Have you ever wondered what allows drill bits to bore through concrete with ease, or how machine tools can shape impossibly hard materials? The answer lies in a remarkable material called hard metal carbide rods. These unassuming metal sticks are the workhorses of countless industries, renowned for their exceptional strength, wear resistance, and ability to withstand extreme temperatures.
This guide delves deep into the world of hard metal carbide rods, exploring their creation process, unparalleled performance characteristics, and the diverse applications that leverage their unique properties. We’ll unpack the science behind their strength, delve into the nitty-gritty of choosing the right carbide rod, and answer some burning questions that might be on your mind. So, buckle up and get ready to discover the fascinating world of these industrial champions!
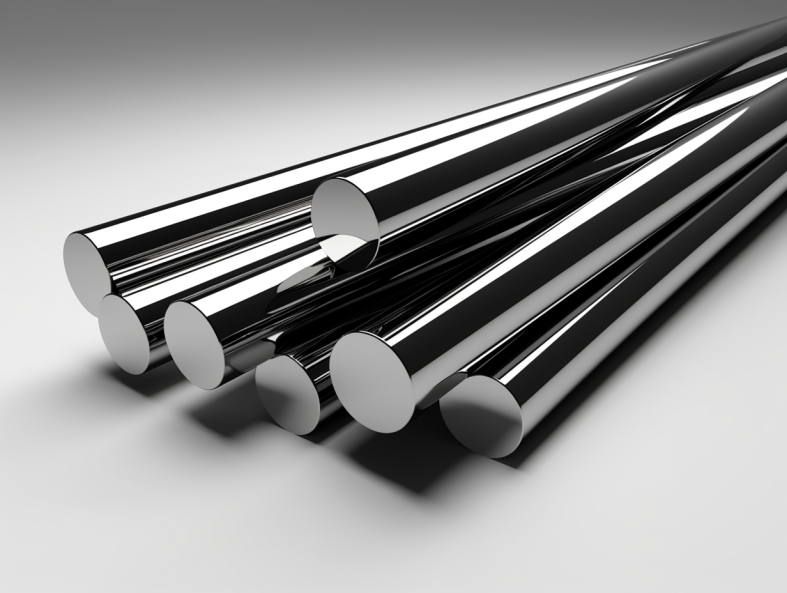
The Production Process of Hard Metal Carbide Rods
Imagine a tiny, high-pressure kitchen where the ingredients aren’t food, but finely ground tungsten carbide powder and cobalt. That’s essentially the first step in creating a hard metal carbide rod. Here’s a breakdown of the key stages involved:
- Powder Preparation: Tungsten carbide, the primary component, boasts remarkable hardness, while cobalt acts as a binding agent, holding everything together. The raw materials are crushed into an ultra-fine powder, ensuring a uniform mixture for optimal performance.
- Mixing and Compacting: The measured quantities of tungsten carbide and cobalt powder are meticulously blended to achieve a homogenous composition. This blend is then subjected to immense pressure in a hydraulic press, transforming it into a dense, green compact – the precursor to our carbide rod.
- Sintering: The green compact is like a raw, unbaked cookie. It needs a high-temperature furnace treatment, called sintering, to solidify and achieve its characteristic strength and hardness. During sintering, the cobalt binder melts, creating strong metallic bonds between the tungsten carbide particles. Imagine the green compact as a loose collection of pebbles, and sintering transforms it into a solid, tightly packed mass of rocks.
- Grinding and Finishing: The sintered rod might not be perfectly sized or have the desired surface finish. Grinding machines meticulously remove excess material, achieving precise dimensions and a smooth, polished surface.
- Quality Control: Throughout the process, stringent quality checks ensure the carbide rod meets the required specifications for density, hardness, and dimensional accuracy.
The final product is a robust, high-performance carbide rod, ready to take on the toughest industrial challenges.
Performance of Hard Metal Carbide Rods
So, what exactly makes hard metal carbide rods such industrial powerhouses? Here’s a closer look at the scientific principles behind their exceptional performance:
- Extreme Hardness: Tungsten carbide, the main ingredient, ranks second in hardness only to diamonds. This inherent hardness translates to the finished carbide rod, enabling it to resist wear and tear from even the most abrasive materials. Imagine a diamond-tipped pencil effortlessly gliding across a sheet of sandpaper – that’s the kind of wear resistance a carbide rod offers.
- Superior Strength: The combination of tungsten carbide’s inherent strength and the binding action of cobalt creates a rod that can withstand immense mechanical stress. Think of it like a microscopic web of super-strong tungsten carbide particles held together by a robust cobalt binder. This synergy allows carbide rods to handle high cutting forces and heavy loads without breaking or deforming.
- Outstanding Thermal Stability: The high melting points of tungsten carbide and cobalt contribute to the remarkable thermal stability of carbide rods. They can maintain their integrity and performance even when exposed to scorching temperatures generated during high-speed machining operations. Imagine a regular metal rod melting away like butter in a hot pan – a carbide rod, on the other hand, stays cool and collected under similar conditions.
- Excellent Wear Resistance: Due to their extreme hardness, carbide rods exhibit minimal wear and tear even after extended use. This translates to longer tool life, reduced downtime for tool changes, and significant cost savings in the long run. In the world of drill bits, a carbide bit can drill through hundreds of holes compared to a standard metal bit that might wear out after a handful of uses.
The synergy of these properties positions hard metal carbide rods as the go-to material for countless industrial applications demanding exceptional strength, wear resistance, and thermal stability.
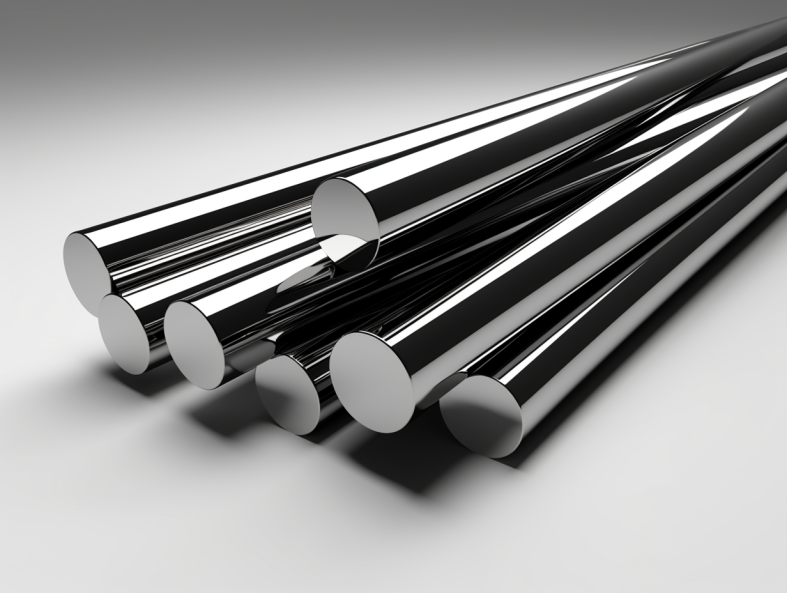
The Application of Hard Metal Carbide Rods
Hard metal carbide rods aren’t just sitting around flexing their industrial muscles. They’re actively employed in a diverse range of applications across various sectors. Here are some prominent examples:
Metalworking and Machining: Carbide rods form the core of countless cutting tools, including drill bits, milling cutters, turning tools, and end mills. Their ability to handle tough materials like steel, stainless steel, and cast iron makes them the preferred choice for high-production environments. Compared to traditional high-speed steel (HSS) tools, carbide rods offer significantly longer tool life, resulting in fewer tool changes, reduced downtime, and ultimately, increased productivity.
Imagine a scenario where you’re drilling holes in a thick steel plate. An HSS drill bit might become blunt and require replacement after a few holes. A carbide rod drill bit, on the other hand, can drill through dozens of holes in the same plate before needing a change. This translates to substantial time and cost savings, especially in large-scale metalworking operations.
Woodworking and Construction: While carbide might seem like a purely metalworking material, it also finds applications in woodworking. Specifically formulated carbide grades are incorporated into router bits, saw blades, and planning blades. These carbide-tipped blades offer superior wear resistance compared to standard steel blades. This translates to cleaner cuts, reduced chipping, and a longer blade lifespan – essential qualities for professional woodworkers and construction crews.
Imagine the frustration of a woodworker constantly battling chipped edges and a dull blade. Carbide-tipped blades provide a smoother cutting experience, cleaner finished products, and require sharpening less frequently, saving time and money in the long run.
Mining and Oil & Gas Exploration: The unforgiving environment of mining and oil & gas exploration demands tools that can withstand extreme wear and tear. Here, carbide rods are used in downhole drilling tools, percussion drilling bits, and other equipment that needs to penetrate hard rock formations and extract valuable resources. Their exceptional wear resistance and ability to handle high impact loads make them ideal for these demanding applications.
Think of drilling a hole miles deep into the earth’s crust. Regular drill bits wouldn’t stand a chance against the abrasive rock and intense pressure. Carbide-based drilling tools, however, can power through these challenges, ensuring efficient and safe extraction of resources.
Other Applications: Beyond these core areas, hard metal carbide rods find uses in various other applications, including:
- Electronics Manufacturing: For creating molds and dies used in the production of electronic components.
- Aerospace Industry: For manufacturing parts that require exceptional strength and heat resistance in harsh aircraft environments.
- Medical Devices: For crafting surgical instruments that need a combination of sharpness, durability, and biocompatibility.
These diverse applications highlight the remarkable versatility of hard metal carbide rods. They are truly the workhorses of industry, contributing to countless processes that shape our modern world.
Choosing the Right Hard Metal Carbide Rod
With so many carbide rod options available, selecting the right one for your specific application can feel overwhelming. Here are some crucial factors to consider:
- Material to be Machined: Different carbide grades are formulated to excel at machining specific materials. For instance, a carbide rod designed for steel might not perform optimally when cutting aluminum. Understanding the properties of the material you’ll be working with is paramount.
- Application Requirements: Consider the specific demands of your application. Is high wear resistance the top priority? Or do you need a carbide rod that excels at handling high impact loads? Matching the carbide grade to the specific needs of the job ensures optimal performance and tool life.
- Size and Geometry: Carbide rods come in various diameters and lengths to suit different applications. The size and geometry of the rod will depend on the specific tool it will be used for – for example, a drill bit will require a different sized rod compared to an end mill.
- Manufacturer Reputation: Opt for carbide rods from reputable manufacturers who employ strict quality control processes. This ensures consistent performance and adherence to industry standards.
Here’s an analogy to consider: Choosing the right carbide rod is like selecting the perfect athletic shoe. You wouldn’t wear running shoes for basketball, and vice versa. Similarly, tailoring the carbide rod to the specific application ensures it performs at its peak and delivers optimal results.
Consulting with a carbide rod supplier or a machining expert can be extremely helpful in navigating the selection process and finding the perfect carbide rod for your needs.
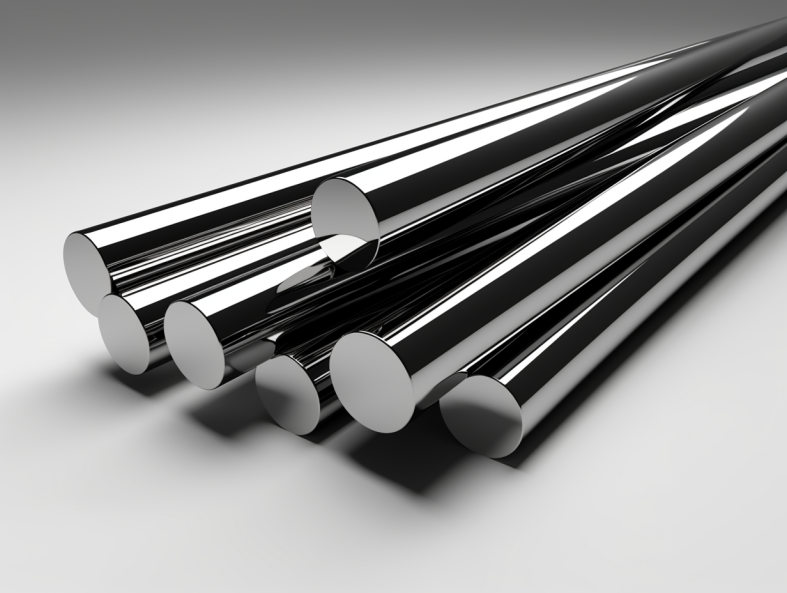
FAQs
What are hard metal carbide rods?
Hard metal carbide rods, also known as tungsten carbide rods or solid carbide rods, are rods made from a composite material. This material combines tungsten carbide powder with a metallic binder, usually cobalt. The result is an extremely hard and wear-resistant rod that can withstand high temperatures.
What are some of the properties of hard metal carbide rods?
Extremely high hardness (second only to diamond)
Excellent wear resistance
High strength and durability
Good thermal conductivity
Resistance to corrosion and deformation
What are some applications of hard metal carbide rods?
Cutting tools (drill bits, milling cutters, etc.)
Molds and dies
Wear parts ( bushings, bearings, etc.)
Mining and construction equipment
Aerospace components
What is the difference between solid carbide rods and carbide inserts?
Solid carbide rods are machined into the final tool shape. Carbide inserts are small pieces of carbide that are brazed onto a steel shank. Inserts are a more economical option for some applications.
How do I choose the right carbide rod for my application?
The type of carbide rod you need will depend on the specific application. Factors to consider include:
The material you will be working with
The desired cutting speed and feed rate
The required tool life
The machining conditions and environment
Can hard metal carbide rods be cut or machined?
Yes, carbide rods can be cut and machined using specialized diamond grinding wheels.
How long do hard metal carbide rods last?
Carbide rods can last a very long time if used properly. The lifespan will depend on the application and factors like the material being machined and the machining conditions.
Can carbide rods be recycled?
Yes, carbide rods can be recycled and used to make new carbide products.
I hope this answers some of the most common questions about hard metal carbide rods. If you have any further questions, please don’t hesitate to ask.