Overview of Tungsten Carbide Inserts
Tungsten carbide inserts are essential tools used in various industries, from machining to manufacturing. These inserts play a crucial role in cutting, shaping, and drilling hard materials. The combination of tungsten and carbon creates a compound that is incredibly hard, durable, and resistant to wear, making it ideal for high-stress applications. But what makes tungsten carbide so unique? How do you choose the right manufacturer for your needs? And what are the key factors to consider when selecting tungsten carbide inserts?
This guide will dive deep into the world of tungsten carbide inserts, exploring everything from specific metal powder models to the characteristics, applications, and selection process. Whether you’re a seasoned professional or just beginning to explore this field, this comprehensive article will provide you with the knowledge you need.
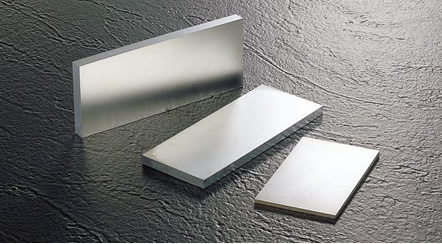
Understanding Tungsten Carbide Inserts
What Are Tungsten Carbide Inserts?
Tungsten carbide inserts are small cutting tools used in industrial machines. They’re designed to cut, shape, and mold various materials, including steel, iron, and even some ceramics. The magic lies in the material itself—tungsten carbide is a composite of tungsten and carbon atoms, combined to form a material that’s twice as stiff as steel and much denser.
How Are They Manufactured?
Manufacturing tungsten carbide inserts involves a process called powder metallurgy. Here’s a simplified breakdown:
- Powder Preparation: Tungsten and carbon powders are mixed together.
- Compacting: The mixture is pressed into a mold to form the desired shape.
- Sintering: The compacted powder is heated to just below its melting point, causing the particles to bond together.
- Finishing: The sintered product is ground to the exact dimensions required.
The result is a cutting tool that can withstand extreme temperatures, pressures, and wear.
Importance of Choosing the Right Manufacturer
Selecting the right manufacturer is crucial. Quality can vary significantly between manufacturers, and a poorly made insert can lead to tool breakage, poor finish quality, and higher costs. Factors such as the purity of the raw materials, precision in manufacturing, and the quality control processes in place all play a significant role in determining the final product’s performance.
Types of Tungsten Carbide Inserts
Tungsten carbide inserts come in various types, each designed for specific applications. Understanding the differences between these types can help you select the right one for your needs.
Indexable Inserts
Indexable inserts are the most common type. They’re designed to be replaced when worn, without the need to replace the entire tool. This makes them cost-effective and versatile.
Brazed Inserts
Brazed inserts are permanently attached to the tool. They offer a solid, stable performance but require replacement of the entire tool once the insert wears out.
Coated Inserts
These inserts have a coating (often titanium carbide or titanium nitride) to increase their hardness and wear resistance. The coating can significantly extend the insert’s life.
Uncoated Inserts
Uncoated inserts are pure tungsten carbide. They’re ideal for specific applications where coatings might not provide additional benefits.
Specialty Inserts
Some manufacturers offer specialty inserts designed for specific materials or applications, such as high-precision cutting or heavy-duty milling.
Applications of Tungsten Carbide Inserts
Tungsten carbide inserts are used in various industries due to their versatility and durability. Here’s a look at some of the common applications.
Machining and Cutting
In machining, tungsten carbide inserts are used for cutting and shaping metals. Their hardness allows them to cut through tough materials like steel and cast iron with ease.
Drilling
In the drilling industry, these inserts are used in drill bits to cut through rock and other hard materials. Their wear resistance ensures that they can withstand the extreme conditions found in drilling operations.
Milling
Tungsten carbide inserts are also used in milling operations, where they help shape materials with high precision. Their ability to maintain sharpness over time makes them ideal for these applications.
Mining
The mining industry uses tungsten carbide inserts in various tools to extract minerals and ores. The durability of these inserts ensures that they can handle the abrasive conditions found in mining environments.
Woodworking
Even in woodworking, tungsten carbide inserts are used in tools that cut and shape wood. Their ability to stay sharp longer than steel tools makes them a preferred choice.
Automotive Industry
In the automotive industry, tungsten carbide inserts are used to manufacture various parts, including engine components and body panels. Their ability to withstand high temperatures and pressures makes them ideal for these applications.
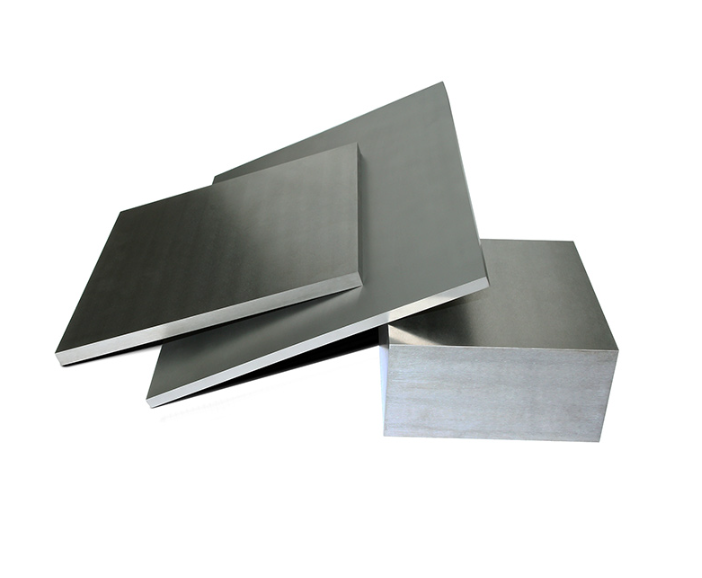
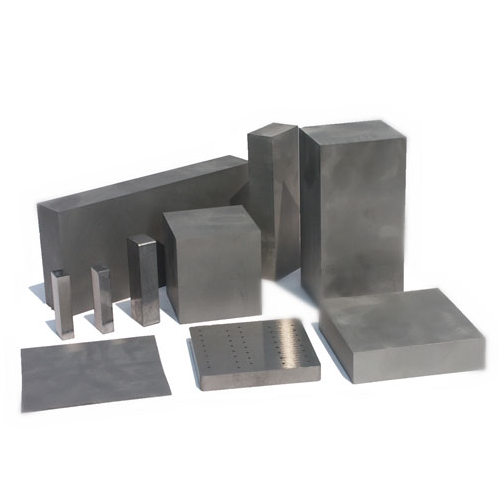
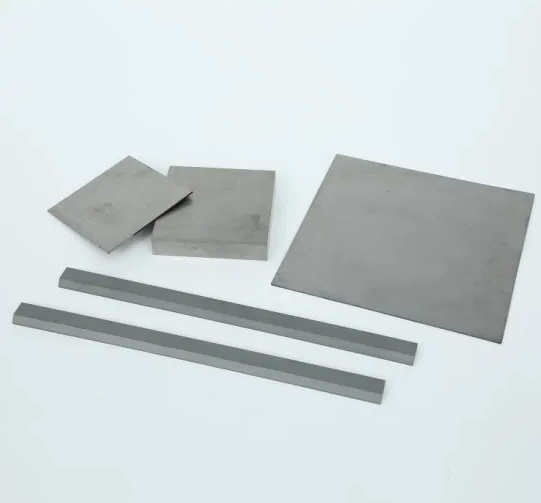
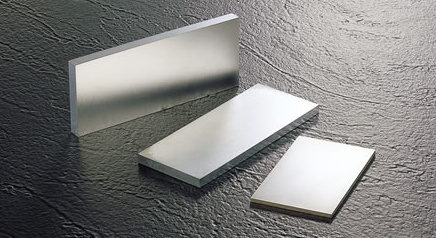
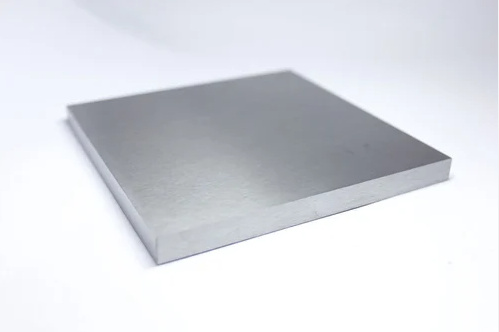
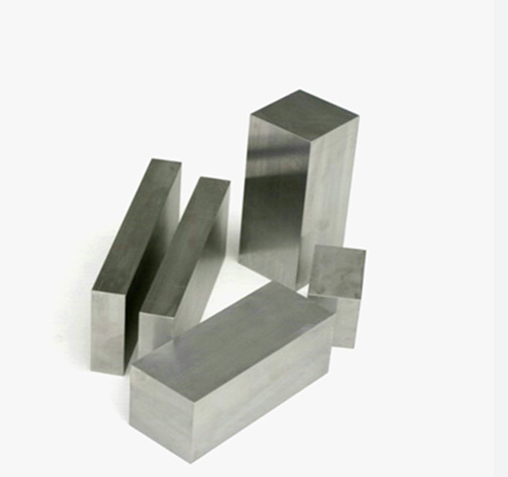
Material Properties of Tungsten Carbide Inserts
Understanding the material properties of tungsten carbide inserts is essential for selecting the right one for your application. Here’s a breakdown of the key properties.
Property | Description |
---|---|
Hardness | Tungsten carbide is extremely hard, measuring 8.5-9 on the Mohs scale. |
Density | With a density of around 15.7 g/cm³, tungsten carbide is denser than most metals. |
Toughness | The toughness of tungsten carbide allows it to withstand significant impact forces. |
Wear Resistance | Tungsten carbide is highly resistant to wear, making it ideal for high-stress applications. |
Thermal Stability | It retains its properties even at high temperatures, up to 1000°C. |
Corrosion Resistance | Tungsten carbide is resistant to corrosion, particularly from acidic environments. |
These properties make tungsten carbide inserts suitable for a wide range of applications, particularly those involving high stress, high temperatures, and abrasive conditions.
Specific Metal Powder Models Used in Tungsten Carbide Inserts
When it comes to tungsten carbide inserts, the type of metal powder used can significantly impact the final product’s performance. Here are some specific metal powder models commonly used:
Metal Powder Model | Description |
---|---|
WC-Co | Tungsten carbide-cobalt, the most common combination, offers a good balance of hardness and toughness. |
WC-Ni | Tungsten carbide-nickel, known for its corrosion resistance and toughness. |
WC-TiC | Tungsten carbide-titanium carbide, offers enhanced wear resistance. |
WC-TaC | Tungsten carbide-tantalum carbide, provides improved thermal stability. |
WC-TiN | Tungsten carbide-titanium nitride, increases hardness and reduces friction. |
WC-NbC | Tungsten carbide-niobium carbide, known for its high-temperature strength. |
WC-Mo | Tungsten carbide-molybdenum, used for applications requiring high toughness. |
WC-Cr | Tungsten carbide-chromium, enhances corrosion resistance and wear properties. |
WC-V | Tungsten carbide-vanadium, improves wear resistance and toughness. |
WC-ZrC | Tungsten carbide-zirconium carbide, provides a balance of hardness and toughness. |
Each of these metal powder models offers specific benefits, making them suitable for different applications. For example, WC-Co is widely used in general machining, while WC-Ni might be preferred in environments where corrosion resistance is critical.
Specifications, Sizes, and Shapes of Tungsten Carbide Inserts
Tungsten carbide inserts come in various sizes and shapes to meet different application needs. Here’s a detailed look at the specifications.
Specification | Description |
---|---|
Sizes | Inserts are available in a range of sizes, typically from 1/8 inch to 1 inch in diameter. |
Shapes | Common shapes include round, square, triangular, and diamond. Each shape offers different benefits in terms of cutting angles and edge retention. |
Standards | Inserts are manufactured to various international standards, including ISO, ANSI, and JIS. |
Edge Types | Inserts can have different edge types, including sharp, rounded, or chamfered edges, depending on the application. |
Coatings | Some inserts are coated to enhance wear resistance, with coatings such as titanium nitride (TiN) or titanium carbide (TiC). |
These specifications allow manufacturers to produce inserts that meet the specific needs of different industries and applications.
Material Composition and Characteristics of Tungsten Carbide Inserts
The composition of tungsten carbide inserts is a key factor in their performance. Here’s a look at the typical composition and characteristics.
Material Composition | Characteristics |
---|---|
Tungsten (W) | Provides the base material, known for its hardness and density. |
Carbon (C) | Combined with tungsten to form tungsten carbide, increasing hardness and wear resistance. |
Cobalt (Co) | Often used as a binder, enhancing toughness and impact resistance. |
Nickel (Ni) | An alternative binder, offers better corrosion resistance. |
Titanium (Ti) | Added to improve wear resistance and reduce friction. |
Tantalum (Ta) | Enhances thermal stability and toughness. |
Vanadium (V) | Improves wear resistance and overall durability. |
Chromium (Cr) | Increases corrosion resistance and enhances overall performance. |
These components are carefully selected and combined to create tungsten carbide inserts that offer a balance of hardness, toughness, and wear resistance.
Comparing Advantages and Limitations of Tungsten Carbide Inserts
When choosing tungsten carbide inserts, it’s essential to weigh their advantages against their limitations.
Advantages | Limitations |
---|---|
High Hardness | Tungsten carbide is harder than most metals, allowing it to cut through tough materials. |
Wear Resistance | The material is highly resistant to wear, extending the life of the insert. |
Thermal Stability | Maintains its properties even at high temperatures, making it ideal for high-heat applications. |
Versatility | Suitable for a wide range of applications, from machining to drilling and milling. |
High Cost | Tungsten carbide inserts are generally more expensive than other types of cutting tools. |
Brittleness | Despite their toughness, tungsten carbide inserts can be brittle and may fracture under high impact. |
Special Handling | Requires careful handling and maintenance to avoid chipping or breakage. |
Limited Flexibility | Not suitable for all applications, particularly those requiring high flexibility. |
By understanding these advantages and limitations, you can make a more informed decision when selecting tungsten carbide inserts for your specific application.
Selecting the Right Tungsten Carbide Inserts
Choosing the right tungsten carbide inserts involves considering various factors. Here’s a guide to help you make the right choice.
Application Requirements
- Material Being Machined: Consider the material you’ll be cutting. Harder materials may require inserts with specific coatings or compositions.
- Cutting Speed: Different inserts are designed for different cutting speeds. High-speed operations may require more durable inserts.
- Tool Life: Consider how long you need the insert to last. Coated inserts often offer longer life but at a higher cost.
Insert Specifications
- Size and Shape: Ensure the insert fits your tool and is appropriate for the type of cutting you’ll be doing.
- Edge Type: The edge type can impact the quality of the cut. Sharp edges are ideal for fine finishes, while rounded edges are better for rough cuts.
- Coating: Coatings can significantly impact the insert’s performance. Choose a coating that matches your application needs.
Manufacturer Reputation
- Quality Control: Look for manufacturers with strict quality control processes to ensure consistent performance.
- Customer Reviews: Customer reviews can provide insight into the reliability and performance of the manufacturer’s products.
- Support and Service: Consider the level of support and service offered by the manufacturer, including availability of technical assistance and replacement parts.
Suppliers and Pricing Details of Tungsten Carbide Inserts
When it comes to purchasing tungsten carbide inserts, the choice of supplier can impact both the quality and cost. Here’s a look at some reputable suppliers and their pricing details.
Supplier | Product Range | Pricing (Approximate) | Special Features |
---|---|---|---|
Kennametal | Wide range of indexable and brazed inserts. | $10 – $50 per insert | High-quality materials, advanced coatings. |
Sandvik Coromant | Extensive selection of coated and uncoated inserts. | $15 – $60 per insert | Innovative designs, global availability. |
Seco Tools | Various shapes and sizes, specialty inserts. | $20 – $55 per insert | Excellent customer support, custom solutions. |
Iscar | High-performance inserts for various applications. | $25 – $70 per insert | Advanced technology, long tool life. |
Sumitomo | Specialty inserts for specific industries. | $30 – $65 per insert | High precision, Japanese craftsmanship. |
These suppliers are known for their quality products, and while prices may vary, they generally offer good value for the performance you receive.
How to Choose Tungsten Carbide Inserts Manufacturers
Selecting the right manufacturer for tungsten carbide inserts can be a daunting task. Here’s a guide to help you navigate this process.
Reputation and Reliability
Start by researching the manufacturer’s reputation. Look for customer reviews, industry awards, and any certifications that indicate a commitment to quality.
Product Range and Specialization
Consider whether the manufacturer specializes in the type of tungsten carbide inserts you need. A manufacturer with a broad product range may offer more options, but one that specializes in your specific area may provide better performance.
Quality Control Processes
Quality control is crucial in the manufacturing of tungsten carbide inserts. Look for manufacturers that have strict quality control measures in place, such as ISO certification.
Customer Support and Service
Consider the level of customer support and service offered by the manufacturer. This includes technical assistance, availability of replacement parts, and the ability to provide custom solutions.
Pricing and Value
While cost is an important factor, it’s essential to consider the value you’re getting for your money. Cheaper inserts may save you money upfront but could lead to higher costs in the long run due to lower performance or shorter lifespan.
Function of Tungsten Carbide Inserts
Tungsten carbide inserts serve several key functions in industrial applications. Here’s a closer look at their primary roles.
Cutting
The primary function of tungsten carbide inserts is cutting. Whether it’s metal, wood, or other materials, these inserts are designed to cut with precision and efficiency.
Shaping
Tungsten carbide inserts are also used for shaping materials. In milling operations, for example, they help create specific shapes and contours with high precision.
Drilling
In drilling operations, tungsten carbide inserts are used to create holes in tough materials. Their hardness and wear resistance make them ideal for this task.
Finishing
Finally, tungsten carbide inserts are often used in finishing operations. They can create smooth surfaces and fine finishes, making them essential in industries like automotive and aerospace.
Selecting the Right Tungsten Carbide Inserts for Your Needs
Choosing the right tungsten carbide inserts is a critical decision that can impact your productivity, costs, and overall success. Here’s a step-by-step guide to help you make the right choice.
Step 1: Identify Your Application Needs
Start by identifying the specific needs of your application. What materials will you be cutting? What kind of finish do you require? What are the operating conditions?
Step 2: Consider the Material Properties
Consider the material properties of the inserts. Do you need high hardness for cutting tough materials? Or perhaps you need high toughness for impact-resistant applications?
Step 3: Evaluate the Manufacturer’s Offerings
Look at what different manufacturers offer. Do they have the specific type of insert you need? Do they offer custom solutions if necessary?
Step 4: Compare Prices and Value
Compare the prices of different inserts, but also consider the value. A higher-priced insert might offer better performance and longer life, leading to lower costs over time.
Step 5: Test and Validate
If possible, test the inserts in your specific application before making a large purchase. This will help you validate your choice and ensure it meets your needs.
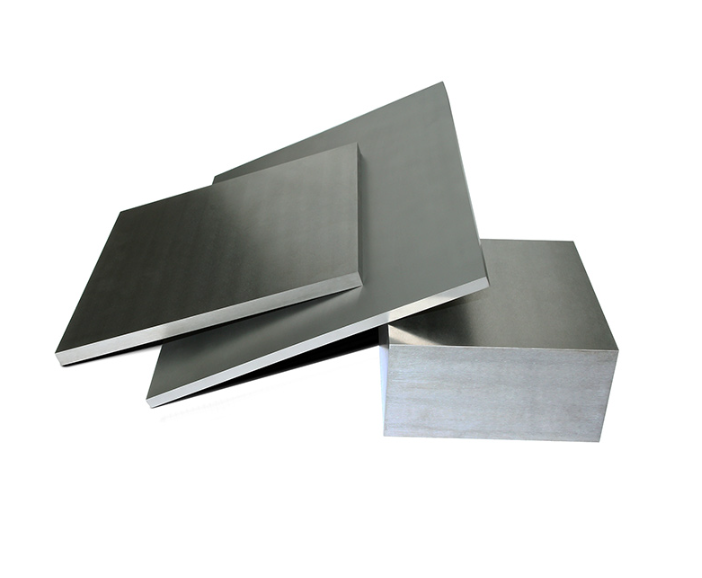
FAQ
Here’s a frequently asked questions section to address common queries about tungsten carbide inserts.
Question | Answer |
---|---|
What are tungsten carbide inserts used for? | Tungsten carbide inserts are used for cutting, shaping, drilling, and finishing materials in various industries. |
How do I choose the right tungsten carbide insert? | Consider your application needs, material properties, and manufacturer reputation when selecting an insert. |
Are coated inserts better than uncoated ones? | Coated inserts often offer longer life and better performance, especially in high-stress applications. |
What is the typical lifespan of a tungsten carbide insert? | The lifespan varies depending on the application, but they generally last longer than steel inserts. |
How do I maintain my tungsten carbide inserts? | Keep them clean, avoid dropping or mishandling them, and store them in a dry, safe place. |
Conclusion
Tungsten carbide inserts are an essential tool in many industries, offering unparalleled hardness, wear resistance, and versatility. Whether you’re cutting metal, drilling through rock, or shaping wood, these inserts can provide the performance you need. By understanding the different types of inserts, their applications, and how to select the right manufacturer, you can ensure you’re making the best choice for your specific needs. Remember, the right tungsten carbide insert can make all the difference in your operation’s efficiency and success. So take the time to choose wisely, and invest in quality tools that will serve you well for years to come.