Customized Blank Carbide Strips allow cost-effective machining into special purpose geometries like cutting tool inserts, precision router bits, extrusion dies and wear components. This guide details technical considerations around procuring customized tungsten, titanium carbide or ceramic blank precision ground strip stock, and then fabricating application-specific carbide parts. It also provides insights on achieving required hardness, surface finishes, tolerances and microstructures while optimizing value.
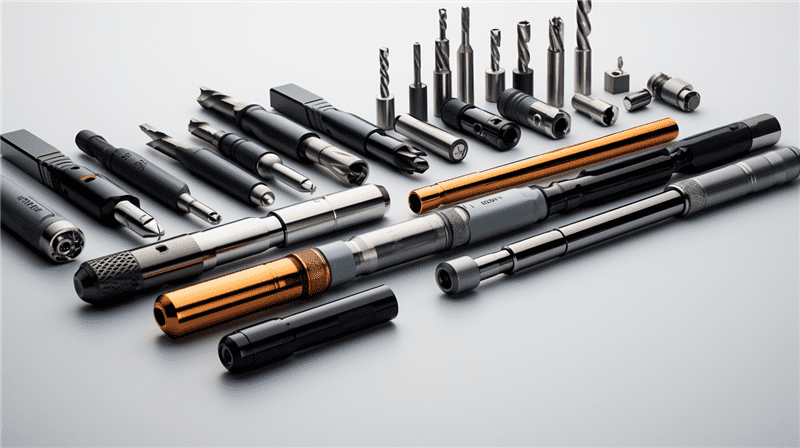
Overview
Numerous manufacturing situations demand durable parts exceeding the limits of high speed steels. Special grades of cemented carbides including tungsten carbide (WC), titanium carbide (TiC) and ceramic reinforcing blends combine hardness, wear resistance and compressive strengths tailored to uses spanning metal cutting, high speed machining, wire drawing, stamping, extrusion and high pressure forming.
Pre-sintered blank stock from qualified suppliers offers flexibility for precision grinding custom geometries on-demand, avoiding the high tooling costs of unique mold dies. Hardness can also be selectively melted and graded across carbide part cross-sections prior to finishing and edge treatments.
This guide covers the properties and production processes around carbide grades for various customized fabrication approaches in detail, allowing engineers to make informed material selection and sourcing decisions.
Carbide Grades for Customized Blanks
We first assess suitable carbide material choices:
Carbide | Hardness | Toughness | Heat Resistance | Corrosion Resistance | Price |
---|---|---|---|---|---|
Tungsten Carbide (WC) | Excellent | Fair | Excellent | Low | $$$ |
Titanium Carbide (TiC) | Excellent | Poor | Excellent | Medium | $$ |
Tantalum Carbide (TaC) | Excellent | Poor | Excellent | Low | $$$$ |
Chromium Carbide | Moderate | Good | Limited | High | $$ |
Tungsten Carbide dominates cutting applications thanks its optimized combination of extreme hardness, red hardness, compressive strength and abrasion resistance. But low thermal shock and corrosion limits usage scenarios.
Titanium Carbide offers slightly lower hardness but better chemical resistance against acidic/alkaline environments. More brittle so usually cobalt cemented.
Tantalum Carbide is chemically inert like tungsten carbide but has thermal shock limitations along with supply scarcity. Melting point of 3880°C allows very high temperature uses.
Chromium Carbide sees service in high corrosion and moderate wear situations, frequently plasma spray coated on strips. Lower hot hardness than tungsten carbides limits metal cutting performance.
Manufacturing Carbide Strips and Blanks
Sintered and metallurgically bonded carbide grades are first formed into billets and blocks, then precision ground into strips and plates to various sizes. Common specifications:
Parameter | Typical Range | Customization |
---|---|---|
Grades | Cobalt cemented tungsten/titanium/tantalum carbides + Carbonitride/Ceramic blends | Available |
Dimensions | Length 10mm to 3000mm Width 10mm to 300mm Thickness 0.5mm to 50mm | Offered |
Hardness | 40 HRC to 92 HRC, 1400 to 3100 HV, 68 to 75 Rc | Case-by-case |
Flatness | Under 50 microns deviation | Tighter by request |
Surface Finish | Down to 4-6 Ra | Mirror polishing offered |
Edge | Square, beveled, radiused corners etc | All profiles |
Tolerances | Length/Width +/- 0.2mm ; Thickness +/- 0.02mm | Tighter if needed |
Volume Discounts | 100 kg = 5% 500 kg = 8% 2500 kg = 12% | Apply for contract pricing |
While wire electrical discharge machining and cutting remains the predominant final fabrication approach for shapping blanks into specialized tooling, other methods are also possible:
- Milling allows rapid prototyping of grooves and 3D profiles
- Laser and water-jet offer intermediate quantity production
- Grinding and polishing achieves fine dimensional tolerances
- EDM Metal disintegration machining fabricates complex cavities
- Joining through vacuum brazing creates larger assemblies
Overall a wide breadth of size, hardness and tolerance combinations are possible working closely with precision carbide grinding vendors early during design concept stages.
Critical Considerations for Carbide Machining
Achieving success fabricating durable finished geometries from blank carbide stock needs careful planning:
- Match Ground Hardness to End Use Load RequirementsSofter grades allow easier machining but sabotage wear life. Harder grades prevent shaping intricacy.
- Minimize Sharp External Angles and CornersStress concentrations promote crack initiations under loads. Gradual contours strengthen components.
- Consider Strategic Surface TreatmentsAdditional PVD, CVD and DLC coatings combat chemical corrosion and release friction.
- Embed Compressive Residual StressesShot peening induces surface compressive preloads countering cracks but mars visible aesthetics.
- Match Tool Path Approach to Carbide GradeBrittle grades chip if machined too aggressively. Rigidity limits edge reaches.
- Allow Grade Margins for Grinding Heat EffectsGenerated heat can over-temper thin sections or alter underlying microstructure.
- Bake Out All Internal StressesStress relieving heat treatments minimize distortion providing dimensional stability.
Overall the optimized combination of ground hardness, achieved tolerance, surface finish and custom carbide grade is absolutely application dependent based on end use loads, prevailing stresses and operating environments.
Carbide Strip Specifications
We next overview popular sizes and grades of cobalt tungsten carbide strips kept readily in inventory for faster fabrication projects:
Grades: YG6, YG8, YG10, YG15 per Chinese standards approximating ISO K,N hardness levels
Dimensions: Cut pieces ranging from 10x10mm to 25x25mm; 30x30mm; length up to 3000mm
Hardness: 88 to 93.5 HRA; 800 to 1600 HV Vickers
Straightness: Under 50 microns per 300mm runout
Surface Roughness: Up to mirror 0.5 microns Ra finish
Flatness: Held under 6 microns peak deviation
Beyond above, additional certification possible includes hardness testing, chemical composition analysis, microphotography and other application specific qualifications.
Cost Analysis
As an advanced engineered material, fabricated carbide tooling attracts premium pricing – but unlocks performance and durability impossible otherwise. We examine typical cost structures:
Cost Component | Range |
---|---|
Carbide Strip Blanks | $25 to $100 per kg |
Grinding/Machining | $60 to $150 per hour |
Final Finishing | $40 to $250 per piece |
Exotic Geometry Surcharge | 10% to 25% markup |
Quick Turnaround | Additional 30% to 50% markup |
Small Quantity Runs | $50 minimum fabrication fee |
Therefore typical custom carbide tooling costs from $80 to $600+ in the finished state depending on complexity, tolerances, lead times and order sizes.
However given longevity measured in production cycles rather than hours, such specialty tooling provides long term value across extended campaigns.
Comparing Customized Blank Carbide Strips vs Alternatives
Tradeoffs against competing high performance materials include:
Material | Hardness | Toughness | Thermal/Chemical Resistance | Relative Price |
---|---|---|---|---|
Carbide Blanks | Best | Fair | Excellent | $$$ |
Tool Steel Blanks | Good | Better | Fair | $ |
Cubic Boron Nitride (PCBN) | Better | Poor | Excellent | $$$$ |
Natural Diamond | Excellent | Poor | Best | $$$$ |
Ceramic Oxides | Varies | Fragile | High | $-$$$$ |
Key advantages of carbide remain:
- Unmatched combination of wear life, chemical inertness and mechanical stability across temperature and loading situations, alongside proven manufacturing processes
- Allows customization of geometries, selective reinforcement and engineered microstructures tuned exactly per each application need
But limitations exist too:
- Brittle behavior limits reuse if micro-cracking or chipping initiates during service
- Poor thermal shock resistance can lead to catastrophic failures
- Relatively heavier than other structural materials on density basis
- Higher upfront fabrication costs but enables longer overall service value after break-even run hours
Engineers balance the carbide tool design envelope against desired life cycle output, operating conditions and business models before locking optimal customized blank initial investment.
Research and Development Outlook
Research directions promise exciting innovations:
Materials: Nanolaminated carbide composites with extreme hardness; Functionally graded zones
Coatings: Next generation anti-stick surfaces; Reinforced interfaces
Design: Topology optimized 3D printable geometries rivaling EDM capabilities
Modeling: Physics-based predictive analytics forecasting wear; AI-guided toolpaths
Machining: Hybridizing EDM, laser and waterjet capabilities
Inspection: Non-destructive evaluation of subsurface zone defects
Recycling: Reusing spent carbides into fresh billet feeds
Ongoing advances across these domains will enable keeping vital cutting component supply chains resilient against shortages or geopolitics.
Summary
Hard and wear resistant carbide blank strips or plates offer engineers, machinists and toolmakers affordable starting feedstock to precision grind into durable custom tooling like inserts, dies, extrusion tips and specialty cutting heads exactly optimized per specific production demands. Carbides outlast steel alternatives across impact, chemical and heat resistance – provided attention is paid to design geometries, achieving surface finishes, handling microscopic cracking risks and matching tailored grades to expected operating conditions. Working closely alongside expert vendors to select compatible compositions, establishing testing protocols and budgeting replacement spare inventory is advised. Future innovative developments across manufacturing techniques, advanced coatings and material recycling will further expand implementing customized carbide components serving indispensable roles across critical manufacturing.