Cutting tools are crucial in modern manufacturing, and the right material can make all the difference. Among the various materials used, tungsten carbide rods stand out for their hardness, strength, and wear resistance. Let’s dive into the world of tungsten carbide rods, their types, applications, properties, and how to choose the right one for your cutting needs.
Overview
Tungsten carbide rods are a key component in many cutting tools due to their exceptional properties. These rods are made from tungsten carbide powder and binder metals, which are sintered to form a dense, hard material. Their high hardness and wear resistance make them ideal for machining and cutting various materials.
Types of Tungsten Carbide Rod for Cutting Tools
Here, we list specific models of tungsten carbide rods used for cutting tools:
Model | Description |
---|---|
YG6 | Known for its high wear resistance and impact toughness. Ideal for cutting non-ferrous metals. |
YG8 | Offers a balance between wear resistance and toughness. Suitable for general-purpose cutting. |
YG10X | High hardness and wear resistance. Excellent for cutting cast iron and non-ferrous metals. |
YG15 | High impact resistance. Used for heavy-duty cutting and drilling applications. |
YG20 | Very tough and resistant to fracture. Suitable for cutting hard steel and other tough materials. |
YG20C | Enhanced toughness and wear resistance. Ideal for mining tools and heavy-duty cutting. |
YG30 | Highest toughness among tungsten carbide grades. Used for extreme cutting conditions. |
ZK10UF | Ultra-fine grain size. Provides a sharp cutting edge for precision machining. |
K44 | Good for cutting stainless steel and heat-resistant alloys. |
CD650 | Contains a higher percentage of cobalt for increased toughness. Suitable for interrupted cuts. |
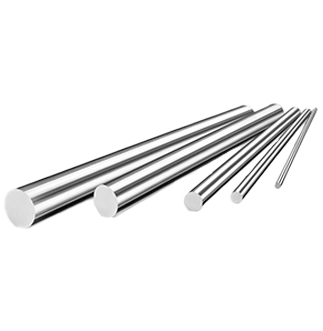
Applications of Tungsten Carbide Rod for Cutting Tools
Tungsten carbide rods find applications in various cutting tools. Here’s how they are used:
Application | Description |
---|---|
Drills | Used in high-performance drills for metals and composites. |
End Mills | Employed in milling operations for precise and smooth cutting. |
Reamers | Ensures accurate hole sizing and finish in materials. |
Cutting Inserts | Replaceable cutting edges in various tools for efficiency and cost-effectiveness. |
Mining Tools | Used in tools for drilling and cutting in mining applications due to high wear resistance. |
Lathe Tools | Precision turning and cutting tools for lathes. |
Router Bits | Used in woodworking and metalworking for shaping and cutting materials. |
Saw Blades | Provides durability and long life for cutting hard materials. |
Planer Blades | Used in planers for smooth and precise surface finishes. |
Taps and Dies | Employed in threading operations for cutting and forming threads. |
Material Properties of Tungsten Carbide Rod for Cutting Tools
Understanding the material properties is crucial for selecting the right tungsten carbide rod. Here are the key properties:
Property | Description |
---|---|
Hardness | Extremely high hardness, usually between 85-95 HRA, providing excellent wear resistance. |
Strength | High compressive strength, making it suitable for heavy-duty cutting and drilling applications. |
Toughness | Good impact resistance, especially in grades with higher cobalt content. |
Wear Resistance | Outstanding wear resistance, which extends the tool life significantly. |
Thermal Conductivity | Efficient heat dissipation, which helps in maintaining cutting efficiency and tool life. |
Corrosion Resistance | Good resistance to corrosion, especially in environments where moisture or chemicals are present. |
Composition, Properties, Characteristics
The composition of tungsten carbide rods influences their properties and performance. Here’s a detailed look:
Model | Composition | Properties | Characteristics |
---|---|---|---|
YG6 | 94% WC, 6% Co | High hardness, good wear resistance | Suitable for non-ferrous metals, high impact resistance |
YG8 | 92% WC, 8% Co | Balanced hardness and toughness | Versatile, general-purpose cutting |
YG10X | 90% WC, 10% Co | Very high hardness, wear resistance | Ideal for cast iron, non-ferrous metals |
YG15 | 85% WC, 15% Co | High impact resistance, toughness | Used in heavy-duty applications, drilling |
YG20 | 80% WC, 20% Co | Tough, resistant to fracture | Suitable for hard steel and tough materials |
YG20C | 80% WC, 20% Co + grain inhibitors | Enhanced toughness, wear resistance | Ideal for mining tools, heavy-duty cutting |
YG30 | 70% WC, 30% Co | Highest toughness, moderate hardness | Extreme cutting conditions, high impact applications |
ZK10UF | 90% WC, 10% Co (ultra-fine grain) | Sharp cutting edge, high precision | Precision machining, fine finishes |
K44 | 88% WC, 12% Co | Good for stainless steel, heat-resistant alloys | High heat and corrosion resistance |
CD650 | 85% WC, 15% Co + special binders | Increased toughness, wear resistance | Suitable for interrupted cuts, high shock applications |
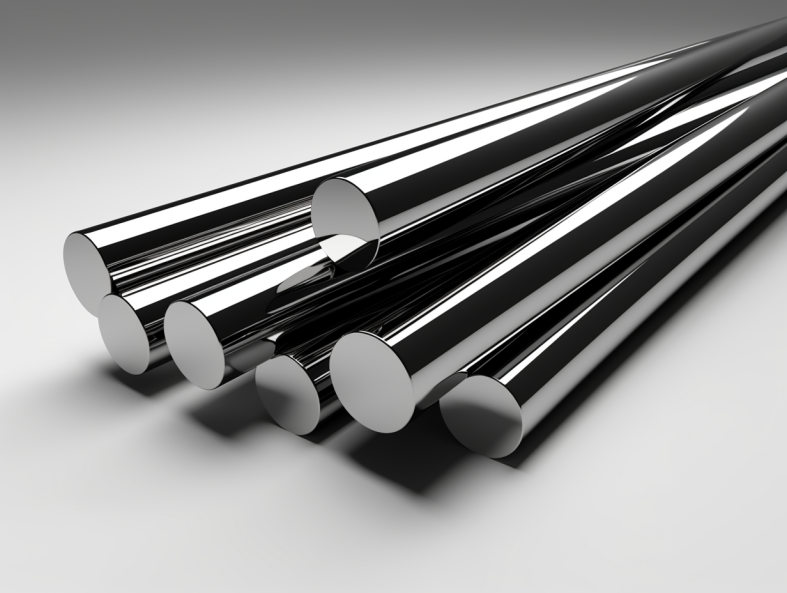
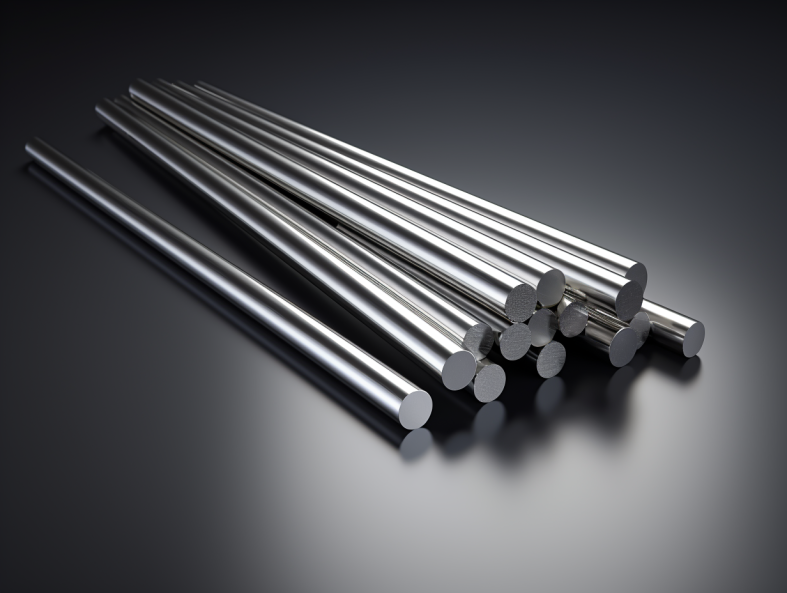
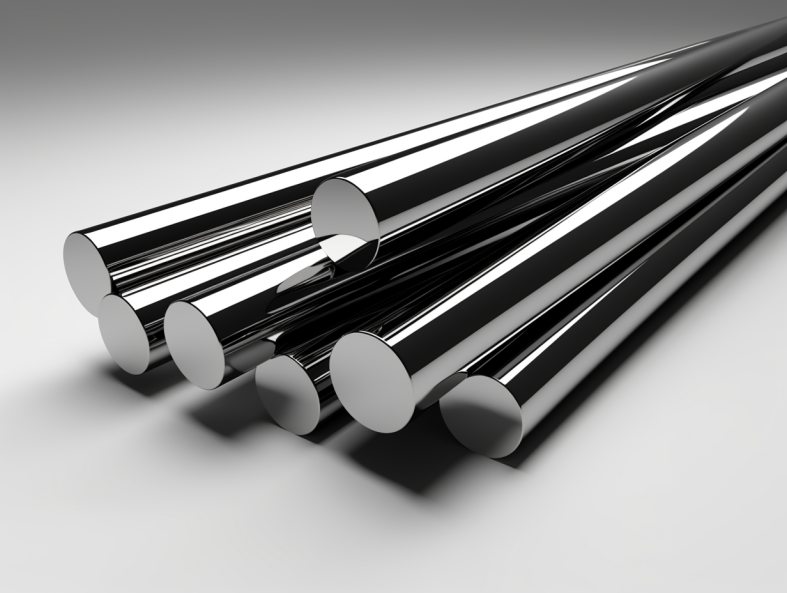
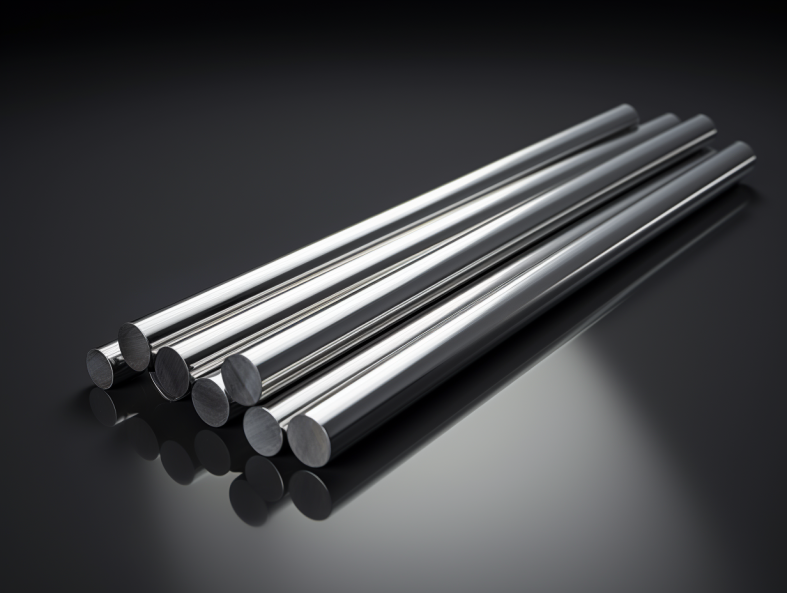
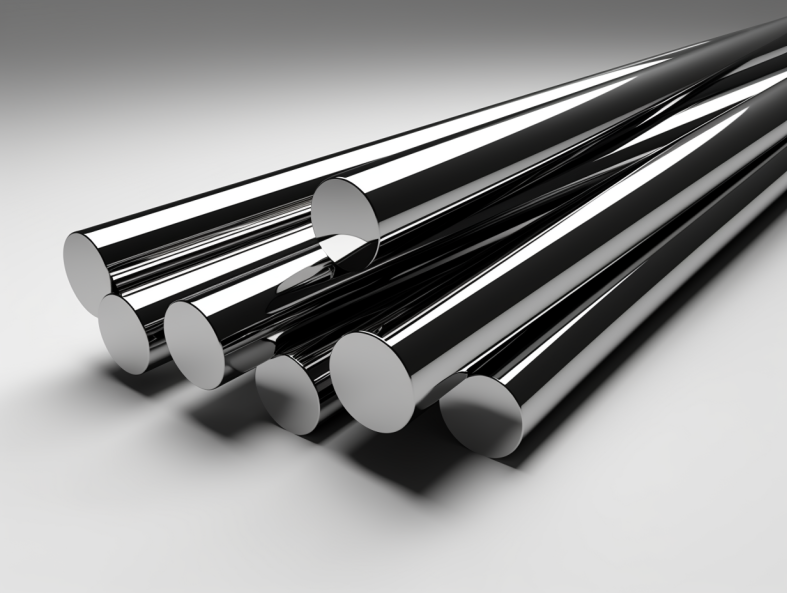
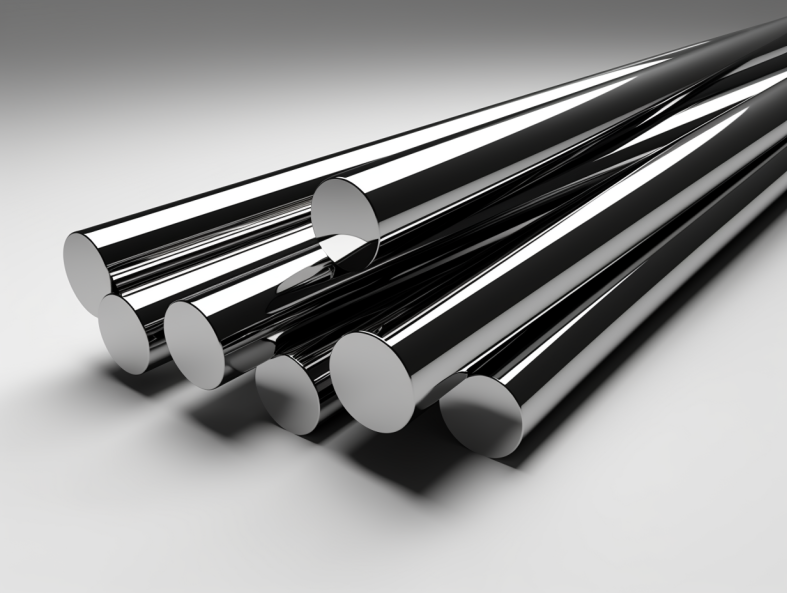
Hardness, Strength, and Wear Resistance
These three properties are critical for evaluating the performance of tungsten carbide rods:
Model | Hardness (HRA) | Strength (MPa) | Wear Resistance |
---|---|---|---|
YG6 | 89.5 | 2250 | High |
YG8 | 88.5 | 2200 | High |
YG10X | 92.0 | 2100 | Very High |
YG15 | 86.0 | 2400 | Moderate |
YG20 | 84.0 | 2500 | Moderate |
YG20C | 83.5 | 2550 | High |
YG30 | 82.0 | 2600 | Moderate |
ZK10UF | 91.0 | 2150 | Very High |
K44 | 88.0 | 2300 | High |
CD650 | 86.5 | 2350 | High |
Specifications, Sizes, Shape, Standards
Tungsten carbide rods come in various specifications, sizes, and shapes. Here’s a look:
Specification | Size Range (mm) | Shape | Standards |
---|---|---|---|
YG6 | Diameter: 1-30, Length: 50-310 | Round, square | ISO 9001, ASTM B777 |
YG8 | Diameter: 1-30, Length: 50-310 | Round, square | ISO 9001, ASTM B777 |
YG10X | Diameter: 1-30, Length: 50-310 | Round, square | ISO 9001, ASTM B777 |
YG15 | Diameter: 1-30, Length: 50-310 | Round, square | ISO 9001, ASTM B777 |
YG20 | Diameter: 1-30, Length: 50-310 | Round, square | ISO 9001, ASTM B777 |
YG20C | Diameter: 1-30, Length: 50-310 | Round, square | ISO 9001, ASTM B777 |
YG30 | Diameter: 1-30, Length: 50-310 | Round, square | ISO 9001, ASTM B777 |
ZK10UF | Diameter: 1-20, Length: 50-310 | Round, square | ISO 9001, ASTM B777 |
K44 | Diameter: 1-30, Length: 50-310 | Round, square | ISO 9001, ASTM B777 |
CD650 | Diameter: 1-30, Length: 50-310 | Round, square | ISO 9001, ASTM B777 |
Selecting the Right Tungsten Carbide Rod for Cutting Tools
Choosing the right tungsten carbide rod involves considering various factors:
Consideration | Description |
---|---|
Material to be Cut | Different grades of tungsten carbide rods are suited for different materials (e.g., non-ferrous metals, hard steel). |
Cutting Conditions | Consider the cutting speed, feed rate, and depth of cut. |
Tool Design | The design of the cutting tool can influence the choice of tungsten carbide rod. |
Wear Resistance | Higher wear resistance is needed for abrasive materials. |
Toughness | Higher toughness is required for interrupted cuts and heavy-duty applications. |
Thermal Conductivity | Efficient heat dissipation is important for maintaining cutting performance. |
Supplier Reputation | Choose reputable suppliers to ensure quality and reliability. |
Cost | Balance the cost with the required performance characteristics. |
Advantages and Limitations
Understanding the advantages and limitations can help in making an informed choice:
Advantages | Limitations |
---|---|
Extremely high hardness and wear resistance | Can be brittle and prone to fracture under high impact |
High thermal conductivity | Higher cost compared to other materials |
Excellent performance in high-speed cutting | May require specialized tools and equipment for machining |
Long tool life, reducing replacement frequency | Can be difficult to shape and grind |
Suitable for a wide range of materials | Not as tough as some other tool materials like HSS |
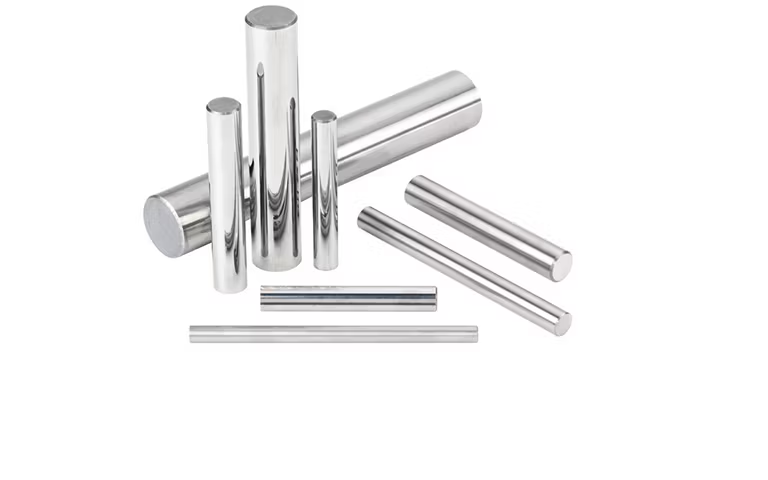
FAQs
Question | Answer |
---|---|
What is tungsten carbide? | Tungsten carbide is a compound of tungsten and carbon, known for its hardness and durability. |
Why is tungsten carbide used in cutting tools? | Its high hardness and wear resistance make it ideal for cutting and machining applications. |
How is tungsten carbide rod made? | It’s made by sintering tungsten carbide powder with a binder metal like cobalt. |
What are the types of tungsten carbide rods? | Various grades like YG6, YG8, YG10X, each suited for different applications. |
How to select the right tungsten carbide rod? | Consider factors like material to be cut, cutting conditions, and tool design. |
What are the advantages of tungsten carbide? | High hardness, wear resistance, and long tool life. |
What are the limitations of tungsten carbide? | Brittleness and higher cost compared to other materials. |
Can tungsten carbide rods be recycled? | Yes, they can be recycled and reused in new tools. |
What is the typical cost of tungsten carbide rods? | Prices range from $45 to $90 per kg depending on the grade and supplier. |
Who are the major suppliers of tungsten carbide rods? | Companies like Kennametal, Sandvik, Ceratizit, and Mitsubishi Materials. |