Carbide block punch blanks are an important tool used in the manufacturing industry for punching, stamping, blanking, and forming operations. This article provides a comprehensive overview of carbide block punch blanks covering applications, types, specifications, suppliers, installation, operation, maintenance, and more.
Overview of Carbide Block Punch Blanks
Carbide block punch blanks are cutting tools made of tungsten carbide that are used to cut holes or shapes out of sheet metal, plates, or strips. They are sturdy blocks of carbide that can be machined into custom shapes and sizes as per the required application.
Carbide punch blanks offer high wear resistance, impact strength, and durability compared to high speed steel blanking dies. They have excellent dimensional stability even under high temperatures and pressures of blanking processes. Carbide maintains sharp cutting edges and smooth surface finishes over long production runs.
Here are the key details about carbide block punch blanks:
- Used for punching, stamping, blanking, and forming sheet metal, plates, coils
- Made of tungsten carbide brazed to steel shank
- Custom machined into different shapes like rounds, squares, rectangles etc.
- Excellent wear resistance and impact strength
- Maintains sharp cutting edges and fine surface finishes
- Withstands high temp and pressures during blanking
- Provides accurate, smooth holes and shapes
- Long service life up to 10x that of steel blanks
- Reduces downtime due to tool changes
- Available in metric and imperial sizes
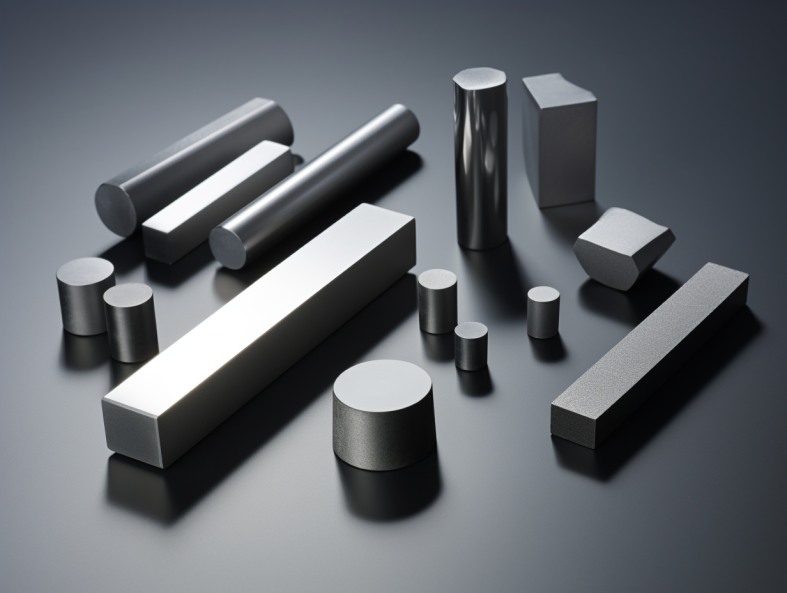
Applications of Carbide Punch Blanks
Carbide block punch blanks are widely used across several industries like automotive, aerospace, electronics, construction, and more. The major applications include:
Sheet Metal Punching
Carbide punch blanks produce clean, burr-free holes in sheet metal with excellent dimensional accuracy and surface finish. Common applications include:
- Punching holes in brackets, enclosures, motor/pump housings
- Louvering and perforating sheet metal for ventilation, aesthetics
- Cutting electrical knockout holes for junction boxes
- Blanking sheet metal components like shims, spacers, gears
Metal Stamping
Carbide blanking dies cut, form, and draw metal precisely for stamping parts like:
- Washers, gaskets, bushings, spacers
- Electronic lead frames, terminals, connectors
- Can lids, caps, aluminium tubing
- Brackets, levers, pulleys, gears
Coin Minting
Carbide provides extended die life for blanking coins compared to steel. It withstands high blanking pressures.
Automotive Industry
Carbide punch blanks produce automotive components like:
- Gaskets, seals, valve components
- Trim and ornamental pieces
- Shims, brackets, pulleys
- Wheel discs, hub caps
- Nuts, bolts, screws
Electronics Industry
Carbide is ideal for blanking precision electronic parts like:
- Semiconductor lead frames
- Connectors, micro-switches, relays
- Computer component blanks
- LCD/LED mounting brackets
Aerospace Industry
Carbide punch blanks make light-weight and durable aerospace components like:
- Engine parts and mounts
- Airframe brackets, struts
- Missile casings
- Aircraft landing gear components
Types of Carbide Block Punch Blanks
Carbide punch blanks are available in different grades, grain sizes, binding processes, and shank types to suit various blanking applications. The major types include:
By Carbide Grade
- C1 – Fine grained for general blanking of metal up to 45 HRC
- C2 – Medium grain for hardened metals up to 50 HRC
- C3 – Coarse grain for sever blanking and metals over 50 HRC
- C4 – Extra coarse grain for high shock and impact
- C5 – Ultrafine grain for thin metals below 0.5mm
By Grain Size
- Fine Grain: 1-3 microns for tight tolerance blanking
- Medium Grain: 3-6 microns for most general blanking operations
- Coarse Grain: 6-15 microns for heavy abuse blanking
By Binding Process
- Brazed Tools – Carbide brazed to steel body
- Solid Carbide – Entire tool made of carbide
By Shank Type
- Straight Shank – Parallel sides for standard holders
- Tapered Shank – For quicker tool changes
Specifications of Carbide Punch Blanks
Carbide block punch blanks are available in a wide range of standard and custom sizes, thickness, hole patterns, and layouts. Typical specifications are:
Parameter | Specifications |
---|---|
Blank Sizes | Diameters: <br>Metric – 10 to 200mm<br>Imperial – 0.5” to 8” |
Thickness | Metric – 5mm to 45mm <br>Imperial – 0.2” to 1.75” |
Hole Diameter | Metric – 0.5mm to 150mm <br>Imperial – 0.019” to 6” |
Hole Patterns | Round, square, rectangular, oblong etc. |
Hole Positions | Center, edge, corner, staggered etc. |
Tolerances | Hole dia: ±0.05mm |
Sharpness | Hole edge radius: < 0.005mm |
Surface Finish | Hole surface Ra value: < 0.4μm |
Larger carbide blocks and custom blank sizes are also available. Superior edge sharpness, hole position accuracy, surface finish, and geometric tolerances are ensured for high quality blanking.
Carbide Block Punch Blank Suppliers
Reputed manufacturers supply a complete range of standard and special carbide blanking dies. Here are some of the major global suppliers:
Company | Description |
---|---|
Advent Tool and Manufacturing | Wide range of standard and special sizes. Brazed and solid carbide. |
Appleton Mfg Division | Custom and catalog carbide blanks up to 8” dia. |
Maga Carbide Tool Co | Carbide blanks with quick delivery services. |
Silver Lake Carbide | Grades C1 to C5 brazed blanks. |
Allied Carbide | Solid carbide CNC ground blanks. |
Barker Carbide Dies | Precision carbide punch and die blanks. |
italic carbide Inc | Top quality carbide blocks up to 6” x 6”. |
Kennametal | Indexable multi-tooth carbide punches. |
Miyanaga Tool Co | Made in Japan carbide blanks. |
Ingersoll Cutting Tools | Carbide blanks and die inserts. |
Most suppliers offer standard catalog blanks in all popular sizes as well as made-to-order custom tools per customer drawings. One can select suppliers based on quality, pricing, lead times, and services.
Carbide Punch Blank Prices
Carbide blank prices depend on several factors like size, grade, grain, binding, and order quantity. Typical price ranges are:
Carbide Punch Size | Price Range |
---|---|
Up to 1” dia | $8 to $75 per piece |
1” to 2” dia | $15 to $150 per piece |
2” to 3” dia | $30 to $250 per piece |
3” to 4” dia | $50 to $350 per piece |
4” to 5” dia | $100 to $500 per piece |
5” to 6” dia | $150 to $750 per piece |
Above 6” dia | $200 to $1000 per piece |
These are approximate prices for brazed fine grain carbide blanks. Solid carbide and coarse grain blanks are costlier. Prices also differ based on quantity ordered.
How to Install Carbide Punch Blanks
Carbide block punch blanks need to be properly installed in punching machines to achieve desired blanking accuracy, speed, and tool life. Here are the main steps:
- Clean the punch press surfaces and ensure proper lubrication.
- Select the right carbide blank per hole size, shape, and metal type.
- Carefully insert the carbide block in the punch holder and tighten.
- Ensure that cutting edge protrudes slightly below bottom surface.
- Confirm alignment of die-set before initiating blanking.
- Use stripper plates to eject cut blanks and avoid re-cutting.
- Set optimal punching speed, clearance, and stripper pressure.
- Start with a few test blankings and inspect cut quality.
- Make any necessary adjustments before starting production.
The carbide block should fit securely in the punch holder. The tip clearance, die alignment, and stripper plates should be set accurately for clean blanking.
How to Operate Carbide Punch Blanks
Carbide block punch blanks need to be operated with care for best performance. Here are some guidelines:
- Run machine at optimal speeds – high speeds increase tool life.
- Use proper punch tip clearance – start with 5-10% of metal thickness.
- Set adequate stripper plate pressure for clean part ejection.
- Ensure steady feed of lubricant during punching operation.
- Maintain uniform contact between punch and metal.
- Avoid excessive vibration or impact loads on carbide blank.
- Check for burrs, galling, weartracks – adjust clearances if needed.
- Do not exceed maximum stroke rate of the punch press.
- Monitor tool wear and change punch on reaching discard size.
- Replace worn stripper plates to prevent scoring on blanks.
Proper speeds, feeds, and clearances help achieve the rated carbide tool life and prevent premature failure. Timely changing of worn punches reduces scrap rate.
Maintenance of Carbide Punch Blanks
Carbide block punch blanks require minimal maintenance for optimal blanking performance:
- Clean punch tip before inserting using solvents. Avoid handling cutting edge.
- Brush away any metal particles stuck on punch face or cutting edge.
- Check for any cracks and change punch blank if found.
- Measure wear land size and replace if beyond discard size.
- Lightly polish very small nicks on edge using fine emery cloth.
- Properly store punches in marked racks to prevent damage.
- Avoid contact with any chemicals that can corrode carbide.
- Re-sharpening of carbide blanks is typically not economical.
With routine inspection and replacement of worn tooling, carbide punches provide predictable production life. Proper handling and storage preserves the precision ground carbide blanks.
How to Select a Reliable Carbide Punch Blank Supplier
Choosing a good carbide blank supplier is vital for obtaining high quality, durable punching tools. Here are important factors to consider:
Parameter | What to Look For |
---|---|
Carbide Grades | Reputed brand carbide rod sources |
Production Facilities | Stringent quality control standards |
Design Capabilities | Custom engineering of complex blanks |
Dimensional Accuracy | Consistent hole size, position, sharpness |
Delivery Reliability | On-time shipments of tools |
Pricing | Reasonable prices for standard and custom blanks |
Technical Support | Guidance on tool selection, troubleshooting |
Customer Service | Quick response to queries and concerns |
Select an established carbide blanking tool manufacturer with in-house engineering expertise, strict process controls, and proven customer service. Getting all punch requirements met by a single source reduces manufacturing risks.
Advantages of Carbide Block Punch Blanks
Carbide blanking dies offer unique performance advantages over conventional tool steel punches:
- Up to 10x longer tool life due to carbide’s wear resistance
- Maintains dimensional accuracy of holes for longer runs
- Provides uniform sharpness resulting in burr-free blanks
- Withstands higher punching speeds and temperatures
- Lower tooling costs over large production volumes
- Smooth surface finish and high quality of punched holes/forms
- Consistent hole size and positional accuracy over tool life
- Carbide has higher impact strength than steel
- Requires lower maintenance due to longer service life
The extended service life and wearing properties of carbide minimize secondary operations like de-burring. The exceptional durability of carbide punches lowers the overall cost per punched part.
Limitations of Carbide Block Punch Blanks
Despite the benefits, carbide blanking dies also have certain limitations:
- Higher initial tooling cost than steel punches
- Not suitable for short production runs
- Brittle material can chip at high loads or incorrect use
- Re-sharpening is not practical
- Limited size availability over 6” diameter
- Carbide grades need to be matched to application
- Brazed tools have lower temperature limit than solid carbide
- Not designed for highly abrasive or gummy metals
- Larger hole sizes need indexable multi-tooth carbide punches
The blanking process needs to be set correctly to prevent tool fracture or chipping. Proper carbide grade selection is critical for optimal wear life and performance.
Choosing Between Solid vs Brazed Carbide Blanks
Parameter | Solid Carbide Blanks | Brazed Carbide Blanks |
---|---|---|
Construction | Entirely made of carbide | Carbide tip brazed to steel body |
Cost | More expensive | Lower cost |
Strength | Highest strength | Slightly lower strength |
Thermal properties | Withstands higher temp | Lower temp limit of braze alloy |
Sizes available | Smaller sizes | Can produce larger blanks |
Lead time | Longer | Shorter |
Applications | Critical tolerance blanking | Most general purposes |
Solid carbide blanks offer ultimate strength for high precision applications but have higher cost. Brazed tools provide cost-effective performance for most applications. The choice depends on blanking requirements, budget, and lead time.
Comparing Fine vs Coarse Grain Carbide Blanks
Parameter | Fine Grain Blanks | Coarse Grain Blanks |
---|---|---|
Carbide grain size | 1-3 microns | Over 6 microns |
Hardness | Higher hardness | Slightly lower hardness |
Wear resistance | Lower wear rate | Faster wear |
Impact strength | May chip under high loads | Higher toughness |
Cutting edge | Excellent sharpness | Slightly blunter edge |
Surface finish | Superior hole finish | Marginally rougher finish |
Cost | More expensive | Lower cost |
Applications | Tight tolerance blanking | Severe blanking conditions |
Fine grain carbide maintains sharper edges and is better for precision work. Coarse grain has higher impact strength suited for abusive blanking on hard metals.
Carbide vs Steel Punch Blanks
Parameter | Carbide Blanks | Steel Blanks |
---|---|---|
Material | Carbide brazed to steel | High speed or alloy steel |
Hardness | Harder, ~90 HRA | Softer, ~60 HRC |
Strength | Very high | Moderate |
Wear rate | Low wear | Undergoes faster wear |
Tool life | 10-20x longer | Short life |
Impact resistance | Prone to chipping | Higher thoughness |
Cutting sharpness | Excellent | Lower edge sharpness |
Dimensional stability | Superior hole size consistency | Hole size grows with wear |
Surface finish | Fine finish | More burrs and roughness |
Cost | Higher | Lower initial cost |
Applications | High production, precision blanking | Short runs, less critical work |
Carbide blanking punches are better suited for long runs where tool life and hole quality matter. Steel punches have lower upfront cost for short runs or prototype work.
FAQ
Q: What metals can carbide punch blanks effectively blank?
A: Carbide blanks can punch sheet metals and plates up to 65 HRC including steel, stainless steel, aluminum, copper, brass, titanium, and super alloys. The carbide grade must be properly selected based on work material.
Q: What press tonnages are required for carbide block punching dies?
A: Carbide blanks require a minimum press capacity of 25 to 35 tons for adequate blanking pressure. Higher tonnages may be needed for larger hole sizes, thicker metal gauges, and difficult materials.
Q: How are custom carbide block sizes and hole patterns made?
A: Carbide suppliers use CNC grinders, EDM, and laser technology to machine blanks from standard carbide blocks as per customer drawings. Complex geometries can be produced.
Q: Should carbide punch blanks be re-sharpened or discarded?
A: Re-sharpening brazed carbide blanks removes its alloy binder weakening it. It is better to use the tool until recommended discard size and replace with new punches.
Q: What is the typical production life of carbide blanking dies?
A: Properly applied carbide blanks produce over 100,000 to 500,000 pieces depending on hole size, material, and other factors. Steel punches average 10,000 to 50,000 hits.
Q: How does solid carbide compare to brazed carbide for blanking?
A: Solid carbide is stronger but costlier. Brazed tools with proper tip-shank clearance provide cost-effective performance for most blanking applications.