Tungsten carbide wear plates are heavy duty components used to resist abrasion, adhesion, erosion, and impact in demanding industrial environments. Made of tungsten carbide particles bonded in a metal matrix, these hardened plates offer superior durability compared to standard steel for critical high wear applications.
With extreme hardness nearing that of diamond and polished surfaces, tungsten carbide deflects particle strikes better than other materials. This enables protection of equipment like chutes, hoppers, cyclones, screens, separators, shoot lines, and truck beds in mining, minerals processing, cement, steel making, paper and more.
This guide provides a comprehensive overview of tungsten carbide wear plate grades, manufacturing methods, properties, design considerations, global suppliers, applications, FAQs and more.
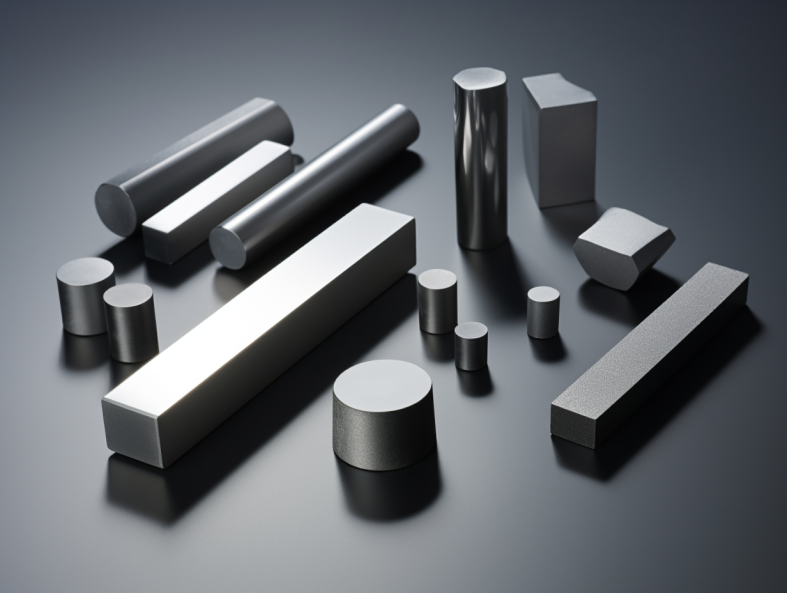
Tungsten Carbide Wear Plate Compositions
Tungsten carbide wear plates feature a composite construction with distinct constituents:
Component | Role |
---|---|
Tungsten carbide particles | Provide extreme hardness to resist wear |
Cobalt / Nickel binder | Bonds the tungsten carbide particles together |
Additives like tantalum, titanium, niobium | Enhance strength, fracture resistance |
Steel or alloy substrate | Backing support layer to build plate thickness |
The primary wear resistance comes from the hard tungsten carbide, while the binder and backing give mechanical support. Varying the carbide grain sizes, binder percentages and alloying elements creates specialized wear plate formulations.
Common tungsten carbide wear plate standards label compositions like 10/15/20% cobalt referring to the amount of cobalt binder used relative to the tungsten carbide content. Higher cobalt increases toughness but lowers hardness.
Tungsten Carbide Wear Plate Properties
The composite construction ensures tailored physical, mechanical and performance properties in tungsten carbide wear plates:
Property | Value |
---|---|
Density | 13.6 to 15.1 g/cm3 |
Hardness | Up to 92 HRA (86 HR45N) |
Compressive strength | Up to 8650 MPa |
Flexural strength | Up to 2410 MPa |
Maximum service temperature | Up to 500°C |
Thermal conductivity | 60-100 W/m°K |
The ultra-high hardness and strength characteristics give tungsten carbide outstanding abrasion resistance compared to 300-400 BHN for alloy steels. Coupled with thermal stability, this enables survival in high stress environments attacking surfaces via particles, bubbles, fluid flow etc.
Specialized “cermet” compositions with titanium carbonitride + nickel also offer peak hardness nearing 92 HRA for extreme abrasion resistance in ores, sands,Dirty feeds etc.
Tungsten Carbide Wear Plate Manufacturing
Two primary techniques are utilized for making tungsten carbide wear plates:
Sintered and Pressed Plates
Tungsten carbide powder and binder are compacted into plates up to 400mm x 400mm sizes and 30 mm thickness under high temperature and pressures. Multiple punched plates may be brazed on steel for thicker sections. These have uniform properties and complex shapes can be produced via pressing dies. However size limits material applications.
Typical sintered tungsten carbide wear plate features
- Consistent microstructure optimizing mechanical performance
- Up to 30 mm finished plate thickness in single layer
- Precision geometry possible via pressing dies
- Available in common cobalt or nickel binders
Fused and Overlaid Plates
By flame spraying, welding or laser cladding processes, crushed tungsten carbide particles are fused on steel substrates to manufacture large one-piece wear plates. These can reach bigger dimensions like 1500 x 6000 mm but have directional hardness variations based on overlay techniques which must be managed.
Typical fused tungsten carbide plate features
- Single pieces with fields up to 9 sqm
- Thicker plate options 40, 50, 60 mm
- Lower raw material input costs
- Some property differences across plate
Overlaid single-piece wear parts save on fabrication while pressed and sintered multi-layer composites provide optimized performance.
Applications of Tungsten Carbide Wear Plates
With best-in-class erosion, corrosion and abrasion resistance, tungsten carbide wear plates protect vital equipment across mining, mineral processing, thermal power, cement, and other material handling sectors:
Industry | Common Wear Issues | Wear Plate Uses |
---|---|---|
Mining | Impact and abrasion from mineral ores like iron, copper, gold, silver | Chute, hopper, screen, cyclone, classifier linings |
Mineral Processing | Erosion from ores, corrosion, flue gases | Pipe elbows, valves, separator lining |
Cement | Impact, abrasion from limestone, coal, additives | Classifier cone, separator blade protection |
Steel making | Abrasion from sinter, coke, mineral loads | Hopper, chutes, screen decks, ducts |
Power plants | Erosion from fly ash, sootblower lanes | Pulverizer throat segments, air preheater components |
With tailored tungsten carbide + binder compositions, these sacrificial wear parts withstand particle velocities exceeding 50 m/s across various temperature zones protecting assets worth millions of dollars.
Tungsten Carbide Plate Standards and Specifications
Industrial tungsten carbide wear plate specifications cover physical, mechanical and compositional properties:
Parameter | Typical Specification |
---|---|
Tungsten carbide content | 70 to 97% weight |
Binder metal | Cobalt / Nickel types and percentages |
Carbide grain size | Micrometers based on wear environment |
Hardness value | Rockwell / Vickers values |
Plate dimensions | Length x width x thickness in mm |
Composition grades | ISO 13384 / 23344 , US LanCarb standards |
Besides physical sizing, properties like hardness, grain size and chemical compositions are specified based on targeted wear environments. Custom formulations are also produced for unique particle types found across ores, clinkers, coal etc.
Industry standards help qualify tungsten carbide wear plates:
- ISO 23344 specifies tungsten carbide grades across mining, mineral processing, steel, thermal spray markets
- ASTM B777 has over 50 tungsten carbide grades covering cobalt, nickel and special binders
- US LanCarb consortium defines ultra-wear resistant tungsten carbide compositions
Leading manufacturers also list proprietary plate product families like MB60, Durit CB500, Permabond TC420 denoting binder types, grain structures and custom additives.
Design Factors for Tungsten Carbide Wear Parts
Application-based considerations for engineering tungsten carbide wear plates include:
Parameter | Design Choices and Recommendations |
---|---|
Surface hardness | – Hardness between 86 to 92 HRA based on particle types – Higher hardness for fine abrasive feeds |
Carbide grain size | – Smaller grains 2-8 μm for fine erosive particles – Larger 12-30 μm grains for impact and coarse abrasion |
Binder percentage | – Higher nickel or cobalt binder for toughness – Lower binder for maximum wear performance |
Plate dimensions | – Wider plates to minimize joints – Optimal lengths for ease of fixing |
Plate thickness and fixing | – Thicker plates allow fewer replacements – Secure stress-relieving mounts to avoid cracks |
With customized wear plate properties tailored for ore hardness, particle shape, feed rate, temperature and other specifics, service life improvements of 300-500% are possible over regular steel.
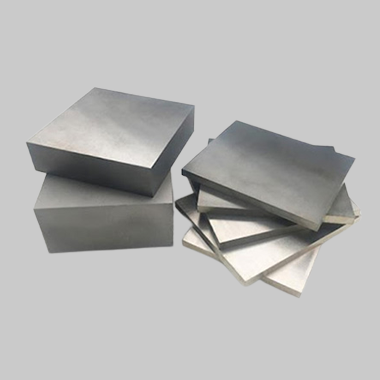
Global Suppliers of Tungsten Carbide Wear Parts
Prominent international tungsten carbide wear product vendors include:
Company | Headquarters | Products |
---|---|---|
Kennametal | USA | Custom tungsten carbide wear plates, tile and bricks |
Element Six | Ireland | Tungsten carbide grades for abrasive slurries |
Sandvik | Sweden | Ceramic tungsten carbide linings and tiles |
Metalogenia | Spain | Tungsten carbide plates fused on steel |
China Minmetals | China | Pressed tungsten carbide wear plate blanks |
Plansee | Austria | Pure tungsten carbide and nickel binder plates |
Both global mining corporations like Rio Tinto, BHP rely on these producers for wear protection across mineral handling sites. Regional players in markets like India, China and Middle East complement international branded suppliers.
Besides finished wear parts, specialized tungsten carbide product companies also supply semi-finished pressed plate blanks, proprietary binder and grain mixes to platens and fabrication workshops for customized wear solutions.
FAQs
What are the different types of tungsten carbide wear plates available?
- Main product categories are multi-layer pressed plates with uniform hardness versus fused overlays on steel with directional properties. Within these, compositions are tailored via carbide sizes, cobalt/nickel percentages etc.
What welding processes can fix tungsten carbide wear plate panels on equipment?
- Special nickel alloy solders, PTA hardfacing and electron beam welds ensure fixturing rated for high vibrations. Mechanical bolting is preferred for easier replacement.
How to select between tungsten carbide or ceramics for wear protection?
- Tungsten carbide prevails for high stress abrasion-dominated environments given fracture resistance. Technical ceramics suit moderate erosion and corrosion applications needing heat tolerance.
What backing plate thickness should be used for wear plate overlays?
- For cranes, excavators and lighter structures, 8-12 mm steel is sufficient for flat deposits without support legs. For chutes, hoppers and shoots seeing impacts, 20-25 mm steel with ribs handle loads better.
What determines the service life of tungsten carbide wear products?
- Life cycle costs involve wear rates dictating plate thickness needed. This depends on particle types, speeds, feed rates and angles. Maintenance schedules for inspection and bolt torqueing also affect durability.
How are tungsten carbide wear parts refurbished or repaired after service?
- Minor erosion can be fixed by metal build-up and machining. For thicker section wear, new overlay deposition renews dimensions. Fully worn parts need replacement with new pressed plate panels.