Imagine you’re a sculptor, meticulously shaping a piece of granite. But instead of a hammer and chisel, you wield a high-powered lathe or milling machine. That’s where triangle carbide inserts come in – the sharp, unrelenting tools that transform raw metal into precise components.
The Material Used to Make Triangle Carbide Inserts
These inserts are the champions of wear resistance. Unlike their high-speed steel counterparts that quickly dull, triangle carbide inserts boast a core of tungsten carbide, one of the hardest materials known to man. Here’s a deeper dive into the fascinating world of metal powders used to craft these inserts:
Common Metal Powders in Triangle Carbide Inserts
Metal Powder | Description | Properties |
---|---|---|
Tungsten Carbide (WC) | The foundation, providing exceptional hardness and wear resistance. | Accounts for 75-95% of the insert’s composition. Enables machining of tough materials like steel, cast iron, and nickel alloys. |
Cobalt (Co) | The binding agent, holding the tungsten carbide particles together. | Makes up 5-25% of the insert. Its content influences the insert’s toughness, hardness, and resistance to fracturing. |
Titanium Carbide (TiC) | A potential addition for enhanced properties. | Improves wear resistance and crater resistance, particularly beneficial for high-speed machining applications. Its presence can range from 0-20%. |
Tantalum Carbide (TaC) | Another potential addition for specific applications. | Offers superior heat resistance and crater resistance compared to TiC. Used sparingly due to its higher cost. |
Niobium Carbide (NbC) | A less common additive, offering properties similar to Tantalum Carbide. | May be used in specialized inserts for high-temperature environments. |
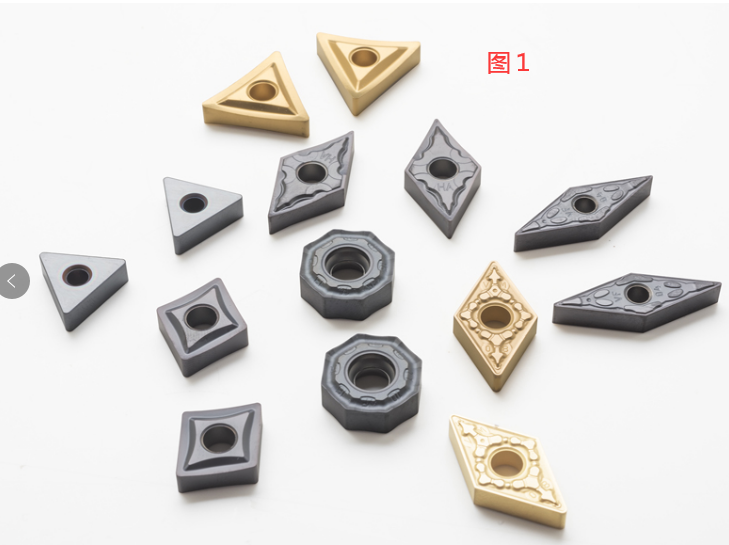
The Shape of Triangle Carbide Inserts
The triangular design isn’t just for aesthetics. It offers several advantages:
- Multiple Cutting Edges: Each corner of the triangle acts as a cutting edge, maximizing tool life. When one edge becomes dull, you can simply rotate the insert to expose a fresh cutting surface. This translates to fewer insert changes and reduced downtime.
- Chip Control: The triangular shape facilitates efficient chip formation and evacuation. This prevents chip buildup, which can lead to poor surface finish and potential tool damage.
- Strength and Stability: The three-sided geometry provides inherent stability during machining operations, particularly beneficial for roughing cuts and high-material removal rates.
Size of Triangle Carbide Inserts
Triangle carbide inserts come in a variety of sizes, measured by the inscribed circle diameter (ICD) – the largest circle that can fit within the triangle’s boundaries. Common sizes include:
- Small Inserts (ICD of 3mm – 8mm): Ideal for intricate details, finishing cuts, and applications with limited tool space.
- Medium Inserts (ICD of 9mm – 15mm): The sweet spot for a balance between cutting edge length and insert strength, suitable for a wide range of turning and milling operations.
- Large Inserts (ICD of 16mm and above): Designed for heavy-duty machining, roughing cuts, and applications requiring high material removal rates.
The Application of Triangle Carbide Inserts
Triangle carbide inserts are versatile performers, tackling various metal machining tasks. Here are some prominent applications:
Application | Description | Benefits of Triangle Carbide Inserts |
---|---|---|
Turning | Shaping cylindrical workpieces through rotational cutting. | Excellent for roughing, finishing, and contour turning of steel, cast iron, and other ferrous materials. |
Milling | Removing material using a rotating multi-tooth cutter. | Effective for face milling, peripheral milling, and slotting operations on various metals. |
Grooving and Threading | Creating grooves and threads on workpieces. | Precise and efficient for generating internal and external threads, as well as various groove profiles. |
Boring | Enlarging existing holes in workpieces. | Triangle carbide inserts enable accurate boring operations with minimal tool deflection. |
Beyond the Basics: Advanced Considerations for Triangle Carbide Inserts
While the core functions are straightforward, several factors influence the selection and performance of triangle carbide inserts:
- Insert Grade: This refers to the specific formulation of the metal powders used. Different grades offer varying combinations of hardness, toughness, and wear resistance, tailored to specific workpiece materials and machining conditions.
- Chipbreaker Geometry: The insert’s geometry plays a crucial role in chip control. Different chipbreaker designs are available to optimize chip formation for various materials and cutting depths.
- Coating: A thin layer of ceramic or other material applied to the insert’s surface can significantly enhance its performance. Common coatings include:
- Titanium Nitride (TiN): Improves wear resistance and crater resistance, particularly beneficial for high-speed machining.
- Titanium Aluminum Nitride (TiAlN): Offers a combination of wear resistance, heat resistance, and oxidation resistance, making it suitable for a wider range of applications.
- Chemical Vapor Deposition (CVD) Coatings: These advanced coatings provide superior performance compared to traditional PVD coatings, offering exceptional hardness, heat resistance, and tool life.
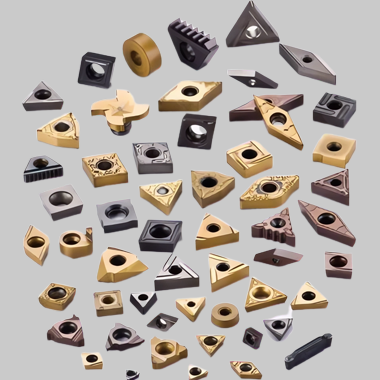
Specifications, Sizes, Grades, and Standards
Choosing the right triangle carbide insert requires careful consideration of several specifications:
- Insert Size (ICD): As discussed earlier, the inscribed circle diameter dictates the insert’s overall size and cutting edge length.
- Insert Thickness: This parameter influences chip formation and insert rigidity. Thicker inserts offer better stability for heavy-duty machining, while thinner inserts may be preferred for finishing applications.
- Insert Geometry: Beyond the basic triangular shape, there are variations in corner radius, rake angle, and clearance angle. These geometric features impact chip formation, cutting forces, and surface finish.
- Insert Grade: A standardized coding system (e.g., ISO standard) designates the insert’s grade based on its composition and properties. Understanding the grade code is essential for selecting the appropriate insert for the material being machined.
Here’s a table summarizing some common insert size designations and corresponding applications:
Inscribed Circle Diameter (ICD) | Insert Thickness | Typical Applications |
---|---|---|
3mm – 8mm | 1mm – 3.5mm | Finishing cuts, small workpieces, intricate details |
9mm – 15mm | 2mm – 5mm | General-purpose turning and milling, balancing cutting edge length and strength |
16mm and above | 4mm – 8mm | Roughing cuts, heavy-duty machining, high material removal rates |
Suppliers and Pricing
Triangle carbide inserts are readily available from a wide range of cutting tool manufacturers and industrial supply companies. Here are some prominent suppliers:
- Kennametal
- Sandvik Coromant
- Seco Tools
- Iscar
- Sumitomo
Pricing varies depending on the insert size, grade, coating, and overall quality. For example, a basic uncoated insert might cost around $5, while an advanced CVD-coated insert for high-performance applications could range from $20 to $50 or more.
Pros and Cons of Triangle Carbide Inserts
Advantages:
- Exceptional Wear Resistance: Triangle carbide inserts offer significantly longer tool life compared to high-speed steel inserts, minimizing downtime and reducing tooling costs in the long run.
- Versatility: They can handle a wide range of machining operations and materials, making them a valuable asset for any machine shop.
- Predictable Performance: The consistent hardness and wear characteristics of carbide ensure predictable tool life and consistent machining results.
- Multiple Cutting Edges: With multiple usable edges per insert, users can maximize tool life by simply rotating the insert when one edge becomes dull.
Limitations:
- Higher Initial Cost: Compared to high-speed steel inserts, triangle carbide inserts have a higher upfront cost. However, their extended tool life often translates to lower overall machining costs.
- Brittleness: While exceptionally hard, carbide can be brittle. Improper handling or excessive machining forces can lead to insert chipping or breakage.
- Heat Sensitivity: At extremely high temperatures, carbide inserts can lose some of their hardness and strength. Careful selection of cutting speeds and feeds is crucial for optimal performance.
Making an Informed Choice: Selecting the Right Triangle Carbide Insert
Given the various factors at play, choosing the optimal triangle carbide insert requires careful consideration of the specific machining application. Here are some key questions to ask yourself:
- What material are you machining? Different materials require inserts with varying degrees of hardness, toughness, and wear resistance.
- What type of machining operation are you performing? Turning, milling, and other operations have distinct cutting forces and require inserts with appropriate geometry.
- What level of surface finish is required? Finishing cuts may necessitate inserts with sharper cutting edges and smoother coatings.
- What is your budget? While advanced inserts offer superior performance, they come at a higher cost. Consider the balance between upfront cost and long-term cost savings.
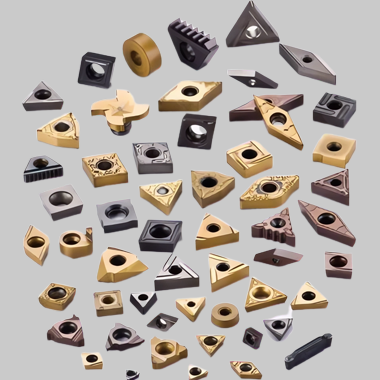
FAQ
Question | Answer |
---|---|
What are the benefits of using triangle carbide inserts over high-speed steel inserts? | Triangle carbide inserts offer significantly longer tool life, better wear resistance, and the ability to handle a wider range of materials. This translates to less downtime for tool changes, reduced overall machining costs, and the ability to achieve higher productivity. |
How do I identify the right insert size for my application? | The inscribed circle diameter (ICD) is the primary indicator of insert size. Consult your machine tool specifications and the recommendations from the insert manufacturer to determine the appropriate ICD for your application. Consider factors like the size of the workpiece, the depth of cut, and the desired level of rigidity. |
What are some tips for maximizing the life of triangle carbide inserts? | Proper handling: Avoid dropping or mishandling inserts, as they can chip or break. Use the correct coolant: Use a coolant appropriate for the material being machined to maintain optimal cutting temperatures and minimize insert wear. Select the right cutting speed and feed: Following the manufacturer’s recommendations for cutting speeds and feeds will help prevent excessive heat generation and ensure optimal insert performance. Chip control: Ensure proper chip formation and evacuation to avoid chip buildup, which can damage the insert and the workpiece. |
Can I re-sharpen triangle carbide inserts? | While not a common practice, some manufacturers offer reconditioning services for certain types of triangle carbide inserts. However, due to the precise geometry and coatings involved, re-sharpening may not always be a cost-effective option. In most cases, replacing the insert with a new one is the preferred approach. |
What are some emerging trends in triangle carbide insert technology? | The future of triangle carbide inserts is likely to see advancements in several areas: Advanced Materials: Research and development efforts are ongoing to develop even harder and more wear-resistant carbide grades for tackling even more challenging materials. Nanotechnology: The incorporation of nanoparticles into the carbide matrix has the potential to further enhance wear resistance and cutting performance. Intelligent Inserts: Sensor-embedded inserts that can monitor cutting parameters and provide real-time feedback to optimize machining processes are a potential future development. |
Conclusion
Triangle carbide inserts have become a cornerstone of modern metal machining. Their exceptional wear resistance, versatility, and predictable performance make them a valuable asset for any machine shop. By understanding the different insert characteristics, selecting the right insert for the job, and following proper handling and machining practices, users can maximize the benefits of these remarkable tools and achieve superior machining results.