Introduction
Imagine a powerful milling machine, its spindle whirring with relentless energy, as it carves through metal with unwavering precision. Now, picture the cutting tool at the heart of this operation—a Type B carbide brazed tips, engineered to withstand the punishing forces and intermittent cutting conditions that characterize milling.
This article delves into the world of Type B carbide brazed tips, exploring their unique characteristics, advantages, and the reasons why they’re the go-to choice for tackling demanding milling applications.
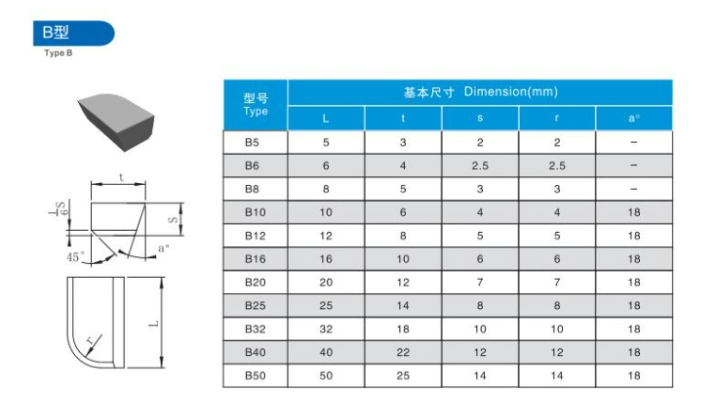
Milling: A Machining Operation Defined by Interrupted Cuts
Understanding the Challenges
Unlike turning, where the cutting tool engages the workpiece continuously, milling involves a series of interrupted cuts. The tool repeatedly enters and exits the workpiece, creating impact loads and fluctuating cutting forces that can challenge even the toughest tooling materials.
These intermittent cutting conditions demand carbide brazed tips with exceptional:
- Impact Resistance: To withstand the repeated shocks and stresses of entering and exiting the workpiece.
- Edge Strength: To prevent chipping or breakage of the cutting edge under fluctuating loads.
- Thermal Shock Resistance: To handle the rapid heating and cooling cycles that occur during interrupted cuts.
Type B Carbide Brazed Tips: Engineered for Milling Dominance
A Winning Combination of Geometry and Grade
Type B carbide brazed tips are specifically designed to excel in milling applications, thanks to their unique combination of:
- Negative Rake Angle: The defining characteristic of Type B tips, a negative rake angle means that the rake face slopes upwards towards the cutting edge. This geometry provides:
- Increased Edge Strength: The thicker cutting edge resulting from a negative rake angle offers superior resistance to chipping and breakage under impact loads.
- Improved Chip Flow: While a negative rake angle can sometimes hinder chip flow in continuous cutting, it can actually aid chip evacuation in milling, where chips tend to accumulate in the cutting zone.
- Tough Carbide Grades: Type B tips typically employ tougher carbide grades, often with higher cobalt (Co) content or additions of other elements like tantalum (Ta) or niobium (Nb). These grades offer:
- Enhanced Impact Resistance: To withstand the repeated shocks encountered in milling.
- Improved Thermal Shock Resistance: To handle the rapid temperature fluctuations that can occur during interrupted cuts.
Advantages of Type B Carbide Brazed Tips in Milling
Unlocking Performance and Productivity
The unique characteristics of Type B carbide brazed tips translate into several key advantages for milling operations:
- Extended Tool Life: Their exceptional impact resistance and edge strength result in longer tool life, reducing downtime for tool changes and lowering overall tooling costs.
- Increased Cutting Parameters: The robust nature of Type B tips allows for higher cutting speeds and feed rates, boosting productivity and reducing machining time.
- Improved Surface Finish: While not typically known for achieving the finest finishes, Type B tips, when applied correctly, can produce acceptable surface quality for many milling applications.
- Versatility in Material Selection: Type B tips are suitable for milling a wide range of materials, including steels, stainless steels, cast iron, and even some harder alloys.
Applications of Type B Carbide Brazed Tips
Where Type B Tips Shine
Type B carbide brazed tips are the go-to choice for a wide array of milling applications, including:
- Face Milling: Creating flat surfaces on workpieces.
- Shoulder Milling: Machining shoulders, steps, and slots.
- Slot Milling: Cutting slots and grooves of various widths and depths.
- Pocket Milling: Machining pockets, recesses, and internal cavities.
- Contour Milling: Creating complex contoured shapes.
Choosing the Right Type B Carbide Brazed Tip: Factors to Consider
Tailoring Your Tooling Selection
While Type B tips excel in milling, selecting the optimal tip within this category involves considering several factors:
- Workpiece Material: The material’s hardness, abrasiveness, and thermal properties influence the choice of carbide grade and coating.
- Milling Operation: The specific milling operation, such as face milling, shoulder milling, or slot milling, dictates the required tip geometry and size.
- Cutting Parameters: Desired cutting speeds, feed rates, and depths of cut influence the choice of tip geometry and grade.
- Machine Tool Capability: The rigidity and power of the machine tool can limit the choice of tip size and cutting parameters.
- Surface Finish Requirements: While not primarily known for finishing, the desired surface finish can influence the choice of tip geometry and cutting edge preparation.
Type B Carbide Brazed Tip Selection: A Simplified Guide
To assist in the selection process, here’s a table summarizing typical applications and considerations for different Type B tip geometries:
Type B Tip Geometry | Typical Applications | Key Considerations |
---|---|---|
Square Shoulder | Shoulder milling, facing, slotting | Strongest geometry, suitable for heavy cuts and interrupted cuts |
CornerRadius | Contour milling, pocketing | Provides a smoother finish than square shoulder tips |
Ball Nose | Contour milling, 3D profiling | Creates a spherical bottom in pockets, ideal for curved surfaces |
Bull Nose | Finishing, contouring | Combines a large radius with a flat bottom for semi-finishing and finishing cuts |
Beyond Geometry and Grade: Optimizing Type B Tip Performance
Factors Influencing Milling Success
While selecting the right Type B carbide brazed tip is crucial, several other factors influence milling performance:
- Cutting Fluid Selection and Application: Proper cutting fluid application can significantly impact tool life, chip evacuation, and surface finish.
- Machine Tool Rigidity and Setup: A rigid machine tool and secure workpiece holding are essential for minimizing vibration and maximizing tool life.
- Cutting Parameter Optimization: Selecting appropriate cutting speeds, feed rates, and depths of cut is crucial for balancing tool life, productivity, and surface finish.
Frequently Asked Questions about Type B Carbide Brazed Tips
Q1: Can Type B carbide brazed tips be used for materials other than metals?
A1: While primarily designed for metals, Type B tips can sometimes be used for machining some harder plastics and composites, but careful consideration of cutting parameters and tool life is essential.
Q2: What are the signs of wear on a Type B carbide brazed tip?
A2: Common wear signs include chipping or breakage of the cutting edge, excessive wear on the rake or flank face, and cratering on the rake face.
Q3: How can I maximize the tool life of my Type B carbide brazed tips?
A3: Key factors include selecting the appropriate tip geometry and grade for the application, optimizing cutting parameters, using proper cutting fluid, and ensuring a rigid machine setup.
Q4: What is the difference between a square shoulder and a corner radius Type B tip?
A4: Square shoulder tips are the strongest and most suitable for heavy cuts and interrupted cuts, while corner radius tips provide a smoother finish and are better suited for contouring and pocketing.
Q5: When would I choose a ball nose Type B tip over a bull nose tip?
A5: Ball nose tips are ideal for creating spherical bottoms in pockets and machining complex curved surfaces, while bull nose tips are better suited for semi-finishing and finishing operations where a combination of a large radius and a flat bottom is desired.