Uncoated carbide inserts are cutting tools made from cemented carbide that do not have any additional coatings applied to them. They are used for machining applications such as turning, boring, grooving, and cutoff operations.
Overview of uncoated carbide inserts
Uncoated carbide inserts provide good wear resistance and machining performance for many applications. They are more economical compared to coated carbide inserts but may not achieve the same level of tool life or performance in very demanding cutting operations.
Advantages of Uncoated Carbide Inserts:
- More economical than coated inserts
- Sufficient tool life and cutting performance for many applications
- Can withstand high cutting speeds and temperatures
- Good all-around inserts usable for roughing and finishing
Disadvantages of Uncoated Carbide Inserts:
- Not as wear-resistant as coated inserts in very tough machining
- May experience crater wear, edge breakdown in continuous cuts
- Limited suitability for light depths of cut below 0.5mm
Key Properties:
- Made of cemented tungsten/titanium carbide
- Hardness of 86 to 93.5 HRA (Rockwell A scale)
- Withstand high temperatures up to 1000°C
- Heat resistance, wear resistance properties
Uncoated carbide is ideal for interrupted cuts and medium to heavy machining at low speeds where high edge strength is needed. For very high-speed machining or finishing passes, coated carbide often performs better.
Types of Uncoated Carbide Insert Grades
There are several uncoated carbide grades used for inserts, classified by material composition and application:
Grade | Description | Key Properties | Applications |
---|---|---|---|
C1 to C5 | Straight tungsten carbides | Toughness, shock resistance | Interrupted rough cuts |
P10 to P50 | Mixed/medium grains | Balance of strength and toughness | General machining |
M10 to M40 | Fine micrograin carbides | Very wear-resistant, heat resistant | Finishing to semi-finishing |
The grain size typically decreases from C to M grades while hardness and wear resistance increases. Finer grains improve surface finish but are more prone to chipping.
ISO Standard Grades
Many uncoated carbide inserts conform to ISO standardized grades based on composition and application area:
ISO Grade | Description |
---|---|
ISO C720 | For steel turning, medium resistance, interrupted cuts |
ISO C750 | For steel/cast iron, good resistance, larger depths |
ISO K10 | High hardness/toughness for hard materials |
ISO K20 | Very high heat/wear resistance grade |
ISO P10-P50 | Universal/general machining grades |
ISO M10-M40 | For finishing operations requiring good surface finish |
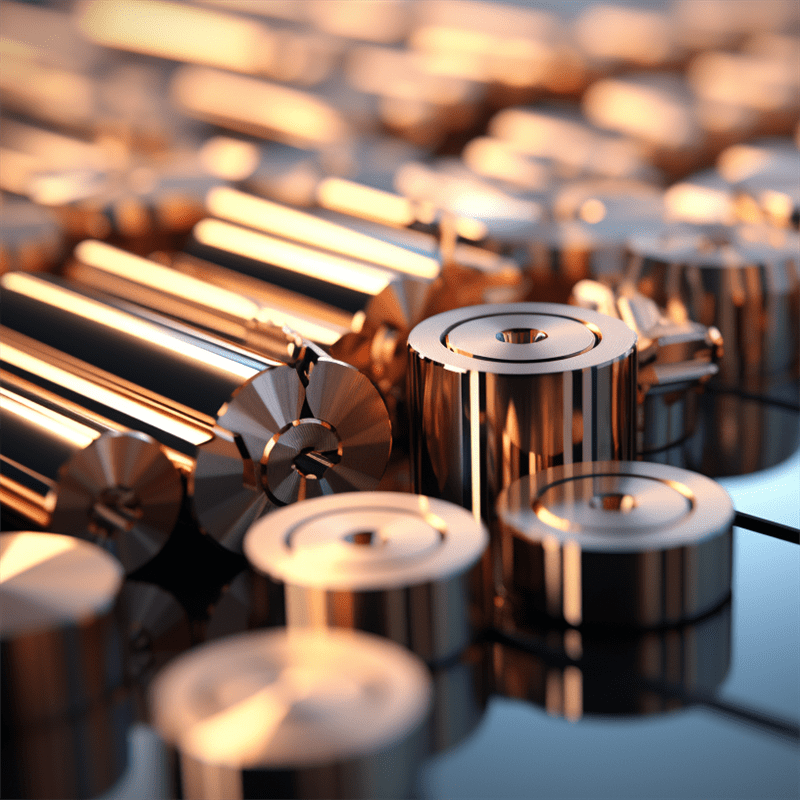
Uncoated Carbide Insert Geometry Options
Uncoated carbide inserts come in many different standard shapes, sizes, and geometries to suit various machining needs:
Insert Shapes:
- Triangle – General purpose shape, 3 cutting corners
- Square – Gives strength, used for feed heavy apps
- Round – Used for heavy depths, extra strength
- Rhombic – Combination of square and triangle shape
- Special shapes – Trapezoid, parallelogram, polygon etc.
Chipbreaker Geometries:
- Flat face – General machining, light finishing
- Grooved face – General machining, medium depths
- Wiper face – Finishing cuts, good surface finish
- Special chipbreakers – Hi-feed, hi-speed, hi-positive etc.
Nose Radii Options:
- Sharp – Used for feeds below 0.006” per rev
- Moderate – 0.008”-0.016” feed rates
- Large radii – Above 0.020” feed per rev
Choosing optimum insert geometry is vital for effective metal removal, good tool life, and desired component finish. The interrelationships between nose radius, feed rates, and cutting speeds must be balanced.
Applications and Suitable Materials
Uncoated carbide performs well for machining harder materials like:
- Alloy steels, tool steels
- Cast iron and hardened cast iron
- Hardened steels, up to 45 HRC
- Nickel/Cobalt based superalloys
- Titanium alloys up to Ti-6Al-4V
Carbide grades and insert geometry must match workpiece hardness characteristics and desired surface finish.
Typical components machined with uncoated carbide tooling:
- Shafts
- Bushes, sleeves
- Automotive parts
- Aerospace components
- Molds, dies, tooling
Materials NOT Suitable for Uncoated Carbide
- Non-ferrous materials like Aluminum – require special insert geometries and dedicated carbide grades to prevent insert wear
- Hard ceramics/composites – require extremely wear-resistant inserts like PCD or CBN
Uncoated Carbide Insert Specifications
Uncoated carbide inserts have established specifications covering inserts dimensions, tolerances, seating platform details etc. to ensure compatibility across tool holders from different manufacturers.
Standard Insert Designations
Inserts follow ISO/ANSI/national standards for the numbering system indicating shape, size, tolerance, hole details etc. Some examples:
Insert Designation | Meaning |
---|---|
CNMG 432 | C = Shape Code, N = Nose radius, M= Tolerance, G = Thickness, 432 = Inscribed Circle Diameter |
DNMX 11 04 08 – PM | Shape, IC size, Insert thickness, Hole dia & posn, Special feature |
Standard Dimensional Tolerances
Insert tolerance grades dictate permitted variations in critical dimensions like thickness, bore diameter/position, seating plane etc.
Tolerance Grade | Tolerance in mm |
---|---|
IT7 (Precision) | Up to 0.013mm |
IT8 (High precision) | 0.018mm to 0.036mm |
IT9 | 0.036mm to 0.072mm |
Tighter tolerances improve seating, performance consistency but increase cost. Standard IT9 tolerance allows acceptable seating for most applications.
Comparative Analysis
Comparison between various uncoated carbide insert types for steel turning applications:
Parameter | C6 Micrograin | C2 Medium Grain | M35 Ultra-fine Grain |
---|---|---|---|
Composition | Mixed MC+WC | 94% WC | Submicron WC+TiC+TaC+NbC |
Hardness | 1600 HV | 1760 HV | 1830 HV |
Toughness | Very High | Medium | Low |
Strength | Medium | Very High | Medium |
Thermal Conductivity | Low | Medium | High |
Tool Life | Long | Medium | Short |
Insert Wear | Abrasion | Chipping | Plastic Deformation |
Finish Achievable | Medium | Medium-Good | Very Good |
Price Level | Low | Economical | High |
Best Suited For | Interrupted Cuts | General Machining | Finishing Cuts |
For steel turning, the medium grain C2 grade provides the best balance between wear resistance and toughness properties like edge line chipping resistance. M35 ultra-fine grade gives an excellent finish but lacks robustness for interrupted cuts. C6 is sufficiently robust but does not give a comparable finish.
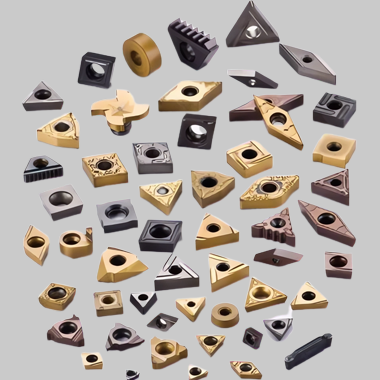
Uncoated Carbide Insert Suppliers
All major cutting tool manufacturers offer uncoated carbide inserts under their product range. Some leading uncoated carbide insert suppliers are:
Company | Grades Offered | Insert Style Options | Estimated Price Range |
---|---|---|---|
Sandvik Coromant | C2, C6, M35, P25, K20 | Triangle, Square, Round, Rhombic | $8 – $50 per insert |
Kennametal | KC850, KC925, K313 | Triangle, Square, Parallelogram | $6 – $40 per insert |
WIDIA | CC650, CC625DV | Triangle, Round | $5 – $30 per insert |
Iscar | IC8150, IC907, IC908 | Triangle, Square, Round, Rhombic | $10 – $60 per insert |
Kyocera Unimerco | CB20, CB30 | Triangle, Square | $15 – $100 per insert |
Prices vary hugely based on insert grade, size, geometry specifics. Bulk order quotes offer considerable cost savings versus individual/small orders.
Uncoated vs. Coated Carbide Inserts
Coated carbide inserts use additional treatment like CVD/PVD TiN, TiCN, TiAlN, AlCrN coatings to impart higher heat/wear resistance.
Parameter | Uncoated Carbide | Coated Carbide |
---|---|---|
Base Composition | Tungsten/Titanium Carbide | Same as uncoated |
Coating Technology | No coating | CVD/PVD TiN, TiCN etc. |
Coating Thickness | NA | 3-5 um typical |
Hardness | 86 to 93.5 HRA | 92 to 96 HRA |
Toughness | Very good | Good |
Heat Resistance | Up to 1000°C | Up to 1100°C |
Oxidation Resistance | Medium | Very Good |
Tool Life | Shorter | Longer |
Cost | Lower | Higher |
At very high cutting parameters, the coated insert’s extra heat protection gives notably longer tool life. However, uncoated carbide has sufficient wear resistance for many general machining applications at lower cost. The choice depends on work material, operating conditions, and finish needs.
FAQs
Q: What is the typical hardness range for uncoated carbide inserts?
A: Most grades used for uncoated carbide inserts have a hardness range of 1600 to 1900 Vickers, equivalent to ~86 to 93.5 on Rockwell A scale. Finer micrograin compositions can reach higher hardness levels exceeding 2000 Vickers.
Q: How are uncoated carbide inserts secured into tool holders?
A: Nearly all inserts use a clamping system, secured via a top clamp or screw. The insert’s underside/seating platform matches the subtle angle and platform geometry of the tool holder pocket. Proper seating ensures insert stability, accuracy, and safety.
Q: Can uncoated carbide inserts machine aluminum effectively?
A: Uncoated carbide can chemically react with aluminum at high cutting temperatures, causing severe aluminum buildup/welding and rapid insert failure. Aluminum-grade inserts with special geometries and dedicated insert grades/compositions are necessary.
Q: What causes inserts to crack or break during machining?
A: Excessive feeds/depths inducing high cutting forces coupled with inadequate insert toughness/bending strength for the cutting conditions leads to chipping or fractures. A less sharp cutting edge and increased edge prep/honing improves edge line toughness.
Q: How many times can an insert be safely reused by indexing to a fresh cutting edge?
A: Insert geometries with 3 usable corners like CNMG/DNMG can often be indexed at least twice for reuse so long as all edges are evenly worn and cutting parameters remain unchanged between cycles. Beyond second reuse may risk uneven loading.