Tungsten carbide strips – those deceptively simple strips of engineered material – are the unsung heroes driving precision and durability across countless industries. From slicing through the toughest metals to shaping intricate woodworking masterpieces, these strips empower us to push the boundaries of what’s possible. Join us as we embark on a deep dive into the world of tungsten carbide strips, exploring their properties, applications, and the key factors to consider when choosing the perfect strip for your needs.
What Makes Tungsten Carbide Strips So Special?
Tungsten carbide strips are thin, flat pieces of cemented carbide, a composite material renowned for its exceptional hardness and wear resistance. Their secret lies in the unique blend of:
- Tungsten Carbide: This powerhouse ingredient, composed of tungsten and carbon atoms bonded in a tightly packed structure, boasts a hardness approaching that of diamond.
- Cobalt Binder: Acting as a metallic glue, cobalt binds the tungsten carbide particles together, providing the necessary toughness and impact resistance.
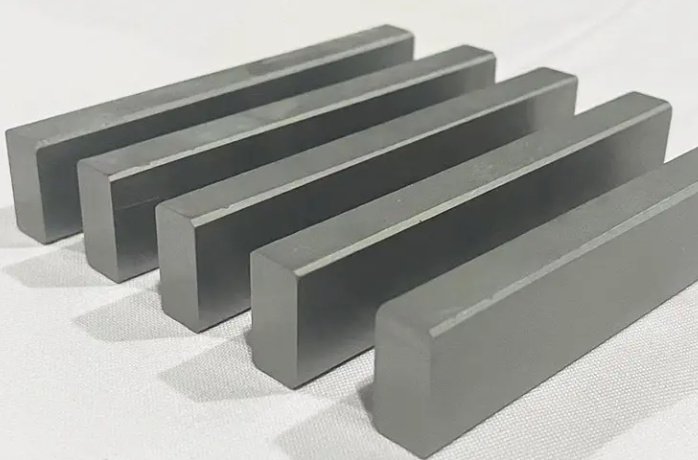
From Powder to Powerhouse: The Making of Tungsten Carbide Strips
The creation of tungsten carbide strips is a testament to precision engineering:
- Powder Metallurgy: Finely ground powders of tungsten carbide and cobalt are meticulously blended in specific ratios to achieve the desired properties.
- Pressing and Shaping: The powder mixture is then subjected to immense pressure within specialized molds, forming the initial shape of the strips.
- Sintering: The Alchemy of Heat: The pressed strips undergo a high-temperature sintering process in a controlled atmosphere. During sintering, the cobalt binder melts and fuses the tungsten carbide particles together, forming a solid, incredibly dense material.
- Finishing Touches: After sintering, the strips may undergo further processing, such as grinding, polishing, or coating, to refine their surface finish, dimensions, and enhance specific properties.
A World of Variety: Types and Properties of Tungsten Carbide Strips
Tungsten carbide strips are not a one-size-fits-all solution. They come in a wide range of grades, sizes, and configurations, each tailored for specific applications. Here’s a glimpse into their diversity:
Tungsten Carbide Strips: A Glimpse into Their Properties
Property | Description | Typical Values |
---|---|---|
Hardness (HRA) | Resistance to scratching and indentation | 88-95 |
Transverse Rupture Strength (TRS) | Ability to withstand bending forces without breaking | 1500-3000 N/mm² |
Density | Mass per unit volume | 13.5-15.0 g/cm³ |
Grain Size | Size of the tungsten carbide particles, influencing hardness and wear resistance | 0.5-10 µm |
Cobalt Content | Percentage of cobalt binder, impacting toughness and wear resistance | 6-12% |
Table 1: Key Properties of Tungsten Carbide Strips
Where Precision and Durability Converge: Applications of Tungsten Carbide Strips
The exceptional properties of tungsten carbide strips make them indispensable in a wide range of industries:
1. Metalworking: Taming the Steel Giants
- Cutting Tools: Tungsten carbide inserts are the heart of lathe tools, milling cutters, drills, and other metal cutting tools, enabling the machining of even the toughest metals with precision and efficiency.
- Wear Parts: Tungsten carbide strips are used to create wear-resistant components in metal forming dies, punches, guides, and other tooling, extending their lifespan and maintaining dimensional accuracy.
2. Woodworking: Crafting Masterpieces with Ease
- Saw Tips: Tungsten carbide strips form the cutting edges of circular saw blades, miter saw blades, and table saw blades, delivering clean, precise cuts in hardwoods, plywood, and composites.
- Router Bits: Tungsten carbide inserts in router bits provide sharp, long-lasting cutting edges for shaping, profiling, and joinery in woodworking projects.
3. Construction: Building a Solid Foundation
- Concrete Sawing: Segments of tungsten carbide strips form the cutting teeth of concrete saw blades, enabling the cutting of concrete, asphalt, and other hard construction materials.
- Drilling and Boring: Tungsten carbide inserts are used in drill bits, core bits, and other drilling tools for penetrating concrete, rock, and other challenging materials.
4. Beyond the Usual Suspects:
The versatility of tungsten carbide strips extends to a wide range of other industries, including:
- Oil and Gas: Wear-resistant components for drilling equipment, valves, and pumps.
- Aerospace: Cutting tools, wear parts, and structural components for aircraft and spacecraft.
- Medical: Surgical instruments, dental tools, and implants.
Comparing the Contenders: Tungsten Carbide Strip Suppliers
Supplier | Location | Price Range (per piece) | Specialties |
---|---|---|---|
TRUER | Global | $5 – $50 | Custom carbide solutions, high-performance grades |
Element Six | Global | $10 – $80 | Wide range of standard and specialized grades, advanced coatings |
Sandvik Coromant | Sweden | $15 – $100 | Advanced geometries and coatings for demanding applications |
Kennametal | US | $8 – $75 | High-quality carbide for cutting tools and wear parts |
Table 2: Comparing Tungsten Carbide Strip Suppliers
Note: Prices are approximate and may vary depending on grade, size, quantity, and market conditions.
The Two Sides of the Coin: Advantages and Limitations of Tungsten Carbide Strips
Tungsten Carbide Strips: A Balanced Perspective
Advantages | Limitations |
---|---|
Exceptional hardness and wear resistance | Relatively brittle, susceptible to fracture under impact |
High cutting efficiency and precision | Can be expensive compared to other materials |
Long tool life, reducing downtime and costs | Requires specialized equipment for machining and processing |
Versatility for various applications and materials | May not be suitable for all cutting or wear applications |
Table 3: Advantages and Limitations of Tungsten Carbide Strips
Beyond the Basics: Interesting Facts About Tungsten Carbide
- Diamond’s Rival: Tungsten carbide boasts a hardness of 9 on the Mohs hardness scale, making it one of the hardest materials known to man, second only to diamond.
- From Lightbulbs to Tools: Tungsten, the key component of tungsten carbide, was initially used in incandescent lightbulb filaments due to its high melting point.
- Space-Age Material: Due to their extreme properties, tungsten carbide materials are used in aerospace applications, including rocket nozzles and cutting tools for space exploration.
Why Choose TRUER for Your Tungsten Carbide Strip Needs?
At TRUER, we are passionate about delivering carbide solutions that empower our customers to achieve exceptional results. Here’s why TRUER stands out:
- Uncompromising Quality: We source the highest quality tungsten carbide materials and employ stringent quality control measures throughout our manufacturing process.
- Custom Solutions: We specialize in tailoring tungsten carbide strips to meet your unique specifications, from grade and geometry to size and finish.
- Technical Expertise: Our team of carbide experts provides expert guidance and support, helping you select the optimal carbide solution for your application.
- Global Reach: With a global presence, we provide timely delivery and responsive customer service wherever you are in the world.
FAQs: Addressing Your Tungsten Carbide Strip Queries
1. What is the difference between tungsten carbide grade and grain size?
Tungsten carbide grade refers to the specific formulation of tungsten carbide, cobalt, and other elements, influencing overall properties. Grain size refers to the size of the tungsten carbide particles within the carbide matrix, affecting hardness and wear resistance.
2. Can tungsten carbide strips be sharpened?
Yes, tungsten carbide strips can be sharpened using specialized diamond grinding wheels and equipment. However, it’s crucial to maintain the correct angles and clearances during sharpening for optimal performance.
3. What are the safety precautions for working with tungsten carbide strips?
Due to their extreme hardness, tungsten carbide strips can be brittle and may shatter if dropped or mishandled. Always wear safety glasses, gloves, and appropriate clothing when handling tungsten carbide strips.
4. How do I choose the right tungsten carbide strip for my application?
Selecting the appropriate tungsten carbide strip involves considering factors such as:
– Material Being Cut: Different carbide grades are optimized for cutting specific materials (e.g., wood, metal, concrete).
– Cutting Conditions: Cutting speed, feed rate, and depth of cut influence the choice of carbide grade and geometry.
– Desired Tool Life: Applications requiring longer tool life may benefit from higher-grade carbide strips.
Consulting with a carbide supplier or tooling expert can provide valuable guidance in selecting the optimal tungsten carbide strip for your needs.
5. What is the lifespan of a tungsten carbide strip?
The lifespan of a tungsten carbide strip depends on several factors, including:
– Carbide Grade: Higher-grade carbide strips generally offer longer tool life.
– Application: Cutting abrasive materials or operating at high speeds can reduce tool life.
– Cutting Parameters: Using appropriate cutting speeds, feed rates, and depths of cut can extend tool life.
– Maintenance: Proper sharpening and handling can significantly prolong the lifespan of tungsten carbide strips.