Carbide wear resistant plates are engineered plates made from tungsten carbide that provide excellent abrasion and impact resistance. They are commonly used in high wear applications across mining, mineral processing, steel making, cement, concrete and other industries.
Overview of Carbide Wear Resistant Plates
Carbide wear resistant plates have the following key characteristics:
- Made from tungsten carbide or chromium carbide for high hardness and wear resistance
- Embedded in a metal matrix like iron, nickel or cobalt that holds the hard carbide
- Provide resistance to sliding abrasion and high stress impact
- Used to line chutes, hoppers, cyclones, mills, separators and other high wear equipment
- Offer 5-10 times more wear life compared to regular steel plates
- Reduce wear part replacement frequency and extend service intervals
- Available in different carbide percentages, binders and sizes
Typical Applications:
- Mining – Chutes, hoppers, apron feeders, conveyors
- Mineral processing – Cyclones, mills, separators
- Cement – Chutes, air slides, separators, classifiers
- Steel – Coal transfer chutes, coke vibrating screens
- Concrete – Mixers, buckets, transfer points
Typical Sizes Available:
- Thickness: 10 mm to 50 mm
- Maximum size: 2 m x 6 m plates
- Custom plates as per design
Standards:
- ASTM A532: Carbide plates using cobalt/nickel binder
- ISO 532: Plates with iron/nickel/cobalt binder
- National standards in Australia, South Africa
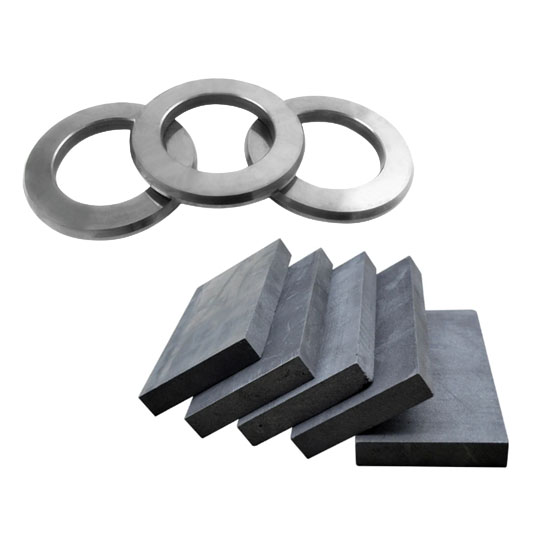
Carbide Wear Resistant Plate Composition
Carbide wear resistant plates have the following typical composition:
Component | Description |
---|---|
Carbide | Tungsten carbide WC (88%-97%) and small chromium carbide Cr3C2 (3%-12%) to provide hardness and wear resistance |
Binder | Cobalt, Nickel or Iron to hold the carbide particles in a matrix |
Carbide grain size | Macro grain carbides > 2.5 mm diameter with >90% carbide content for applications with high stress impact <br> Micro grain carbides 0.5 – 2.5 mm diameter with up to 97% carbide for maximum abrasion resistance |
Additives | Small amounts of elements like carbon, chromium, manganese, silicon added to binder to optimize properties |
Typical carbide percentages: 90%, 92%, 94% and 97%
Typical binders: Nickel at 10-12%, Cobalt at 6-8% and Iron at 3-5%
Higher binder percentages make softer and tougher plates. Lower binder give harder and stronger plates.
Properties of Carbide Wear Resistant Plates
Carbide plates have the following typical properties:
Property | Value |
---|---|
Hardness | Up to 1700 HV (Vickers) for 97% tungsten carbide which is much harder than 400 BHN of steel |
Strength | 500-1400 MPa compressive and 120-250 MPa transverse rupture strength |
Toughness | Up to 25 MPa√m for macro grain carbide plates |
Density | Around 13 gm/cc to 15 gm/cc |
Service temperature | Up to 500oC |
Electrical conductivity | Low, especially with polymer fillers |
Non-magnetic | Except with steel binder |
The extremely high hardness makes carbide plates highly resistant to abrasion while the toughness allows it to survive high impacts. The hardness is often graded similar to tool steel as C1, C2 etc. Higher C values indicate more wear resistance.
Features and Advantages
Carbide wear resistant plates provide the following features and benefits:
Features
- High tungsten carbide content
- Uniformly dispersed carbide grains
- Excellent carbide-to-binder bond
- Low porosity
- Optimal grain structure
Advantages
- Up to 10 times more wear resistant than steel
- Provide predictable wear life
- Resist abrasion and withstand impacts
- Lower wear part replacement frequency
- Extend maintenance intervals
- Reduce life cycle and downtime costs
By significantly enhancing equipment service life, carbide plates offer a very high return on investment in terms of reduced operating costs.
Carbide Plate Manufacturing Process
Carbide plates are manufactured using powder metallurgy techniques:
Steps
- Tungsten carbide and chromium carbide powders are blended with binder metals
- Small amounts of additives are included in the binder powder
- The thoroughly mixed carbide-binder powder undergoes granulation for optimal packing density and fluidity
- It is compacted into a mold at high pressures around 1000 to 1600 MPa while heated using induction heating or sintering furnaces
- The molded green compact undergoes final sintering at 1300oC to 1500oC temperature in a hydrogen atmosphere
- Additional impregnation and infiltration may be done to further enhance properties
- The sintered high-density plate undergoes machining, grinding and lapping if required to achieve dimensional accuracy and surface finish
Advantages of powder metallurgy include
- Homogeneous microstructure with uniformly distributed carbides
- Near full density and optimal carbide grain size
- Excellent consistency in properties from plate to plate
- Plates can be manufactured in a wide range of sizes as per requirement
Applications of Carbide Wear Resistant Plates
Some typical applications include:
Industry | Applications |
---|---|
Mining | Chute liners, hopper liners, truck tray liners, grizzly screen plates |
Mineral Processing | Mill liners, classifier cones, cyclone spigots, pump casings, spiral chute |
Cement | Chutes, air slides, clinker transfer, blending silo discharge |
Steel making | Sinter crusher hammers and bars, coke screen plates |
Material handling | Screw conveyors in fertilizer plants, pellet lines |
Construction | Bucket protection plates in wheel loaders, concrete transit mixer |
Other applications are in dredgers, excavators, off-shore oil and gas, biomass handling, boiler equipment and custom wear solutions.
Carbide plates and tiles lined equipment have a typical service life of 12-36 months depending on the severity of the application versus just 2-6 months from regular steel. This helps significantly reduce replacement frequency and associated costs.
Carbide Plate Suppliers
Some major global suppliers of tungsten carbide wear solutions are:
Brand | Description |
---|---|
Hardox HiCr | High chromium carbide iron-bonded wear plates from SSAB, Sweden |
Ultima | cobalt-bonded carbide plates from Castolin Eutectic / Messer |
Durmax | Carbide plates from Durum, Germany with extra nickel or chromium carbide |
Metso Carbide | several carbide grades based on grain size and binder |
ESCO | Offers Platewelder attachments to fix carbide plates on hammers, buckets |
Carbide plates are sold based on size, percentage carbide content, type of carbide grains used and properties needed for the application.
Prices range widely based on the product specifications from USD 20 per kg to over USD 100 per kg. Minimum order quantities and long lead times may be applicable.
Design Considerations for Carbide Wear Liners
Some key aspects in selection and design:
Plate thickness – thicker plates provide longer life but can crack under excessive impact. Rule of thumb is to not exceed 3 times the feed size.
Method of fixing – Mechanical fastening gives more flexibility versus welding directly. Allows for repositioning and sequential replacement of individual plates.
Using more plates – Multiple thinner plates are better than one thick plate to handle thermal stresses and impact. Allows faster replacement of individual damaged plates.
Surface finish is critical – carbide plates usually need additional machining and metal spray overlay for optimal fit. Gaps can cause uneven wear and failure.
Sealing joints – Use gaskets, GRP overlays or resilient fillets to prevent material entry behind plates which could pry them out.
Shape and coverage – Ensure proper coverage over impact zones, at transitions, corners, and edges. Custom shaping in relation to wear patterns is needed.
Supporting structure has to be rigid – loose support will result in plate cracking under impact and vibration.
Specifications
Typical specifications of carbide wear resistant plates include:
Grades
Grade | Description |
---|---|
C1 | Tungsten-chromium carbide blend with 8-12% cobalt for excellent impact resistance |
C2 | As C1 but with slightly lower toughness and higher wear resistance |
C3 | Mostly tungsten carbide with steel or nickel binder for applications with very high sliding abrasion |
Sizes
Parameter | Range |
---|---|
Thickness | 10 mm to 50 mm |
Width | Up to 2000 mm |
Length | Up to 6000 mm |
Standards
Standard | Description |
---|---|
ASTM A532 class I | Chemical composition, grain size and mechanical properties |
ASTM A532 class II | Additional transverse rupture strength criteria |
ISO 532 | Carbide grains embedded in iron group binder |
Typical properties
Grade | % Carbide | Hardness | Impact value | Wear rate |
---|---|---|---|---|
C1 | 88-92% | Up to 65 HRC | Over 25 MPa√m | Under 8 cu mm per kg |
C2 | Up to 95% | Over 70 HRC | 15-25 MPa√m | 4-7 cu mm per kg |
C3 | Over 97% | Over 75 HRC | Under 15 MPa√m | 2-4 cu mm per kg |
As hardness increases, the impact resistance goes down but wear resistance goes up. Optimal balance is needed based on the operating conditions.
Comparison of Carbide Plates
Versus Chrome / Manganese Steel
Parameter | Carbide Plate | Chrome Steel Plate |
---|---|---|
Hardness | Up to 75 HRC | Max 50 HRC |
Strength | 1000-1400 MPa | 800 MPa |
Toughness | 10 MPa√m | Up to 30 MPa√m |
Wear resistance | Excellent | Fair |
Work hardening rate | Low | High |
Service temp | 500oC | 800oC |
Price | 4-10X higher | Lower |
Applications | Optimal for high abrasion/impact | Used for low/medium wear and high temp |
Micro-grain versus Macro-grain Carbide Plates
Parameter | Micro grain < 2.5 mm | Macro grain > 2.5 mm |
---|---|---|
% Carbide | Up to 97% | 88-93% |
Hardness | Over 70 HRC | Up to 65 HRC |
Toughness | Lower at 10-15 MPa√m | Higher at over 20 MPa√m |
Wear rate | Excellent at 2-5 cu mm | Very good at 5-10 cu mm |
Price | Higher | Lower |
Applications | High abrasion but lower impacts | Excellent for applications with high impacts |
Micro-grain plates provide the highest wear resistance while macro-grain handle impacts better. Choice depends on whether the wear mechanism is predominantly sliding abrasion or stress impact.
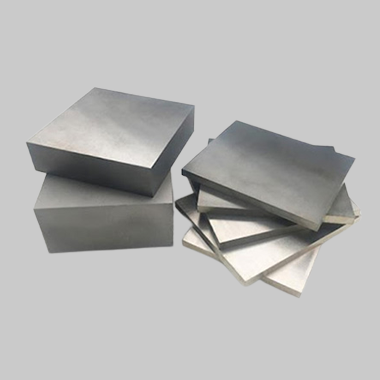
Ceramic Wear Composites Comparison
Ceramic wear composites like alumina, silicon carbide and zirconia provide the following differences to carbide plates:
Advantages
- Extreme hardness of over 2000 HV
- Maximum abrasion resistance
- High temperature stability over 800°C
- Lower density under 5 gm/cc
- Non-sparking and non-magnetic
Disadvantages
- Brittle with very low toughness
- Vulnerable to thermal shocks
- Low strength and poor impact resistance
- Higher costs for custom solutions only
Applications:
Ceramic wear plates are optimal for fine particle abrasion at high temperatures beyond the capability of carbide plates. But require very controlled operating conditions.
FAQs
Q: Why are carbide plates so expensive compared to regular steel?
A: Carbide plates have 10 times more tungsten carbide which is around 40 times more expensive than steel. They also require specialized powder metallurgy manufacturing with extensive processing for optimal properties. But provide 5 to 10 times longer service life to justify the investment.
Q: What causes carbide plates to crack or break prematurely?
A: Most cracking failures are due to Unsupported overhangs, loose backing, material packing behind plates causing prying action, excessive impacts beyond design specs, poor quality control or improper installation.
Q: How to attach carbide wear plates on equipment?
A: Mechanical fastening with high grade alloy bolts allows removal or repositioning of individual plates. Welded overlays, tungsten inert gas (TIG) welding and metal spraying provide permanent fixation but no flexibility.
Q: What maintenance is needed for carbide lined equipment?
A: Beyond routine inspections, very minimal maintenance is needed owing to long service life. Individual plates can be replaced as they gradually wear out depending on thickness loss. This avoids costly downtime from complete replacements as needed with steel liners.
Conclusion
Engineered tungsten carbide plates deliver substantial performance and economic benefits in abrasion and impact service. With optimal upfront design considering wear patterns, mechanisms and desired life, they enable process equipment to handle extreme conditions exceeding the limits of regular steels. Their widespread adoption continues to grow as customers realize the high return on investment from reduced operating costs.