Overview of Tungsten Carbide Blanks
Tungsten carbide blanks are integral to numerous industrial applications due to their exceptional hardness, wear resistance, and strength. These blanks serve as the foundational material for manufacturing cutting tools, wear parts, and various industrial components. Choosing the right supplier for tungsten carbide blanks can significantly impact the performance and longevity of your tools and components. In this comprehensive guide, we’ll delve into everything you need to know about tungsten carbide blanks, from types and applications to material properties and selecting the best supplier.
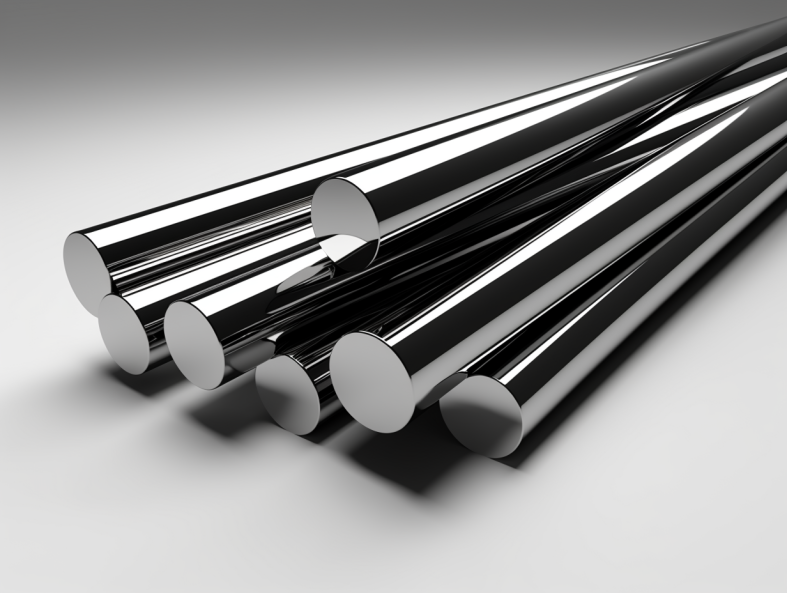
Types of Tungsten Carbide Blanks
Understanding the different types of tungsten carbide blanks is essential for selecting the right material for your specific application. Here’s a detailed breakdown of some of the most common types of tungsten carbide blanks.
Type | Description |
---|---|
K10 | Ideal for general-purpose machining and offers good wear resistance and toughness. |
K20 | Provides a balance between hardness and toughness, suitable for various cutting applications. |
K30 | Known for high hardness and wear resistance, excellent for finishing and semi-finishing. |
P10 | Perfect for light cutting, featuring high hardness and wear resistance. |
P20 | Balanced properties for general-purpose cutting, offering good toughness and wear resistance. |
P30 | Designed for heavy-duty cutting operations with enhanced toughness. |
C1 | Excellent for roughing applications, providing high impact resistance. |
C2 | Suitable for medium cutting conditions, balancing hardness and toughness. |
C3 | Used in finishing applications, offering high hardness and good wear resistance. |
C4 | Best for fine finishing and ultra-high precision cutting with superior hardness. |
Applications of Tungsten Carbide Blanks
Tungsten carbide blanks are utilized in a variety of industries due to their unique properties. Here’s how these blanks are applied across different sectors:
Application | Industry | Description |
---|---|---|
Cutting Tools | Manufacturing | Used in drills, end mills, and cutting inserts for machining metals. |
Wear Parts | Mining | Essential in the production of wear-resistant components like buttons and inserts for mining drills. |
Precision Tools | Aerospace | Applied in making precision tools for high-accuracy machining. |
Punches and Dies | Automotive | Used in the stamping and forming processes in automotive manufacturing. |
Seals and Valve Seats | Oil and Gas | Ensures durability and longevity in harsh environments. |
Boring Bars | Construction | Critical for creating accurate holes in construction materials. |
Mold and Die Components | Electronics | Used in the production of semiconductor components and micro-tools. |
Material Properties of Tungsten Carbide Blanks
The material properties of tungsten carbide blanks make them highly desirable for various industrial applications. Let’s explore these properties in detail:
Property | Description |
---|---|
Hardness | Tungsten carbide is known for its extreme hardness, ranging from 70 to 90 HRA. |
Wear Resistance | Exhibits superior wear resistance, making it ideal for high-stress environments. |
Toughness | Offers a good balance of hardness and toughness, depending on the grade. |
Thermal Conductivity | High thermal conductivity ensures heat is effectively dissipated during machining. |
Corrosion Resistance | Good resistance to corrosion, extending the lifespan of tools in corrosive environments. |
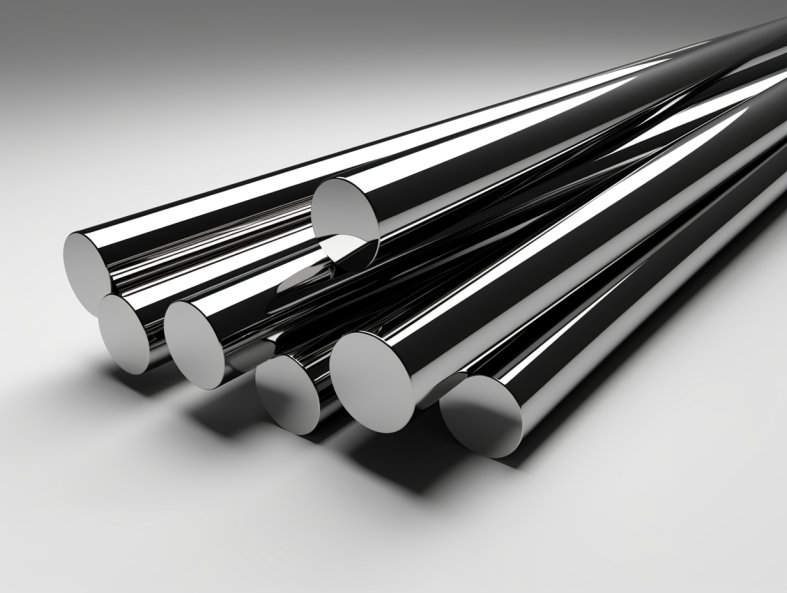
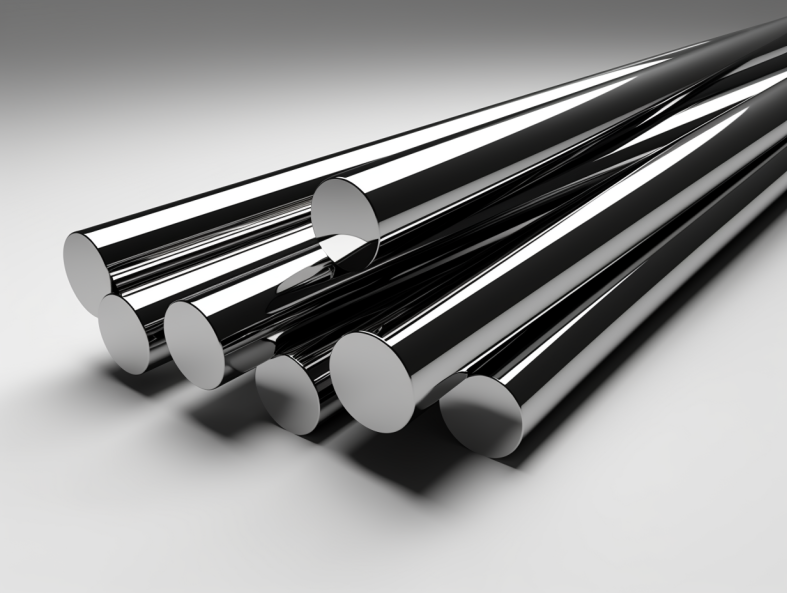
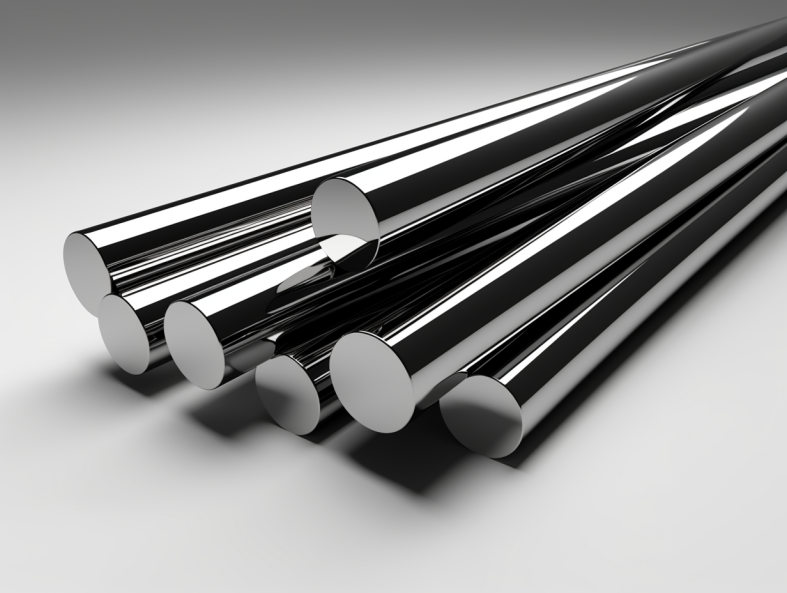
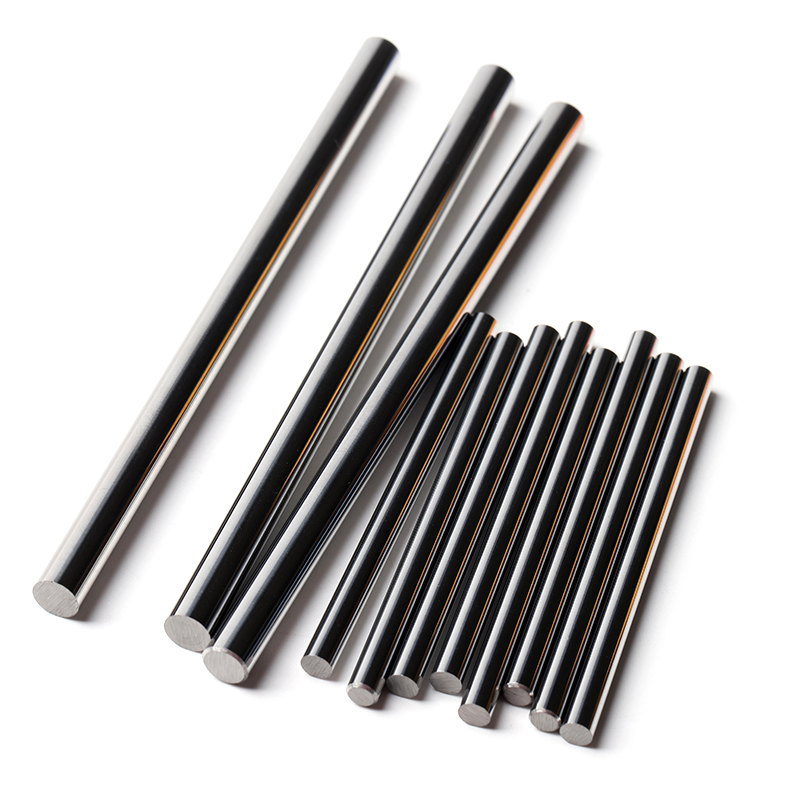
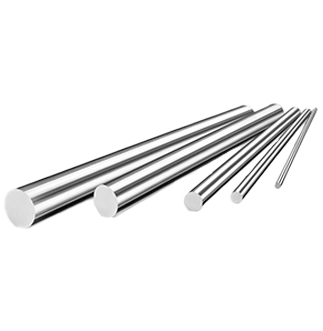
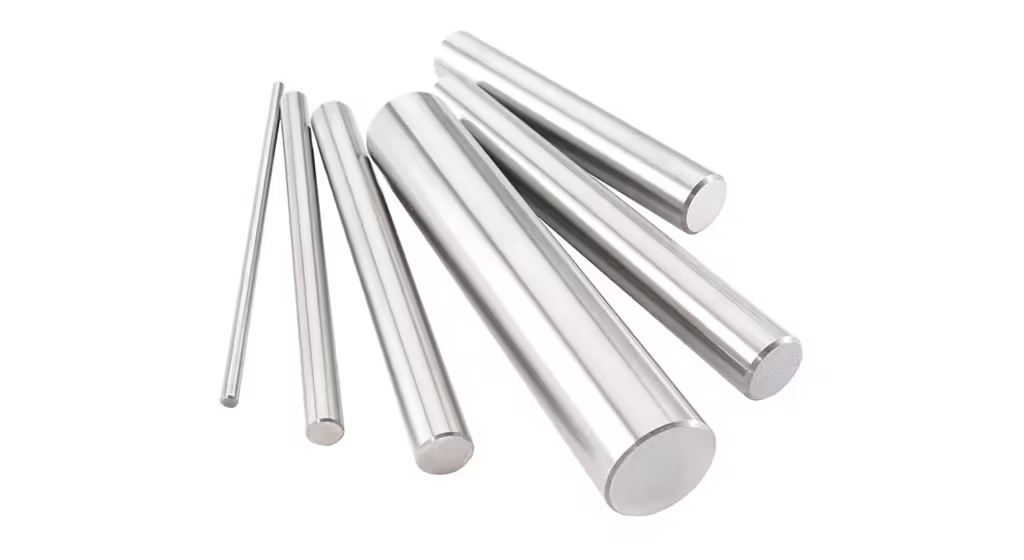
Composition and Characteristics
The composition of tungsten carbide blanks significantly influences their properties and performance. Here’s a detailed look at the typical composition and characteristics:
Component | Percentage | Characteristic |
---|---|---|
Tungsten Carbide (WC) | 85-95% | Provides hardness and wear resistance. |
Cobalt (Co) | 5-15% | Acts as a binder, offering toughness and strength. |
Titanium Carbide (TiC) | 0-5% | Enhances hardness and corrosion resistance. |
Tantalum Carbide (TaC) | 0-5% | Improves high-temperature stability and wear resistance. |
Niobium Carbide (NbC) | 0-5% | Increases toughness and thermal stability. |
Hardness, Strength, and Wear Resistance
Comparing the hardness, strength, and wear resistance of different tungsten carbide grades can help in selecting the right material for your application:
Grade | Hardness (HRA) | Transverse Rupture Strength (MPa) | Wear Resistance |
---|---|---|---|
K10 | 89 | 2200 | High |
K20 | 88 | 2400 | Moderate |
K30 | 87 | 2600 | Very High |
P10 | 91 | 2000 | High |
P20 | 90 | 2200 | Moderate |
P30 | 89 | 2400 | High |
C1 | 86 | 2800 | Moderate |
C2 | 85 | 3000 | Moderate |
C3 | 90 | 2400 | High |
C4 | 92 | 2200 | Very High |
Specifications, Sizes, Shapes, and Standards
When selecting tungsten carbide blanks, it’s essential to consider their specifications, sizes, shapes, and standards:
Specification | Detail |
---|---|
Sizes | Available in a wide range from small inserts to large blocks. |
Shapes | Cylindrical, rectangular, square, and custom shapes. |
Standards | ISO, ANSI, DIN, and JIS standards. |
Surface Finish | Ground, unground, polished, and rough. |
Tolerances | Tight tolerances for precision applications. |
Suppliers and Pricing Details
Finding reliable suppliers for tungsten carbide blanks is crucial. Here’s a comparison of some reputable suppliers and their pricing details:
Supplier | Location | Pricing (per kg) | Minimum Order Quantity (MOQ) |
---|---|---|---|
ABC Carbide | USA | $120 | 10 kg |
XYZ Metals | Germany | $110 | 20 kg |
Carbide Pro | China | $90 | 30 kg |
Global Tungsten | Japan | $130 | 5 kg |
Premier Carbide | Canada | $115 | 15 kg |
Selecting the Right Tungsten Carbide Blanks
Choosing the right tungsten carbide blanks involves several factors. Here’s a guide to help you make an informed decision:
Factor | Consideration |
---|---|
Application | Match the grade to the specific application needs. |
Material Properties | Consider hardness, toughness, and wear resistance. |
Supplier Reliability | Check supplier reputation, quality standards, and certifications. |
Cost | Balance cost against performance and longevity. |
Customization | Look for suppliers offering custom shapes and sizes. |
Advantages and Limitations of Tungsten Carbide Blanks
Understanding the advantages and limitations of tungsten carbide blanks can guide your selection process:
Advantages | Limitations |
---|---|
High Hardness | Can be brittle under high impact. |
Excellent Wear Resistance | May be costlier than other materials. |
Thermal Stability | Requires precise machining due to hardness. |
Corrosion Resistance | Limited flexibility in applications needing high ductility. |
Long Lifespan | Heavier compared to some alternative materials. |
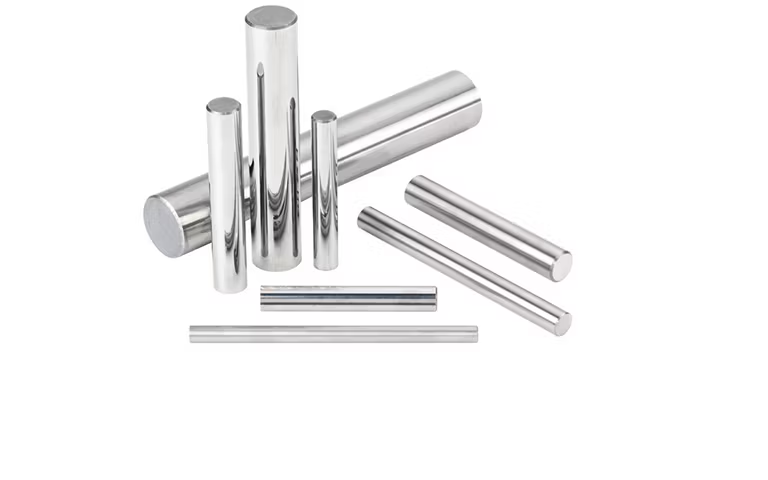
FAQ
Here’s a detailed FAQ section to address common queries regarding tungsten carbide blanks:
Question | Answer |
---|---|
What are tungsten carbide blanks? | Tungsten carbide blanks are raw materials used to produce cutting tools, wear parts, and other industrial components. They are known for their hardness, wear resistance, and toughness. |
How are tungsten carbide blanks made? | They are made by blending tungsten carbide powder with a binder, such as cobalt, and then sintering the mixture at high temperatures. |
What applications use tungsten carbide blanks? | They are used in machining, mining, aerospace, automotive, oil and gas, and electronics industries. |
What are the benefits of using tungsten carbide blanks? | Benefits include high hardness, excellent wear resistance, thermal stability, and a long lifespan. |
How do I choose the right grade of tungsten carbide blanks? | Consider the application requirements, such as the need for hardness, toughness, wear resistance, and thermal stability. |
Are tungsten carbide blanks expensive? | They can be more expensive than other materials, but their durability and performance often justify the cost. |
Can tungsten carbide blanks be customized? | Yes, many suppliers offer customization in shapes, sizes, and grades to meet specific application needs. |
Conclusion
Choosing the right tungsten carbide blanks supplier is a crucial step in ensuring the performance and longevity of your industrial tools and components. By understanding the types, applications, properties, and selection criteria, you can make an informed decision that best suits your needs.