario is kept at bay by the tireless workhorses of the industry: blank carbide plates.
These unassuming rectangles are the foundation for a vast array of metalworking tools. They might not be the finished product that catches the eye, but their role in shaping our metal world is undeniable. So, buckle up as we delve into the fascinating realm of blank carbide plates!
the Composition: A Powerful Cocktail of Materials
At the heart of a blank carbide plate lies a remarkable material called tungsten carbide. Here’s a breakdown of the key players:
Component | Function |
---|---|
Tungsten Carbide (WC) | This superstar ingredient boasts exceptional hardness, akin to diamonds. It’s the muscle behind the plate’s ability to withstand immense wear and tear. |
Cobalt (Co) | Imagine a skilled mechanic holding the team together. Cobalt acts as the binder, cementing the tungsten carbide grains into a cohesive unit. The percentage of cobalt influences the plate’s toughness and hardness. |
Other Additives (Optional) | Depending on the desired properties, additional elements like tantalum or vanadium might be incorporated into the mix for enhanced performance. |
Key takeaway: The specific tungsten carbide to cobalt ratio and any additional elements determine the final characteristics of the blank carbide plate.
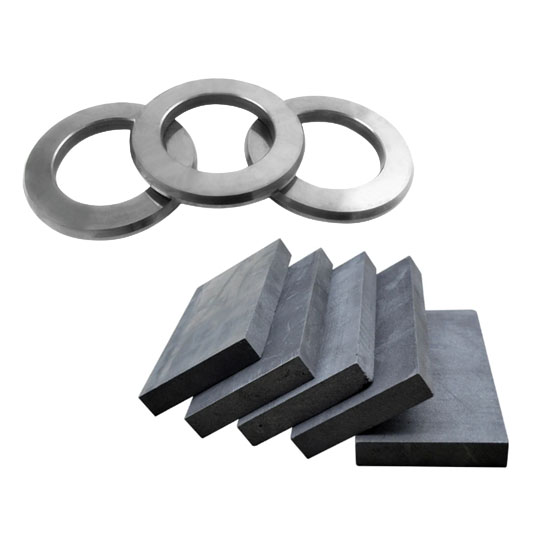
Types of Blank Carbide Plates
Blank carbide plates aren’t created equal. They come in a variety of flavors to cater to diverse industrial needs:
- Virgin Grade Plates: These are the top dogs, crafted from brand new raw materials, delivering unparalleled performance and consistency.
- Recycled Grade Plates: Eco-conscious manufacturers might opt for recycled grades, containing a portion of reprocessed carbide materials. While slightly less expensive, they might exhibit minor variations in properties.
Beyond the grade, variations can also exist in:
- Grain Size: The size of the tungsten carbide grains within the plate influences properties like toughness and wear resistance. Finer grain sizes generally translate to higher hardness but potentially lower fracture resistance.
- Coating: Some plates might be coated with additional layers like titanium nitride (TiN) to enhance specific properties like heat resistance or lubricity.
Remember: The ideal type of blank carbide plate hinges on the intended application. Consider factors like the material being worked on, the desired level of wear resistance, and budget constraints when making your selection.
Properties and Characteristics of Blank Carbide Plates
Blank carbide plates aren’t your average metal sheet. They possess a unique set of properties that make them irreplaceable in metalworking:
- Exceptional Hardness: We mentioned the diamond analogy earlier, and it holds true. Blank carbide plates boast a Rockwell hardness (a measure of resistance to permanent indentation) that surpasses even high-quality steel. This translates to the ability to tackle tough materials like hardened steel and abrasive composites with ease.
- Superior Wear Resistance: Imagine a drill bit that stays sharp for hours on end. That’s the magic of blank carbide plates. Their resistance to wear and tear allows tools fabricated from them to maintain their cutting edge for extended periods, minimizing downtime and maximizing productivity.
- High Strength: Blank carbide plates aren’t just tough; they’re incredibly strong. They can withstand immense pressure without succumbing to deformation or breakage. This makes them ideal for heavy-duty applications like metal stamping and deep-hole drilling.
- Heat Resistance: The scorching temperatures generated during metalworking processes can soften and damage conventional tools. But blank carbide plates shrug off the heat. They retain their strength and hardness even at elevated temperatures, ensuring consistent performance.
These properties, combined, make blank carbide plates the go-to material for a vast array of metalworking tools.
Applications of Blank Carbide Plates
The applications of blank carbide plates are as diverse as the metalworking industry itself. Here’s a glimpse into where you might encounter them:
Application | Example |
---|---|
Cutting Tools | Turning tools, milling inserts, drill bits, end mills, threading dies |
Wear Parts | Bushings, liners, guides, dies for stamping and forming |
Mining and Construction | Rock drilling bits, wear plates for earthmoving equipment |
Woodworking | Tips for saw blades, router bits |
Electronics | Substrates for semiconductor manufacturing |
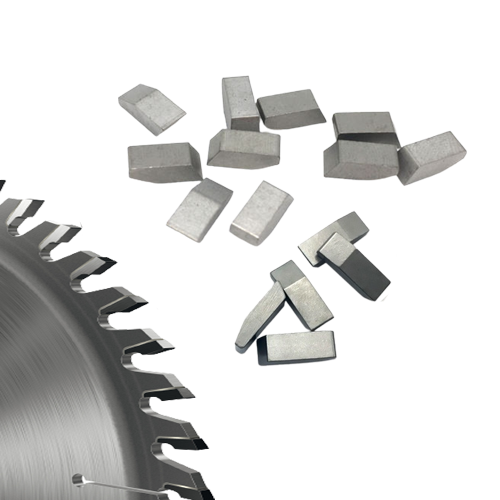
Sizes, Grades, and Standards of Blank Carbide Plates
Just like any industrial product, blank carbide plates come in a variety of specifications to cater to specific needs. Here’s a breakdown of the key factors to consider:
Sizes:
- Thickness: Blank carbide plates range in thickness from a mere fraction of a millimeter to several centimeters. Thin plates might be used for delicate cutting tools, while thicker ones are ideal for heavy-duty wear parts.
- Length and Width: Dimensions can vary greatly depending on the intended application. Manufacturers offer standard sizes, but custom options are also available for specific needs.
Grades:
As mentioned earlier, the grade of a blank carbide plate refers to the composition, particularly the tungsten carbide to cobalt ratio. Here’s a general classification:
- ISO Grades: The International Organization for Standardization (ISO) has established a system for grading blank carbide plates based on their hardness. Common grades include K-type (very hard) and H-type (tough).
- Manufacturer-Specific Grades: Many manufacturers have their own proprietary grading systems that categorize plates based on a combination of factors like hardness, toughness, and specific applications.
Standards:
Several industry standards govern the specifications and quality of blank carbide plates. These standards ensure consistency and reliability for manufacturers and users alike. Some prominent examples include:
- ISO Standards: ISO offers a range of standards for blank carbide plates, covering aspects like dimensions, tolerances, and material properties.
- ASTM International Standards: The American Society for Testing and Materials (ASTM) offers standards for various aspects of blank carbide plates, including testing methods and material performance requirements.
By understanding these specifications, you can select the most suitable blank carbide plate for your specific application.
How Much Does a Blank Carbide Plate Cost?
The cost of a blank carbide plate can vary depending on several factors:
- Size: Larger plates naturally command a higher price tag due to the increased material used.
- Grade: Plates with higher hardness or specialized properties typically cost more than their standard counterparts.
- Quantity: Bulk purchases often come with discounted pricing compared to smaller orders.
- Manufacturer and Supplier: Prices can fluctuate between different manufacturers and suppliers due to variations in production processes and market competitiveness.
As a general ballpark figure, expect to pay anywhere from a few dollars for small, standard-grade plates to hundreds or even thousands of dollars for large, high-grade plates.
Here’s a table summarizing the typical price range for blank carbide plates (prices may vary depending on factors mentioned above):
Size (mm) | Grade | Price Range (USD) |
---|---|---|
5 x 10 x 3 (small) | Standard | $1 – $10 |
10 x 20 x 5 (medium) | K-type (Hard) | $20 – $50 |
20 x 30 x 10 (large) | H-type (Tough) | $100 – $500+ |
Remember, these are just estimates. It’s crucial to consult with manufacturers or suppliers for the latest pricing information.
the Pros and Cons: Advantages and Limitations of Blank Carbide Plates
Blank carbide plates offer a multitude of advantages for metalworking applications. However, it’s essential to be aware of their limitations as well.
Advantages:
- Exceptional Durability: Blank carbide plates reign supreme in terms of wear resistance and tool life. They can withstand extended periods of use with minimal degradation, minimizing downtime and replacement costs.
- Unmatched Hardness: Their ability to tackle tough and abrasive materials surpasses that of conventional steel tools. This allows for efficient machining of challenging workpieces.
- High Strength: They can handle immense pressure without succumbing to deformation or breakage, making them ideal for heavy-duty applications.
- Heat Resistance: They retain their strength and performance even at elevated temperatures, ensuring consistent results in hot metalworking environments.
Limitations:
- High Cost: Compared to conventional steel tools, blank carbide plates carry a steeper price tag. This initial investment needs to be weighed against the benefits of extended tool life and reduced downtime.
- Brittleness: While incredibly hard, blank carbide plates can be brittle under certain conditions. Extreme impacts or sudden temperature changes might cause them to chip or fracture.
- Limited Machinability: They require specialized grinding techniques for shaping due to their extreme hardness. This can add complexity and cost to the manufacturing process.
By understanding these advantages and limitations, you can make an informed decision about whether blank carbide plates are the right choice for your specific needs.
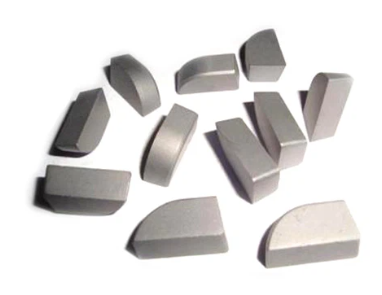
FAQs
Here are some commonly asked questions regarding blank carbide plates, presented in a clear table format for easy reference:
Question | Answer |
---|---|
What are the benefits of using blank carbide plates over other materials for metalworking tools? | Blank carbide plates offer superior wear resistance, hardness, strength, and heat resistance compared to traditional steel tools. This translates to longer tool life, the ability to tackle challenging materials, suitability for heavy-duty applications, and consistent performance at high temperatures. |
What factors should I consider when choosing a blank carbide plate? | Consider the size (thickness, length, and width) required for your application. The grade (hardness, toughness) should match the material being worked on and the desired performance. Standards (ISO, ASTM) can ensure quality and consistency. Finally, factor in cost based on size, grade, and supplier. |
Can blank carbide plates be recycled? | Yes, some manufacturers offer recycled grade blank carbide plates, which contain a portion of reprocessed carbide materials. This can be a more eco-friendly option while offering slightly lower cost compared to virgin grade plates. |
How are blank carbide plates shaped into finished tools? | Due to their extreme hardness, specialized grinding techniques are used to shape blank carbide plates into their final form. This can involve CNC grinding machines or other high-precision equipment. |
Where can I buy blank carbide plates? | Blank carbide plates are available from a variety of industrial tool suppliers and metalworking distributors. Many manufacturers also sell directly through their websites. It’s recommended to compare prices and specifications from multiple vendors before making a purchase. |
Are there any safety precautions to consider when working with blank carbide plates? | Always wear appropriate safety gear, including eye protection, gloves, and respirators when handling or grinding blank carbide plates. The fine dust generated during machining can be harmful if inhaled. |
By providing answers to these common questions, this FAQ section aims to empower readers with a well-rounded understanding of blank carbide plates and their applications.
Conclusion
Blank carbide plates may not be the most glamorous components in the metalworking world, but their role is undeniable. They are the foundation for a vast array of tools that shape our metal landscape. From the drill bits that power construction projects to the dies that stamp out car parts, blank carbide plates play a vital role in keeping the wheels of industry turning.
So, the next time you marvel at a piece of meticulously crafted metalwork, remember the unsung hero behind the scenes: the blank carbide plate.