tungsten carbide lathe tool inserts are widely used in metal cutting applications like turning, milling and drilling to efficiently machine parts to precision dimensions and fine surface finish thanks to their extreme hardness, wear resistance, and thermal properties. This guide offers a detailed look at various grades and geometries of tungsten carbide inserts specified for different materials and lathe turning operations.
Overview of tungsten carbide lathe tool inserts for Turning
Engineered with a hard carbide composition dispersed in tough cobalt metal matrix, tungsten carbide inserts are a popular choice of cutting tool material for single point turning and grooving in automatic lathes, screw machines, CNC lathes and machining centers owing to advantages like:
- Extreme hardness and wear resistance for high metal removal rates
- Strength to withstand cutting forces and shocks at elevated temperatures
- Thermal shock resistance for stable precision machining
- Chemically inert to work materials like steel, stainless steel, cast iron, heat resistant superalloys, titanium and nickel-based alloys
- Reusable by rotating/indexing to utilize multiple cutting edges
- Coated grades offer higher lubricity, heat resistance, wear protection
Proper insert shape, size, grade selection coupled with optimized operation parameters maximizes productivity in turning high performance alloys, tough aerospace materials and common engineering metals.
Types of tungsten carbide lathe tool inserts
Tungsten carbide inserts come in various standard sizes, geometries with special profiles, coatings and identifiers denoting grade to suit different workpiece attributes and machining requirements:
Tungsten Carbide Grades for Turning Inserts
Carbide grade influences strength, fracture toughness, heat and wear resistance. Common classifications:
Grade | Details | Typical Uses |
---|---|---|
C1-C4 | Straight tungsten carbides with 6-10% cobalt binder | General machining of low/medium alloy steels |
P10-P50 | Fine grained carbides for improved hardness and heat resistance | High speed steel turning applications |
M10-M40 | Tougher grades containing titanium carbide (TiC), tantalum carbide (TaC) additions | Tough materials like stainless steel, heat resistant superalloys |
K10-K40 | Containings specialized carbides like niobium carbide (NbC) for extreme wear resistance | Difficult-to-machine nickel alloys, hardened steels |
Higher grade number indicates better hot hardness, heat and wear resistance.
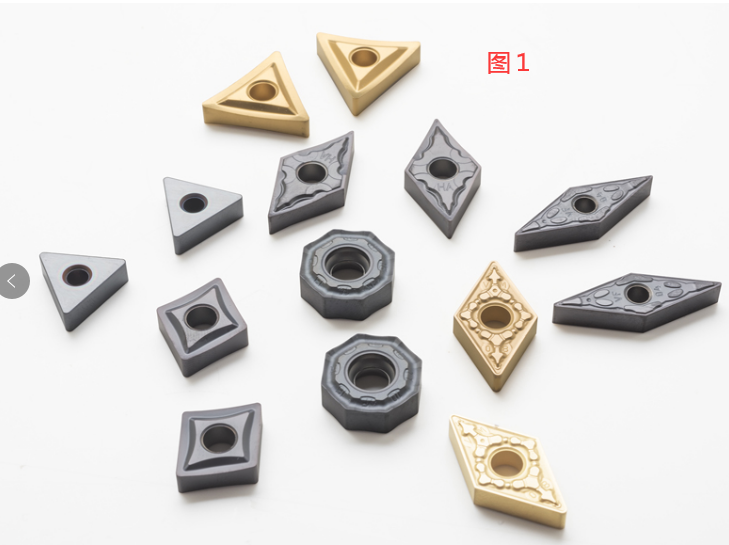
Tungsten Carbide Insert Coatings
Coating | Composition | Key Features |
---|---|---|
TiN | Titanium nitride | High hardness, lubricious golden finish |
TiCN | Titanium carbonitride | Resistance to heat and crater wear |
TiAlN | Titanium aluminum nitride | High hot hardness and oxidation resistance |
AlCrN | Aluminum chromium nitride | Excellent wear resistance and lubricity |
Multilayer, nanostructured, superlattice coatings can combine beneficial properties for demanding applications. Uncoated inserts are still widely used for short runs in easier materials.
Tungsten Carbide Insert Shapes/Styles for Turning
Common options include:
Shape | Features | Uses |
---|---|---|
Square | Four cutting edges, mechanical clamping | Low cost general purpose roughing |
Round | Round insert shape, center screw clamping | Finishing in grooves, rounds |
Trigon | Triangle shape with 3 cutting edges | Medium roughing applications |
Diamond | 35° rhombic shape for strength | Interrupted cuts, high feed mill-turn |
Dovetail | Special clamping groove geometry | High precision machining |
Various custom and proprietary shapes also offered for specific turning operations or tool holder systems.
In addition to shape, important insert dimensions like inscribed circle size, thickness, nose radius, lead angle and hand of cut determine suitability for facing, profiling, parting/grooving, boring, threading and other applications.
Properties of tungsten carbide lathe tool inserts
Key performance attributes stem from composition and microstructure:
Tungsten Carbide Insert Properties
Property | Role |
---|---|
Hardness | Resist deformation, enables faster metal removal |
Fracture toughness | Avoid brittle failure under machining loads |
Transverse rupture strength | Withstand cutting forces without breaking |
Resistance to plastic deformation | Retain shape accuracy and surface finish |
Thermal conductivity | Manage heat at tool-workpiece interface |
Coefficient of thermal expansion | Compatibility with substrate to prevent inserts popping out |
Grain size, binder content and composition are optimized in various carbide grades to maximize a combination of hardness, strength and toughness needed for specific machining scenarios.
Manufacturing Process for Tungsten Carbide Inserts
Key steps in fabrication of tungsten carbide turning inserts:
Tungsten Carbide Insert Manufacturing Sequence
Step | Details |
---|---|
Powder processing | Carbides like WC, TiC, TaC blended with Co binder |
Compaction | Pressing into green compact shape |
Sintering | 1300-1500°C furnace treatment to develop dense microstructure |
Grinding | Profile grinding to accurate geometry |
Edge preparation | Special edge treatments for chip control, less friction |
Coating | Optional PVD/CVD coating deposition |
Packaging | Protective packaging for shipment |
Strict process controls during mixing, pressing, sintering, edge preparation and coating result in precision inserts delivering consistent tool life and machining performance.
Applications of tungsten carbide lathe tool inserts
Tungsten carbide is extensively used for single point external turning operations on manual lathes, CNC lathes, screw machines and machining centers.
Tungsten Carbide Insert Turning Applications
Material | Components | Benefits |
---|---|---|
Carbon, alloy steels | Shafts, cylinders, bushings | High metal removal rates |
Stainless steels | Valve bodies, pump parts, fasteners | Corrosion resistance for medical, food, marine parts |
Heat resistant superalloys | Turbine disks, combustor liners, transitions | Withstand extreme environments |
Titanium, nickel alloys | Aircraft hydraulic/fuel tubes, IGT parts | Strength-to-weight ratio |
Cast iron | Automotive cylinders, gearbox casings | Dimensional accuracy |
Hardened steels | Cutting tools, molds, dies | Precision components |
Indexable insert tooling systems allow quick changeover between operations, minimizing downtime for producing high precision turned parts across industries.
Tungsten Carbide Insert Standards and Specifications
Standardization of insert dimensions, identification nomenclature, packaging, testing methods facilitates usage across global supply chain:
Tungsten Carbide Insert Standards
Standard | Organization | Role |
---|---|---|
ISO 1832 | International Organization for Standardization | Insert designation code with shape, size, tolerance, direction info |
ANSI B212.4-1986 | American National Standards Institute | Carbide insert standards guide |
JIS B4122 | Japanese Industrial Standards Committee | Carbide cutting tool specifications |
GB/T 20866 | Standardization Administration of China | Carbide insert specification |
Imposed by tooling manufacturers, suppliers also implement strict grades and quality control benchmarks:
Typical Carbide Insert Specifications
Parameter | Range / Benchmark |
---|---|
Density | >14.5 g/cc |
Hardness | 88-93 HRA (Rockwell A scale) |
Transverse rupture strength | >350 kgf/mm<sup>2</sup> |
Coating thickness | 3-5 μm |
Coating adhesion | HF1-2 per ISO 26443 |
These thresholds validate superior performance linked to precision dimensions, coating quality, microstructure uniformity and freedom from defects.
Global Suppliers of Tungsten Carbide Inserts
Prominent makers and distributors of tungsten carbide turning inserts include:
Tungsten Carbide Insert Brands
Company | Grades | Coatings |
---|---|---|
Sandvik Coromant | C, P, M, K | TiN, TiCN, TiAlN, AlCrN |
Kennametal | C, M, K, beyond | TiAlN, AlTiN, TiSiN |
WIDIA (Iscar) | C, P, M | TiN, AlTiN, TiSiN |
Walter Tools | Standard + custom grades | TiCN, AlCrN, TiAlCrN |
Sumitomo | Customized micrograin grades | Proprietary AC2000, AC3000 |
Kyocera Unimerco | Ultra-fine grained grades | Multilayer coatings |
Tungaloy | Customized ultra-hard grades | TiOCN, AlCrON |
Guhring | Ultra-wear resistant spec. carbide grades | TiAlN, TiCN, thick TiN+AlCrN |
Most manufacturers offer inserts in all common sizes and geometries tailored for various work materials, operations and tool holder systems.
Grade, coating and tolerances differentiate premium insert lines claiming longest tool life and most consistent machining performance albeit at higher price levels compared to value brands.
Comparative Analysis: Carbide Insert Types
Key differences between tungsten carbide insert options:
Parameter | Coated carbide insert | Ceramic insert | cBN insert | PCD insert |
---|---|---|---|---|
Composition | WC-Co carbide-metal matrix | Alumina or silicon nitride ceramics | Cubic boron nitride-ceramic mix | Diamond particles in metallic/ceramic binder |
Hardness | Very hard 88-93.1 HRA | Extremely hard up to 95 HRA | Close to diamond; over 45 GPa | Hardest; up to 80 GPa |
Fracture toughness | Much higher | More brittle | Brittle | Relatively brittle |
Thermal conductivity | Moderate | Low | High | High |
Friction coefficient | 0.15-0.35 typical | 0.20-0.80 | 0.05-0.50 | 0.05-0.25 |
Temperature limit | 600-1000°C | Around 1000°C | 1400°C | 700°C |
While more expensive inserts like PCD provide ultimate tool life and consistency in some alloys, limited cutting parameters make coated carbide the workhorse for production turning jobs across easier and harder metals.
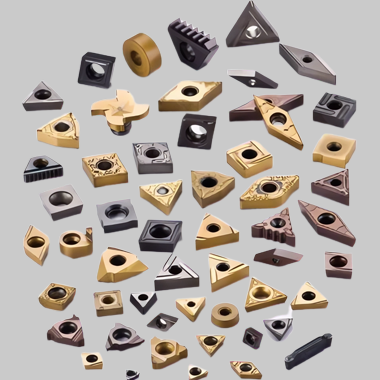
Advantages and Disadvantages of Tungsten Carbide Inserts
Pros and Cons of Carbide Inserts for Turning
Advantages | Disadvantages |
---|---|
Extremely hard and wear resistant | Brittle with lower fracture toughness than HSS tools |
Maintains hardness value at higher temperatures | Shock sensitive requiring rigid setups, smooth operation |
Chemically inert to most engineering materials | Expensive consumable, need for optimization |
Allows faster cutting parameters and lower cycle times | Proper selection and usage technique essential |
Indexable inserts provide multiple cutting edges | Special tooling, holders required |
Wide range of geometries, sizes and tolerance availability | Limitations on depth of cut versus solid carbide tools |
Applicable for most materials from plastics to hardened metals heat resistant superalloys | Regrinding or resharpening not feasible |
While demanding on setup rigidity, machine capability and level of operator skill, carbide inserts rightly dominate as material of choice for most production turning tasks favoring their supreme tool life and productivity benefits at moderate step-up in initial insert cost over HSS.
Frequently Asked Questions
Q1: Why are some tungsten carbide inserts black in appearance?
Answer: Dark appearance comes from TiAlN or similar wear-resistant PVD coating applied in thickness of 2-5 microns to provide lubricious protective layer that combats wear and welding during machining at higher temperatures.
Q2: When should a tungsten carbide insert be replaced?
Answer: Criteria for insert index or replacement includes dimensional tolerance drift exceeding specified limit due to flank wear, catastrophic chipping or fracture that leaves used cutting edges unserviceable, crater wear degrading work finish, or noticeable build up of material on rake face inhibiting chip flow and evacuation.
Q3: How to select the best tungsten carbide insert shape for production turning?
Answer: Square inserts offer four usable cutting edges and low per edge cost for roughing cuts while triangle or diamond inserts provide added strength for interrupted cuts. Round inserts excel in finishing grooves and profiles. Insert style can dictate suitable cutting tool holders.
Q4: What is the role of lead angle on tungsten carbide turning inserts?
Answer: Lead angle or plane rake tilts insert’s major cutting edge relative to base, varying contact area. Positive lead angles around +25° suit finishing as it lowers forces while negative lead angles approaching -25° benefit roughing by increasing strength.
Q5: Should tungsten carbide inserts be stored in any special manner?
Answer: Carbide inserts need proper enclosed storage in abrasion-resistant, labeled compartments to prevent contact or edge damage during handling. Controlled humidity environment prevents premature coating failure or spot corrosion.