When it comes to materials known for their exceptional hardness and wear resistance, tungsten carbide cemented plates are at the top of the list. These plates are essential in various industries due to their robustness and reliability. This guide will delve deep into what makes tungsten carbide cemented plates so special, their applications, and how to select the right one for your needs. Let’s dive in!
Overview of Tungsten Carbide Cemented Plates
Tungsten carbide cemented plates are made by combining tungsten carbide powder with a binder metal, usually cobalt. This combination creates a material that is incredibly hard and resistant to wear, making it ideal for applications that require durability and strength. These plates are commonly used in industries such as mining, metalworking, and construction due to their ability to withstand harsh conditions and maintain their structural integrity.
Key Properties of Tungsten Carbide Cemented Plates
- Hardness: Tungsten carbide is one of the hardest materials available, providing exceptional wear resistance.
- Strength: High compressive strength makes it suitable for demanding applications.
- Durability: Resistant to deformation, corrosion, and abrasion.
- Thermal Stability: Maintains properties at high temperatures.
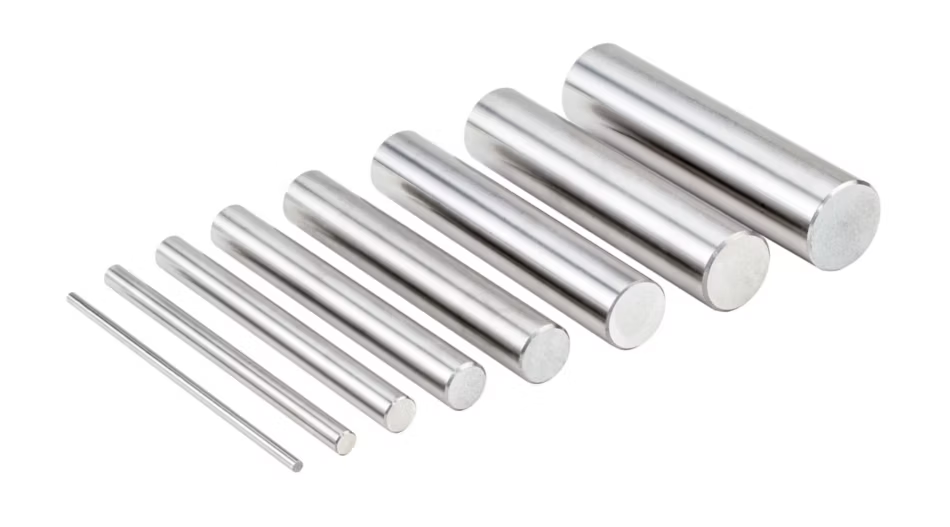
Types of Tungsten Carbide Cemented Plates
Understanding the different types of tungsten carbide cemented plates is crucial for selecting the right one for your application. Here’s a comprehensive table to help you out.
Type | Description |
---|---|
Standard Grade | Basic tungsten carbide plate with good hardness and toughness. |
Micro Grain | Finer grain size for higher hardness and better surface finish. |
Corrosion-Resistant Grade | Enhanced resistance to chemical corrosion, suitable for harsh environments. |
Impact-Resistant Grade | Improved toughness and resistance to impact, ideal for heavy-duty applications. |
Heat-Resistant Grade | Maintains properties at high temperatures, suitable for high-heat applications. |
Wear-Resistant Grade | Superior wear resistance for abrasive environments. |
Ultra-Fine Grain | Extremely fine grain size for the highest hardness and best surface finish. |
High Compressive Strength | Designed for applications requiring high compressive strength. |
Binder-Free | Pure tungsten carbide with no binder, offering maximum hardness. |
Mixed Binder | Combination of different binders to tailor properties for specific applications. |
Applications of Tungsten Carbide Cemented Plates
Tungsten carbide cemented plates are versatile and used in various applications. Here’s a table outlining where these plates are commonly used.
Application | Description |
---|---|
Mining | Used in drilling, cutting, and crushing due to high wear resistance. |
Metalworking | Ideal for cutting tools, dies, and punches. |
Construction | Used in tools and machinery that encounter abrasive materials. |
Oil and Gas | Employed in drilling equipment and wear parts. |
Aerospace | Components that require high strength and resistance to extreme conditions. |
Automotive | Engine components and other parts that experience high wear and heat. |
Medical | Surgical tools and implants requiring high precision and durability. |
Textile | Components in machinery that undergo continuous wear. |
Electronics | Used in manufacturing of electronic components due to high precision. |
Defense | Armor-piercing projectiles and other high-strength applications. |
Material Properties of Tungsten Carbide Cemented Plates
Understanding the material properties is essential for choosing the right plate for your application. Here are the key properties.
Property | Description |
---|---|
Hardness | Typically measured in Vickers (HV), ranges from 1400 to 2400 HV. |
Compressive Strength | Up to 4000 MPa, providing exceptional strength under load. |
Density | Approximately 15 g/cm³, depending on the binder content. |
Fracture Toughness | Measured in MPa√m, indicating resistance to crack propagation. |
Thermal Conductivity | Around 85 W/mK, allowing for effective heat dissipation. |
Young’s Modulus | Approximately 550 GPa, indicating stiffness. |
Poisson’s Ratio | Around 0.22, reflecting the material’s deformation under stress. |
Thermal Expansion | Low coefficient, around 5.0 x 10^-6 /°C, minimizing expansion under heat. |
Corrosion Resistance | Highly resistant to most acids and alkalis, depending on the binder used. |
Magnetic Properties | Depending on binder type, some grades are magnetic (cobalt-bonded), others are not. |
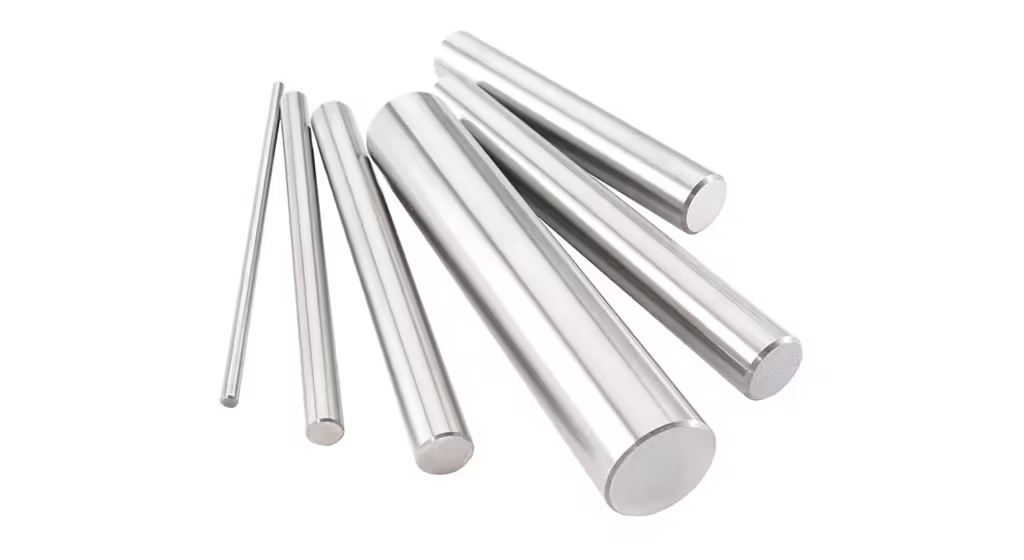
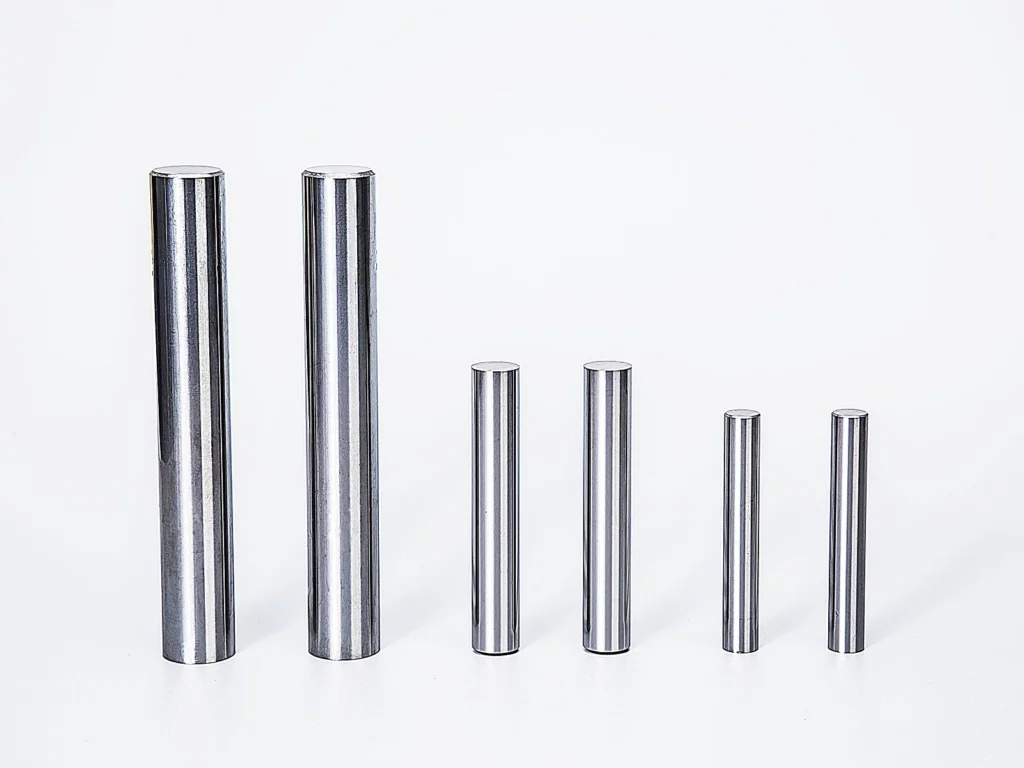
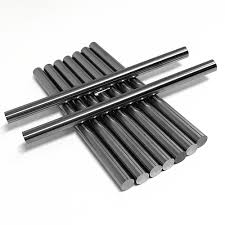
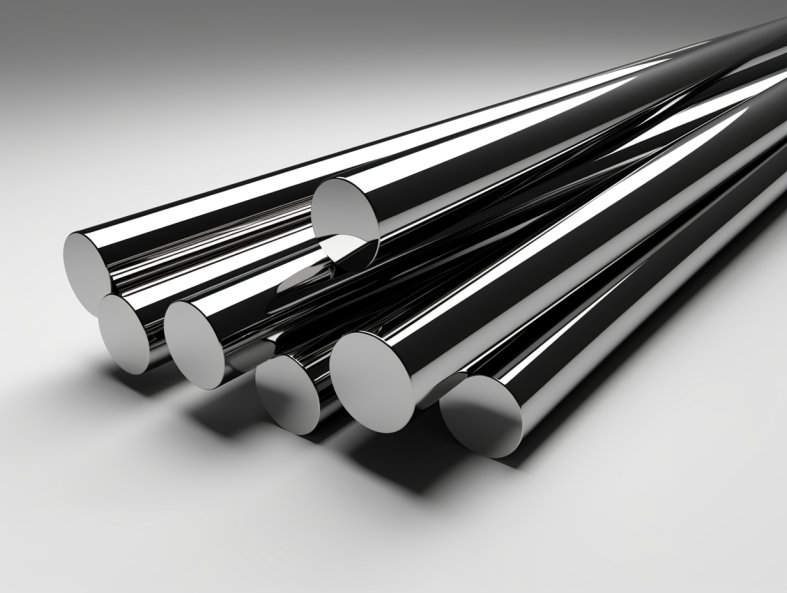
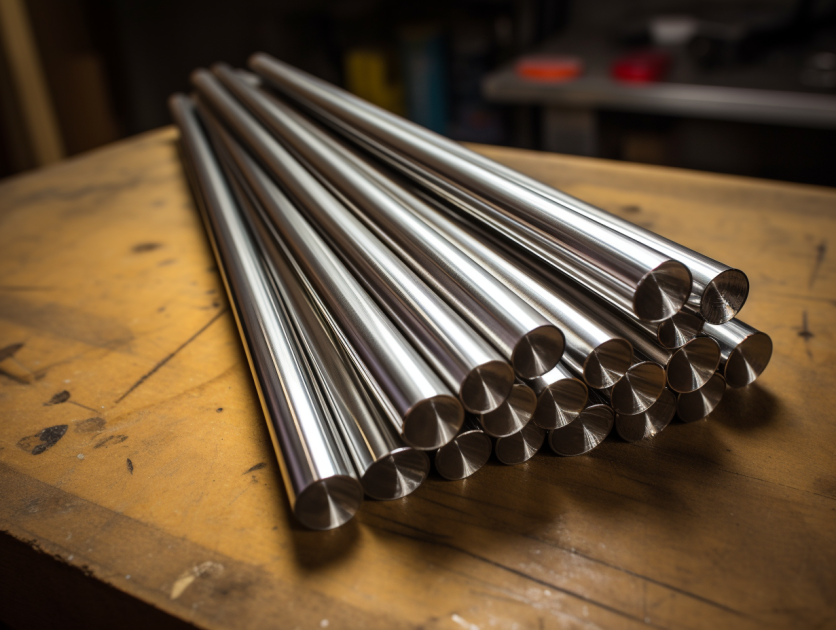
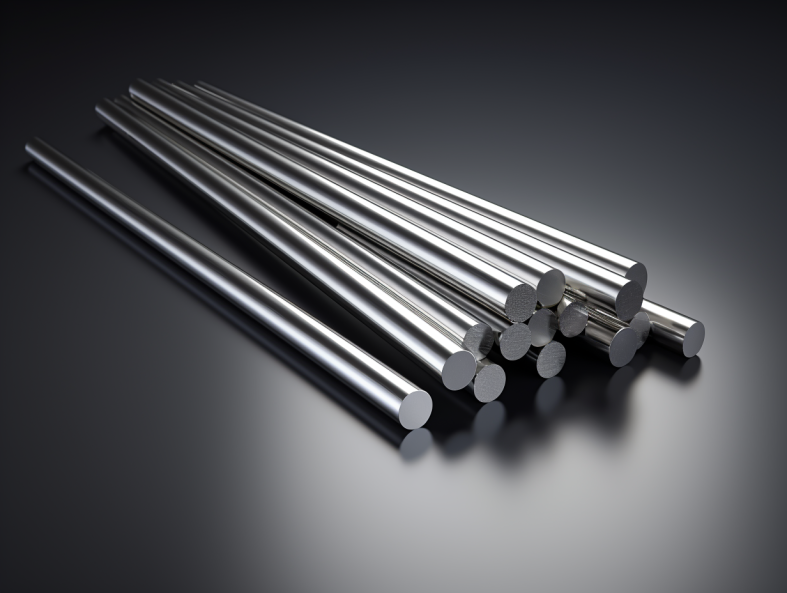
Composition and Characteristics
Here’s a detailed look at the composition and characteristics of tungsten carbide cemented plates.
Component | Description |
---|---|
Tungsten Carbide | Primary component, provides hardness and wear resistance. |
Cobalt Binder | Commonly used binder, provides toughness and strength. |
Nickel Binder | Alternative to cobalt, offers better corrosion resistance. |
Chromium Carbide | Sometimes added to enhance corrosion resistance and wear properties. |
Tantalum/Niobium | Added to improve high-temperature properties and toughness. |
Vanadium Carbide | Enhances grain refinement and improves overall properties. |
Hardness, Strength, and Wear Resistance
The following table highlights the hardness, strength, and wear resistance of different tungsten carbide cemented plates.
Grade | Hardness (HV) | Compressive Strength (MPa) | Wear Resistance |
---|---|---|---|
Standard Grade | 1400 | 3000 | High |
Micro Grain | 2000 | 3500 | Very High |
Corrosion-Resistant | 1600 | 2800 | Moderate |
Impact-Resistant | 1300 | 4000 | High |
Heat-Resistant | 1500 | 3200 | High |
Wear-Resistant | 2200 | 2900 | Very High |
Ultra-Fine Grain | 2400 | 3400 | Extremely High |
High Compressive | 1400 | 4000 | High |
Binder-Free | 2500 | 3200 | Extremely High |
Mixed Binder | 1800 | 3300 | High |
Specifications, Sizes, and Shapes
When selecting tungsten carbide cemented plates, knowing the specifications, sizes, and shapes is crucial. Here’s a table to guide you.
Specification | Details |
---|---|
Sizes | Available in a range of sizes, from small inserts to large plates. |
Shapes | Rectangular, square, circular, custom shapes available. |
Thickness | Typically ranges from 1 mm to 50 mm, customizable as per requirement. |
Standards | Compliant with international standards like ISO, ASTM, and DIN. |
Surface Finish | Options include ground, polished, or unpolished. |
Edge Type | Sharp edges, chamfered edges, or custom edge profiles. |
Tolerances | High precision tolerances available, typically within ±0.05 mm. |
Suppliers and Pricing Details
Finding the right supplier and understanding pricing is key to making an informed decision. Here’s a table with some details.
Supplier | Region | Price Range (per kg) | Contact Information |
---|---|---|---|
Supplier A | North America | $50 – $70 | [email protected], +1 234 567 890 |
Supplier B | Europe | €60 – €80 | [email protected], +44 123 456 789 |
Supplier C | Asia | $45 – $65 | [email protected], +86 987 654 321 |
Supplier D | Global | $55 – $75 | [email protected], +1 800 123 456 |
Supplier E | South America | $50 – $70 | [email protected], +55 21 1234 5678 |
Selecting the Right Tungsten Carbide Cemented Plate
Choosing the right tungsten carbide cemented plate can be challenging. Here’s a table to help guide your selection process.
Criteria | Considerations |
---|---|
Application | Identify the specific use case (e.g., mining, cutting tools, construction). |
Material Properties | Consider hardness, strength, wear resistance, and other key properties relevant to your needs. |
Size and Shape | Ensure the plate size and shape match your application requirements. |
Budget | Balance cost with performance needs. |
Supplier Reputation | Choose suppliers with good reviews and proven track records. |
Customization Needs | Determine if you need custom sizes, shapes, or properties. |
Environmental Factors | Consider exposure to corrosive substances, high temperatures, and mechanical stress. |
Advantages and Limitations
To help you make an informed decision, here’s a comparison of the advantages and limitations of tungsten carbide cemented plates.
Advantages | Limitations |
---|---|
Exceptional Hardness | Can be brittle and prone to cracking under heavy impact. |
High Wear Resistance | Higher cost compared to other materials. |
Durability | Heavier than alternative materials. |
Thermal Stability | Limited availability of some custom grades. |
Versatility | Requires specialized tools for machining and shaping. |
Corrosion Resistance | Some grades may require specific conditions to achieve optimal performance. |
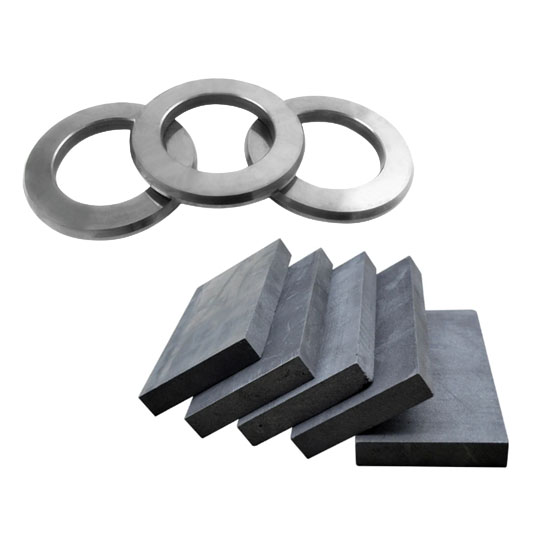
FAQ
What are tungsten carbide cemented plates used for?
Tungsten carbide cemented plates are used in various industries, including mining, metalworking, construction, oil and gas, aerospace, automotive, medical, textile, electronics, and defense. They are valued for their exceptional hardness, wear resistance, and durability.
How do I choose the right tungsten carbide cemented plate for my application?
When choosing the right plate, consider the specific application, required material properties, size and shape, budget, supplier reputation, customization needs, and environmental factors. Each of these criteria will help ensure you select a plate that meets your needs.
What are the main advantages of tungsten carbide cemented plates?
The main advantages include exceptional hardness, high wear resistance, durability, thermal stability, versatility, and corrosion resistance. These properties make them suitable for demanding applications in various industries.
Are there any limitations to using tungsten carbide cemented plates?
Yes, there are some limitations. Tungsten carbide cemented plates can be brittle and prone to cracking under heavy impact. They are also more expensive compared to other materials and require specialized tools for machining and shaping.
Can tungsten carbide cemented plates be customized?
Yes, tungsten carbide cemented plates can be customized in terms of size, shape, and properties. Many suppliers offer custom solutions to meet specific application requirements.
How do tungsten carbide cemented plates compare to other materials?
Tungsten carbide cemented plates are harder and more wear-resistant than many other materials, including steel and ceramics. However, they can be more brittle and expensive. The choice of material depends on the specific needs of the application.
What are the typical sizes and shapes available for tungsten carbide cemented plates?
Tungsten carbide cemented plates are available in a range of sizes, from small inserts to large plates, and in various shapes, including rectangular, square, circular, and custom shapes. Thicknesses typically range from 1 mm to 50 mm.
What factors affect the price of tungsten carbide cemented plates?
The price of tungsten carbide cemented plates can be affected by factors such as the type and grade of the plate, the size and shape, the supplier, and any customization requirements. Prices can also vary by region.
What are some common applications of tungsten carbide cemented plates in the automotive industry?
In the automotive industry, tungsten carbide cemented plates are used for engine components, cutting tools, and other parts that require high wear resistance and thermal stability. They help improve the durability and performance of automotive systems.
Are tungsten carbide cemented plates environmentally friendly?
Tungsten carbide cemented plates are durable and long-lasting, reducing the need for frequent replacements and minimizing waste. However, the production process can have environmental impacts. It’s important to choose suppliers that follow environmentally responsible manufacturing practices.
Conclusion
Tungsten carbide cemented plates are invaluable in numerous industries due to their unmatched hardness, wear resistance, and durability. Understanding the types, applications, material properties, and how to select the right plate ensures you make an informed decision that meets your specific needs. Whether you’re in mining, metalworking, construction, or any other industry that demands high-performance materials, tungsten carbide cemented plates are a reliable choice. Remember to consider your application requirements, budget, and environmental factors when making your selection. With the right plate, you can enhance the efficiency and longevity of your tools and machinery, ensuring optimal performance in even the most demanding conditions.