Tungsten carbide inserts have become a cornerstone of modern metalworking, revered for their exceptional hardness, durability, and ability to deliver clean, precise cuts. But what exactly are these inserts, and how do they revolutionize machining processes? Delve into this guide to unlock the secrets of tungsten carbide inserts and discover how they can elevate your metalworking projects.
Composition and Properties of Tungsten Carbide Inserts
At the heart of a tungsten carbide insert lies a formidable material: tungsten carbide (WC). This ceramic compound boasts an impressive 80% tungsten carbide content, bonded together by a metallic binder, typically cobalt (Co). This synergistic union grants the insert its remarkable properties:
- Exceptional Hardness: Tungsten carbide ranks second in hardness only to diamond, making it ideal for tackling challenging materials like steel, cast iron, and nickel alloys. Imagine a butter knife effortlessly slicing through a brick – that’s the kind of cutting prowess tungsten carbide inserts possess.
- Outstanding Wear Resistance: Unlike traditional high-speed steel (HSS) tools that quickly dull, tungsten carbide inserts retain their sharpness for extended periods. This translates to fewer tool changes, reduced downtime, and significant cost savings in the long run. Think of it as the difference between a disposable razor and a high-quality, self-sharpening one.
- High-Temperature Tolerance: Machining often generates significant heat. Tungsten carbide inserts excel in these fiery conditions, maintaining their structural integrity and cutting performance even at elevated temperatures. Imagine a firefighter fearlessly charging into an inferno – that’s the tungsten carbide insert’s resilience against heat.
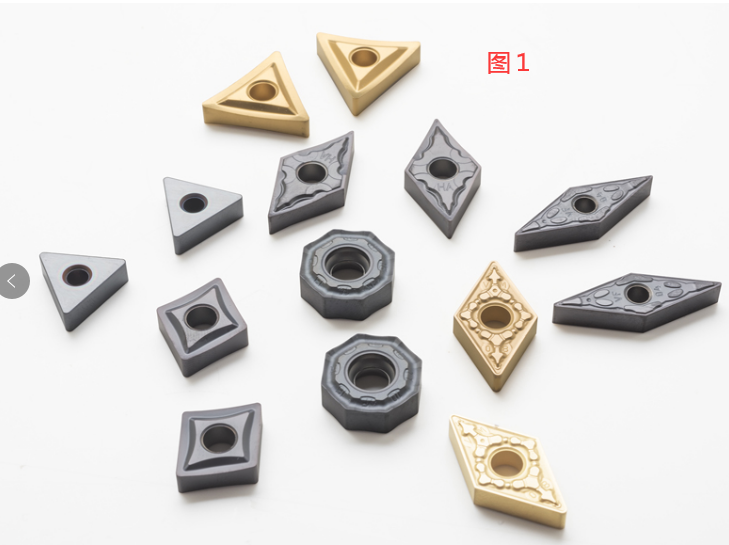
The Role of the Binder: The cobalt binder plays a crucial role in holding the tungsten carbide particles together and ensuring the insert’s overall toughness. However, the exact cobalt content influences the insert’s characteristics. Higher cobalt percentages enhance toughness but may reduce wear resistance. Conversely, lower cobalt content yields harder inserts but with slightly less toughness. This delicate balance is what engineers meticulously calibrate to create tungsten carbide inserts suited for specific applications.
Application Fields of Tungsten Carbide Inserts
The versatility of tungsten carbide inserts extends across a broad spectrum of metalworking applications:
- Turning: Imagine shaping a piece of metal on a lathe. Here, tungsten carbide inserts mounted on turning tools excel at creating precise external and internal diameters, grooves, and other intricate features. Their ability to handle high cutting speeds translates to faster production times.
- Milling: Milling involves shaping metal using a multi-tooth rotary cutter. Tungsten carbide inserts equip milling tools to tackle various tasks, including face milling, end milling, and slotting. Their superior wear resistance allows for deeper cuts and longer tool life.
- Drilling: Drilling precise holes in metal is another forte of tungsten carbide inserts. They empower drill bits to penetrate tough materials with exceptional efficiency and leave clean, burr-free holes. Compared to HSS drill bits, they require less frequent sharpening, minimizing downtime.
- Thread Cutting: Creating accurate threads on metal components is a breeze with tungsten carbide inserts. Their sharp edges ensure clean thread profiles, reducing the risk of imperfections or defects.
These are just a few examples – tungsten carbide inserts are instrumental in countless other metalworking operations, from grooving and facing to boring and reaming. Their ability to handle a wide range of materials, from soft aluminum to hard stainless steel, further expands their utility.
Advantages of Tungsten Carbide Inserts
When compared to traditional HSS tools, tungsten carbide inserts offer a compelling array of benefits:
- Superior Cutting Speeds and Feed Rates: Tungsten carbide inserts can handle significantly higher cutting speeds and feed rates than HSS tools. This translates to faster machining times, increased productivity, and lower production costs. Imagine the difference between riding a bicycle and a high-speed train – that’s the leap in efficiency tungsten carbide inserts enable.
- Exceptional Surface Finish: The inherent hardness of tungsten carbide inserts allows them to produce superior surface finishes on machined parts. This reduces or eliminates the need for additional finishing processes, saving time and resources. Think of the difference between a hand-sanded and a machine-polished surface – that’s the level of smoothness tungsten carbide inserts can achieve.
- Reduced Downtime: As mentioned earlier, tungsten carbide inserts boast exceptional wear resistance, translating to fewer tool changes and less downtime. This keeps your machinery productive and minimizes disruptions in your workflow. Imagine a marathon runner who barely needs to stop for water breaks – that’s the endurance tungsten carbide inserts provide.
- Cost-Effectiveness: While the initial cost of tungsten carbide inserts might be higher than HSS tools, their extended lifespan and reduced downtime make them a cost-effective choice in the long run.
- Broader Material Compatibility: Tungsten carbide inserts excel at machining a wider range of materials compared to HSS tools. They can handle not only various steels but also cast iron, nickel alloys, and even some harder materials. This versatility makes them a valuable asset in any metalworking shop. Imagine a chef’s knife that can effortlessly slice through meat, vegetables, and even cheese – that’s the versatility of tungsten carbide inserts.
Beyond Efficiency: Additional Benefits
In addition to the core performance advantages, tungsten carbide inserts offer some lesser-known but equally valuable benefits:
- Improved Machine Tool Life: By minimizing vibration and heat generation during machining, tungsten carbide inserts contribute to the longevity of your machine tools. This translates to lower maintenance costs and less frequent equipment replacement. Think of them as protective gear for your machinery, extending its lifespan and performance.
- Enhanced Operator Safety: Reduced tool changes and breaks due to superior wear resistance lead to a safer work environment for operators. Less handling of potentially hot or damaged tools translates to fewer opportunities for accidents. Imagine a self-driving car that minimizes the risk of driver error – that’s the safety benefit of fewer tool changes with tungsten carbide inserts.
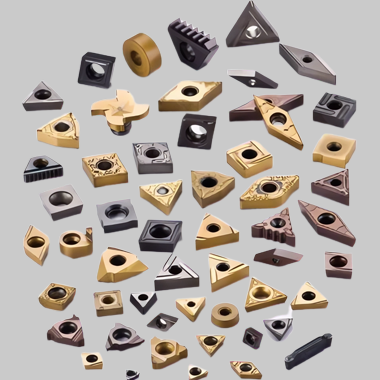
Disadvantages of Tungsten Carbide Inserts
While tungsten carbide inserts reign supreme in many aspects, it’s essential to acknowledge their limitations:
- Higher Initial Cost: As mentioned earlier, the upfront cost of tungsten carbide inserts can be higher than HSS tools. However, their extended lifespan and other benefits can offset this initial investment over time. Consider them an investment in long-term productivity and efficiency.
- Brittleness: While incredibly hard, tungsten carbide inserts can be brittle under certain conditions. Sharp impacts or excessive force can cause them to chip or fracture. Imagine a diamond – incredibly hard but susceptible to breaking if struck the wrong way. Proper handling and tool selection are crucial to avoid this drawback.
- Application-Specific Selection: The vast array of tungsten carbide insert grades and geometries necessitates careful selection based on the specific material being machined and the desired outcome. Choosing the wrong insert can lead to subpar performance or even tool failure. Consulting with a knowledgeable supplier or machinist is vital to ensure optimal selection.
Choosing the Right Tungsten Carbide Insert
Given the diverse range of know more Tungsten carbide available, selecting the right one for your project requires careful consideration of several factors:
- Material to be Machined: Different insert grades are optimized for specific materials. For example, inserts designed for steel might not perform well on cast iron. Understanding the properties of the material you’ll be working with is paramount.
- Machining Operation: Turning, milling, drilling, and threading each require different insert geometries. The cutting edge profile, rake angle, and clearance angle all influence chip formation and cutting performance.
- Cutting Parameters: Factors like cutting speed, feed rate, and depth of cut will influence the insert selection. Consulting the insert manufacturer’s recommendations is crucial to ensure optimal performance and tool life.
Advanced Considerations
For more demanding applications, additional factors come into play:
- Coating: Certain tungsten carbide inserts are coated with materials like titanium nitride (TiN) or aluminum titanium nitride (AlTiN). These coatings can further enhance wear resistance, improve chip evacuation, and reduce heat generation. Imagine a non-stick pan that makes cooking and cleaning easier – that’s the advantage coatings offer.
- Chip Breakers: The shape of the insert’s cutting edge can significantly impact chip formation. Inserts with integrated chip breakers help control chip size and prevent them from re-welding to the workpiece or insert, improving surface finish and tool life.
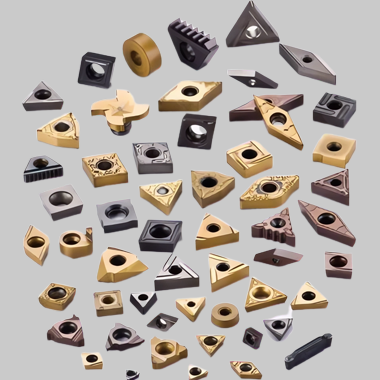
FAQ
Q: How long do tungsten carbide inserts last compared to HSS tools?
A: Tungsten carbide inserts can last several times longer than HSS tools between sharpening or replacement. The exact lifespan depends on various factors like the material being machined, cutting parameters, and insert grade.
Q: Are tungsten carbide inserts safe to use?
A: When used properly, tungsten carbide inserts are safe. However, always wear appropriate safety gear like eye protection and gloves when working with any cutting tools. Additionally, avoid using damaged or chipped inserts, as these can pose a safety hazard.
Q: Can I use tungsten carbide inserts for woodworking?
A: While some specialty tungsten carbide inserts are designed for woodturning applications, they are not typically used for general woodworking. For most woodworking tasks, high-quality HSS or carbide-tipped router bits and saw blades are better suited.
Q: Where can I buy tungsten carbide inserts?
A: Tungsten carbide inserts can be purchased from a variety of industrial tool suppliers, both online and in physical stores.
Conclusion
Tungsten carbide inserts have revolutionized metalworking, offering unparalleled cutting performance, exceptional wear resistance, and the ability to tackle a wide range of materials. Their advantages translate into faster production times, improved surface finishes, reduced downtime, and ultimately, increased profitability. While some limitations exist, careful selection and proper handling mitigate these drawbacks.
By partnering with a reputable supplier who can guide you through the selection process and offer additional support, you can unlock the full potential of tungsten carbide inserts and elevate your metalworking projects to new heights. So, the next time you embark on a metalworking endeavor, consider these remarkable inserts – they might just become your most trusted ally in the workshop.