Tungsten carbide square blanks refer to square-shaped pieces of tungsten carbide that serve as a starting material for manufacturing various cutting tools and wear parts. The unique properties of tungsten carbide make it an ideal material for high wear resistance applications.
This guide provides a detailed overview of tungsten carbide square blanks, their compositions, manufacturing process, sizes, tolerances, applications, selection considerations, suppliers, costs and comparisons with alternatives.
Introduction to Tungsten Carbide Square Blanks
Tungsten carbide square blanks have the following key characteristics:
- Square shaped pieces of tungsten carbide material
- Available in different standard sizes
- Used as blanks for manufacturing cutting tools
- Provides very high wear resistance
- Harder than other tool materials like HSS
- Manufactured by sintering tungsten carbide powders
Tungsten carbide blanks serve as a standardized starting raw material that can be ground and shaped into final tooling products like inserts, dies, form cutters etc. based on application requirements.
Composition and Properties of Tungsten Carbide Blanks
The composition and properties of tungsten carbide blanks is:
- Made of tungsten carbide grains bonded in a cobalt matrix
- Contains 85-95% tungsten carbide and 5-15% cobalt binder
- Small amounts of other carbides and additives
- Extremely hard – HV 1300-1600 kg/mm2
- Density of 14.5 – 15.1 g/cc
- Compressive strength upto 6.5 GPa
- High stiffness and thermal conductivity
- Excellent abrasion and erosion resistance
The unique properties of tungsten carbide provide wear resistance superior to other tool materials. The cobalt binder gives fracture toughness. Carbide grain size and cobalt content are tailored based on application.
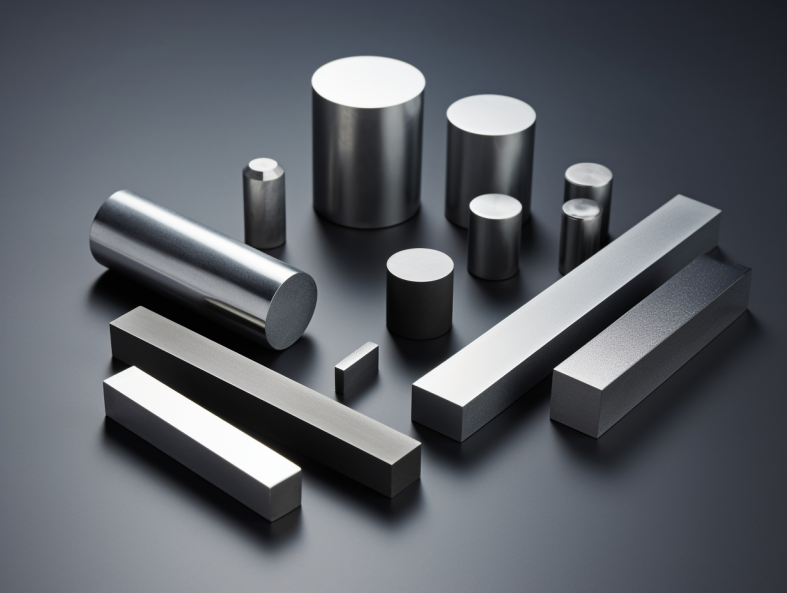
Manufacturing Process for Tungsten Carbide Blanks
Tungsten carbide square blanks are manufactured by:
Powder Processing
- Blending tungsten carbide, cobalt, and other powder additives
- Ball milling powders to achieve uniform mixture
Compaction
- Pressing the milled powder in a die at high pressures
- Cold isostatic pressing used for complex shapes
- Produces “green” compact parts
Sintering
- Heating compact parts to 1400-1500°C in a controlled atmosphere
- Causes densification and bonding of particles
- Shrinkage of 20% or more during sintering
Finishing
- Grinding blanks to achieve size tolerance
- Lapping, honing and polishing to required surface finish
- Close dimensional control of ±0.025 mm
The controlled pressing and sintering processes ensure consistent properties and dimensions of the blanks.
Sizes and Tolerances of Tungsten Carbide Blanks
Tungsten carbide blanks are produced in standardized square sizes:
Common Standard Sizes
- 10 x 10 mm
- 12 x 12 mm
- 16 x 16 mm
- 20 x 20 mm
- 25 x 25 mm
Thickness Range
- 2 mm to 10 mm
Size Tolerance
- ±0.025 mm
Various blank dimensions are manufactured to suit different cutting tool requirements. Thicker blanks allow longer tools to be produced for rigidity. Precise size control minimizes grinding allowance needed when making final tools.
Applications and Use of Tungsten Carbide Blanks
The major applications of tungsten carbide square blanks include:
- Cutting tools – inserts, drills, endmills, form tools
- Drawing and extrusion dies
- Wire drawing dies
- Pelletizing presses
- Stamping and coining dies
- Bearings and seals
- Mining and construction tools
Tungsten carbide blanks provide an ideal starting material for manufacturing wear parts needing very high hardness, strength and abrasion resistance properties. The ground blanks are brazed or clamped into tool holders.
Benefits and Advantages of Tungsten Carbide Blanks
Some key benefits of using tungsten carbide square blanks:
- Extremely high hardness and wear resistance
- High compressive and bending strength
- Retains strength at elevated temperatures
- Thermal shock and corrosion resistance
- Consistent properties from controlled manufacturing
- Standardized dimensions for ease of tool design
- Less expensive than custom sintered parts
- Faster delivery than custom blank sizes
- Ease of machining into final tool geometry
The unique properties of tungsten carbide combined with standardized square blanks make it an ideal and cost-effective choice for high wear tooling applications.
Limitations of Tungsten Carbide as a Tool Material
Some limitations of tungsten carbide to consider are:
- Brittle with lower fracture toughness
- Prone to chipping under shock loads
- Difficult to machine requiring diamond grinding
- Heavier than other tool materials
- More expensive than HSS tools
- Square blanks limit tool geometry options
- Not suitable for low rigidity holders
- Chemical incompatibility with some alloys
- Re-sharpening can alter blank accuracy
The limitations require designing tungsten carbide tools properly based on specific application requirements.
Price and Cost of Tungsten Carbide Blanks
The price range for tungsten carbide square blanks is:
Tungsten Carbide Blanks Price
Size | Thickness | Price Range |
---|---|---|
10 x 10 mm | 3 mm | $8 – $12 |
16 x 16 mm | 5 mm | $15 – $22 |
20 x 20 mm | 6 mm | $25 – $35 |
25 x 25 mm | 8 mm | $45 – $60 |
- Prices depend on size, grade, thickness and order quantity
- Grades with finer grain size cost more
- Thicker blanks are more expensive
- Smaller orders have higher per piece costs
Tungsten carbide is more expensive than other tool materials but provides much longer service life in extreme wear conditions. This makes it economical for specific applications.
How to Select Tungsten Carbide Blanks
Key selection criteria for tungsten carbide blanks:
- Application – Parameters like expected wear rates, loads, speeds, and temperature
- Tool size – Choose standard blank size closest to finished tool dimensions
- Thickness – Thicker blanks for longer tools needing rigidity
- Tolerances – Tighter tolerances for precision wear parts
- Surface finish – Finer surface finishes for better performance
- Grade – Balance of hardness, strength and toughness
- Coating – Any post-coating to improve lubricity, wear protection
- Manufacturer – Reputable manufacturer ensuring consistent quality
- Delivery – Standard blanks enable faster delivery
- Cost – Balance performance versus total tooling cost
The tool designer selects the optimum blank specification tailored for each tooling application.
Comparing Tungsten Carbide Blanks with Alternatives
Comparison with Other Tool Materials
Parameter | Tungsten Carbide | High Speed Steel | Ceramics |
---|---|---|---|
Wear resistance | Excellent | Moderate | Excellent |
Toughness | Moderate | Very Good | Low |
Thermal properties | Good | Moderate | Excellent |
Corrosion resistance | Excellent | Moderate | Excellent |
Machinability | Difficult | Easy | Difficult |
Cost | High | Low | High |
Advantages over Custom Sintered Parts
- Significantly lower cost
- Faster delivery for standard sizes
- Reduced tool design constraints
- Simpler inventory management
Tungsten carbide blanks provide the ideal balance of properties and cost for most wear part applications, especially when standard sizes meet requirements.
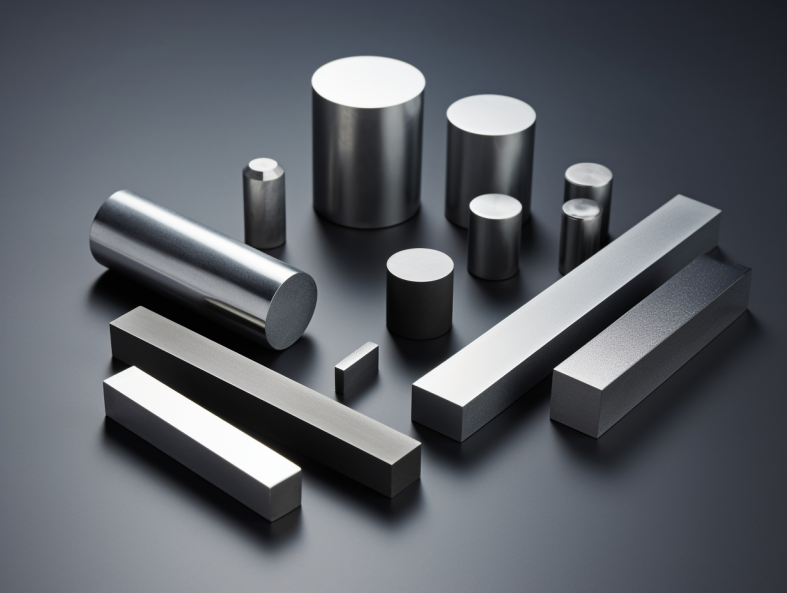
FAQs
What are tungsten carbide blanks used for?
Tungsten carbide blanks are used as a starting raw material for manufacturing various cutting tools, dies, bearings and wear parts that require high abrasion resistance.
How are tungsten carbide blanks manufactured?
TC blanks are manufactured by compacting tungsten carbide and cobalt powders and then sintering them at high temperature to produce a dense material. The sintered parts are ground to shape.
What are the main properties of tungsten carbide?
Tungsten carbide has very high hardness and compressive strength, excellent wear and erosion resistance, high thermal conductivity, and good corrosion resistance.
What are the benefits of using TC blanks versus custom sintered parts?
Benefits are lower costs, faster delivery, and greater flexibility by using standardized blank sizes. This simplifies inventory and production.
How to select the right tungsten carbide blank size and grade?
Consider the tool size, rigidity needed, tolerances, surface finish, production quantities, operating conditions and total tooling cost. Choose a reputable manufacturer.
What tolerances are provided on tungsten carbide blanks?
Typical size tolerance is ±0.025 mm. Finer tolerances like ±0.01 mm are possible for precision applications but cost more.
How are tungsten carbide blanks sharpened or reconditioned?
TC blanks are sharpened by diamond grinding proper wheel selections to minimize damage. Repeated sharpening can compromise blank accuracy requiring replacement.
What are the limitations of using tungsten carbide as a tool material?
Limitations include lower toughness than other materials, difficulty in machining, heavier parts, and higher base cost. Proper design and application engineering is important.
What coatings are applied to tungsten carbide blanks?
Common coatings include titanium aluminum nitride (TiAlN), titanium nitride (TiN) and titanium carbon nitride (TiCN). This improves wear performance and tool life in specific applications.