Tungsten carbide brazed tips refer to tungsten carbide material braze-joined to a steel shank to serve as a cutting tool insert for machining applications. The hard tungsten carbide provides wear resistance while the steel shank enables mounting into tool holders.
Overview of Tungsten Carbide Brazed Tips
Tungsten carbide brazed tips feature a composite design with distinct material zones leveraging individual performance advantages:
- Fine grain tungsten carbide zone forms the functional cutting surface
- Cobalt binder matrix to facilitate sintering and provide toughness
- Braze alloy layer usually nickel or copper based
- Steel shank for mounting into insert holders
This construction combines hardness, strength and shock resistance for metal removal operations under demanding conditions.
Key attributes of tungsten carbide brazed tips:
- Composite metal cutting insert design
- High hardness tungsten carbide cutting zone
- Excellent wear resistance and edge retention
- Brazed join between WC and steel body
- Enables interrupted and heavy machining
- Lower cost alternative to solid carbide inserts
Types of Tungsten Carbide Brazed Tips
Various standard and special tool geometries are produced with brazed carbide tips including:
Type | Details |
---|---|
Turning | Positive rake styles for external turning |
Grooving | ‘L’ and ‘T’ style inserts for cut-off grooving |
Cutting-off | Triple edged blades for severing stock |
Boring | Special boring bars with brazed tip |
Custom | Special geometries for specific uses |
Composition of Tungsten Carbide Brazed Tips
Tungsten carbide brazed tip inserts consist of distinct composition zones:
Zone | Composition | Role |
---|---|---|
Functional | WC grains + Cobalt | Hard wearing cutting surface |
Braze joint | Ni, Cu, Zn alloys | Joins WC and steel |
Shank | Medium carbon steel | Enables tool mounting |
Properties of Tungsten Carbide Brazed Tips
Key properties include:
Property | Function |
---|---|
Hardness | Resists cutting edge wear during machining |
Strength | Withstands high machining forces |
Toughness | Handles impact loads interrupting cuts |
Thermal shock resistance | Allows heat generation during cutting |
Chemical resistance | Compatibility with workpiece materials |
Characteristics of Tungsten Carbide Brazed Tips
Parameter | Details |
---|---|
Grain size | Ultrafine grain sizes down to 0.4 μm |
Grades | K, P, M indicating composition |
Edge preparation | Special honing or treatments |
Dimensional accuracy | Precise control of angles and clearances |
Balance | Controlled to run true during high speeds |
Testing | Sample examination ensures quality |
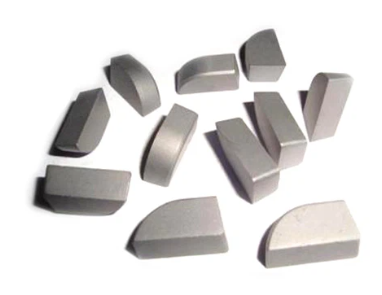
Applications of Tungsten Carbide Brazed Tips
Tungsten carbide brazed tools widely used where economical tooling for difficult materials is needed:
Application | Common Uses |
---|---|
Interrupted cutting | Milling slots, pockets, contours |
High speed machining | Turning hardened steels over 45 HRC |
Rough boring | Enlarging holes in gray and ductile cast iron |
Parting and grooving | Cutting off stock and making grooves |
Indexable tooling | Custom toolholders for multi-tip brazed blades |
Tungsten Carbide Brazed Tips for Turning
Brazed carbide tip turning inserts used for:
- Roughing cuts and semi-finishing passaes
- External longitudinal turning operations
- Type D and Type S insert styles common
- Positive rake angles from 5 to 25 degrees
- High productivity on low and medium carbon steels
Tungsten Carbide Brazed Tips for Grooving
‘L’ and ‘T’ style tungsten carbide brazed tip inserts designed for cut-off grooving operations.
Features include:
- Narrow cutting profile for deep groove depths
- Advanced groove bottom geometries
- TiAlN coating for pre-hardened steels
- Reduced tendency for workpiece burring
- Groove widths from 1.5 mm to 8 mm range
Tungsten Carbide Brazed Blades for Cutting-Off
Triple edged parting blades utilize brazed carbide tips allowing economic severed cuts. Three cutting corners per insert reduces indexings during batch production cutting.
Attributes include:
- 1.2 mm to 2.5 mm blade heights
- Coated grades resist welding
- Advanced chipbreaker designs
- Reduced vibrations from asymmetric blade style
- Tolerances approaching grind-to-size inserts
Indexable Tooling Using Tungsten Carbide Brazed Tips
Indexable custom tooling incorporates tungsten carbide brazed inserts allowing simple, low-cost tips changes after wear versus regrinding special tooling.
Tooling includes:
- Brazed carbide tips in shank boring bars
- Face and peripheral milling bodies
- Special profiled form cutters
- Multi-insert adjustable cartridges
- Quick change style tool blocks
Simplifies maintenance with tip replacement while controlling investment costs.
Tungsten Carbide Brazed Tip Specifications
International standards help define composition, properties and quality requirements:
Standard | Organization | Scope |
---|---|---|
ISO 1832 | ISA | Nominal binder content |
JIS G 4053 | Japanese Industrial Standard | Classification method |
ASTM B774 | ASTM International | Specification for brazed tips |
These help ensure brazed insert procurement to appropriate grade and style needs.
Sizes of Tungsten Carbide Brazed Tips
Common size ranges include:
Parameter | Size Range |
---|---|
Inscribed circle | 3 mm to 25 mm |
Thickness | 1.5 mm to 8 mm |
Corner radius | 0.4 mm to 2.5 mm |
Larger geometries over 25 mm diameters possible for custom boring bars, milling, and specialty applications.
Grades of Tungsten Carbide Brazed Tips
Tips use tungsten carbide grade based on nominal binder content and grain size:
Grade | Description |
---|---|
K | Low cobalt content for max hardness |
P | Intermediate cobalt for strength |
M | Higher cobalt for increased toughness |
C | Fine 0.4 μm grain size for polishable finish |
Advanced substrates and special post-sinter treatments further expand grade capabilities.
Braze Alloy Options for Tungsten Carbide Tips
Alloy Type | Composition | Properties |
---|---|---|
Nickel | Ni-Cr-B-Si / Ni-Mn | Cost effective, 600 -800°C brazing |
Copper | Cu-Zn-Mn / Cu-Mn-Ni | Higher strength, 700 – 900°C braze |
Active | Ti / Zr / Hf added | Reactive, improves carbide wetting |
Silver | Ag-Cu / Ag-Cu-Zn-Cd | Low temperature 500 – 600°C brazing |
Choice depends on carbide grade, strength needs, temperature constraints and cost targets.
Tungsten Carbide Brazed vs Sintered Tips
Parameter | Brazed Tips | Solid Carbide Inserts |
---|---|---|
Construction | Cemented WC welded to steel shank | 100% sintered WC |
Hardness | Up to 92 HRA (85-88 typical) | 92 – 94 HRA |
Strength | 700 – 900 MPa transverse rupture strength | Higher > 1000 MPa |
Toughness | Moderate fracture resistance | Higher but varies by grade |
Thermal load | Sensitive to rapid temperature changes | Better shock resistance |
Cost | Lower material cost | Expensive molded tooling |
Brazed tips offer economic performance while solid inserts provide maximum capability where affordability less critical.
Global Manufacturers of Tungsten Carbide Brazed Tips
Company | Country | Comments |
---|---|---|
Iscar | Israel | Wide range of carbide grades and geometries |
Tungaloy | Japan | Focus on turning and grooving inserts |
Sandvik Coromant | Sweden | Advanced substrates and coatings |
Kennametal | USA | Indexable and multi-tip designs |
Ceratizit | Luxembourg | Precision carbide components |
Cost Analysis of Tungsten Carbide Brazed Tips
Carbide tip costs from:
- Raw materials – powder, cobalt binder, braze alloys
- Manufacturing – pressing, sintering, grinding, brazing
- Insert geometry complexity
- Size, radius, thickness, tolerance
- Quantity and order volume
- Special coating or edge treatments
Item | Price Range |
---|---|
Indexable turning insert | $2 – $12 each |
Parting or grooving blade | $1 – $5 each |
Large diameter boring bar | $50 – $250 each |
Custom profile milling body | $100+ per piece |
Pricing varies significantly based on dimensions, grade, special features, order volume and supplier term agreements.
Advantages and Limitations of Tungsten Carbide Brazed Tips
Advantages
- Significantly lower cost than solid tungsten carbide inserts
- Tailorable binder content for hardness vs toughness needs
- Advanced carbide grain structures for specific applications
- Composite design resists sudden load changes
- Variety of standard and custom insert geometries
- Simplified tool resharpening via tip replacement
- Broad compatibility with steels, irons, exotics
Limitations
- Lower hardness and wear resistance than solid WC inserts
- Maximum operating parameters usually less than molded tips
- Braze joint integrity reliance under high stress loads
- Thermal shock resistance less than 100% sintered
- Limited extremely high precision grooving or cuts
Ongoing braze developments continue expanding capabilities while maintaining economic advantages over solid tungsten carbide tooling alternatives.
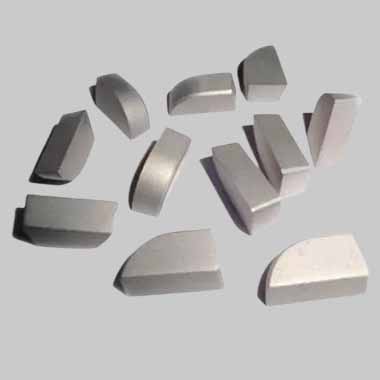
Frequently Asked Questions
What are the most commonly used braze filler alloys to join tungsten carbide and steel?
Nickel and copper based braze alloys are most common, with Ni-Cr-B-Si and Cu-Zn-Mn compositions being well proven for carbide brazing over decades of use.
What causes braze joint failures in tungsten carbide tipped cutting tools?
Potential reasons for braze failures include inadequate braze filler volumes during manufacture, brazing atmosphere issues leading to voids or inclusions, problems with brazeability of specific grades, and poor mating surface preparation prior to brazing.
Is surface grinding necessary for tungsten carbide brazed tips?
Yes, grinding after brazing is important for precise insert geometries, optimal surface finish and edge sharpness needed for clean workpiece cutting. It also exposes embedded flaws preventing in-service failures.
Can tungsten carbide brazed inserts use advanced PVD coatings?
Yes, advanced coating like TiAlN can be applied via physical vapor deposition to the carbide surface of tipped inserts. This helps resist built-up edge and improves effectiveness when machining high temperature alloys or hardened materials over 45 HRC.
What are recommended operating parameters for indexable tools using brazed tungsten carbide tips?
Indexable tooling with brazed carbide tips often limits speeds to 100-150 m/min, feed rates between 0.15–0.4 mm/rev, and depths of cut from 0.5–4 mm. Reduced DOC and widths of cut further aid multi-insert tool life between sharpenings.
What causes edge build up when machining with tungsten carbide brazed inserts?
Insufficient insert temperatures from low speeds, feeds or DOC can create smearing and welding of workpiece material. More positive geometries, TiAlN coatings and appropriate parameter selection reduces tendencies for edge build up in most materials.
When should I choose solid tungsten carbide inserts over brazed carbide tipped tooling?
Solid tungsten carbide inserts are recommended for very high precision grooving under 0.1mm land widths, micro machining, HD hard part machining over 50HRC, and extremely demanding operations needing maximum wear resistance and thermal shock tolerance.
Can I reuse tungsten carbide brazed inserts by simply re-brazing new cutting tips?
Reusing the steel shanks is not recommended – braze cycles thermally age the substrate material. New inserts should be used for reliability. However, the old shanks can potentially be recycled.
What causes insert chipping and breakage when machining using brazed carbide tools?
Chipping or fracturing during operation can result from inadequate insert grades for the application, built-up edge issues, chatter problems from improper parameter selection, or damage mishandling inserts while indexing. Eliminating the root cause is key.
What steps should I take for safely grinding tungsten carbide tipped cutting tools?
Always wear appropriate respirator masks before grinding tungsten carbide, ensure adequate ventilation, use grinding wheels matched for carbide materials, dress wheels to keep cutting surfaces fresh, go slowly to minimize heat buildup, and cool inserts with water or oil fluid during grinding.