Introduction: When Precision Reigns Supreme
In the world of machining, achieving a flawless surface finish is often the hallmark of exceptional craftsmanship. Whether it’s the gleaming surface of a precision component or the intricate details of a delicate part, the quest for perfection drives the pursuit of ever-finer finishes. At the forefront of this pursuit stand Type C carbide brazed tips, meticulously engineered to deliver the ultimate in surface quality and dimensional accuracy.
This article delves into the realm of Type C carbide brazed tips, unveiling their unique attributes, advantages, and the reasons why they’re the top choice for machinists seeking to achieve impeccable results.
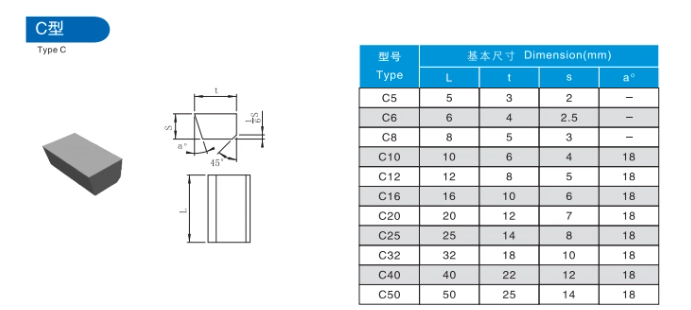
The Essence of Finishing: A Symphony of Precision and Finesse
Beyond Roughing and Shaping
While roughing operations focus on removing large amounts of material quickly, and semi-finishing operations bridge the gap, finishing is where the true artistry of machining shines. It’s about achieving:
- Exceptional Surface Smoothness: Minimizing surface roughness to create a mirror-like finish or meet stringent surface finish requirements.
- Precise Dimensional Accuracy: Holding tight tolerances to ensure that parts conform to exact specifications.
- Enhanced Aesthetics and Functionality: A superior surface finish not only enhances a part’s visual appeal but can also improve its functionality by reducing friction, wear, and corrosion.
Type C Carbide Brazed Tips: Architects of Exquisite Surfaces
A Fusion of Sharpness and Finesse
Type C carbide brazed tips are purpose-built for finishing operations, distinguished by their:
- Sharp Positive Rake Angles: The rake face slopes downwards towards the cutting edge, creating a sharp cutting action that shears material cleanly, leaving a smooth surface behind. This geometry minimizes cutting forces and reduces the tendency for material to build up on the cutting edge, both of which contribute to a finer finish.
- Small Nose Radii: The nose radius, the rounded portion at the tip’s cutting edge, is kept small in Type C tips. This allows for:
- Finer Surface Finishes: A smaller nose radius leaves behind finer surface irregularities, resulting in a smoother surface.
- Tighter Tolerance Control: The precise cutting action of a small nose radius enables the machining of intricate features and the holding of tight dimensional tolerances.
- Fine-Grained Carbide Grades: Type C tips often utilize fine-grained carbide grades with high hardness and wear resistance. These grades:
- Maintain Sharp Cutting Edges: Essential for achieving and maintaining fine surface finishes over extended machining periods.
- Minimize Cutting Edge Wear: Reducing the need for frequent tool changes and ensuring consistent surface quality throughout the machining process.
Advantages of Type C Carbide Brazed Tips in Finishing
Elevating Surface Quality and Precision
The specialized characteristics of Type C carbide brazed tips translate into several key advantages for finishing operations:
- Superior Surface Finishes: Their sharp cutting edges and small nose radii enable the achievement of exceptionally smooth surfaces, often eliminating the need for subsequent grinding or polishing operations.
- Tight Tolerance Control: The precise cutting action of Type C tips allows for the machining of intricate features and the holding of tight dimensional tolerances, ensuring that parts meet exacting specifications.
- Extended Tool Life: While not subjected to the same impact loads as roughing tips, Type C tips still benefit from wear-resistant carbide grades, providing extended tool life, especially in finishing operations where cutting parameters are typically lower.
- Versatility in Material Selection: Type C tips are well-suited for finishing a wide range of materials, including aluminum, brass, plastics, and even some steels, depending on the specific grade and coating.
Applications of Type C Carbide Brazed Tips
Where Precision Takes Center Stage
Type C carbide brazed tips are the preferred choice for finishing operations where surface quality and dimensional accuracy are paramount:
- Precision Turning: Creating smooth, accurate diameters on cylindrical workpieces.
- Facing: Producing flat, perpendicular surfaces.
- Boring: Enlarging and finishing existing holes.
- Grooving: Machining precise grooves for seals, O-rings, or retaining rings.
- Finishing Cuts in Milling: While not typically used for heavy milling, Type C tips can be employed for light finishing cuts in milling operations where surface finish is critical.
Choosing the Right Type C Carbide Brazed Tip: Factors to Consider
Fine-Tuning Your Tooling Selection
Selecting the optimal Type C carbide brazed tip involves careful consideration of several factors:
- Workpiece Material: The material’s hardness, abrasiveness, and thermal properties influence the choice of carbide grade and coating.
- Finishing Operation: The specific finishing operation, such as turning, facing, or boring, dictates the required tip geometry and size.
- Surface Finish Requirements: The desired surface finish, often specified in terms of Ra (roughness average) or Rz (average peak-to-valley roughness), is a primary factor in tip selection.
- Tolerance Requirements: The required dimensional tolerances influence the choice of tip geometry and cutting edge preparation.
- Machine Tool Capability: The rigidity and precision of the machine tool can influence the achievable surface finish and tolerances.
Type C Carbide Brazed Tip Selection: A Simplified Guide
To aid in the selection process, here’s a table summarizing typical applications and considerations for different Type C tip geometries:
Type C Tip Geometry | Typical Applications | Key Considerations |
---|---|---|
Round Insert | General-purpose finishing, turning, facing | Provides a good balance of sharpness and strength |
Diamond Insert | Precision turning, boring, grooving | Offers a sharper cutting edge for finer finishes |
Triangle Insert | Turning, facing, grooving | Provides three cutting edges for increased versatility |
Frequently Asked Questions about Type C Carbide Brazed Tips
Q1: Can Type C carbide brazed tips be used for roughing operations?
A1: While possible in some limited cases with very light cuts, Type C tips are not designed for roughing and their use in such applications is not recommended due to the risk of edge chipping or breakage.
Q2: What are the signs of wear on a Type C carbide brazed tip?
A2: Common wear signs include rounding of the cutting edge, wear on the rake or flank face, and built-up edge (BUE) formation on the cutting edge.
Q3: How can I achieve the best possible surface finish with a Type C carbide brazed tip?
A3: Key factors include selecting the appropriate tip geometry and grade for the application, optimizing cutting parameters (using lower feeds and depths of cut), ensuring proper cutting fluid application, and maintaining a rigid machine setup.
Q4: What is the difference between a round insert and a diamond insert Type C tip?
A4: Round inserts provide a good balance of sharpness and strength for general-purpose finishing, while diamond inserts offer a sharper cutting edge for achieving even finer surface finishes.
Q5: When would I choose a triangle insert Type C tip?
A5: Triangle inserts are a versatile choice for turning, facing, and grooving, offering three cutting edges for increased tool life and cost-effectiveness.