Overview of Tungsten Carbide
Tungsten carbide is a compound of tungsten and carbon, recognized for its incredible hardness and durability. Often compared to diamonds in terms of hardness, tungsten carbide is an essential material in various industrial applications, ranging from cutting tools to armor-piercing ammunition. But today, we’ll focus on a specific form of tungsten carbide: plates. These plates are indispensable in manufacturing, mining, and other heavy-duty industries.
Why are tungsten carbide plates so popular? Well, imagine trying to cut through a tough metal with a regular steel blade. It’s like using a butter knife on a tree branch—not very effective, right? Tungsten carbide, on the other hand, offers superior wear resistance, making it the go-to material for tools and applications where durability is paramount.
Importance of Tungsten Carbide Plates in Industrial Applications
Tungsten carbide plates are the unsung heroes in many industries. They’re the silent workhorses that endure immense pressure, resist wear and tear, and maintain their integrity under the harshest conditions. Whether it’s in mining operations, where they break down rock and ore, or in metalworking, where precision and durability are key, tungsten carbide plates perform where others fail.
Choosing the right supplier for these plates isn’t just about finding a vendor; it’s about securing the backbone of your operations. A high-quality plate can be the difference between a smooth-running machine and one that’s constantly breaking down. The right supplier ensures that you receive consistent, high-quality plates that meet the demands of your specific applications.
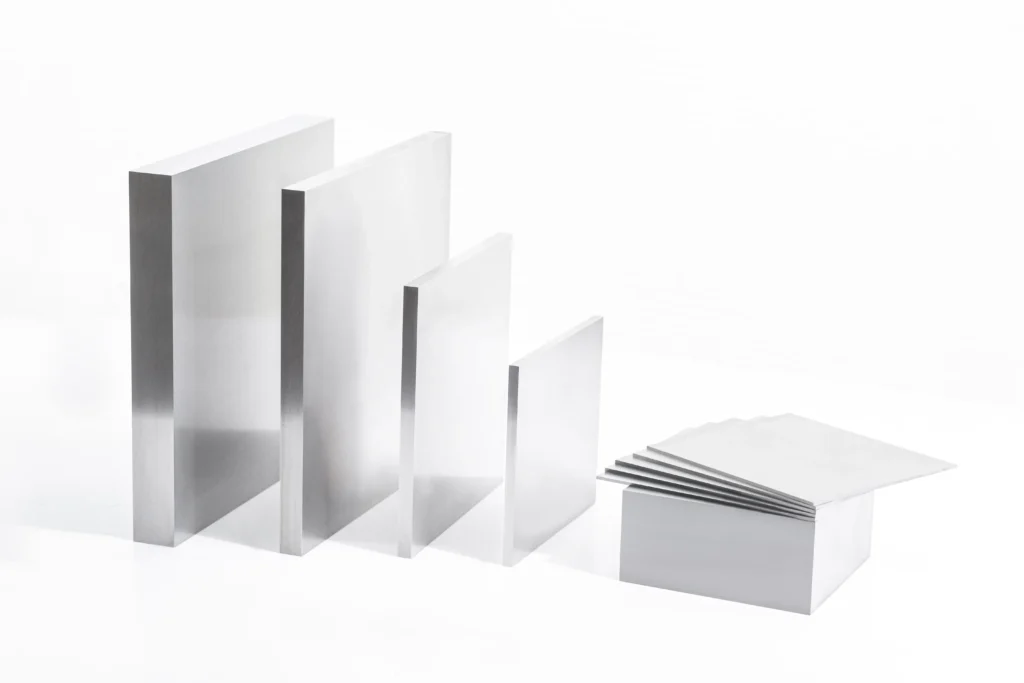
Why Choosing the Right Supplier Matters
So, why does selecting the right supplier make such a difference? Think of it this way: you wouldn’t trust just any mechanic to work on your car, especially if it’s your livelihood. Similarly, the supplier of your tungsten carbide plates plays a crucial role in your business’s efficiency and success.
A reliable supplier provides not only top-notch products but also the support and consistency that ensure your operations run smoothly. In contrast, an unreliable supplier might save you money upfront but could cost you more in the long run due to lower-quality products, inconsistent delivery times, or poor customer service.
Understanding Tungsten Carbide Plates
What are Tungsten Carbide Plates?
Tungsten carbide plates are flat, rectangular blocks of tungsten carbide, often used in applications where high levels of hardness, wear resistance, and durability are required. These plates can be custom-cut or molded into various shapes and sizes, depending on the specific needs of the application.
But what exactly makes tungsten carbide so special? Let’s break it down. Tungsten carbide is created by combining tungsten, a heavy metal known for its high melting point, with carbon, a non-metal that provides hardness. The result is a material that’s incredibly tough and resistant to abrasion, making it ideal for use in harsh environments.
Whether used in cutting tools, molds, or as wear-resistant parts in machinery, tungsten carbide plates offer unmatched performance. They’re the unsung champions of the industrial world, taking on the toughest tasks without breaking a sweat.
Properties and Characteristics of Tungsten Carbide Plates
Let’s dive into the properties that make tungsten carbide plates stand out:
- Hardness: Tungsten carbide is renowned for its hardness, second only to diamonds. This makes it incredibly resistant to wear and tear, ensuring longevity in demanding applications.
- Density: Tungsten carbide is dense, which contributes to its strength and durability. This density also provides the heft needed in various industrial processes.
- Wear Resistance: One of the standout features of tungsten carbide plates is their wear resistance. They can withstand continuous use in abrasive environments, making them ideal for cutting tools and machinery parts.
- Corrosion Resistance: Tungsten carbide is also resistant to corrosion, which extends the lifespan of the plates, even in environments where they’re exposed to chemicals or moisture.
- Thermal Conductivity: Tungsten carbide conducts heat efficiently, which is crucial in applications where temperature control is necessary.
These characteristics make tungsten carbide plates indispensable in industries where performance, longevity, and reliability are non-negotiable.
Material Properties of Tungsten Carbide Plates
Property | Description |
---|---|
Hardness | 8.5-9.0 Mohs |
Density | 15.7-15.8 g/cm³ |
Wear Resistance | High, capable of withstanding harsh abrasive conditions |
Corrosion Resistance | Excellent, especially when exposed to chemicals or moisture |
Thermal Conductivity | Good, with a thermal conductivity of 84-92 W/m.K |
Melting Point | 2,870°C |
Tensile Strength | 350-400 MPa |
Compressive Strength | 4,500-6,500 MPa |
Composition and Characteristics
Element | Percentage (%) | Characteristics |
---|---|---|
Tungsten (W) | 70-97 | Provides strength, density, and high melting point |
Carbon (C) | 3-30 | Adds hardness and wear resistance |
Cobalt (Co) | 0-15 | Acts as a binder, enhancing toughness and making the material easier to work with |
Nickel (Ni) | 0-10 | Another binder alternative to cobalt, offering different mechanical properties |
Titanium (Ti) | 0-5 | Increases hardness, resistance to deformation, and corrosion resistance |
Tantalum (Ta) | 0-3 | Adds toughness and thermal stability |
Types of Tungsten Carbide Plates
Different Models of Tungsten Carbide Plates
Tungsten carbide plates come in various models, each designed for specific applications. Understanding these models is crucial for selecting the right plate for your needs. Let’s explore some of the most commonly used models.
Specific Metal Powder Models of Tungsten Carbide Plates
Model | Description |
---|---|
WC-Co 85/15 | 85% tungsten carbide, 15% cobalt. Excellent for wear parts, such as dies and punches. |
WC-Co 94/6 | 94% tungsten carbide, 6% cobalt. Ideal for cutting tools requiring high hardness. |
WC-Ni 90/10 | 90% tungsten carbide, 10% nickel. Used in applications requiring corrosion resistance. |
WC-TiC-Co 80/20 | Tungsten carbide-titanium carbide blend, with 20% cobalt. Superior wear resistance. |
WC-Co 97/3 | 97% tungsten carbide, 3% cobalt. Preferred for ultra-hard tools and parts. |
WC-Co 88/12 | 88% tungsten carbide, 12% cobalt. Balances hardness and toughness for machining tools. |
WC-Ni 85/15 | 85% tungsten carbide, 15% nickel. Best for corrosive environments like chemical plants. |
WC-Co 92/8 | 92% tungsten carbide, 8% cobalt. Used in precision tools requiring wear resistance. |
WC-TaC-Co 80/20 | Tungsten carbide-tantalum carbide blend, with 20% cobalt. High-temperature applications. |
WC-Co 90/10 | 90% tungsten carbide, 10% cobalt. Excellent for heavy-duty cutting tools and drill bits. |
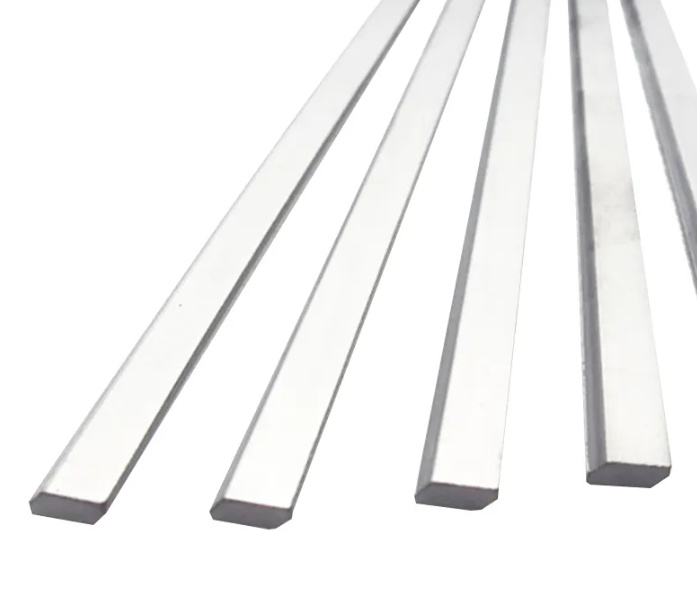
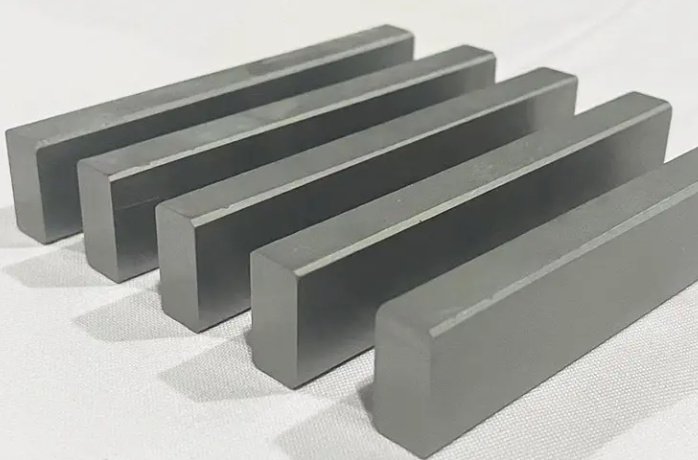
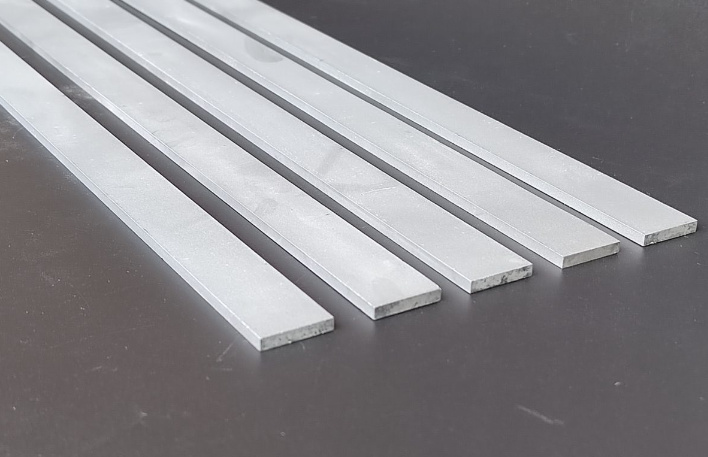
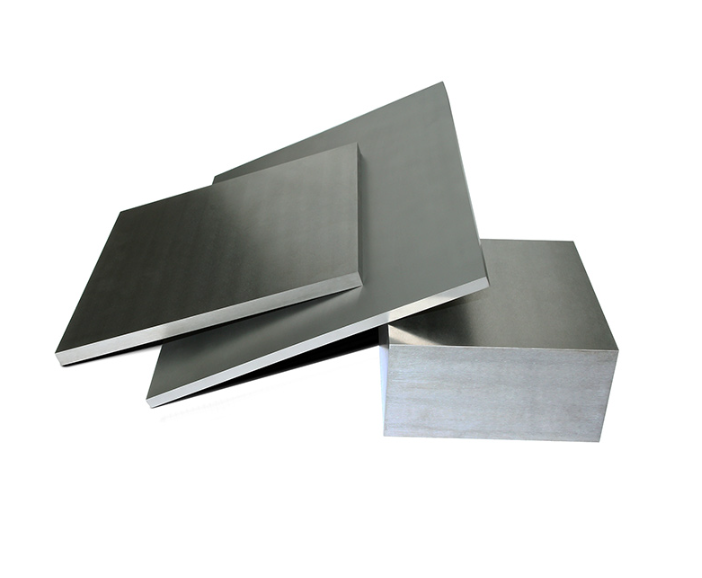
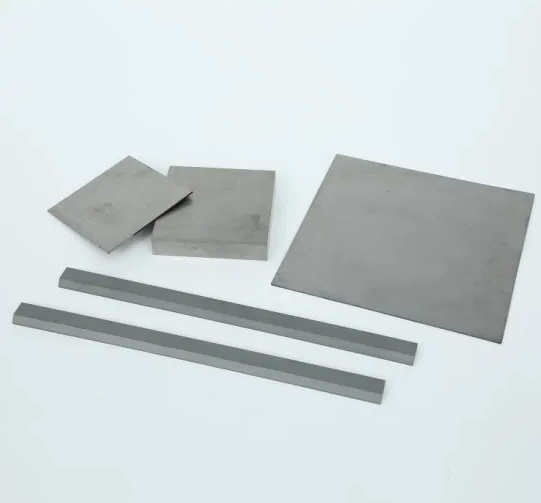
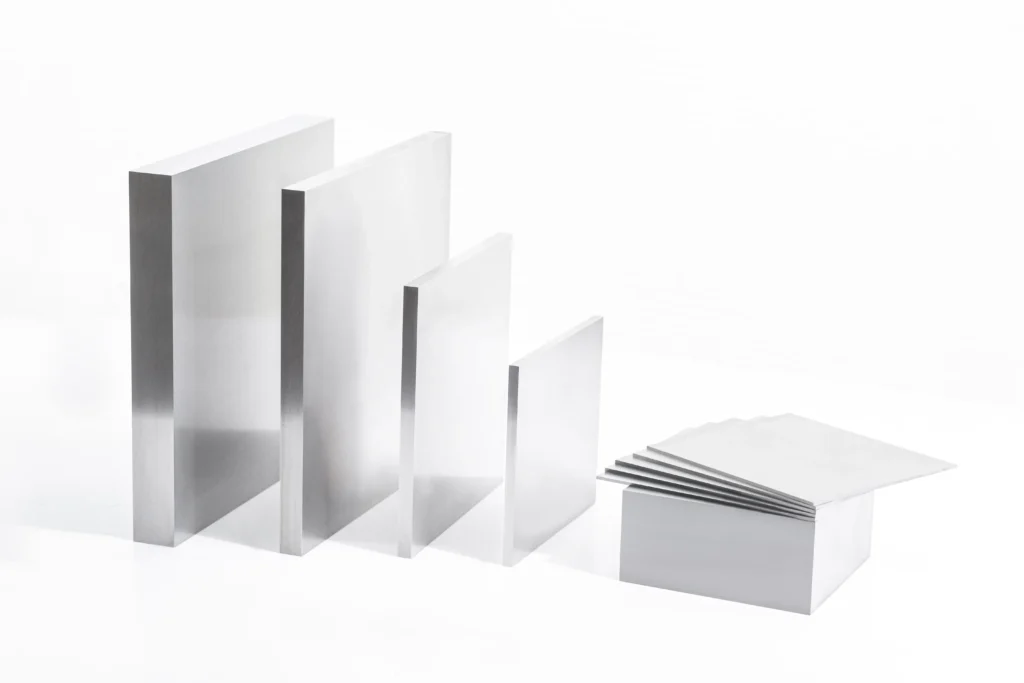
Explanation of Each Model and Their Uses
Now that we’ve listed the models, let’s break down what makes each one tick.
- WC-Co 85/15: This model is a workhorse in manufacturing. The blend of 85% tungsten carbide and 15% cobalt makes it tough yet versatile. It’s commonly used in dies and punches where repeated stress is the norm.
- WC-Co 94/6: With a higher tungsten carbide content, this model excels in cutting tools. The 6% cobalt acts as a binder, maintaining the material’s integrity while allowing for precise, clean cuts in hard materials.
- WC-Ni 90/10: Nickel as a binder provides superior corrosion resistance, making this model ideal for applications where the plates are exposed to corrosive substances, like in chemical processing plants.
- WC-TiC-Co 80/20: The addition of titanium carbide enhances wear resistance, making this model perfect for environments where abrasion is a significant concern. It’s often used in cutting tools and mining equipment.
- WC-Co 97/3: For the most demanding applications where maximum hardness is required, this model shines. With 97% tungsten carbide, it’s nearly as hard as diamonds, making it ideal for ultra-hard tools.
- WC-Co 88/12: This model strikes a balance between hardness and toughness, making it versatile for machining tools that need to maintain sharpness without being brittle.
- WC-Ni 85/15: Like its 90/10 counterpart, this model excels in corrosive environments. The higher nickel content offers additional corrosion resistance, making it suitable for chemical plants and similar settings.
- WC-Co 92/8: Precision tools benefit from this model’s balance of wear resistance and toughness. The 8% cobalt ensures the plate can withstand fine, intricate work without chipping or breaking.
- WC-TaC-Co 80/20: Tantalum carbide enhances this model’s performance in high-temperature applications, such as in the aerospace and automotive industries.
- WC-Co 90/10: This model is a favorite for heavy-duty applications, like drill bits and large cutting tools, where both durability and hardness are essential.
Applications of Tungsten Carbide Plates
Industries That Rely on Tungsten Carbide Plates
Tungsten carbide plates are integral to numerous industries, thanks to their durability, hardness, and resistance to wear. Let’s explore some of the key industries that depend on these plates.
Applications of Tungsten Carbide Plates by Industry
Industry | Applications |
---|---|
Mining | Drill bits, rock crushers, wear parts in excavation machinery. |
Metalworking | Cutting tools, dies, punches, and molds. |
Oil & Gas | Wear-resistant parts in drilling and extraction equipment. |
Aerospace | High-temperature resistant parts, cutting tools for composites. |
Automotive | Engine components, tooling for manufacturing, precision parts. |
Construction | Heavy-duty cutting tools, wear plates for machinery. |
Defense | Armor-piercing ammunition, protective plates, and impact-resistant parts. |
Chemical Processing | Corrosion-resistant parts, valves, and pump components. |
Electronics | Molds for semiconductor production, cutting tools for microcomponents. |
Jewelry Manufacturing | Tooling for cutting and shaping, as well as wear-resistant dies. |
Specific Applications and How They Benefit from Tungsten Carbide
- Mining: In the mining industry, tungsten carbide plates are essential for drill bits and rock crushers. Their hardness and wear resistance allow them to break down tough materials without frequent replacements, reducing downtime and increasing efficiency.
- Metalworking: Tungsten carbide is a staple in metalworking, particularly in cutting tools and molds. The ability to maintain sharpness and resist wear under high-pressure conditions makes these plates invaluable in this sector.
- Oil & Gas: The oil and gas industry uses tungsten carbide plates in drilling and extraction equipment, where they must withstand high pressure and abrasive materials. Their durability ensures the longevity of the equipment, even in harsh environments.
- Aerospace: High-temperature resistance is crucial in aerospace applications, where tungsten carbide plates are used in parts that must perform reliably under extreme conditions. These plates are also used in cutting tools for composite materials, which are common in modern aircraft.
- Automotive: In the automotive industry, tungsten carbide plates are used in engine components and tooling for manufacturing processes. Their precision and durability are essential for producing high-quality parts that meet strict safety standards.
- Construction: Heavy-duty construction machinery relies on tungsten carbide plates for cutting tools and wear-resistant parts. These plates help extend the life of the equipment, reducing the need for frequent maintenance.
- Defense: Tungsten carbide’s hardness makes it ideal for armor-piercing ammunition and protective plates used in military applications. Its impact resistance ensures that it can withstand the most demanding conditions.
- Chemical Processing: In chemical processing plants, corrosion-resistant tungsten carbide plates are used in valves, pumps, and other components exposed to aggressive chemicals. Their ability to resist corrosion extends the life of the equipment.
- Electronics: The precision required in electronics manufacturing makes tungsten carbide the material of choice for molds and cutting tools used in the production of semiconductors and microcomponents.
- Jewelry Manufacturing: Even in the delicate world of jewelry making, tungsten carbide plates play a role in cutting and shaping materials, as well as in wear-resistant dies used to create intricate designs.
Selecting the Right Tungsten Carbide Plate Supplier
Factors to Consider When Choosing a Supplier
Selecting the right tungsten carbide plate supplier can feel like a daunting task. But don’t worry; I’m here to guide you through the process. When choosing a supplier, consider the following factors:
- Quality Assurance: Ensure the supplier provides consistent, high-quality tungsten carbide plates. Ask about their quality control processes and certifications.
- Customization Options: Depending on your needs, you might require custom sizes, shapes, or compositions. A good supplier should offer flexibility and customization.
- Pricing: While cost shouldn’t be the only factor, it’s crucial to find a supplier who offers competitive pricing without compromising on quality.
- Lead Time: How quickly can the supplier deliver your order? Reliability in meeting deadlines is critical, especially in industries where downtime can be costly.
- Technical Support: Does the supplier offer technical support or advice on selecting the right tungsten carbide plates? Their expertise can be invaluable.
- Reputation: Check reviews, testimonials, and references to gauge the supplier’s reputation in the industry. A well-regarded supplier is more likely to provide high-quality products and service.
Questions to Ask Potential Suppliers
When vetting potential suppliers, don’t hesitate to ask questions. Here are a few to get you started:
- What is your minimum order quantity?
- Can you provide references from clients in my industry?
- What are your standard lead times for tungsten carbide plates?
- Do you offer customization services?
- What quality control measures do you have in place?
- Can you provide material certifications and test reports?
How to Select the Right Tungsten Carbide Plate
Criteria | Importance |
---|---|
Quality Assurance | High – Ensures reliability and performance in your applications. |
Customization Options | Medium – Important if you need specific shapes, sizes, or compositions. |
Pricing | Medium – Balance cost with quality to get the best value. |
Lead Time | High – Critical for maintaining production schedules. |
Technical Support | Medium – Valuable for selecting the right plate and resolving issues. |
Reputation | High – Indicates reliability and customer satisfaction. |
Comparing Tungsten Carbide Plate Suppliers
What Sets Suppliers Apart?
In a competitive market, what truly sets tungsten carbide plate suppliers apart? The answer lies in a combination of quality, service, and expertise. While many suppliers might offer similar products, the difference often comes down to the details: the quality of the material, the consistency of the plates, the level of customer support, and the ability to meet specific requirements.
Some suppliers specialize in certain industries, offering tailored solutions that cater to the unique needs of those sectors. Others might differentiate themselves through innovative manufacturing processes or by offering additional services like custom fabrication or technical support.
When comparing suppliers, consider the following:
- Product Range: Does the supplier offer a wide range of tungsten carbide plates, including various grades and sizes?
- Customization Capabilities
: Can they accommodate special requests or provide custom solutions?
- Quality Control: What processes do they have in place to ensure product consistency and quality?
- Customer Service: How responsive and helpful is their customer support team?
- Pricing: Are their prices competitive without sacrificing quality?
- Lead Times: How quickly can they fulfill orders?
Price vs. Quality: Striking the Right Balance
Balancing price and quality is often the biggest challenge when selecting a supplier. It’s tempting to go for the cheapest option, but as the saying goes, “You get what you pay for.” Lower prices might mean lower quality materials, which can lead to higher costs down the line due to increased wear, frequent replacements, or even machine downtime.
Conversely, the most expensive option isn’t always the best either. It’s about finding a supplier who offers the right balance: high-quality tungsten carbide plates at a fair price, with the service and support to match.
Comparing Suppliers by Price, Quality, and Service
Supplier | Price | Quality | Customization | Lead Time | Customer Service |
---|---|---|---|---|---|
Supplier A | $$$ | High | Yes | 2 weeks | Excellent |
Supplier B | $$ | Medium | No | 1 week | Good |
Supplier C | $$$$ | Very High | Yes | 3 weeks | Excellent |
Supplier D | $ | Low | No | 4 weeks | Fair |
Supplier E | $$$ | High | Yes | 2 weeks | Excellent |
Technical Specifications of Tungsten Carbide Plates
Understanding Specifications and Standards
When dealing with tungsten carbide plates, understanding technical specifications is crucial. These specs define the material’s performance and suitability for different applications. Whether you’re looking at hardness, grain size, or composition, each specification tells you something important about how the plate will perform under certain conditions.
Specifications often include:
- Hardness: Measured on the Mohs scale, it indicates the material’s resistance to scratching and abrasion.
- Grain Size: Finer grains often result in harder, more wear-resistant materials, while coarser grains can improve toughness.
- Binder Content: Typically cobalt or nickel, the binder holds the tungsten carbide particles together and influences the plate’s toughness.
- Tolerances: These define the acceptable limits for variations in size, shape, and other dimensions.
- Surface Finish: The smoothness of the plate’s surface, which can affect how it interacts with other materials or components.
How to Interpret Material Grades and Tolerances
Material grades and tolerances can seem like a foreign language, but once you understand them, they’re invaluable in selecting the right tungsten carbide plate. Here’s a quick guide:
- Grades: These are often designated by a combination of letters and numbers (e.g., WC-Co 94/6). The letters indicate the material type, while the numbers typically represent the percentage composition of tungsten carbide and the binder.
- Tolerances: Expressed as a range or a maximum/minimum value, tolerances ensure that the plates meet specific dimensional requirements. For example, a tolerance of ±0.01 mm means the plate’s dimensions can vary by up to 0.01 mm from the specified size.
Specifications, Sizes, Shapes, and Standards
Specification | Description |
---|---|
Hardness | 8.5-9.0 Mohs |
Grain Size | Fine (1-5 microns) |
Binder Content | 6-15% (Cobalt or Nickel) |
Tolerances | ±0.01 mm |
Surface Finish | Ra 0.2-0.8 µm (Fine ground) |
Standard Sizes | 100×100 mm, 200×200 mm, 300×300 mm |
Custom Sizes | Available upon request |
Shapes Available | Rectangular, Square, Custom |
International Standards | ISO 9001, ISO 45001, ASTM B777, DIN 5468, JIS Z2550 |
Advantages and Disadvantages of Tungsten Carbide Plates
What Makes Tungsten Carbide Plates Superior?
Tungsten carbide plates offer several advantages that make them superior to other materials in various applications:
- Exceptional Hardness: As one of the hardest materials available, tungsten carbide is unmatched in its ability to resist wear and tear.
- Durability: These plates last longer than those made from steel or other metals, reducing the need for frequent replacements.
- Heat Resistance: Tungsten carbide can withstand high temperatures without losing its structural integrity, making it ideal for high-heat applications.
- Corrosion Resistance: In environments where moisture or chemicals are present, tungsten carbide resists corrosion, extending the life of the plate.
- Versatility: Whether in mining, construction, or metalworking, tungsten carbide plates can be used across a wide range of industries.
Potential Drawbacks and Considerations
While tungsten carbide plates are impressive, they’re not without their drawbacks:
- Brittleness: Despite their hardness, tungsten carbide plates can be brittle, especially under impact or when subjected to high stress without adequate support.
- Cost: The superior properties of tungsten carbide come at a price. These plates are generally more expensive than alternatives like steel or ceramic.
- Machining Difficulty: Tungsten carbide is challenging to machine due to its hardness, requiring specialized tools and techniques.
- Weight: Tungsten carbide is dense and heavy, which can be a disadvantage in applications where weight is a concern.
Advantages and Limitations of Tungsten Carbide Plates
Advantages | Limitations |
---|---|
High Hardness | Brittleness – Can crack under impact |
Wear Resistance | Cost – Higher than alternative materials |
Thermal Stability | Machining Difficulty – Requires special tools |
Corrosion Resistance | Weight – Heavier than other materials |
Long Lifespan | Limited Flexibility – Not ideal for all applications |
Versatility | Environmental Impact – Tungsten mining can be ecologically damaging |
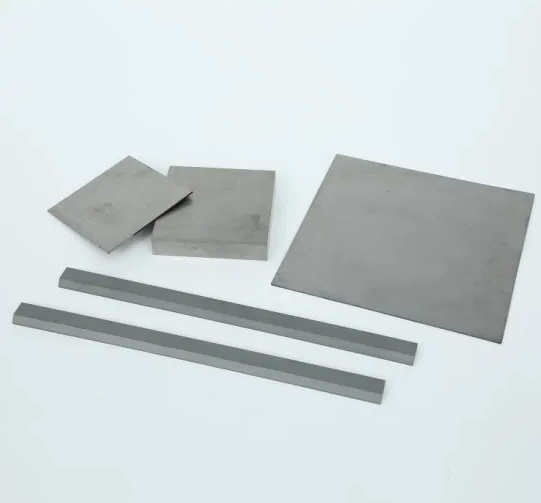
FAQ
Question | Answer |
---|---|
What is tungsten carbide? | Tungsten carbide is a compound of tungsten and carbon, known for its extreme hardness and durability. |
Why choose tungsten carbide plates? | They offer unmatched wear resistance, hardness, and longevity, making them ideal for demanding applications. |
What industries use tungsten carbide plates? | Industries like mining, metalworking, oil & gas, aerospace, automotive, construction, defense, chemical processing, and electronics. |
How do I choose the right tungsten carbide plate? | Consider the application’s requirements, including hardness, toughness, corrosion resistance, and temperature stability. |
Are tungsten carbide plates expensive? | Yes, they are generally more expensive than other materials due to their superior properties. |
Can tungsten carbide plates be customized? | Yes, many suppliers offer custom sizes, shapes, and compositions to meet specific needs. |
What are the alternatives to tungsten carbide? | Alternatives include steel, ceramics, and other carbide materials, though none offer the same combination of properties. |
How are tungsten carbide plates made? | They are typically made through powder metallurgy, where tungsten carbide powder is mixed with a binder, pressed into shape, and sintered. |
What is the typical lifespan of a tungsten carbide plate? | The lifespan varies depending on the application but generally exceeds that of other materials by a significant margin. |
Conclusion
Summarizing the Importance of Choosing the Right Supplier
Choosing the right tungsten carbide plate supplier is not just a business decision—it’s a strategic move that can impact the efficiency, reliability, and success of your operations. A high-quality supplier ensures that you get the best tungsten carbide plates tailored to your specific needs, backed by reliable customer service and technical support.
Final Thoughts and Recommendations
In a world where performance and durability are non-negotiable, tungsten carbide plates stand out as the material of choice. Whether you’re in mining, manufacturing, or any other industry that demands high performance, investing in quality tungsten carbide plates from a trusted supplier is a decision that pays off in the long run.
So, the next time you’re in the market for these essential components, remember to weigh your options carefully, ask the right questions, and prioritize quality over cost. After all, when it comes to tungsten carbide plates, cutting corners is never worth the risk.