Introduction
Definition of Tungsten Carbide Drill Blanks
Tungsten carbide drill blanks are high-performance cutting tools used in various industries for drilling holes in hard materials. These drill blanks are made from a combination of tungsten and carbon, resulting in a material that is extremely hard and wear-resistant. The definition of tungsten carbide drill blanks refers to their ability to withstand high temperatures, maintain sharpness, and deliver precision drilling. Due to their exceptional durability and strength, tungsten carbide drill blanks are widely used in applications such as metalworking, woodworking, and mining. These versatile tools are essential for achieving accurate and efficient drilling operations in challenging materials.
History of Tungsten Carbide Drill Blanks
Tungsten carbide drill blanks have a rich history that dates back to the early 20th century. The development of tungsten carbide as a material for drill blanks revolutionized the drilling industry. In the early years, drill blanks were made from high-speed steel, which had its limitations in terms of hardness and durability. However, with the discovery of tungsten carbide, a compound of tungsten and carbon, drill blanks became much stronger and more resistant to wear and heat. This breakthrough in material technology paved the way for the production of high-performance drill blanks that could withstand the toughest drilling conditions. Today, tungsten carbide drill blanks are widely used in various industries, including automotive, aerospace, and manufacturing, due to their exceptional hardness, toughness, and longevity.
Applications of Tungsten Carbide Drill Blanks
Tungsten carbide drill blanks are widely used in various industries due to their exceptional hardness and wear resistance. One of the key applications of tungsten carbide drill blanks is in the manufacturing of cutting tools, such as drills, end mills, and reamers. The superior hardness of tungsten carbide allows these tools to cut through tough materials like steel, cast iron, and stainless steel with ease, making them essential in metalworking and machining processes. Additionally, tungsten carbide drill blanks find applications in the mining industry for drilling and exploration purposes. Their durability and resistance to wear make them ideal for drilling into hard rock formations. Furthermore, tungsten carbide drill blanks are also utilized in the construction industry for drilling holes in concrete and masonry. Overall, the applications of tungsten carbide drill blanks are diverse and crucial in various sectors where high-performance drilling is required.
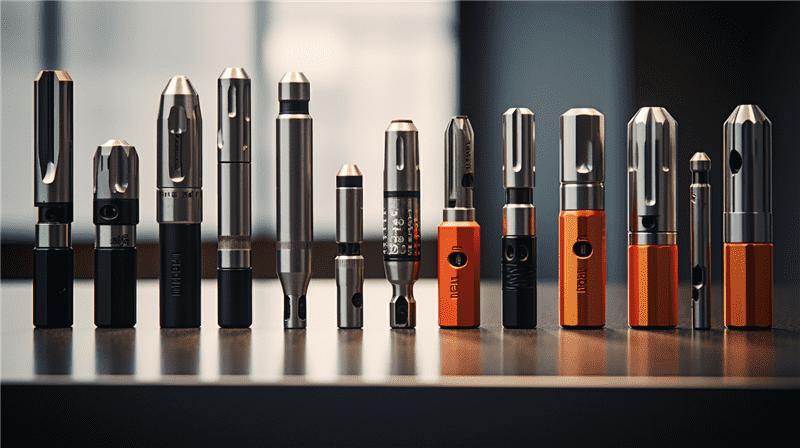
Composition of Tungsten Carbide Drill Blanks
Tungsten Carbide
Tungsten carbide, also known as cemented carbide, is a versatile and highly durable material used in various industries. It is made by combining tungsten and carbon atoms, resulting in a hard and wear-resistant compound. Tungsten carbide drill blanks, in particular, are widely used in the manufacturing of cutting tools and drilling equipment. These blanks are known for their exceptional hardness and ability to withstand high temperatures, making them ideal for drilling through tough materials such as metal, wood, and concrete. With their superior strength and longevity, tungsten carbide drill blanks are a popular choice among professionals and DIY enthusiasts alike for precision drilling applications.
Cobalt Binder
Cobalt binder is a crucial component in tungsten carbide drill blanks. It acts as a binding agent, holding the tungsten carbide particles together and providing strength and durability to the drill blanks. The cobalt binder also helps in improving the overall performance of the drill blanks by enhancing their resistance to wear and heat. With the right amount of cobalt binder, tungsten carbide drill blanks can withstand high-speed drilling and heavy-duty applications, making them an excellent choice for various industries such as manufacturing, construction, and mining.
Other Additives
Tungsten carbide drill blanks are widely used in various industries due to their exceptional hardness and wear resistance. However, in addition to tungsten carbide, there are several other additives that can be incorporated into drill blanks to enhance their performance. These additives may include cobalt, nickel, titanium, and tantalum, among others. Each additive brings its unique properties to the drill blanks, such as improved toughness, increased corrosion resistance, and enhanced thermal conductivity. By combining tungsten carbide with these additives, manufacturers can create drill blanks that are customized for specific applications, ensuring optimal performance and longevity.
Manufacturing Process
Powder Preparation
Powder preparation is a crucial step in the production of tungsten carbide drill blanks. It involves carefully selecting and blending the raw materials, which typically include tungsten powder and carbon black. The goal is to create a homogeneous mixture with the desired composition and particle size distribution. This is achieved through various processes such as milling, mixing, and sieving. The quality of the powder preparation directly affects the performance and durability of the drill blanks, making it a critical aspect of the manufacturing process.
Mixing and Blending
Mixing and blending are crucial processes in the production of tungsten carbide drill blanks. These processes involve combining tungsten carbide powder with a binder material, such as cobalt, to create a homogeneous mixture. The mixture is then carefully blended to ensure uniform distribution of the binder material throughout the tungsten carbide particles. This step is essential for achieving the desired properties and performance of the drill blanks. The mixing and blending process requires precision and expertise to ensure the final product meets the highest quality standards.
Compaction and Shaping
Compaction and shaping are crucial processes in the production of tungsten carbide drill blanks. Compaction involves compressing the tungsten carbide powder into a desired shape using high pressure. This process helps to achieve a high density and uniformity in the material, ensuring the strength and durability of the drill blanks. Shaping, on the other hand, involves forming the compacted powder into the final shape of the drill blanks. This can be done through various techniques such as extrusion, pressing, or injection molding. The precision and accuracy of the shaping process are essential to ensure that the drill blanks meet the required specifications and dimensions. Overall, compaction and shaping play a vital role in the manufacturing of tungsten carbide drill blanks, ensuring their quality and performance.
Properties of Tungsten Carbide Drill Blanks
Hardness
Tungsten carbide drill blanks are known for their exceptional hardness. With a hardness rating of up to 90 HRA, these drill blanks are incredibly durable and can withstand high temperatures and heavy loads. The hardness of tungsten carbide makes it ideal for drilling through tough materials such as stainless steel, cast iron, and hardened steel. Whether used in industrial applications or for DIY projects, the hardness of tungsten carbide drill blanks ensures long-lasting performance and reliable drilling results.
Wear Resistance
Wear resistance is a key characteristic of tungsten carbide drill blanks. Due to its high hardness and strength, tungsten carbide is able to withstand the abrasive forces that occur during drilling operations. This exceptional wear resistance ensures that the drill blanks maintain their cutting edge for longer periods of time, resulting in increased productivity and cost savings. Additionally, the wear resistance of tungsten carbide allows for the drilling of tough materials such as stainless steel, cast iron, and hardened steel with ease and precision. With its remarkable ability to resist wear, tungsten carbide drill blanks are the preferred choice for demanding drilling applications.
Heat Resistance
Tungsten carbide drill blanks are known for their exceptional heat resistance. This unique property makes them ideal for applications that involve high temperatures and intense heat. Whether it’s drilling through tough materials or working in extreme conditions, tungsten carbide drill blanks can withstand the heat and maintain their performance. The high melting point of tungsten carbide, combined with its hardness and strength, allows it to resist thermal deformation and maintain its shape even at elevated temperatures. This makes tungsten carbide drill blanks a reliable choice for professionals in industries such as aerospace, automotive, and manufacturing, where heat resistance is crucial for successful operations.
Advantages of Tungsten Carbide Drill Blanks
High Cutting Speed
Tungsten carbide drill blanks are known for their exceptional performance when it comes to high cutting speed. With their unique composition and hardness, these drill blanks can effortlessly cut through tough materials such as stainless steel, cast iron, and hardened steel. The high cutting speed provided by tungsten carbide drill blanks allows for efficient and precise drilling, making them an ideal choice for industrial applications that require fast and accurate drilling operations. Whether it’s for metalworking, construction, or automotive industries, the use of tungsten carbide drill blanks ensures enhanced productivity and superior results.
Long Tool Life
Tungsten carbide drill blanks are known for their exceptional long tool life. This high-performance material is renowned for its hardness and durability, making it perfect for demanding drilling applications. With tungsten carbide drill blanks, you can expect extended usage without compromising on performance. These drill blanks are designed to withstand high temperatures, abrasion, and wear, ensuring that they maintain their sharpness and effectiveness over time. Whether you’re drilling through tough materials or working on precision projects, tungsten carbide drill blanks offer the reliability and longevity you need for successful drilling operations.
Versatility
Tungsten carbide drill blanks offer exceptional versatility in various industrial applications. With their high hardness and wear resistance, these drill blanks can effectively drill through tough materials such as steel, cast iron, and stainless steel. Additionally, their excellent thermal conductivity ensures efficient heat dissipation during drilling, preventing overheating and extending tool life. The versatility of tungsten carbide drill blanks makes them a reliable choice for professionals in industries such as automotive, aerospace, and manufacturing.
Applications of Tungsten Carbide Drill Blanks
Metalworking
Metalworking is a fascinating field that involves shaping and manipulating various types of metals. One material that plays a crucial role in metalworking is tungsten carbide drill blanks. These drill blanks are specially designed to be incredibly hard and durable, making them ideal for drilling through tough materials like steel and concrete. With their exceptional heat resistance and strength, tungsten carbide drill blanks are widely used in industries such as automotive, construction, and manufacturing. Whether it’s creating precision holes or removing material, tungsten carbide drill blanks are essential tools in the metalworking industry, enabling professionals to achieve accurate and efficient results.
Woodworking
Woodworking is a popular hobby that involves working with wood to create beautiful and functional pieces. One essential tool in woodworking is the tungsten carbide drill blanks. These drill blanks are known for their durability and strength, making them perfect for drilling through various types of wood. Whether you’re a professional woodworker or a DIY enthusiast, having tungsten carbide drill blanks in your toolbox is a must. They provide precision and efficiency, allowing you to create precise holes and achieve smooth finishes. With tungsten carbide drill blanks, you can take your woodworking projects to the next level and create stunning pieces that will last for years to come.
Mining and Construction
Mining and construction industries heavily rely on tungsten carbide drill blanks for their drilling operations. These high-performance tools are known for their exceptional hardness and wear resistance, making them ideal for cutting through tough materials like rocks, concrete, and metal. Tungsten carbide drill blanks are widely used in mining operations to extract valuable minerals and ores from the earth’s crust. In the construction industry, these drill blanks are essential for various tasks such as drilling holes for foundations, installing utility lines, and creating tunnels. With their durability and precision, tungsten carbide drill blanks play a crucial role in ensuring efficient and reliable drilling in mining and construction projects.