Carbide end mills are the unsung heroes of precision machining, cutting through metal like a hot knife through butter. If you’ve ever marveled at the intricate details of metalwork, chances are carbide end mills played a starring role. But what makes them so exceptional? Let’s dive into the nitty-gritty of carbide end mills, from their composition and types to applications, production processes, and more. This guide will not only inform but empower you to make better choices when selecting these incredible tools.
What Are Carbide End Mills?
Carbide end mills are cutting tools used primarily in CNC (Computer Numerical Control) machining. They are composed of tungsten carbide—a compound known for its durability and heat resistance—often paired with cobalt or other metals for improved performance. Think of them as the scalpel of the machining world: precise, sharp, and indispensable.
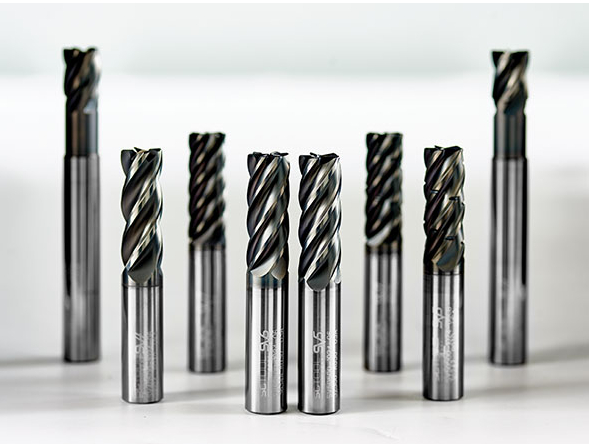
Types of Carbide End Mills
Here’s a table summarizing the main types of carbide end mills and their unique purposes:
Type of Carbide End Mill | Description | Key Use Cases |
---|---|---|
Square End Mills | Flat ends for sharp corners in cuts. | Slotting, plunge cutting, and profiling. |
Ball Nose End Mills | Rounded ends for smooth curves and contours. | 3D contour machining, mold-making, and die work. |
Corner Radius End Mills | Similar to square end mills but with rounded corners. | Enhancing durability while machining edges. |
Roughing End Mills | Serrated cutting edges for faster material removal. | Heavy-duty machining, large material removal volumes. |
Finishing End Mills | Smooth cutting edges for refined surface finishes. | Final passes to achieve high-quality surfaces. |
Tapered End Mills | Conical shapes for deep cuts and intricate details. | Machining deep molds and cavities. |
Thread Mills | Specialized for cutting internal threads. | Precision threading in hard materials. |
Single Flute End Mills | One cutting edge for maximum chip clearance. | Soft materials like plastics and aluminum. |
Multi-Flute End Mills | Multiple cutting edges for smoother finishes. | Harder materials requiring precision cuts. |
Coated End Mills | End mills coated with materials like TiAlN or DLC for added durability. | High-speed machining with improved tool life. |
Raw Material and Composition Analysis of Carbide End Mills
Carbide end mills are predominantly made from tungsten carbide powder, a material that combines toughness with heat resistance. Here’s what typically goes into them:
- Tungsten Carbide Powder: Forms the primary structure, offering hardness and wear resistance.
- Cobalt: Acts as a binder, enhancing toughness.
- Titanium Carbide: Improves thermal resistance.
- Tantalum or Niobium: Increases strength at high temperatures.
This unique blend ensures carbide end mills outperform high-speed steel (HSS) tools, especially in demanding environments.
Applications of Carbide End Mills
Industry | Specific Applications |
---|---|
Aerospace | Cutting titanium alloys for lightweight yet strong components. |
Automotive | Manufacturing engine parts and precision gears. |
Medical | Machining surgical tools and prosthetics. |
Electronics | Cutting tiny components for semiconductors and circuit boards. |
Mold and Die Making | Crafting intricate molds and dies for plastic and metal casting. |
Oil and Gas | Fabricating components for harsh, high-pressure environments. |
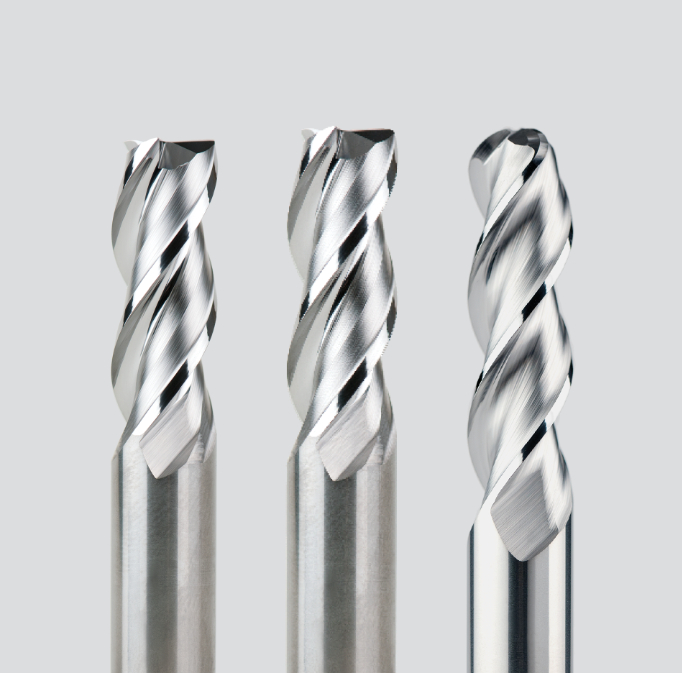
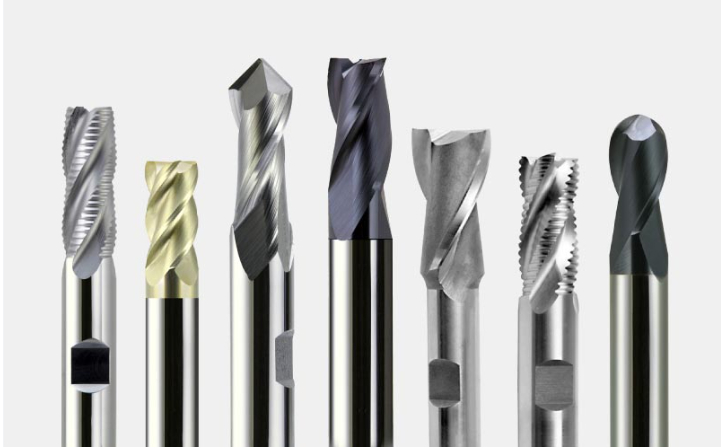

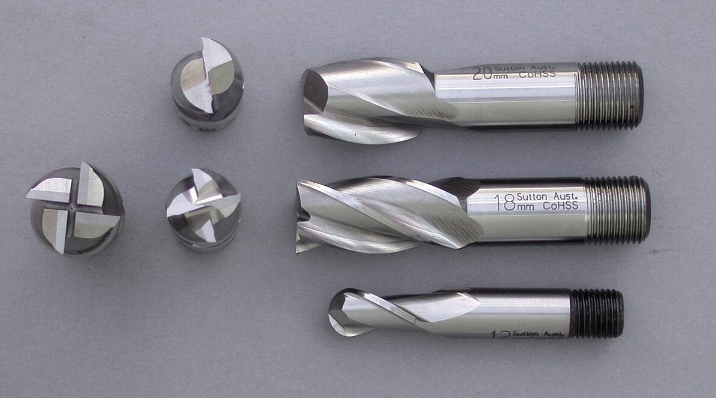
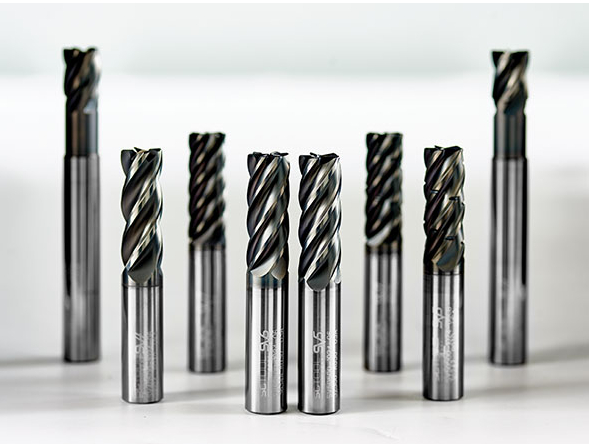
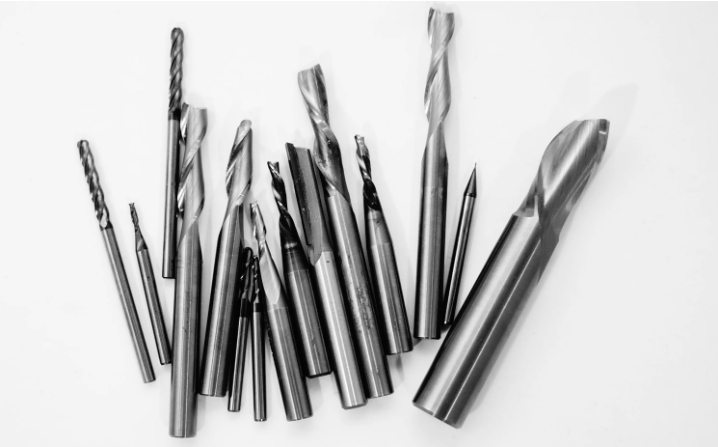
Production Process Flow of Carbide End Mills
The manufacturing of carbide end mills involves several meticulous steps:
- Powder Mixing: Tungsten carbide and other elements are blended.
- Compaction: The mixture is compressed into desired shapes.
- Sintering: High-temperature treatment fuses the materials.
- Cutting and Shaping: The raw blanks are ground into precise forms.
- Coating (Optional): Specialized coatings are applied for enhanced performance.
Material Properties of Carbide End Mills
Property | Description |
---|---|
Hardness | Extremely hard, ensuring long tool life even under high stress. |
Thermal Resistance | Withstands high temperatures during intense machining processes. |
Wear Resistance | Offers exceptional durability, reducing wear and tear. |
Strength | High compressive strength for cutting tough materials like steel and titanium. |
Composition, Properties, and Characteristics
Component | Role | Characteristics |
---|---|---|
Tungsten Carbide | Main ingredient | Hardness, wear resistance. |
Cobalt Binder | Toughness enhancer | Improves resilience and reduces brittleness. |
Titanium Additives | Thermal stability booster | Allows for higher speed machining. |
Hardness, Strength, and Wear Resistance
Metric | Value | Significance |
---|---|---|
Hardness (HRC) | 89-93 | Maintains sharp edges under stress. |
Compressive Strength | 3000 MPa | Handles heavy loads without deformation. |
Wear Resistance | High | Extends operational life, reducing replacement needs. |
Specifications, Sizes, Shapes, and Standards
Specification | Available Range | Remarks |
---|---|---|
Diameter | 0.1 mm to 20 mm | Suitable for both fine details and heavy machining. |
Length | 20 mm to 150 mm | Varies depending on depth requirements. |
Shank Type | Straight, Tapered | Ensures compatibility with various machine setups. |
Flute Count | 1 to 12 | Adjusted for material and finish requirements. |
Selecting the Right Carbide End Mills
Criteria | Considerations |
---|---|
Material Being Cut | Match end mill hardness to material. |
Coating Type | TiAlN for heat, DLC for lubrication. |
Flute Design | Single flute for plastics; multi-flute for steel. |
Cutting Speed | Higher speeds require coated tools. |
Budget | Balance cost and performance. |
Advantages vs. Limitations of Carbide End Mills
Advantages | Limitations |
---|---|
Exceptional durability | Higher initial cost compared to HSS tools. |
Heat and wear resistance | Brittle under improper usage. |
Versatile for various applications | Requires specific equipment for sharpening. |
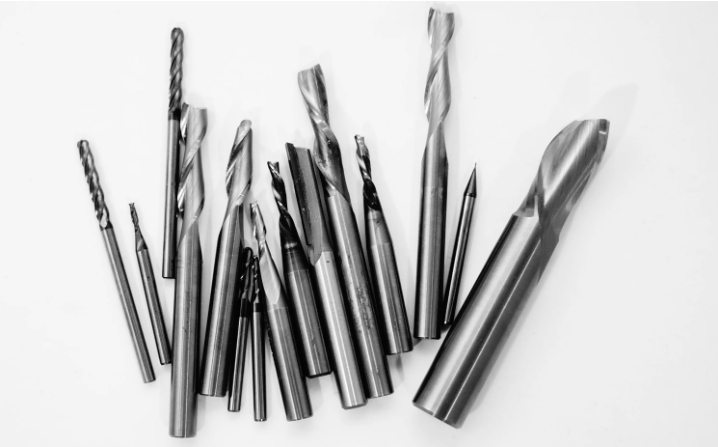
Suppliers and Pricing Details
Supplier | Pricing Range | Key Features |
---|---|---|
Kennametal | $50 – $300 | High-quality coatings, diverse range. |
Seco Tools | $60 – $400 | Specialized for aerospace and automotive. |
Sandvik | $70 – $350 | Exceptional performance in high-speed machining. |
FAQs
Question | Answer |
---|---|
Why choose carbide over HSS tools? | Carbide tools last longer, handle higher speeds, and are more resistant to wear. |
Can I use carbide end mills on wood? | Yes, but it’s overkill; HSS tools work fine for wood. |
What coatings are best for high heat? | TiAlN and AlCrN are excellent for heat-intensive applications. |
Are coated end mills worth it? | Absolutely, especially for high-speed or abrasive material machining. |