Overview of Tungsten Carbide Tool Blanks
Tungsten carbide tool blanks refer to unfinished blocks of tungsten carbide material that are ground and machined into finished cutting tools. The extremely high hardness and wear resistance of tungsten carbide makes it an ideal material for metal cutting applications.
This guide provides a comprehensive overview of tungsten carbide grades, tool blank types, manufacturing methods, grinding processes, applications, design considerations, specifications, suppliers, costs, advantages vs limitations, and other FAQs about tungsten carbide tool blanks.
Types of Tungsten Carbide Tool Blanks
The main types of tungsten carbide grades for tool blanks include:
- Straight tungsten carbide (WC)
- Cobalt-cemented tungsten carbide (WC-Co)
- Chromium carbide coated
- Titanium carbide added
- Tantalum carbide enriched
- Niobium carbide grades
WC-Co grades with 6-12% cobalt content are most widely used. The cobalt acts as a binder matrix for the tungsten carbide particles. Other carbides and coatings provide specific enhancements in properties.
Tungsten Carbide Tool Blanks Types
Common tungsten carbide tool blank types:
Type | Details | Applications |
---|---|---|
Round rod blanks | Cylindrical bars | Reamers, end mills, drills |
Square blanks | Square section rods | Broaches, slitting saws |
Rectangular blanks | Rectangular section rods | Cutters, router bits |
Disc blanks | Cylindrical discs | Gear cutters |
Block blanks | Rectangular blocks | Form tools, dies |
The blank shape is designed to suit the eventual tool machining process and final tool geometry.
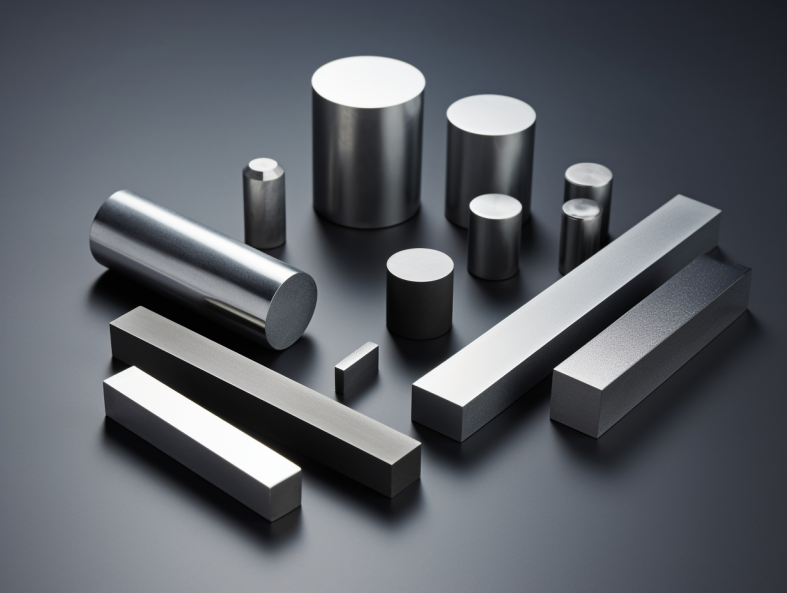
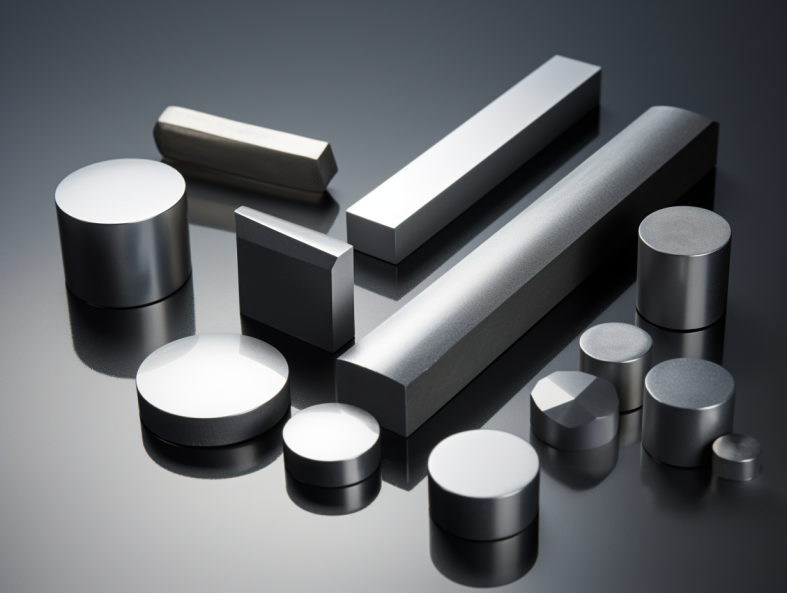
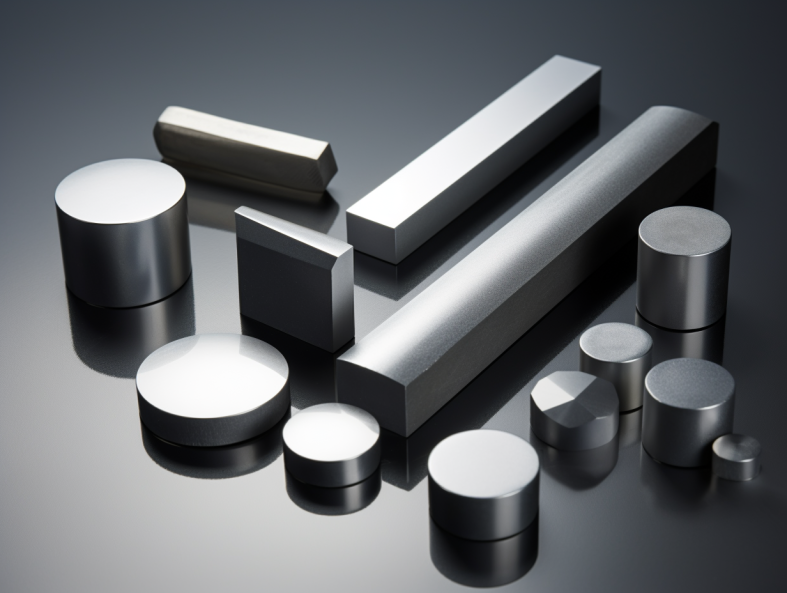
Tungsten Carbide Tool Blank Manufacturing
Key tungsten carbide blank manufacturing steps:
- Milling and blending – Powdered tungsten carbide and cobalt thoroughly mixed
- Compaction – Powder pressed into desired blank shape
- Sintering – Blanks fired at 1400-1600°C to densify and toughen
- Grinding – Blanks ground to precise dimensions
- EDM – Electrical discharge machining used for complex profiles
- Laser cutting – Precise laser cutting ofPCD/CBN layers
- Coating – CVD and PVD coatings applied if needed
- Inspection – Dimensional accuracy, finish, and defect checks
Advanced sintering and machining techniques produce consistent tool blank quality.
Tungsten Carbide Tool Grinding Processes
Common grinding methods for machining sintered tungsten carbide tool blanks:
- Surface grinding – Flattens surfaces and sets dimensions
- Cylindrical grinding – Grinds radii and creates round profiles
- Centerless grinding – Precisely grinds diameters of cylindrical parts
- Internal grinding – Grinds inside diameters of holes and bores
- Honing – Finishes hole size and geometry to high precision
- EDM – Cuts complex shapes not possible by abrasive grinding
Each process provides specific geometry capability for the tool design.
Applications of Tungsten Carbide Tool Blanks
Tungsten carbide tool blanks are used to manufacture cutting tools for:
- Milling – End mills, slab mills, face mills
- Turning/Boring – Boring bars, inserts, tool bits
- Drilling – Twist drills, gun drills, countersinks
- Reaming – Tapered reamers, spiral flute reamers
- Gear cutting – Hobs, shaper cutters, skiving tools
- Broaching – Internal and external broaches
- Sawing – Slitting saws, circle cutters
- Threading – Thread mills, taps, thread whirling tools
- Specialty tools – Form tools, counterbores, chamfer tools
Tungsten carbide’s hardness makes it suitable for nearly all metalworking tool types.
Design Considerations for Tungsten Carbide Tool Blanks
Key design factors for tungsten carbide tool blanks:
- Carbide grade – Selection for required hardness, toughness, wear resistance
- Binder content – Higher cobalt for better fracture toughness
- Blank shape and size – Designed for subsequent machining process
- Surface finish – Ground to tight tolerances and surface finish
- Coatings – CVD, PVD coatings enhance wear protection
- Brazed tips – Carbide tips brazed to steel shanks
- QA/QC – Rigorous inspection protocols to ensure defect-free blanks
The blank properties are tailored to suit the operating conditions and life requirements of the final machining application.
Specifications
Typical specifications for tungsten carbide tool blanks:
Parameter | Specification |
---|---|
Hardness | 88-93 HRA (~1600-2100 HV) |
Density | 14.95 – 15.10 g/cm3 |
Transverse Rupture Strength | 500,000 – 750,000 psi |
Tungsten Carbide Content | 84 – 97% wt |
Cobalt Content | 3 – 16% wt |
Porosity | Near zero, fully dense |
Surface Finish | Up to 10 μin, mirror finish |
Dimensions | ±0.0005 in tolerance |
The precise composition, microstructure, hardness, strength, and machined finish determine tool blank quality.
Global Suppliers
Leading tungsten carbide tool blank manufacturers:
- Kennametal
- Sandvik
- Mitsubishi Materials
- OSG Corporation
- Nachi-Fujikoshi
- Sumitomo
- LMT Tools
- Guhring
- Halcyon Technologies
- Rock River Tool
Many tooling brands source blanks from these established carbide suppliers to create finished tools under their brand name.
Cost Factors
Factors influencing tungsten carbide tool blank costs:
- Carbide grade selected
- Quantity ordered
- Blank dimensions and complexity
- Tolerances and surface finish needs
- Additional grinding or coating
- Testing requirements
- Production method used
- Manufacturer’s reputation and capabilities
- Global supply and demand dynamics
Cost range: $5 – $100+ per blank, highly application dependent
Contacting manufacturers for a custom quotation is recommended.
Purchasing Considerations
Key considerations when sourcing tungsten carbide tool blanks:
- Carbide properties needed for the application
- Designating the appropriate blank shape and size
- Required surface finish and dimensional tolerances
- Understanding lead time for different grades and volumes
- Manufacturer’s technical expertise and customer service
- Overall track record and reputation for quality
- Qualifications like ISO certification
- Compliance with RoHS, REACH, and conflict mineral reporting
- Total costs for various size orders
Careful planning and partnering with the right carbide blank supplier ensures a smooth procurement process and successful end-application performance.
Pros and Cons of Tungsten Carbide Blanks
Advantages
- Extreme hardness for excellent wear resistance
- Maintains hardness and strength at high temperatures
- High modulus of elasticity
- Chemically inert to most solutions
- Can be ground to mirror-like finish
Limitations
- Brittle with limited fracture toughness
- Relatively expensive material
- Heavily dependent on cobalt pricing
- Specialized grinding needed to machine
- Challenging to recycle after use
FAQs
What are the main advantages of tungsten carbide cutting tools?
The extreme hardness, high hot hardness, superior wear resistance, strength, and chemical inertness allow tungsten carbide tools to machine materials like hardened steel that cannot be cut with high-speed steel or carbide inserts.
What grades offer the best combination of hardness and toughness?
Medium grain size cobalt-cemented tungsten carbides in the WC-6Co to WC-8Co range offer a good balance of hardness, strength and fracture resistance for most general machining applications.
How are tungsten carbide tool tips brazed to steel tool shanks?
Carbide tips or inserts are brazed to steel shanks using high temperature silver brazing alloys that can withstand up to 700°C. Proper braze gap allowance and brazing process controls are critical.
What causes premature tool failure or wear?
Potential causes include inadequate surface finish causing stress concentrations, improper carbide grade for the application, depths of cut or speeds exceeding tool capacity, lack of coolant, built-up edge, and excessive tool runout or vibration.
What safety precautions should be taken when grinding tungsten carbide?
Use proper wheel guards, dust collection, and PPE to control exposure to grinding dust. Tungsten carbide dust is a potential respiratory hazard if inhaled.
Conclusion
Tungsten carbide’s unique properties make it the first choice for tool blank materials destined for machining applications requiring high wear resistance and hardness. Careful grade selection, precise grinding and finishing, and controlling cobalt content allow manufacturers to tailor blanks to optimize tool life and performance. As tungsten carbide tooling technology continues advancing, finished tools produced from quality carbide blanks will play an increasing role across more demanding metalworking industry applications.