Tungsten carbide hardfacing rods are essential in many industries due to their remarkable hardness, wear resistance, and strength. Whether you are looking to extend the lifespan of your tools or enhance the durability of surfaces exposed to extreme conditions, understanding tungsten carbide hardfacing rods can be incredibly beneficial.
In this comprehensive guide, we’ll dive into everything you need to know about tungsten carbide hardfacing rods, from types and applications to material properties and selection tips. Let’s get started!
Overview of Tungsten Carbide Hardfacing Rods
Tungsten carbide hardfacing rods are engineered to provide exceptional wear resistance and durability. They are widely used in industries like mining, construction, agriculture, and manufacturing to protect and repair metal surfaces subjected to high abrasion and impact.
These rods are typically applied through welding, creating a hard, wear-resistant surface that significantly extends the life of the base material. They are composed primarily of tungsten carbide particles embedded in a metal matrix, usually cobalt, nickel, or a combination of metals.
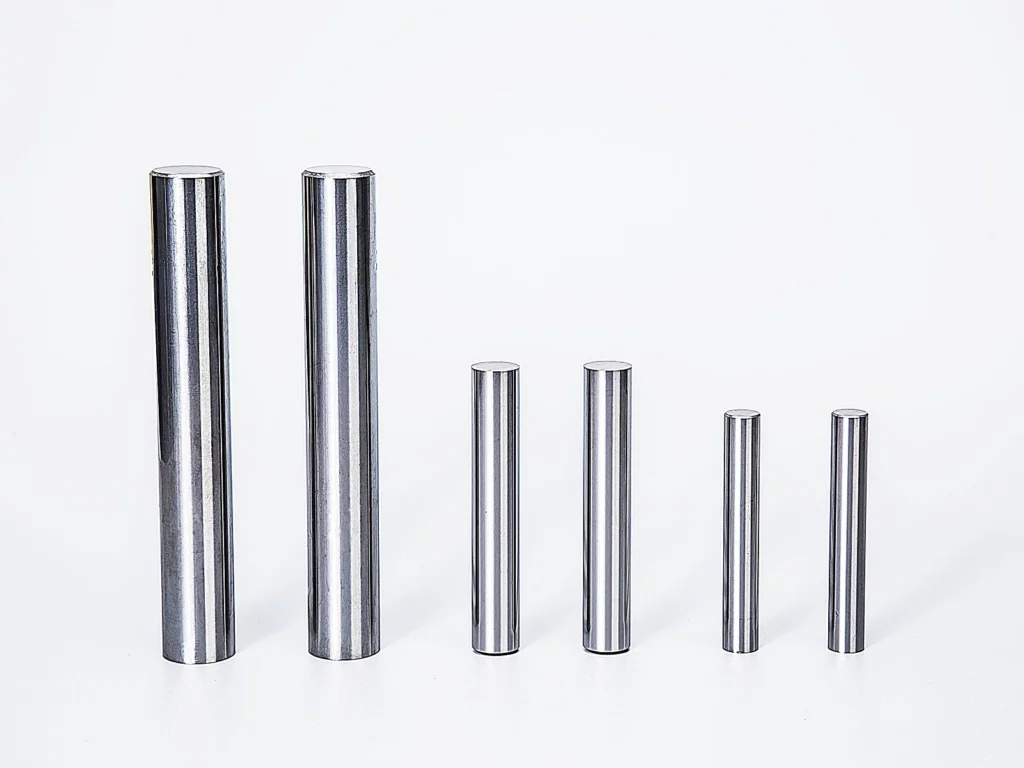
Types of Tungsten Carbide Hardfacing Rods
To help you understand the variety of tungsten carbide hardfacing rods available, here’s a detailed table with specific models and their descriptions:
Type | Model | Description |
---|---|---|
Standard Tungsten Carbide Rods | WC-Co 6% | A popular choice for general-purpose applications, offering a good balance of hardness and toughness. |
Microstructure Enhanced Rods | WC-Ni 10% | Enhanced with nickel for improved corrosion resistance and toughness. |
High Hardness Rods | WC-Co 12% | Contains a higher percentage of tungsten carbide for maximum hardness. |
Impact Resistant Rods | WC-Co/Ni 8% | A blend designed for applications involving high impact and abrasion. |
Corrosion Resistant Rods | WC-Ni/Cr 15% | Enhanced with chromium and nickel for superior corrosion resistance. |
Wear Resistant Rods | WC-Co 14% | Optimized for applications requiring exceptional wear resistance. |
Composite Rods | WC-Co/Ni/Cr 10% | A composite blend offering a balance of wear resistance, toughness, and corrosion resistance. |
High-Temperature Rods | WC-Co 20% | Designed for high-temperature applications with excellent thermal stability. |
Ultra-Fine Grain Rods | WC-Co 8% Fine | Contains ultra-fine tungsten carbide particles for superior surface finish and wear resistance. |
Custom Alloy Rods | WC-Custom Alloy | Tailored compositions to meet specific application requirements. |
Applications of Tungsten Carbide Hardfacing Rods
Tungsten carbide hardfacing rods are used in a variety of applications to protect and enhance the performance of metal surfaces. Here’s a detailed table of their applications:
Application | Description |
---|---|
Mining Equipment | Used to hardface drill bits, crushers, and wear plates to extend their service life in abrasive conditions. |
Construction Tools | Applied to bulldozer blades, excavator buckets, and grader blades for increased durability. |
Agricultural Machinery | Enhances the wear resistance of plowshares, cultivator points, and harvester components. |
Manufacturing Equipment | Protects molds, dies, and cutting tools from wear and tear. |
Oil and Gas Industry | Hardfaces components like valve seats, drill pipes, and pump parts to resist corrosion and abrasion. |
Power Generation | Used in turbines and boiler tubes to withstand high temperatures and abrasive environments. |
Steel and Cement Industries | Hardfaces hammers, chutes, and conveyor screws to prolong their lifespan. |
Automotive Industry | Applied to engine components, transmission parts, and gears for enhanced performance and longevity. |
Aerospace Industry | Protects landing gear, engine parts, and other critical components from wear and corrosion. |
Marine Industry | Used in propellers, shafts, and other components exposed to seawater for corrosion resistance. |
Material Properties of Tungsten Carbide Hardfacing Rods
Understanding the material properties of tungsten carbide hardfacing rods is crucial for selecting the right product for your needs. Here’s a table outlining key properties:
Property | Description |
---|---|
Hardness | Typically ranges from 1600 to 2200 HV (Vickers Hardness), providing excellent resistance to wear and abrasion. |
Toughness | Varies depending on the metal matrix (cobalt, nickel, etc.), with higher toughness materials being more impact resistant. |
Corrosion Resistance | Enhanced with the addition of elements like nickel and chromium, making some rods suitable for harsh environments. |
Thermal Stability | Can withstand high temperatures, making them ideal for applications involving intense heat. |
Density | Generally ranges from 14.0 to 15.5 g/cm³, providing a robust and durable solution for heavy-duty applications. |
Fracture Toughness | Critical for applications involving high impact or stress, with higher values indicating better resistance to cracking. |
Wear Resistance | Exceptional due to the high hardness of tungsten carbide particles, significantly extending the lifespan of the base material. |
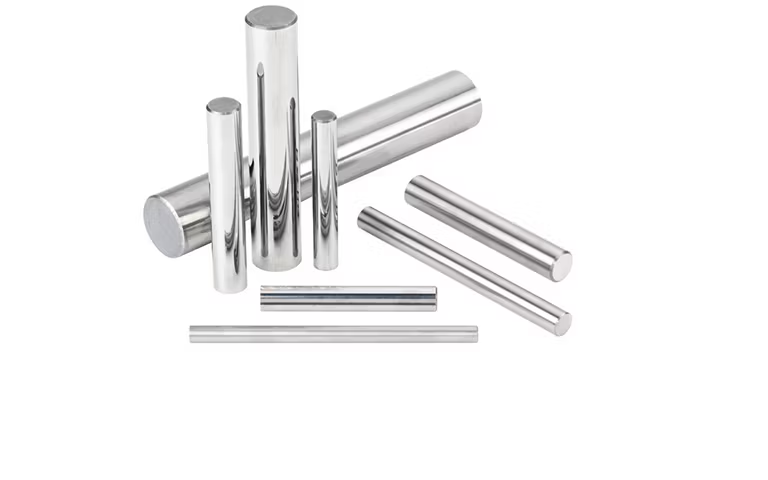
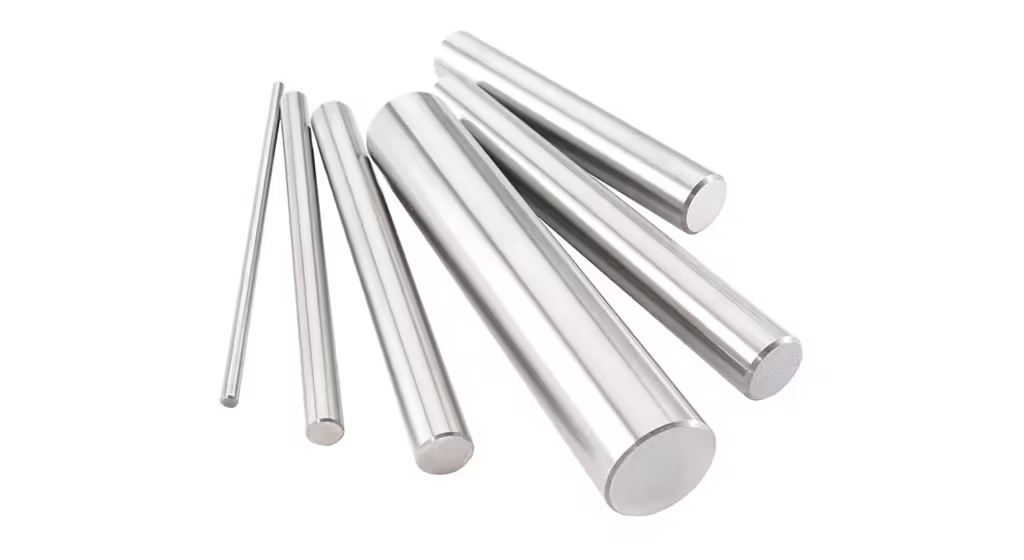
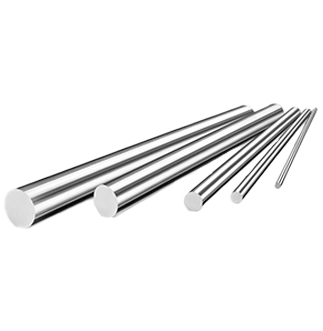
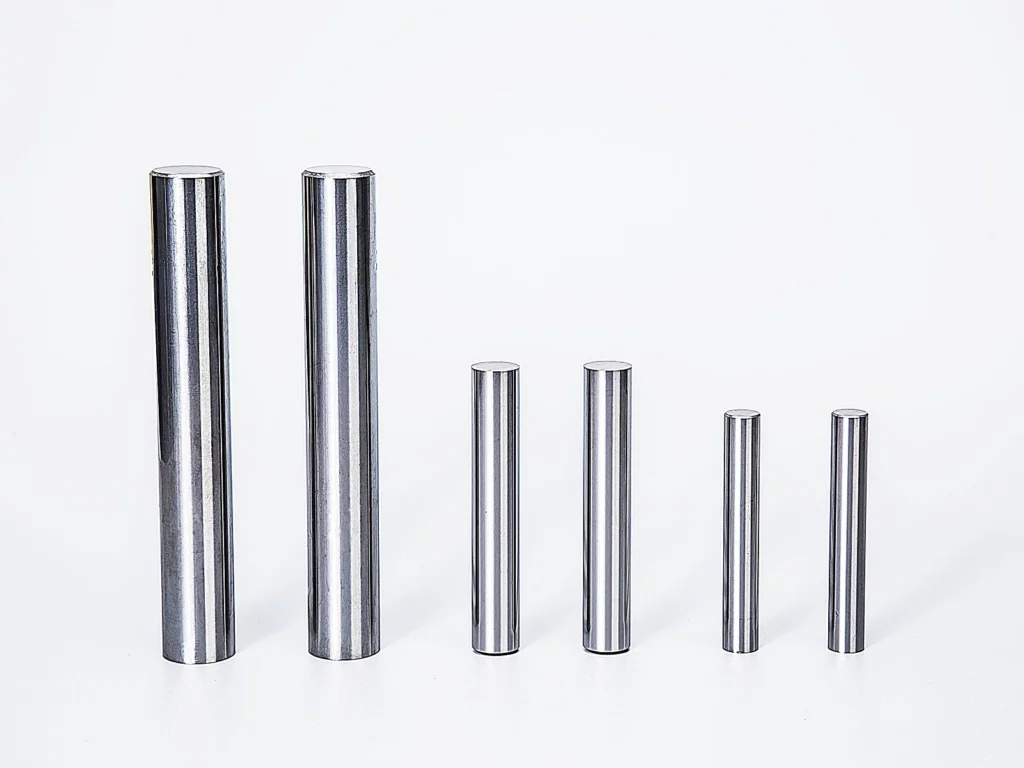
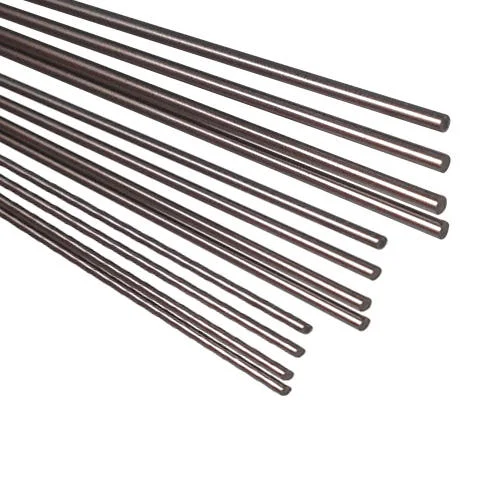
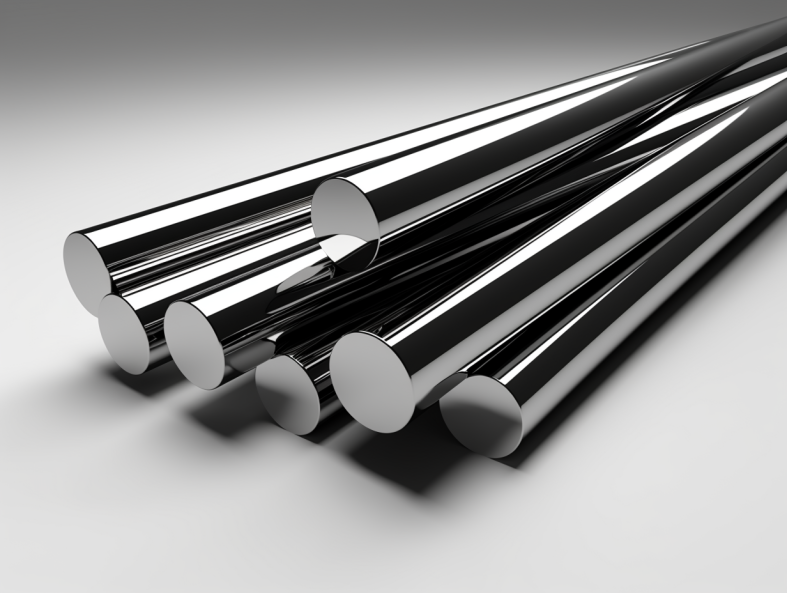
Composition, Properties, and Characteristics
Here’s a detailed table summarizing the composition, properties, and characteristics of various tungsten carbide hardfacing rods:
Type | Composition | Hardness (HV) | Toughness | Corrosion Resistance | Key Characteristics |
---|---|---|---|---|---|
WC-Co 6% | 94% WC, 6% Co | 1600 | High | Moderate | Good balance of hardness and toughness. |
WC-Ni 10% | 90% WC, 10% Ni | 1500 | Very High | High | Excellent corrosion resistance. |
WC-Co 12% | 88% WC, 12% Co | 1800 | Moderate | Moderate | Maximum hardness for extreme wear resistance. |
WC-Co/Ni 8% | 92% WC, 8% Co/Ni | 1700 | High | Moderate | Balanced for impact and abrasion. |
WC-Ni/Cr 15% | 85% WC, 10% Ni, 5% Cr | 1400 | High | Very High | Superior corrosion resistance. |
WC-Co 14% | 86% WC, 14% Co | 1900 | Moderate | Moderate | Optimized for wear resistance. |
WC-Co/Ni/Cr 10% | 90% WC, 5% Co, 3% Ni, 2% Cr | 1600 | High | High | Balanced properties for varied applications. |
WC-Co 20% | 80% WC, 20% Co | 2000 | Low | Moderate | Excellent for high-temperature applications. |
WC-Co 8% Fine | 92% WC, 8% Co (ultra-fine) | 1750 | High | Moderate | Superior surface finish and wear resistance. |
WC-Custom Alloy | Varies according to requirements | Varies | Varies | Varies | Tailored to specific application needs. |
Hardness, Strength, and Wear Resistance
Tungsten carbide hardfacing rods are renowned for their superior hardness, strength, and wear resistance. Here’s a comparison table to highlight these attributes:
Model | Hardness (HV) | Strength | Wear Resistance |
---|---|---|---|
WC-Co 6% | 1600 | High | Excellent |
WC-Ni 10% | 1500 | Very High | Very Good |
WC-Co 12% | 1800 | Moderate | Outstanding |
WC-Co/Ni 8% | 1700 | High | Excellent |
WC-Ni/Cr 15% | 1400 | High | Very Good |
WC-Co 14% | 1900 | Moderate | Exceptional |
WC-Co/Ni/Cr 10% | 1600 | High | Excellent |
WC-Co 20% | 2000 | Low | Outstanding |
WC-Co 8% Fine | 1750 | High | Very Good |
WC-Custom Alloy | Varies | Varies | Varies |
Specifications, Sizes, Shapes, and Standards
When selecting tungsten carbide hardfacing rods, it is crucial to consider the specifications, sizes, shapes, and standards. Here’s a detailed table:
Specification | Details |
---|---|
Sizes | Typically available in diameters ranging from 1/8″ to 1/2″ and lengths of 12″ to 36″. |
Shapes | Round rods, flat bars, and custom shapes. |
Standards | Meets AWS A5.21, ISO 9001, and other relevant industry standards. |
Packaging | Available in various packaging options including boxes, tubes, and custom packaging. |
Suppliers and Pricing Details
Choosing the right supplier can impact the quality and cost of tungsten carbide hardfacing rods. Here’s a table of suppliers and their pricing details:
Supplier | Location | Product Range | Pricing (Approx.) |
---|---|---|---|
Hardfacing Solutions Inc. | USA | Full range of tungsten carbide rods | $100 – $500 per kg |
Global Tungsten & Powders | Germany | High-quality rods and custom alloys | $120 – $550 per kg |
Durum Verschleißschutz GmbH | Germany | Standard and specialized hardfacing rods | $110 – $530 per kg |
Kennametal | USA | Comprehensive range of hardfacing products | $130 – $600 per kg |
Weartech International | USA | Custom and standard hardfacing rods | $115 – $520 per kg |
Castolin Eutectic | Switzerland | Innovative hardfacing solutions | $125 – $580 per kg |
Polymet Corporation | USA | High-performance hardfacing rods | $105 – $490 per kg |
Selecting the Right Tungsten Carbide Hardfacing Rod
Selecting the appropriate tungsten carbide hardfacing rod depends on several factors, including application requirements, material properties, and environmental conditions. Here’s a table to guide your selection process:
Criteria | Considerations | Recommended Type |
---|---|---|
Abrasion Resistance | High hardness and wear resistance | WC-Co 12%, WC-Co 14% |
Impact Resistance | Good balance of toughness and hardness | WC-Co/Ni 8%, WC-Co/Ni/Cr 10% |
Corrosion Resistance | Enhanced resistance to corrosive environments | WC-Ni 10%, WC-Ni/Cr 15% |
High-Temperature Stability | Ability to withstand high operating temperatures | WC-Co 20% |
Surface Finish | Fine particle distribution for superior surface finish | WC-Co 8% Fine |
Custom Requirements | Tailored compositions to meet specific needs | WC-Custom Alloy |
Comparing Advantages and Limitations
Here’s a comparison table to help you understand the advantages and limitations of different tungsten carbide hardfacing rods:
Model | Advantages | Limitations |
---|---|---|
WC-Co 6% | Good balance of properties, versatile | Moderate corrosion resistance |
WC-Ni 10% | Excellent corrosion resistance, high toughness | Lower hardness compared to other types |
WC-Co 12% | Maximum hardness, outstanding wear resistance | Lower impact resistance |
WC-Co/Ni 8% | High impact and abrasion resistance | Moderate corrosion resistance |
WC-Ni/Cr 15% | Superior corrosion resistance, high toughness | Lower hardness |
WC-Co 14% | Exceptional wear resistance | Lower impact resistance |
WC-Co/Ni/Cr 10% | Balanced properties for varied applications | Moderate performance in extreme conditions |
WC-Co 20% | Excellent high-temperature stability | Lower toughness |
WC-Co 8% Fine | Superior surface finish and wear resistance | Higher cost |
WC-Custom Alloy | Tailored to specific needs, optimal performance | May require longer lead times and higher cost |
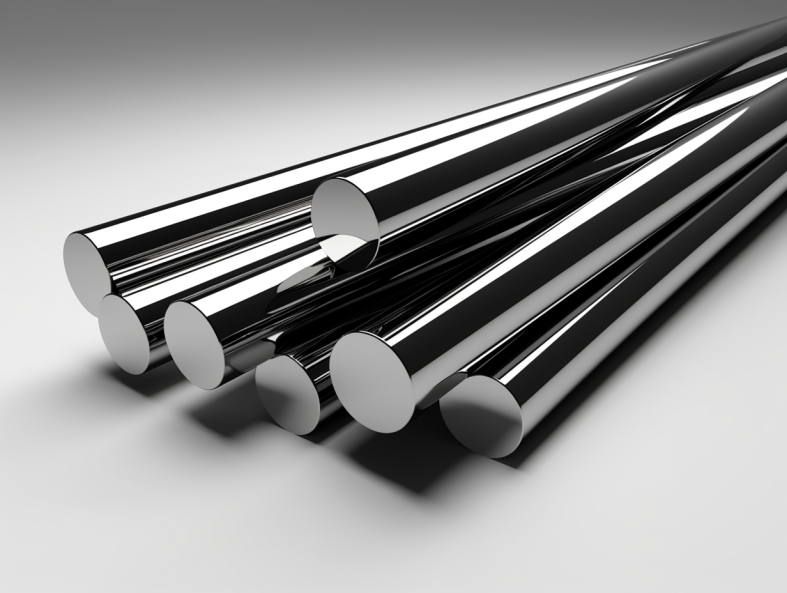
FAQ
Here are some frequently asked questions about tungsten carbide hardfacing rods, formatted in a table for clarity:
Question | Answer |
---|---|
What is tungsten carbide hardfacing? | Tungsten carbide hardfacing involves applying a layer of tungsten carbide particles onto a metal surface to enhance wear resistance. |
How are tungsten carbide hardfacing rods applied? | They are typically applied through welding processes such as oxy-acetylene or arc welding. |
What are the main benefits of using tungsten carbide hardfacing rods? | They provide exceptional hardness, wear resistance, and durability, extending the life of metal surfaces. |
Can tungsten carbide hardfacing rods be used in high-temperature environments? | Yes, certain types like WC-Co 20% are designed for high-temperature stability. |
How do I select the right tungsten carbide hardfacing rod for my application? | Consider factors like abrasion resistance, impact resistance, corrosion resistance, and operating temperature. |
Are there any specific standards for tungsten carbide hardfacing rods? | Yes, they often meet standards like AWS A5.21 and ISO 9001. |
What is the typical hardness of tungsten carbide hardfacing rods? | It usually ranges from 1600 to 2200 HV, depending on the composition. |
Can these rods be customized? | Yes, many suppliers offer custom alloy compositions to meet specific application requirements. |
What industries commonly use tungsten carbide hardfacing rods? | They are used in mining, construction, agriculture, manufacturing, oil and gas, power generation, and more. |
Where can I buy tungsten carbide hardfacing rods? | They are available from suppliers like Hardfacing Solutions Inc., Global Tungsten & Powders, Kennametal, and more. |
Conclusion
Tungsten carbide hardfacing rods are an invaluable tool in many industries, offering unmatched wear resistance, durability, and performance. Whether you’re protecting mining equipment, construction tools, or agricultural machinery, selecting the right tungsten carbide hardfacing rod can make a significant difference in operational efficiency and cost savings.
By understanding the different types, properties, applications, and selection criteria, you can make informed decisions to ensure your equipment and surfaces remain protected under the harshest conditions. Always consider the specific needs of your application and consult with suppliers to find the best product for your requirements.