Tungsten carbide is one of the toughest materials on Earth, making it essential in industries requiring strength, durability, and wear resistance. Whether you’re involved in manufacturing, mining, or precision machining, you’ve probably encountered tungsten carbide in some form. But did you know that not all tungsten carbide grades are the same? The different grades of tungsten carbide come with varying compositions, properties, and applications. Understanding these differences is key to making the right choice for your needs.
In this article, we’ll explore the details of tungsten carbide grades, the factors affecting their properties, and how to select the best grade for your specific application. From raw material analysis to detailed production processes, we’ll cover everything you need to know.
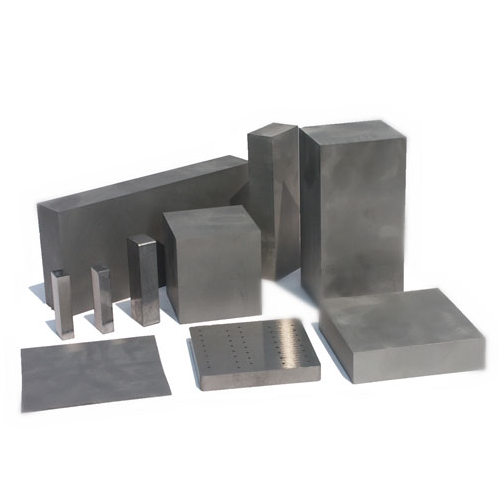
Types of Tungsten Carbide Grades
Before we dive into the specifics of tungsten carbide grades, let’s first look at the various types of grades available on the market. These grades are determined by the tungsten carbide powder’s composition and how it’s processed.
Tungsten Carbide Powder Models
Here are 10 specific tungsten carbide powder models with detailed descriptions:
Grade | Composition | Key Characteristics | Applications |
---|---|---|---|
WC-Co 10 | 90% Tungsten Carbide, 10% Cobalt | High hardness, good wear resistance, moderate toughness | Used in cutting tools, drill bits, and mining equipment. |
WC-Co 20 | 80% Tungsten Carbide, 20% Cobalt | Enhanced toughness and impact resistance | Suitable for oilfield equipment and heavy-duty tools. |
WC-Ni 6 | 94% Tungsten Carbide, 6% Nickel | Good corrosion resistance, moderate hardness | Ideal for cold-working and abrasive applications. |
WC-Co 30 | 70% Tungsten Carbide, 30% Cobalt | Extremely tough, high wear resistance | Applied in rock drilling, construction, and mining. |
WC-Co 12 | 88% Tungsten Carbide, 12% Cobalt | Balanced hardness and toughness | Commonly used for automotive and aerospace tooling. |
WC-Fe 7 | 93% Tungsten Carbide, 7% Iron | Excellent wear resistance, lower cost | Used in cutting and grinding tools for metalworking. |
WC-Co 8 | 92% Tungsten Carbide, 8% Cobalt | High hardness, moderate wear resistance | Popular in wood and plastic cutting tools. |
WC-Co 15 | 85% Tungsten Carbide, 15% Cobalt | Good resistance to shock and impact | Ideal for mining, construction, and heavy machinery. |
WC-Ni 3 | 97% Tungsten Carbide, 3% Nickel | High strength, low cost | Suitable for budget applications in non-high-wear areas. |
WC-Co 25 | 75% Tungsten Carbide, 25% Cobalt | Excellent toughness, moderate wear resistance | Ideal for oil and gas drilling, and high-impact tools. |
These grades are tailored for different applications, and the choice of grade depends on the specific needs of the task.
Raw Material and Composition Analysis of Tungsten Carbide Grades
Tungsten carbide is made by combining tungsten metal (usually in powder form) with carbon to form the carbide. This process requires precise control of temperature and conditions to achieve the desired hardness and durability.
Composition Breakdown
- Tungsten (W): The primary component, making up the majority of the material. Tungsten is known for its extreme hardness and high melting point, which is why it contributes significantly to the toughness of the final product.
- Cobalt (Co): Cobalt is often used as a binder to hold the tungsten carbide particles together. The proportion of cobalt affects the material’s toughness and wear resistance.
- Nickel (Ni): In some grades, nickel is used instead of cobalt. Nickel enhances the material’s corrosion resistance, making it suitable for certain industrial applications.
- Iron (Fe): Iron is another binder that can be used in some grades of tungsten carbide. It is often employed in more cost-effective grades, though it might not offer the same level of toughness as cobalt.
Applications of Tungsten Carbide Grades
Each tungsten carbide grade has distinct advantages depending on its composition. Below is a table outlining the typical applications for different grades.
Tungsten Carbide Grade | Common Applications |
---|---|
WC-Co 10 | Cutting tools, drilling bits, wear parts for machinery |
WC-Co 20 | Mining equipment, oilfield tools, industrial blades |
WC-Ni 6 | Cold-working tools, abrasive applications, machining components |
WC-Co 30 | Rock drilling, mining, construction, wear-resistant parts |
WC-Co 12 | Aerospace components, automotive tooling, high-precision tools |
WC-Fe 7 | Grinding tools, cutting edges, industrial cutting machinery |
WC-Co 8 | Plastic and wood processing tools, general cutting applications |
WC-Co 15 | Heavy-duty drilling, construction tools, mining machinery |
WC-Ni 3 | Non-high-wear tools, cost-effective applications |
WC-Co 25 | Oil and gas exploration, high-impact and high-temperature tools |
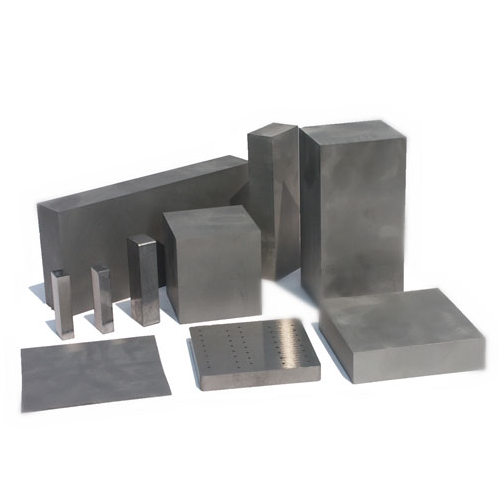
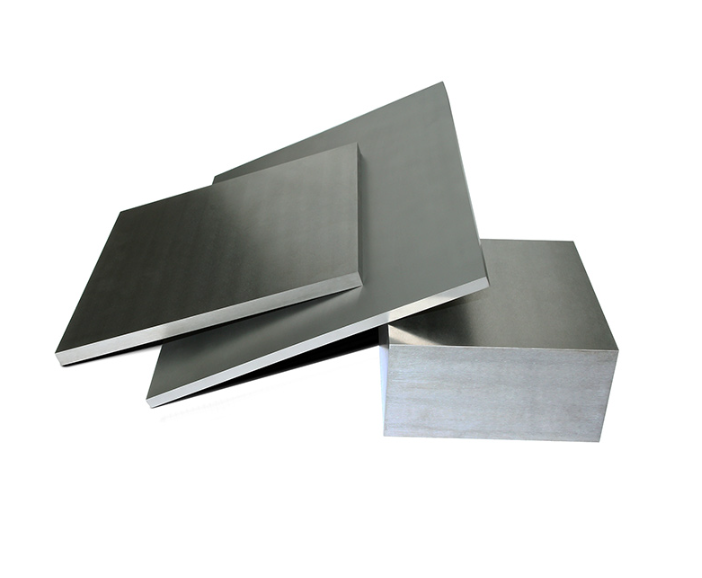
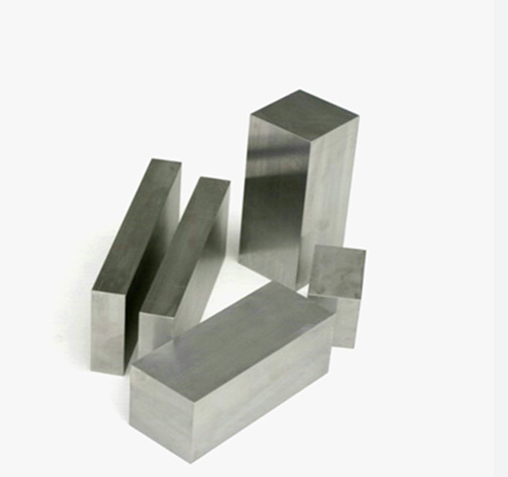
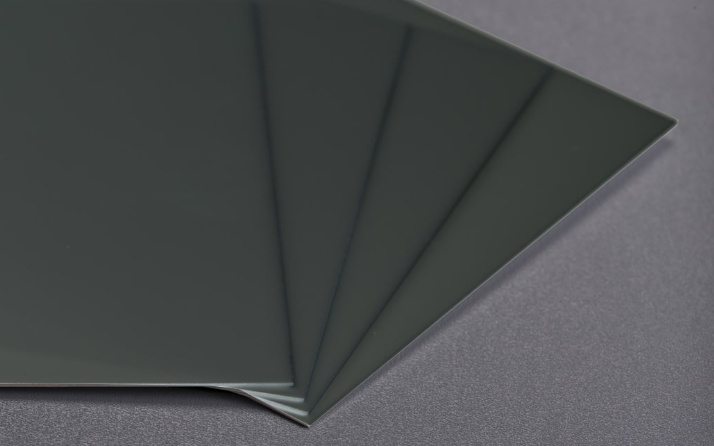
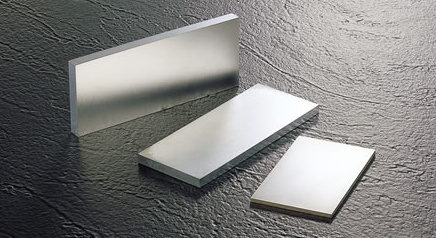
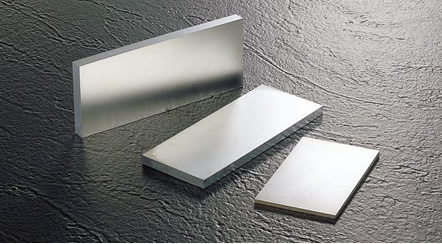
Production Process Flow of Tungsten Carbide Grades
The production of tungsten carbide begins with the combination of tungsten powder and carbon (in the form of graphite). This mixture is then subjected to a high-temperature process known as sintering. Here’s an overview of the production flow:
Production Process Steps:
- Powder Preparation: Tungsten powder is mixed with a carbon source (typically graphite) to create tungsten carbide powder.
- Binder Addition: Cobalt, nickel, or iron powder is mixed with the tungsten carbide powder to form a binder phase that holds the carbide particles together.
- Molding: The mixture is shaped into the desired form using a process called cold pressing.
- Sintering: The shaped material is heated at extremely high temperatures (usually 1,400–1,600°C) in a vacuum or controlled atmosphere to bind the tungsten carbide particles together.
- Finishing: After sintering, the material undergoes finishing processes like grinding, polishing, or coating to achieve the final product.
Material Properties of Tungsten Carbide Grades
The key properties of tungsten carbide grades are influenced by the amount of tungsten, cobalt, nickel, and other additives used in the composition. Below is a table presenting some of the important material properties for different tungsten carbide grades.
Property | WC-Co 10 | WC-Co 20 | WC-Ni 6 | WC-Co 30 | WC-Co 12 |
---|---|---|---|---|---|
Hardness (HRA) | 88-90 | 85-88 | 90-92 | 85-88 | 88-90 |
Density (g/cm³) | 15.2 | 15.3 | 14.9 | 15.0 | 15.1 |
Compressive Strength | 5000 MPa | 6000 MPa | 5500 MPa | 6500 MPa | 5800 MPa |
Flexural Strength | 2000 MPa | 2200 MPa | 2100 MPa | 2500 MPa | 2200 MPa |
Tensile Strength | 1400 MPa | 1500 MPa | 1300 MPa | 1600 MPa | 1450 MPa |
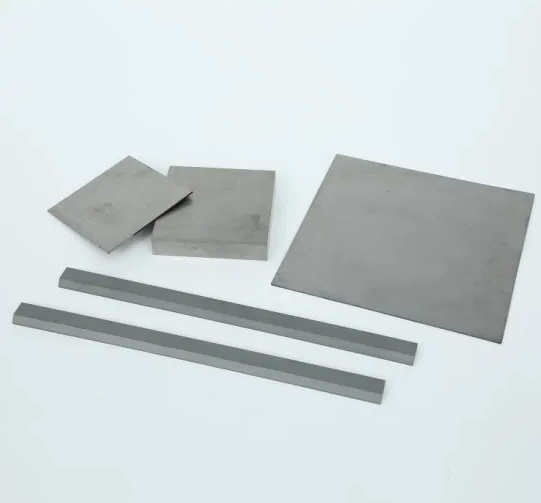
Choosing Tungsten Carbide Grades Supplier
When choosing a supplier for tungsten carbide, it’s important to compare various aspects such as pricing, delivery time, and product quality. The right supplier should have a reputation for consistency, reliability, and technical support. Below is a table to guide you in selecting the right supplier.
Supplier Criteria | Considerations |
---|---|
Reputation | Look for suppliers with positive customer feedback and years of experience in the industry. |
Pricing | Compare prices from multiple suppliers to ensure you’re getting competitive rates without compromising quality. |
Quality Control | Ensure the supplier follows strict quality control processes, including certifications like ISO. |
Customization | Some suppliers offer custom formulations based on your needs. |
Delivery Time | Check if the supplier can meet your delivery schedules. |
How to Select the Right Tungsten Carbide Grade
Selecting the right grade of tungsten carbide depends on the application requirements. Consider the following parameters:
- Wear Resistance: If the material will experience extreme wear, choose a grade with higher tungsten content.
- Impact Resistance: For applications that involve high impact or shock, grades with higher cobalt or iron content may be preferred.
- Cost: Some grades are more cost-effective than others. For general applications, lower-grade tungsten carbide with a higher binder content can suffice.
Advantages and Limitations of Tungsten Carbide Grades
Advantages:
- Extreme Hardness: Tungsten carbide is one of the hardest materials, making it perfect for wear-resistant tools and machinery.
- High Wear Resistance: It resists wear and tear, even in harsh industrial environments.
- Versatility: With different grades available, you can choose the best material for your specific needs.
Limitations:
- Brittleness: While it is incredibly hard, tungsten carbide can be brittle under certain conditions.
- Cost: Some high-performance grades can be expensive due to their material composition and manufacturing process.
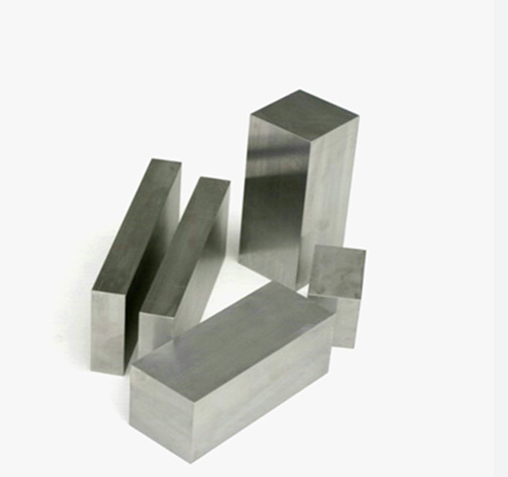
FAQ
Question | Answer |
---|---|
What are the main differences between tungsten carbide grades? | The main differences lie in the binder content (cobalt, nickel, or iron), which affects toughness, wear resistance, and cost. Each grade has unique properties suited to different applications. |
Why is tungsten carbide so hard? | Tungsten carbide is hard due to the strong bond between tungsten and carbon atoms, which creates a dense structure that resists scratching and abrasion. |
Can I use tungsten carbide in all machining applications? | No, it’s ideal for high-impact, high-wear applications. For lower-stress applications, softer materials might be more cost-effective. |
Conclusion
Tungsten carbide is a powerhouse in the world of industrial materials. With a wide range of grades available, each offering different benefits in terms of hardness, toughness, and wear resistance, it’s crucial to choose the right one for your specific application. By understanding the composition, properties, and applications of various tungsten carbide grades, you can make more informed decisions that will enhance your production processes and improve the lifespan of your tools and machinery.