Overview of Trigon Carbide Inserts
Trigon carbide inserts are essential tools in the machining industry, prized for their durability, efficiency, and precision. These inserts are used in a variety of cutting and shaping applications, primarily in metalworking. Their unique triangular shape allows for multiple cutting edges, which can be indexed as they wear out, maximizing their lifespan. But what makes trigon carbide inserts stand out? Let’s dive into the details.
Types of Trigon Carbide Inserts
Understanding the different types of trigon carbide inserts is crucial for selecting the right one for your application. Here’s a table summarizing the key types:
Type | Description |
---|---|
TNMG | General-purpose inserts with a 60° triangular shape and negative rake angles, offering excellent strength and versatility. |
TPMG | Positive rake angle inserts designed for precision machining, providing a smoother cut and better chip control. |
TCMT | Positive rake angle inserts with a 7° clearance angle, ideal for finishing applications. |
WNGP | High-feed inserts with a wiper edge for improved surface finish at high feed rates. |
TNGG | High-precision inserts for fine finishing and semi-finishing operations. |
TPGH | Inserts with a sharp cutting edge for light and medium cutting operations. |
TNGX | High-performance inserts with optimized geometry for heavy-duty cutting. |
TNMM | Negative rake inserts designed for roughing operations, offering maximum strength. |
TPMR | Positive rake inserts for reducing cutting forces and enhancing surface finish. |
WCMX | Versatile inserts suitable for both roughing and finishing applications. |
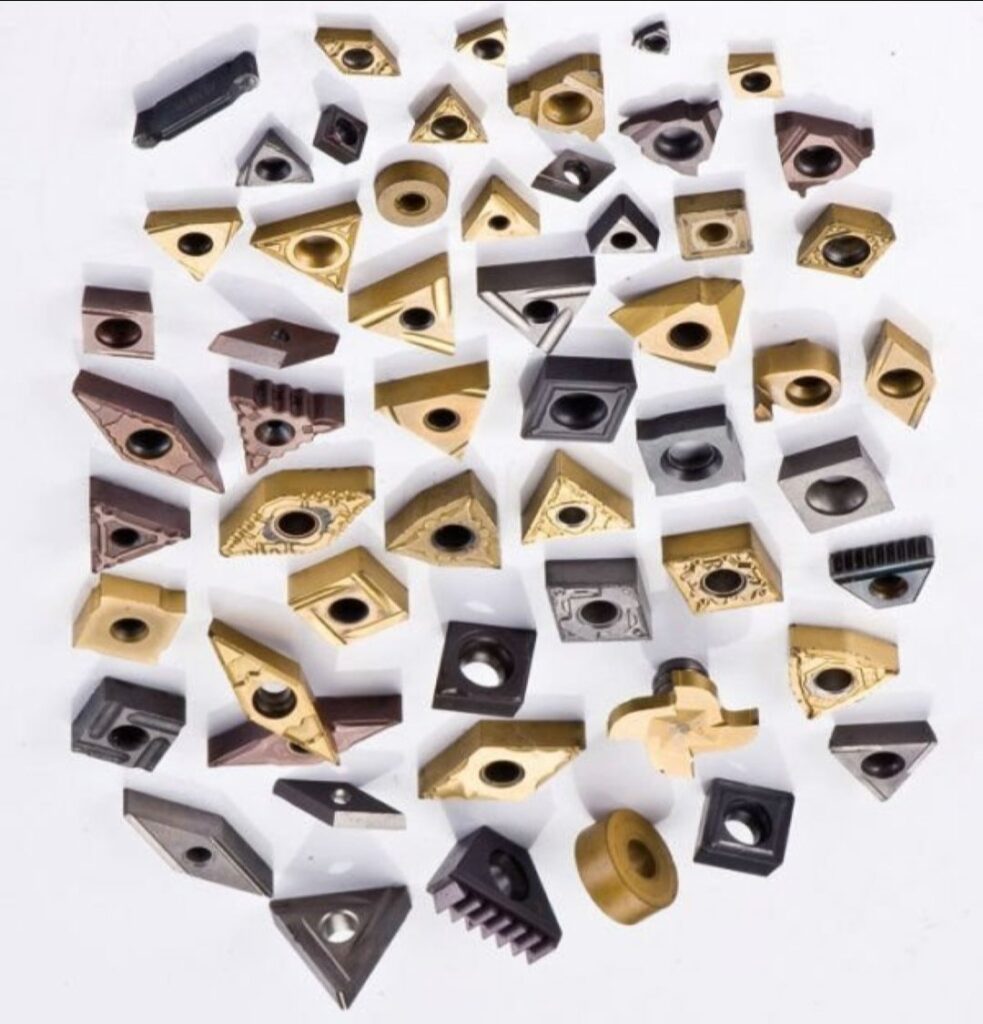
Applications of Trigon Carbide Inserts
Trigon carbide inserts are versatile and find applications in various industries. Here’s a detailed table outlining their uses:
Industry | Application |
---|---|
Automotive | Machining engine components, brake parts, and transmission components. |
Aerospace | Cutting and shaping high-strength alloys and composite materials. |
Oil & Gas | Drilling, reaming, and boring operations in harsh environments. |
Medical | Precision machining of surgical instruments and implants. |
Heavy Machinery | Fabrication of large parts and components for industrial machinery. |
Tool & Die | Mold and die manufacturing with high precision and finish. |
Metal Fabrication | General cutting, shaping, and finishing of metal parts. |
Electronics | Machining of small, intricate components for electronic devices. |
Material Properties of Trigon Carbide Inserts
To understand why trigon carbide inserts are so effective, it’s important to look at their material properties. Here’s a table summarizing key properties:
Property | Value |
---|---|
Hardness | 1600-2200 HV (Vickers Hardness) |
Toughness | High, capable of withstanding impact and shock loads. |
Wear Resistance | Excellent, due to the presence of hard carbide particles. |
Thermal Stability | High, maintains performance at elevated temperatures. |
Chemical Resistance | Resistant to corrosion and chemical attack. |
Composition and Characteristics of Trigon Carbide Inserts
The composition of trigon carbide inserts largely determines their performance characteristics. Here’s a detailed table:
Component | Function | Characteristics |
---|---|---|
Tungsten Carbide (WC) | Provides hardness and wear resistance. | Very hard, retains sharpness. |
Cobalt (Co) | Acts as a binder, providing toughness. | Increases toughness and impact resistance. |
Titanium Carbide (TiC) | Enhances wear resistance and thermal stability. | Improves performance at high temperatures. |
Tantalum Carbide (TaC) | Adds strength and hardness. | Further improves hardness and wear resistance. |
Niobium Carbide (NbC) | Enhances resistance to deformation. | Improves thermal stability and wear resistance. |
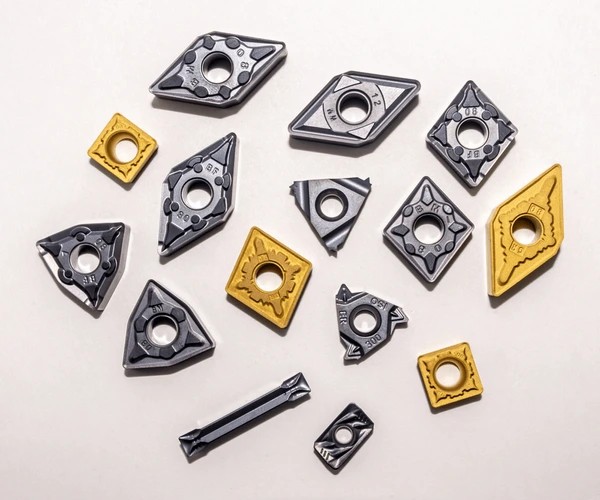
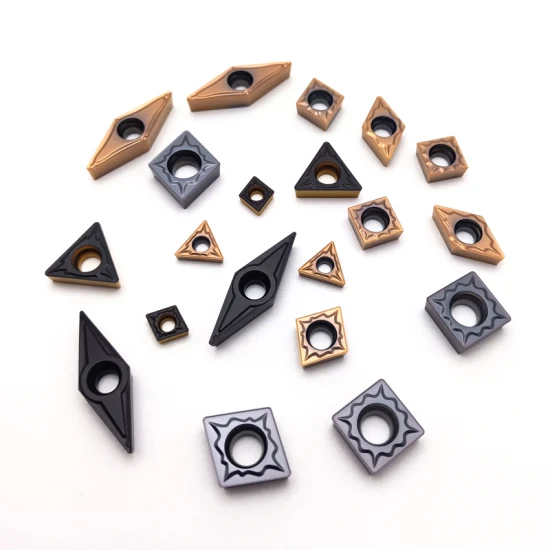
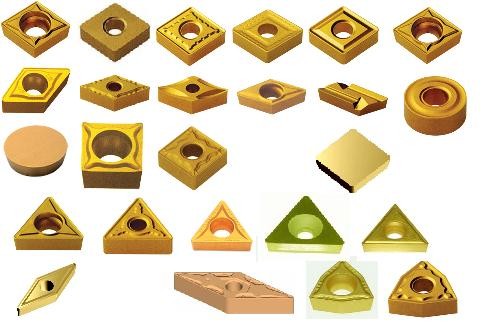
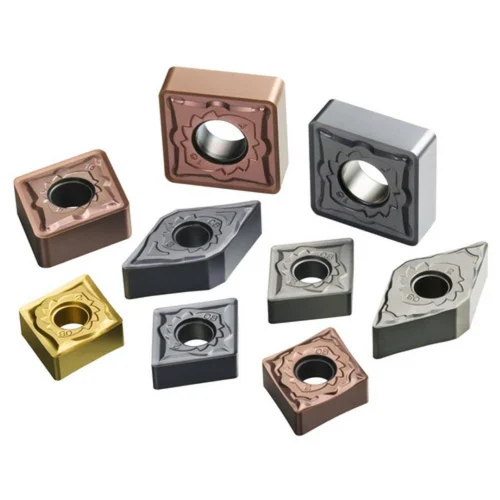
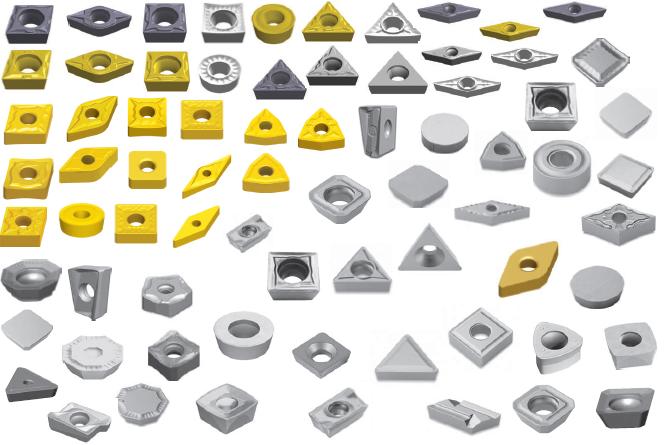
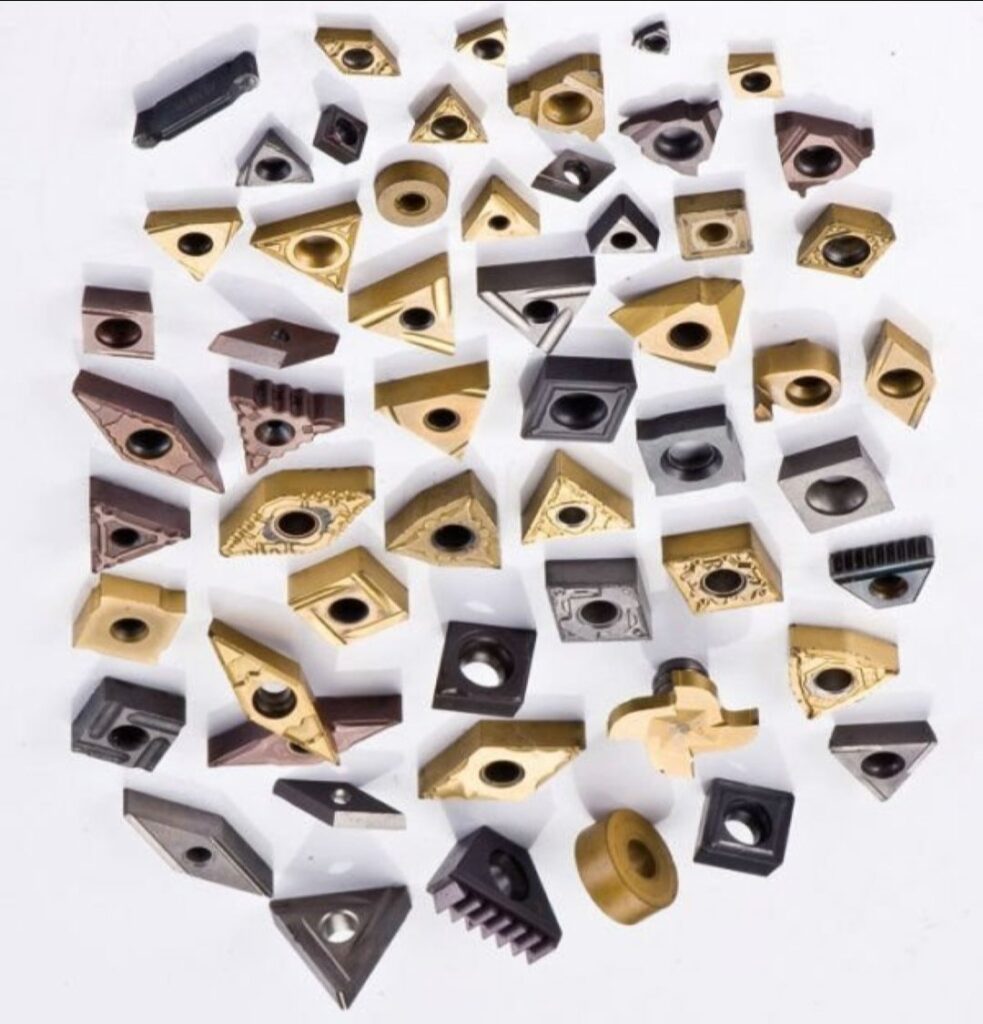
Hardness, Strength, and Wear Resistance of Trigon Carbide Inserts
These are crucial factors to consider when selecting inserts for different applications. Here’s a comparative table:
Type | Hardness (HV) | Strength (MPa) | Wear Resistance |
---|---|---|---|
TNMG | 1800 | 2800 | High |
TPMG | 1900 | 2700 | Very High |
TCMT | 1700 | 2500 | High |
WNGP | 2000 | 3000 | Very High |
TNGG | 2100 | 2900 | Excellent |
TPGH | 1600 | 2400 | High |
TNGX | 2200 | 3100 | Exceptional |
TNMM | 1800 | 2800 | High |
TPMR | 1900 | 2700 | Very High |
WCMX | 2000 | 3000 | Very High |
Specifications, Sizes, Shapes, and Standards of Trigon Carbide Inserts
When choosing trigon carbide inserts, it’s essential to consider their specifications, sizes, shapes, and compliance with industry standards. Here’s a detailed table:
Specification | Description |
---|---|
ISO Standard | ISO 1832:2017 specifies the designation system for indexable inserts. |
Size | Available in sizes ranging from small (IC 5mm) to large (IC 25mm). |
Shape | Triangular with various angles and edge preparations. |
Thickness | Typically ranges from 3mm to 5mm. |
Corner Radius | Options include sharp corners to rounded radii (0.2mm to 1.2mm). |
Coating | Various coatings like TiN, TiCN, Al2O3 for enhanced performance. |
Suppliers and Pricing Details of Trigon Carbide Inserts
Knowing where to source trigon carbide inserts and understanding their pricing is crucial for procurement. Here’s a table of prominent suppliers and their pricing details:
Supplier | Model | Price (per insert) | Bulk Pricing |
---|---|---|---|
Sandvik Coromant | TNMG 160408-PM | $10.00 | $8.50 (100+ units) |
Kennametal | TPMG 160404 | $12.00 | $10.20 (100+ units) |
Mitsubishi Materials | TCMT 16T308 | $11.00 | $9.30 (100+ units) |
ISCAR | WNGP 080404 | $13.50 | $11.70 (100+ units) |
Seco Tools | TNGG 160402L | $14.00 | $12.00 (100+ units) |
Walter AG | TPGH 090204 | $9.50 | $8.00 (100+ units) |
Kyocera | TNGX 120408 | $15.00 | $13.00 (100+ units) |
Sumitomo Electric | TNMM 160412 | $10.50 | $9.00 (100+ units) |
Tungaloy | TPMR 110304 | $11.50 | $9.80 (100+ units) |
Korloy | WCMX 030208 | $12.50 | $10.50 (100+ units) |
How to Select the Right Trigon Carbide Inserts
Choosing the right trigon carbide insert involves considering several factors, including the material to be machined, the type of operation, and the desired surface finish. Here’s a guide to help you make the right choice:
Factor | Considerations | Recommended Type |
---|---|---|
Material | Steel, Stainless Steel, Cast Iron, Non-Ferrous Metals | TNMG, TPMG, TCMT |
Operation Type | Roughing, Finishing, Semi-Finishing | TNMG (Roughing), TNGG (Finishing), TNGX (Semi-Finishing) |
Surface Finish | High, Medium, Low | WNGP (High), TPMR (Medium), TPGH (Low) |
Cutting Speed | High, Medium, Low | WNGP (High), TNMG (Medium), TCMT (Low) |
Feed Rate | High, Medium, Low | WNGP (High), TPMR (Medium), TPGH (Low) |
Depth of Cut | Deep, Medium, Shallow | TNMG (Deep), TNMM (Medium), TCMT (Shallow) |
Advantages and Limitations of Trigon Carbide Inserts
Each type of trigon carbide insert has its own set of advantages and limitations. Here’s a comparative analysis:
Type | Advantages | Limitations |
---|---|---|
TNMG | Strong, versatile, multiple edges. | Higher cutting forces, may require more power. |
TPMG | Smooth cutting, good chip control. | Less suitable for roughing. |
TCMT | Excellent for finishing, sharp edges. | Not ideal for heavy cuts. |
WNGP | High feed rates, good surface finish. | Higher cost. |
TNGG | High precision, excellent finish. | Limited to light cutting. |
TPGH | Sharp cutting edge, low cutting forces. | Less durable. |
TNGX | High performance, durable. | Higher cost. |
TNMM | Strong, ideal for roughing. | Less precise. |
TPMR | Reduced cutting forces, better finish. | Not for heavy-duty applications. |
WCMX | Versatile, suitable for roughing and finishing. | Moderate performance in both areas. |
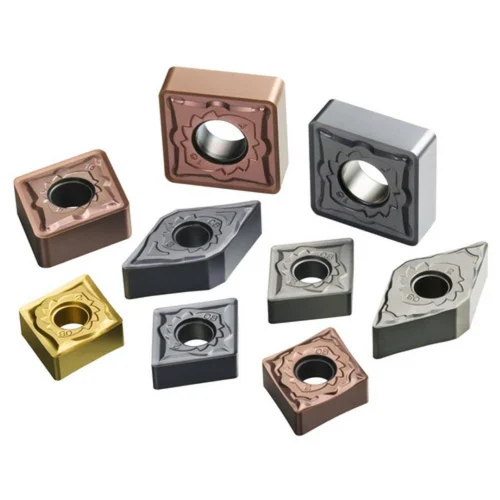
FAQs
To address common questions and provide additional insights, here’s an FAQ section:
Question | Answer |
---|---|
What are trigon carbide inserts used for? | Trigon carbide inserts are used for cutting, shaping, and finishing metal parts in various industries like automotive, aerospace, and medical. |
How do I choose the right trigon carbide insert? | Consider the material, operation type, surface finish, cutting speed, feed rate, and depth of cut. Refer to the selection guide provided. |
What are the benefits of using trigon carbide inserts? | They offer multiple cutting edges, high durability, excellent wear resistance, and can handle a variety of materials and applications. |
Can trigon carbide inserts be used for both roughing and finishing? | Yes, certain types like WCMX are versatile and suitable for both roughing and finishing. |
How do I maximize the lifespan of my carbide inserts? | Use the right insert for the material and operation, maintain proper cutting parameters, and ensure regular maintenance of your machining tools. |
Are coated carbide inserts better than uncoated ones? | Coated inserts often provide better performance, enhanced wear resistance, and longer lifespan, especially in high-speed and high-temperature applications. |
What is the typical lifespan of a trigon carbide insert? | Lifespan varies based on usage, material, and cutting conditions, but they generally last longer than other types of inserts due to their multiple cutting edges. |
How are trigon carbide inserts manufactured? | They are made from a mixture of carbide particles and a binder, typically cobalt, which is pressed into shape and sintered at high temperatures. |
Can trigon carbide inserts be recycled? | Yes, carbide inserts can be recycled, and many manufacturers offer recycling programs to reclaim valuable materials. |
What safety precautions should I take when using carbide inserts? | Always wear appropriate personal protective equipment, follow the manufacturer’s guidelines, and ensure your machining equipment is properly maintained and set up. |
Conclusion
Trigon carbide inserts are an indispensable tool in modern machining, offering unparalleled performance, durability, and versatility. By understanding the different types, applications, and material properties, you can make an informed decision and choose the right inserts for your specific needs. Whether you’re working in automotive, aerospace, or any other industry, trigon carbide inserts can help you achieve precision and efficiency in your machining operations. Remember, the key to maximizing their potential lies in selecting the appropriate type for your application and maintaining proper cutting parameters