Introduction
Definition of blank carbide plate
A blank carbide plate refers to a flat, rectangular piece of carbide material that has not been shaped or formed into a specific product. It is typically made from tungsten carbide, a hard and durable material known for its high strength and resistance to wear and corrosion. Blank carbide plates are commonly used in various industries, such as manufacturing, mining, and construction, where they are further processed and transformed into specialized components, tools, or wear-resistant parts. These plates serve as a versatile and reliable foundation for creating customized carbide products that meet specific requirements and applications.
Applications of blank carbide plate
The blank carbide plate is a versatile material that finds numerous applications in various industries. It is commonly used in the manufacturing and engineering sectors for its exceptional hardness and wear resistance. One of the key applications of blank carbide plate is in the production of cutting tools, such as drills, milling cutters, and inserts. The high hardness of the carbide plate allows these tools to withstand the extreme forces and temperatures encountered during machining processes. Additionally, blank carbide plate is also utilized in the production of wear parts, such as nozzles, dies, and punches, where its exceptional wear resistance ensures extended service life. Furthermore, the excellent thermal conductivity of the carbide plate makes it suitable for applications in heat sinks and electronic components, where efficient heat dissipation is crucial. Overall, the blank carbide plate is a valuable material that plays a vital role in various industries, offering durability, precision, and performance.
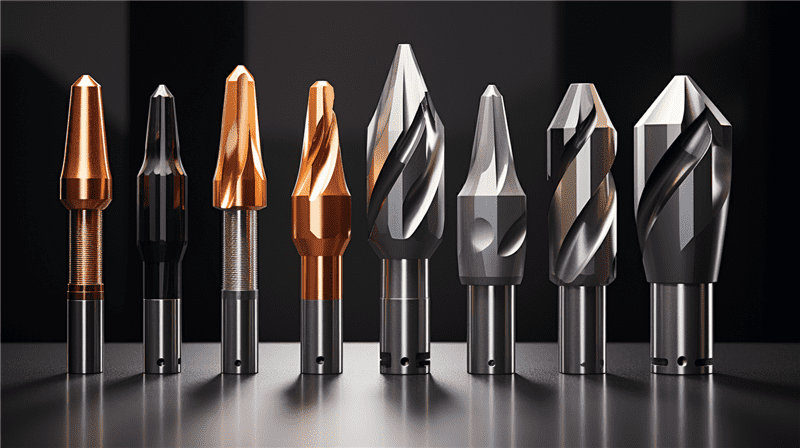
Importance of blank carbide plate in various industries
The blank carbide plate plays a crucial role in various industries due to its exceptional properties and versatility. It is widely used in manufacturing processes that require high strength, hardness, and wear resistance. The blank carbide plate is particularly important in industries such as automotive, aerospace, and oil and gas. In the automotive industry, it is used for producing cutting tools, molds, and dies, ensuring precision and durability in the manufacturing of car parts. In the aerospace industry, the blank carbide plate is utilized for fabricating turbine blades, engine components, and structural parts, contributing to the efficiency and safety of aircraft. Additionally, in the oil and gas industry, it is employed for drilling tools, valves, and wear-resistant components, enabling efficient exploration and extraction of natural resources. Overall, the blank carbide plate is of utmost importance in various industries, driving innovation, productivity, and reliability.
Composition and Properties
Materials used in blank carbide plate
The materials used in blank carbide plate are crucial for its performance and durability. Typically, blank carbide plates are made from high-quality tungsten carbide, which is known for its exceptional hardness and wear resistance. The tungsten carbide is combined with a binder material, such as cobalt or nickel, to enhance its strength and toughness. This combination results in a carbide plate that can withstand extreme conditions and provide excellent cutting performance. Additionally, the blank carbide plate may also contain trace elements or additives to further optimize its properties for specific applications. Overall, the careful selection and composition of materials play a significant role in ensuring the reliability and effectiveness of blank carbide plates.
Physical and chemical properties of blank carbide plate
Blank carbide plate is a type of material that possesses distinct physical and chemical properties. In terms of its physical properties, blank carbide plate is known for its high hardness, excellent wear resistance, and exceptional thermal stability. It is also characterized by its high melting point and low coefficient of thermal expansion. On the other hand, the chemical properties of blank carbide plate include its resistance to corrosion and oxidation, making it suitable for various industrial applications. Additionally, blank carbide plate exhibits good chemical stability and is resistant to acids, alkalis, and other harsh chemicals. Overall, the unique combination of physical and chemical properties of blank carbide plate makes it a highly desirable material in industries such as manufacturing, engineering, and construction.
Mechanical properties of blank carbide plate
The mechanical properties of blank carbide plate play a crucial role in its performance and suitability for various applications. These properties include hardness, toughness, strength, and wear resistance. The hardness of the carbide plate determines its ability to withstand abrasive forces and maintain its shape under high pressure. The toughness of the plate is important for its resistance to cracking or fracturing under impact or heavy loads. The strength of the plate determines its load-bearing capacity and ability to withstand deformation. Additionally, the wear resistance of the carbide plate ensures its durability and longevity in harsh operating conditions. Understanding and optimizing these mechanical properties is essential for achieving the desired performance and reliability of blank carbide plates in different industrial sectors.
Manufacturing Process
Raw material preparation
Raw material preparation is a crucial step in the manufacturing process of a blank carbide plate. It involves carefully selecting and preparing the raw materials that will be used to create the plate. The quality and composition of the raw materials play a significant role in determining the final properties and performance of the carbide plate. During this stage, the raw materials are inspected, sorted, and processed to remove impurities and ensure uniformity. This ensures that the resulting carbide plate will have the desired strength, hardness, and durability. Raw material preparation is a meticulous process that requires attention to detail and adherence to strict quality control measures.
Mixing and blending
Mixing and blending are crucial processes in the production of a blank carbide plate. These processes ensure that the carbide powder and other ingredients are thoroughly mixed and evenly distributed, resulting in a consistent and high-quality plate. The mixing and blending stage involves the use of specialized equipment and precise measurements to achieve the desired composition and properties of the carbide plate. It is during this stage that the carbide powder is combined with binders and additives, creating a homogenous mixture that can be pressed and sintered to form the final product. Proper mixing and blending techniques contribute to the strength, hardness, and wear resistance of the blank carbide plate, making it suitable for various industrial applications.
Compaction and shaping
Compaction and shaping are crucial steps in the production of blank carbide plates. During the compaction process, powdered carbide material is pressed into a desired shape using high pressure. This ensures that the carbide particles are densely packed together, resulting in a solid and uniform structure. Shaping, on the other hand, involves trimming and cutting the compacted carbide to achieve the desired dimensions and surface finish. Both compaction and shaping are essential for creating high-quality blank carbide plates that can be further processed and used in various industrial applications.
Types of Blank Carbide Plates
Solid carbide plates
Solid carbide plates are a type of carbide plate that are known for their exceptional hardness and durability. These plates are made from a solid piece of carbide material, which is a composite of tungsten carbide particles and a metallic binder. The unique composition of solid carbide plates gives them superior strength, making them ideal for applications that require high wear resistance and toughness. Additionally, solid carbide plates have excellent heat resistance, allowing them to withstand extreme temperatures without deformation or degradation. With their outstanding performance and reliability, solid carbide plates are widely used in various industries, including manufacturing, automotive, aerospace, and mining.
Brazed carbide plates
Brazed carbide plates are a versatile and durable solution for a wide range of industrial applications. These plates are made by brazing a layer of carbide onto a steel or other metal substrate, creating a strong bond that can withstand high temperatures and heavy loads. The carbide layer provides excellent wear resistance, making these plates ideal for use in cutting tools, wear parts, and other demanding applications. With their exceptional hardness and toughness, brazed carbide plates offer superior performance and longevity compared to traditional steel plates. Whether used in mining, construction, or manufacturing, brazed carbide plates are a reliable choice for achieving precision and efficiency in various industries.
Indexable carbide plates
Indexable carbide plates are a crucial component in various industries, including manufacturing, construction, and engineering. These plates are made from blank carbide, a high-strength material known for its exceptional hardness and resistance to wear. The blank carbide plate serves as a foundation for the indexable inserts, which are used for cutting, milling, and drilling operations. With their precise cutting edges and durable construction, indexable carbide plates offer superior performance and longevity. Whether it’s shaping metal or working with tough materials like stainless steel or cast iron, these plates provide the reliability and efficiency needed to achieve precise and consistent results. Additionally, indexable carbide plates can be easily replaced or repositioned, making them a cost-effective solution for industries that require frequent tool changes. Overall, indexable carbide plates are an essential tool for professionals seeking high-quality and efficient machining processes.
Applications
Cutting tools
A blank carbide plate is a versatile material that is commonly used in the manufacturing of cutting tools. With its high hardness and exceptional wear resistance, it is an ideal choice for applications that require precision cutting, such as in the aerospace and automotive industries. The blank carbide plate can be easily shaped and ground into various cutting tool designs, including drills, end mills, and inserts. Its superior strength and durability ensure long-lasting performance, making it a valuable asset for any cutting tool manufacturer. Whether it is for milling, turning, or drilling operations, the blank carbide plate provides the necessary strength and reliability to meet the demands of modern machining processes.
Wear parts
A blank carbide plate is a type of wear part that is commonly used in various industries. These plates are made from carbide, which is a highly durable and wear-resistant material. They are designed to withstand the harsh conditions and abrasive environments that wear parts often encounter. The blank carbide plate is typically used as a base material for manufacturing customized wear parts, such as cutting tools, dies, and punches. Its exceptional hardness and toughness make it an ideal choice for applications that require high-performance and long-lasting wear parts. With its excellent resistance to wear, corrosion, and heat, the blank carbide plate is a reliable solution for industries that rely on durable and efficient wear parts.
Mining and construction equipment
A blank carbide plate is an essential component used in mining and construction equipment. It is made from a strong and durable material known as carbide, which is known for its high hardness and resistance to wear and corrosion. The blank carbide plate is used in various applications such as cutting, drilling, and crushing rocks and other hard materials. Its superior strength and toughness make it an ideal choice for heavy-duty equipment in the mining and construction industry. With its excellent performance and reliability, the blank carbide plate plays a crucial role in enhancing the efficiency and productivity of mining and construction operations.
Advantages and Disadvantages
Advantages of using blank carbide plate
The use of blank carbide plate offers several advantages in various industries. Firstly, blank carbide plate provides exceptional hardness and wear resistance, making it ideal for applications that require cutting, drilling, and machining. Additionally, blank carbide plate has excellent thermal stability, allowing it to withstand high temperatures without deformation or loss of performance. This makes it suitable for use in high-speed machining operations. Furthermore, blank carbide plate has a long lifespan, reducing the need for frequent replacements and saving costs in the long run. Overall, the advantages of using blank carbide plate make it a valuable material for enhancing productivity and efficiency in industrial processes.
Disadvantages of using blank carbide plate
Blank carbide plates have several disadvantages that users should be aware of. Firstly, blank carbide plates are prone to chipping and cracking, especially when exposed to high impact or heavy loads. This can result in a shorter lifespan and increased maintenance costs. Additionally, blank carbide plates may not offer the same level of precision and accuracy as other materials, making them less suitable for applications that require tight tolerances. Furthermore, blank carbide plates can be more expensive compared to alternative materials, making them less cost-effective for some users. Finally, the hardness and brittleness of blank carbide plates can make them difficult to machine and shape, requiring specialized equipment and expertise. Overall, while blank carbide plates have their uses, it is important to consider these disadvantages before choosing them for a specific application.
Comparison with other materials
When comparing the blank carbide plate with other materials, it becomes evident that it offers distinct advantages. The blank carbide plate is known for its exceptional hardness and wear resistance, making it ideal for applications that require high levels of durability. Additionally, the blank carbide plate exhibits excellent thermal stability, allowing it to withstand extreme temperatures without compromising its performance. Furthermore, the blank carbide plate has superior corrosion resistance, ensuring its longevity even in harsh environments. Overall, the blank carbide plate stands out as a reliable and versatile material option for various industrial and manufacturing applications.