Carbide blanks refer to pieces of cemented carbide that serve as a precursor material for making cutting tools and wear parts. This guide provides a detailed overview of rectangular carbide blanks including types, manufacturing process, applications, specifications, suppliers, installation, operation and maintenance procedures, selection criteria, pros and cons, and FAQs.
Overview of Rectangular Carbide Blanks
Rectangular carbide blanks consist of fine particles of carbides like tungsten carbide or titanium carbide bonded together in a cobalt matrix via liquid phase sintering.
Key properties:
- High hardness and wear resistance
- Strength at high temperatures
- Resistance to abrasion and erosion
- Structural rigidity
- Chemical inertness
Rectangular blanks are used to manufacture indexable inserts, cutting tools, wear parts and custom components needing hardness and wear resistance by techniques like grinding, EDM and drilling.
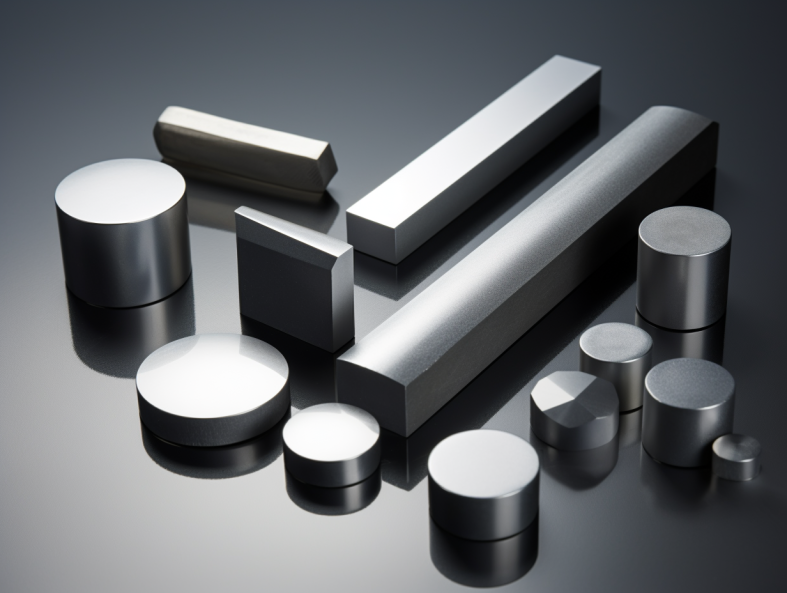
Types of Rectangular Carbide Blanks
There are several grades of rectangular carbide blanks with specific properties:
Grade | Composition | Characteristics |
---|---|---|
C1/WC-Co | 94% tungsten carbide, 6% cobalt | General purpose grade, low cost |
C2/WC-Co | 91% tungsten carbide, 9% cobalt | Improved toughness and strength |
C3/WC-Co | 88% tungsten carbide, 12% cobalt | Good resistance to abrasive wear |
C4/WC-Co | 86% tungsten carbide, 14% cobalt | Excellent toughness and shock resistance |
C5/WC-TiC-Co | 86% WC, 5% titanium carbide, 9% cobalt | High hot hardness and wear resistance |
C6/WC-TiC-TaC-Co | WC+TiC+TaC+Co | Superior wear resistance, high temperature strength |
The specific grade is selected based on the service conditions, type of wear, and desired properties.
Applications of Rectangular Carbide Blanks
Rectangular carbide blanks are used to manufacture cutting tools and wear parts across applications:
Industry | Applications |
---|---|
Automotive | Cutting and milling tools, drawing dies, gages |
Aerospace | Cutters, reamers, drilling and boring tools |
Construction | Milling tools, drill bits, saw tips |
Mining | Crushing equipment wear parts, drill bits |
Agriculture | Tillage and harvesting tools, saw chain links |
Pulp and paper | Chipper and shredder knives, pulping equipment |
Some major usage benefits:
- Hardness for cutting, shearing and forming operations
- Wear resistance for long service life
- Strength and toughness in high pressure applications
- Dimensional stability at elevated temperatures
- Corrosion and chemical resistance
Specifications of Rectangular Carbide Blanks
Rectangular carbide blanks are available with the following characteristics:
Parameter | Typical Values |
---|---|
Carbide grade | C1 to C6 |
Dimensions | Length: 50 – 200 mm Width: 20 – 80 mm Thickness: 5 – 25 mm |
Tolerances | +/- 0.2 mm |
Surface finish | Up to 0.4 μm Ra |
Parallelism | <0.02 mm |
Density | Up to 98% theoretical density |
Hardness | 88 – 93 HRA |
The composition, dimensions, tolerances, surface finish and properties can be customized as per requirements.
Manufacturing Process for Carbide Blanks
The typical steps for manufacturing rectangular carbide blanks are:
- Milling – Carbide powders are wet milled to achieve uniform fine particle size
- Drying and compaction – Powder is dried, blended and compacted into a dense part under high pressures
- Debinding – Binder materials are removed from the compact via thermal or chemical means
- Sintering – Compact is sintered at 1300-1600°C in a controlled atmosphere to achieve high density
- Grinding – The sintered blank is ground to achieve desired tolerances and surface finish
- Quality control – Each blank is inspected for defects and tested for hardness and microstructure
The process parameters are controlled to obtain optimal carbide microstructure, properties and quality.
Suppliers and Pricing of Carbide Blanks
Some of the major global suppliers and price ranges for rectangular carbide blanks:
Supplier | Location | Price Range |
---|---|---|
Element Six | Ireland | $8 – $25 per piece |
Sandvik | Sweden | $10 – $30 per piece |
Allied Carbide | USA | $6 – $15 per piece |
Tunco Manufacturing | Mexico | $4 – $12 per piece |
Miranda Tools | India | $2 – $8 per piece |
Pricing depends on:
- Carbide grade and properties
- Dimensions and tolerances
- Order quantity
- Additional fabrication or finishing
Custom blanks with special requirements command higher pricing. Volume discounts can be negotiated with suppliers.
Installation of Carbide Blank Equipment
Key considerations for installing carbide blank grinding and machining equipment:
Parameter | Guidelines |
---|---|
Foundations | Concrete foundations to dampen vibrations |
Power supply | Sufficient electrical supply and backup |
Dust extraction | Industrial dust collection systems |
Coolant systems | Chilled water supply and recycling |
Safety | Guarding, emergency stop buttons |
Handling | Hoists, cranes, bins for blank storage and transfer |
Layout | Logical flow from blank storage to finished tools |
Proper foundations, utilities supply and material handling provisions are critical for safe and optimal operation.
Operation and Maintenance of Carbide Blank Equipment
Activity | Instructions |
---|---|
Inspection | Check incoming blanks for defects and certification |
Machining | Follow SOPs and machining parameters |
Tooling | Use recommended grade inserts and tool materials |
Cooling | Maintain continuous coolant flow and temperature |
Maintenance | Periodic inspection and lubrication of moving parts |
Housekeeping | Prompt removal of grinding swarf and dust |
Safety | Ensure all guards are in place, use dust masks |
Key operation guidelines:
- Validate supplier quality and compliance certificates
- Monitor process parameters like speed, feed, depth of cut
- Schedule preventive maintenance during planned shutdowns
- Store and handle blanks carefully to prevent chipping
- Ensure proper disposal of grinding waste
Selecting a Rectangular Carbide Blank Supplier
Factors to consider when choosing a carbide blank supplier:
Criteria | Considerations |
---|---|
Quality | Consistency in achieving specifications |
Technical expertise | Knowledge of grades, ability to recommend suitable blanks |
Manufacturing process | Use of proper milling, sintering and grinding steps |
Certifications | ISO standards compliance, material certification |
R&D capabilities | Developing custom blank compositions and properties |
Logistics | On-time deliveries, minimum order quantities |
Pricing | Competitive pricing for bulk purchases |
Customer service | Responsiveness to technical queries |
It is recommended to validate supplier quality certifications, get blank samples tested independently, and seek technical advice on appropriate blank selection before procurement.
Pros and Cons of Rectangular Carbide Blanks
Pros | Cons |
---|---|
Excellent hardness and wear resistance | Brittle with lower fracture toughness than steel |
Strength and rigidity at high temperatures | High material cost compared to steel |
Good chemical and corrosion resistance | Limited availability of custom blank dimensions |
Dimensional stability in machining | Re-sharpening or coating not possible |
Enables high productivity machining | Prone to chipping if handled roughly |
Wide range of grades available | Shape limitations compared to round blanks |
The exceptional hardness and wear properties justify the use of carbide blanks for critical cutting and forming tools, wear parts and components.
FAQs
Q: What are the main powder compositions used in carbide blanks?
A: The main powder compositions are tungsten carbide, titanium carbide, tantalum carbide, and cobalt. Cobalt acts as the binder matrix for the carbide particles.
Q: What size of carbide blanks is commonly used to make cutting tool inserts?
A: Indexable carbide inserts are commonly manufactured from carbide blank sizes of 32x32mm, 25x25mm or 16x16mm using precision grinding processes.
Q: What is the role of cobalt in cemented carbide blanks?
A: Cobalt acts as the ductile binder matrix that holds the hard and brittle carbide particles together, providing toughness and strength to the carbide blank.
Q: What are some alternatives to tungsten carbide for wear applications?
A: Some alternatives include ceramics like silicon carbide and aluminum oxide. But tungsten carbide remains superior in terms of combined wear resistance and toughness.
Q: What standards are used for quality control testing of carbide blanks?
A: Key standards include ISO 513 for determination of hardness, ISO 4499 for measurement of microstructure and ISO 281 for testing grain size of cemented carbides.
Q: What are the latest innovations in carbide blank manufacturing?
A: Use of nano-structured carbide powders, advanced milling and sintering methods, and custom blank compositions with cubic carbides and carbonitrides.
Q: What is the benefit of using rectangular carbide blanks over round blanks?
A: Rectangular blanks avoid the wasted triangular corners associated with using round blanks, allowing more inserts or tools to be produced per blank.
Q: Should carbide blanks be stored in vacuum packaging?
A: Yes, vacuum packaging prevents moisture ingress which can lead to cobale leaching and oxidation, resulting in degradation of blank properties.
Q: What are the main applications of cobalt-free carbide blanks?
A: Cobalt-free blanks find use in food processing and medical applications to avoid risk of cobalt leaching and contamination.
Conclusion
Rectangular carbide blanks provide the optimum combination of hardness, wear resistance and high temperature strength required in cutting tools, wear parts and components used in demanding conditions. This guide provides a detailed overview of various grades, manufacturing methods, specifications, applications, selection criteria and FAQs related to rectangular carbide blanks to support procurement teams, engineers and designers. With their exceptional properties and microstructural stability, carbide blanks will continue to play a critical role in machining, mining, construction and other high-wear industries.