What is Tungsten Carbide Powder?
Tungsten carbide powder (WC) is a high-performance material widely used in industrial applications due to its exceptional hardness, wear resistance, and high melting point. This fine powder is composed of tungsten (W) and carbon (C), forming a dense crystalline structure that rivals diamonds in terms of hardness. It is the primary raw material for producing tungsten carbide-based products such as cutting tools, wear-resistant parts, and abrasives.
Why is tungsten carbide so popular? Think of it like the superhero of metal powders – strong, resilient, and practically indestructible under extreme conditions. It’s a staple in industries like mining, aerospace, and manufacturing because it can withstand significant wear and tear.
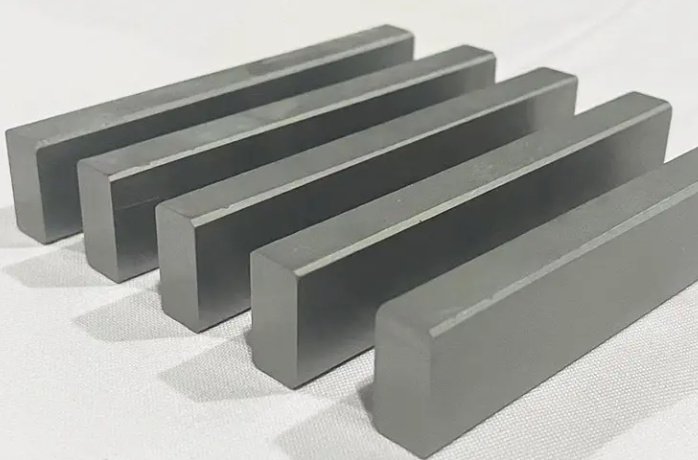
Tungsten Carbide Powder Production Process
Producing high-quality tungsten carbide powder involves multiple steps to ensure its purity and superior mechanical properties. Let’s break it down:
1. Raw Material Preparation
- Tungsten ore (scheelite or wolframite) is extracted from mines.
- The ore is then processed through concentration, refining, and chemical treatment to obtain ammonium paratungstate (APT), a precursor for tungsten powder.
2. Tungsten Powder Reduction
- APT is heated in a hydrogen atmosphere at high temperatures, reducing it to pure tungsten powder.
- The process ensures fine particle sizes, which are crucial for the final properties of tungsten carbide.
3. Carbonization Process
- Tungsten powder is mixed with high-purity carbon black.
- This mixture is heated to 1,400-2,000°C in a controlled atmosphere.
- The reaction forms tungsten carbide powder, which is then milled and classified based on grain size.
4. Quality Control and Refinement
- The final product undergoes rigorous testing to ensure its particle distribution, chemical purity, and hardness meet industrial standards.
- The powder is then packaged for various industrial applications.
Applications of Tungsten Carbide Powder
Tungsten carbide powder is indispensable across multiple industries. But where exactly is it used? Let’s take a look:
1. Cutting Tools and Machining
- Used in drill bits, end mills, and cutting inserts for metalworking.
- Provides extended tool life compared to high-speed steel (HSS).
2. Wear-Resistant Components
- Ideal for pump parts, nozzles, and bearings in high-friction environments.
- Offers superior wear resistance, reducing maintenance costs.
3. Mining and Drilling
- Essential for rock drilling, oil exploration, and tunneling tools.
- Withstands extreme pressure and abrasive conditions.
4. Aerospace and Defense
- Applied in aircraft turbine blades and armor-piercing projectiles.
- Enhances durability and performance under extreme conditions.
5. Medical and Industrial Applications
- Used in surgical instruments and radiation shielding materials.
- Ensures high precision and reliability in medical tools.
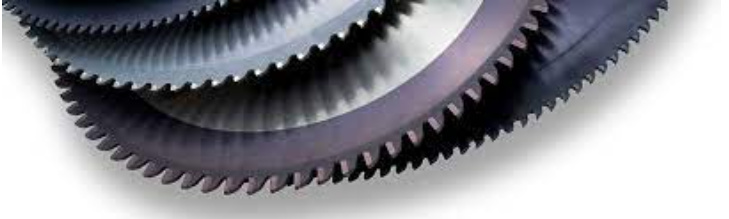
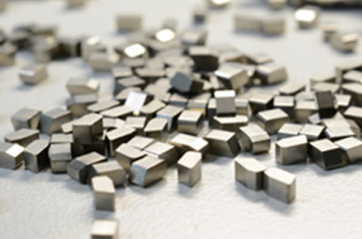
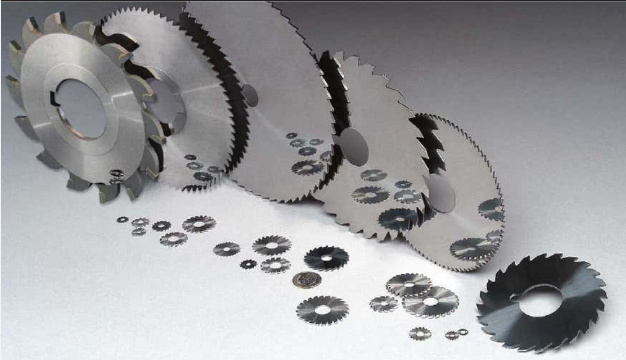
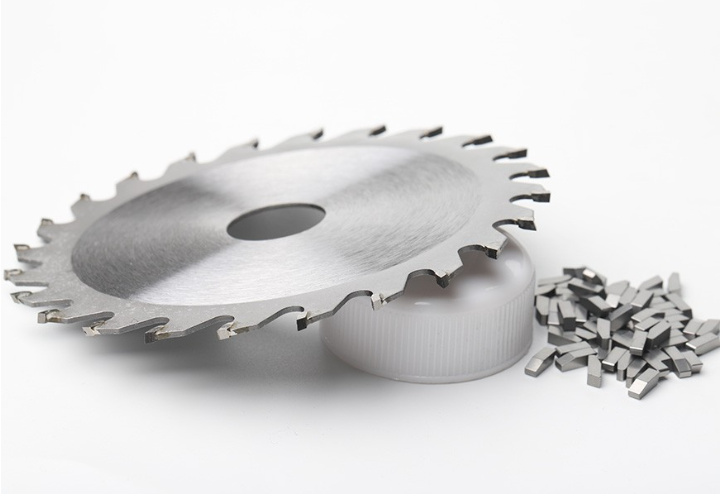
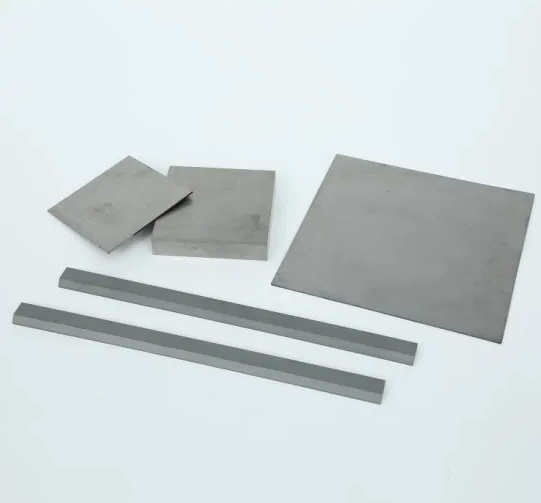
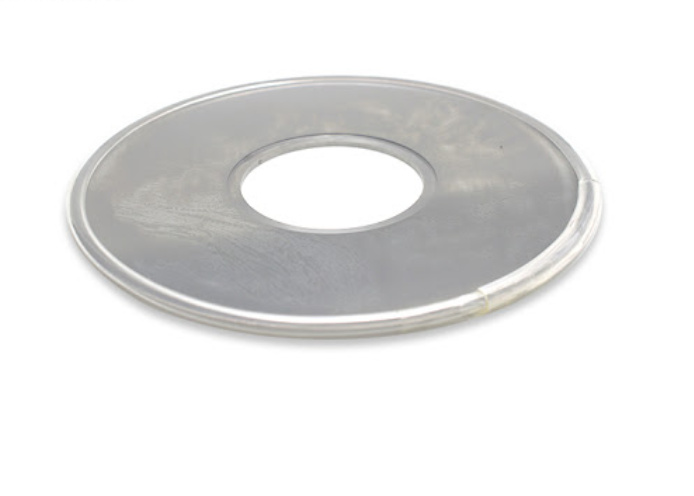
Market Trends and Future Prospects of Tungsten Carbide Powder Processing
Market Factor | Current Trend | Future Projection |
---|---|---|
Demand in Automotive Industry | High demand for cutting and wear-resistant tools | Expected to grow due to increasing automation |
Technological Innovations | Nanostructured tungsten carbide development | Enhanced properties with better efficiency |
Raw Material Availability | Stable supply but subject to geopolitical factors | Possible price fluctuations impacting production costs |
Environmental Regulations | Stricter regulations on tungsten mining | Emphasis on recycling and sustainable sourcing |
Expansion in Aerospace and Defense | Growing application in high-performance materials | Further R&D into lightweight yet strong composites |
How to Choose a Reliable Tungsten Carbide Powder Supplier?
Factor | Why It Matters? | What to Look For? |
---|---|---|
Purity and Quality | Ensures superior performance | Supplier must provide quality certifications (ISO, ASTM) |
Customization Options | Different applications require specific grain sizes | Supplier should offer a variety of grades and sizes |
Technical Support | Proper guidance ensures better application | Look for suppliers with strong R&D and technical support |
Pricing and Delivery | Affects project costs and timelines | Competitive pricing and reliable shipping |
Sustainability | Environmental concerns are growing | Suppliers should focus on ethical sourcing and recycling programs |
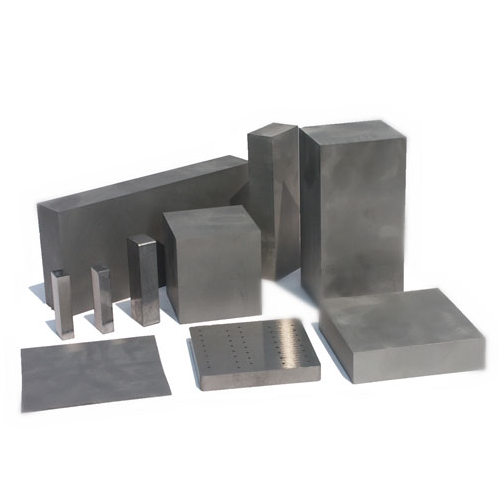
FAQ
Question | Answer |
---|---|
What is the typical hardness of tungsten carbide powder? | Tungsten carbide powder has a hardness of about 9 on the Mohs scale, just below diamond. |
How is tungsten carbide powder different from tungsten metal? | Tungsten carbide is much harder and more wear-resistant than pure tungsten metal. It is formed by combining tungsten with carbon. |
Can tungsten carbide powder be recycled? | Yes! Many industries are focusing on recycling tungsten carbide due to environmental and cost-saving benefits. |
What are the main factors affecting tungsten carbide powder quality? | Purity, particle size distribution, carbon content, and production method play crucial roles. |
Why is tungsten carbide used in high-performance tools? | Its extreme hardness, durability, and heat resistance make it ideal for machining and drilling applications. |
How does tungsten carbide powder compare to ceramic materials? | While ceramics offer heat resistance, tungsten carbide provides better toughness and impact resistance. |