When it comes to machining and tooling, precision is everything. One of the most critical components that machinists rely on are carbide inserts. In particular, triangle carbide inserts are widely used due to their versatility and efficiency. If you’re looking to deepen your knowledge about these tools, you’ve come to the right place. This comprehensive guide will delve into everything you need to know about triangle carbide insert sizes, including detailed descriptions of specific metal powder models, their applications, material properties, and much more.
Overview of Triangle Carbide Insert Sizes
Triangle carbide inserts are triangular-shaped cutting tools typically used in milling and turning operations. Their shape allows for multiple cutting edges, providing increased efficiency and longevity. The choice of insert size and type depends on the specific requirements of the machining operation, such as the material being machined and the desired finish.
Key Characteristics of Triangle Carbide Inserts
- Versatility: Suitable for various machining operations.
- Durability: Made from tough carbide materials that withstand high temperatures and wear.
- Efficiency: Multiple cutting edges reduce the need for frequent tool changes.
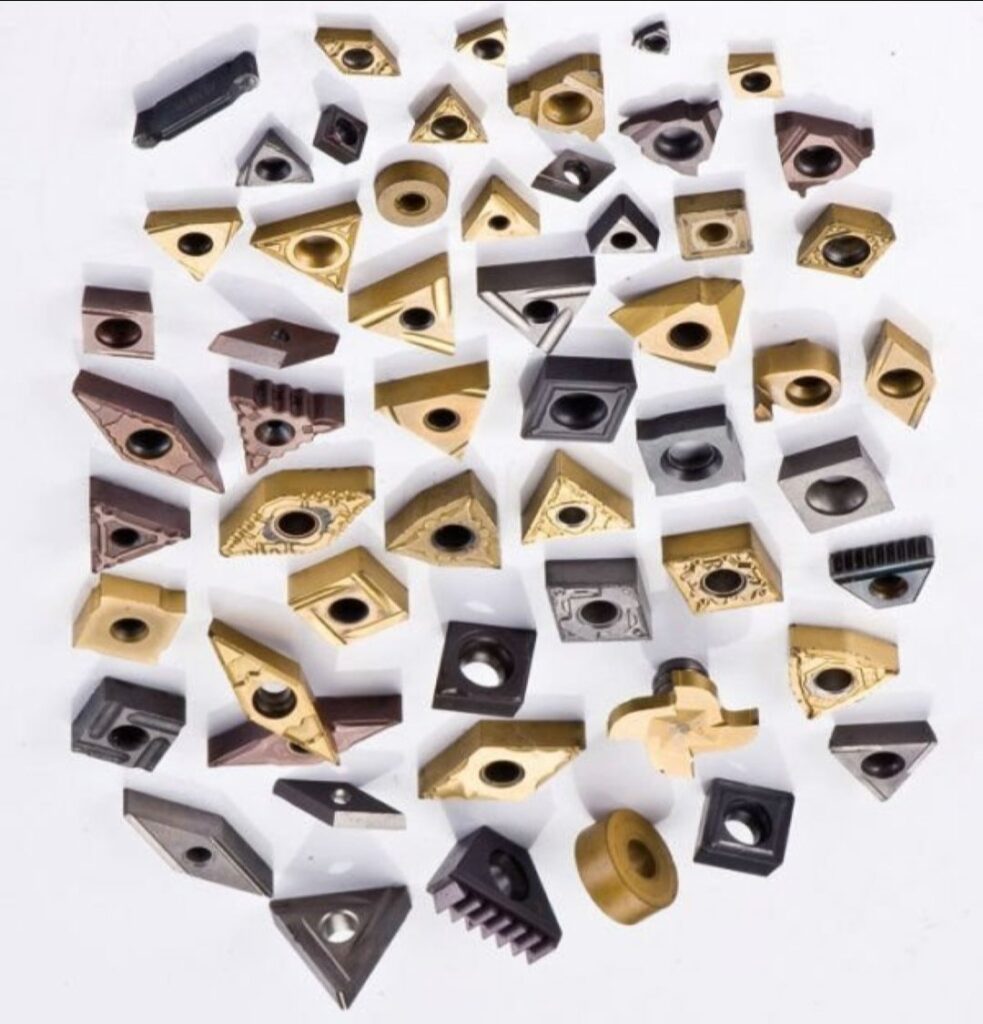
Triangle Carbide Insert Sizes and Types
Triangle carbide inserts come in various sizes and types, each tailored to specific applications. Here, we list and describe some of the most common models:
Model | Size (mm) | Application | Characteristics |
---|---|---|---|
TNMG 160404 | 16x04x04 | General turning | High wear resistance, suitable for steel and cast iron |
TCGT 110302 | 11x03x02 | Finishing operations | Sharp cutting edge, excellent surface finish |
TPMR 090304 | 09x03x04 | Precision machining | High precision, minimal vibration |
TNMG 220408 | 22x04x08 | Heavy-duty turning | Robust, ideal for interrupted cuts |
TPGH 160304 | 16x03x04 | Aluminum machining | Polished surface, reduces built-up edge |
TNMA 160408 | 16x04x08 | Roughing operations | High toughness, suitable for roughing |
TCMT 090204 | 09x02x04 | Light machining | Versatile, good for light to medium-duty |
TPGT 110302 | 11x03x02 | Finishing | Precision finishing, sharp cutting edge |
TNMG 331 | 3/8″ IC | Heavy cutting | High durability, excellent for heavy-duty machining |
TPMT 160304 | 16x03x04 | Semi-finishing | Balanced performance for semi-finishing |
Applications of Triangle Carbide Insert Sizes
Triangle carbide inserts are designed for a wide range of applications. The table below highlights the primary uses of different sizes:
Application | Insert Size | Materials |
---|---|---|
General Turning | TNMG 160404 | Steel, Cast Iron |
Finishing | TCGT 110302 | Stainless Steel, Aluminum |
Precision Machining | TPMR 090304 | Hardened Steel |
Heavy-duty Turning | TNMG 220408 | Alloy Steel, High-Temperature Alloys |
Aluminum Machining | TPGH 160304 | Aluminum Alloys |
Roughing | TNMA 160408 | Cast Iron, Steel |
Light Machining | TCMT 090204 | Non-ferrous Metals |
Semi-finishing | TPMT 160304 | Various Alloys |
Material Properties of Triangle Carbide Inserts
The performance of triangle carbide inserts is largely determined by their material properties. The following table summarizes these properties:
Property | Description |
---|---|
Hardness | High hardness for wear resistance |
Toughness | Ability to withstand impact and avoid chipping |
Heat Resistance | Stability at high cutting temperatures |
Chemical Stability | Resistance to oxidation and chemical wear |
Thermal Conductivity | Efficient heat dissipation during cutting |
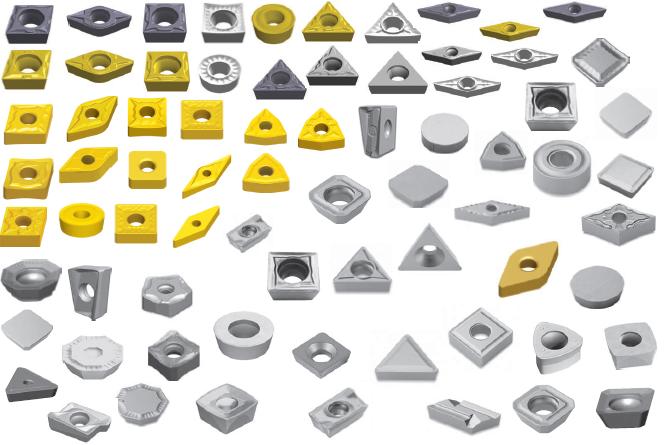
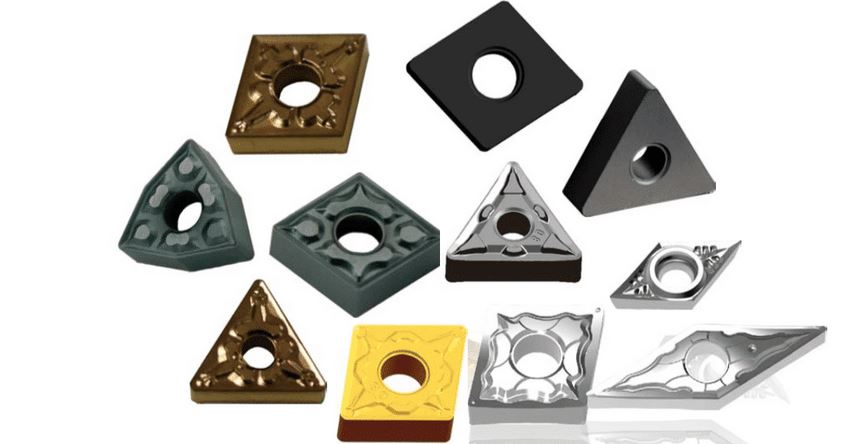
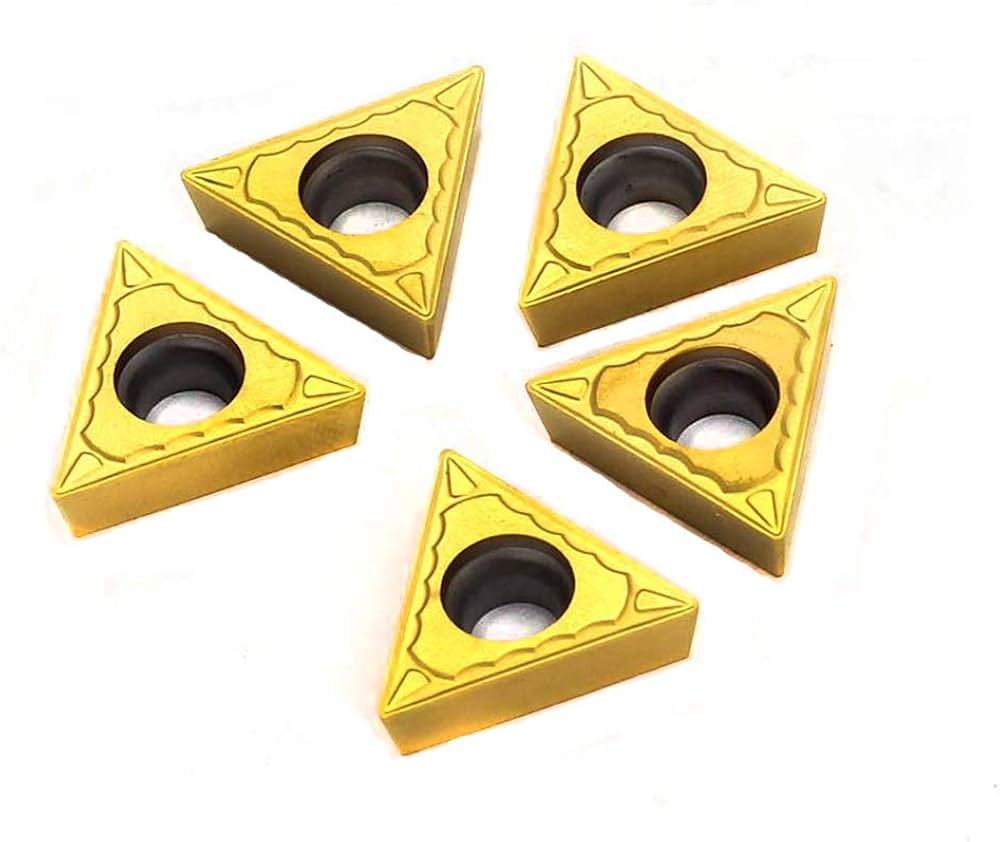
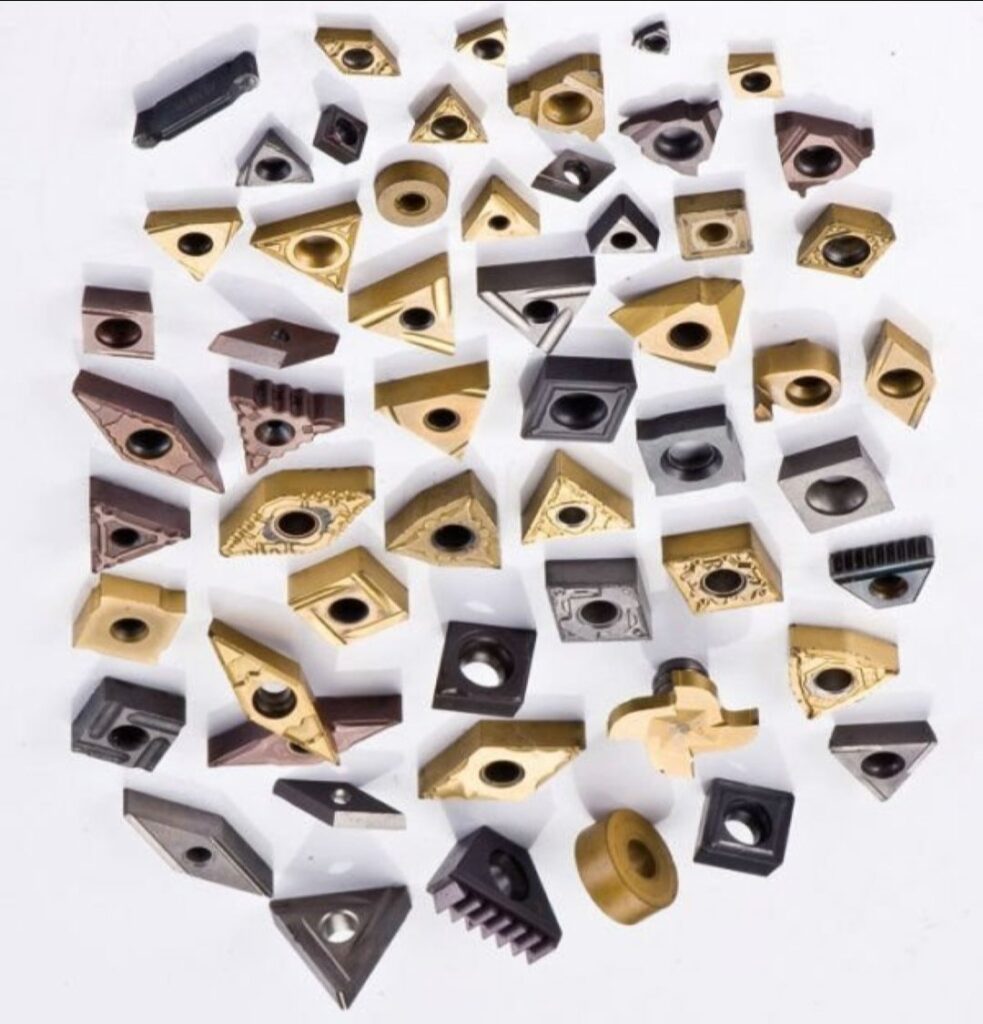
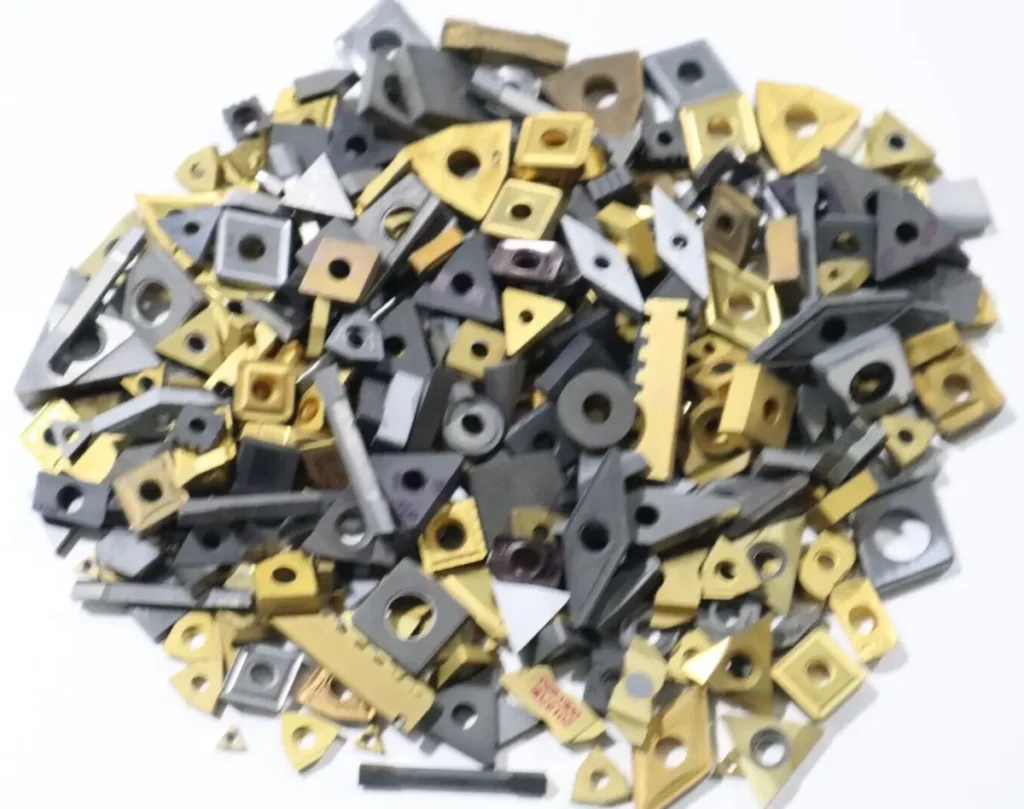
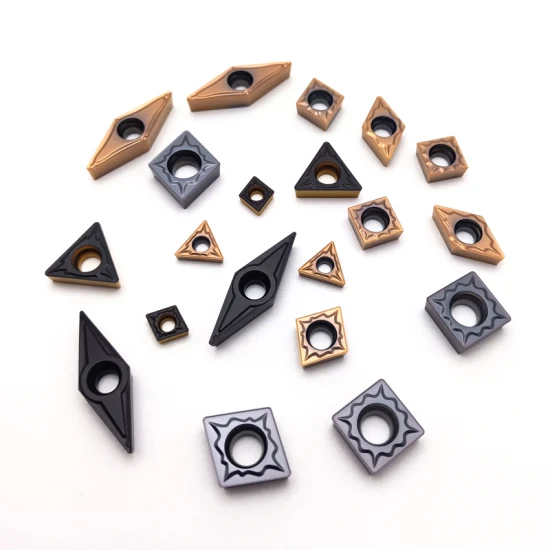
Composition and Characteristics
Carbide inserts are made from a composite material comprising a hard phase (carbides) and a binder metal (typically cobalt). This composition gives them their unique properties:
Component | Properties |
---|---|
Tungsten Carbide (WC) | High hardness, wear resistance |
Cobalt (Co) | Provides toughness and strength |
Titanium Carbide (TiC) | Improves heat resistance and chemical stability |
Tantalum Carbide (TaC) | Enhances toughness and thermal shock resistance |
Hardness, Strength, and Wear Resistance
Different carbide grades are used to achieve specific hardness, strength, and wear resistance levels. The table below compares these properties for common carbide grades:
Grade | Hardness (HRA) | Transverse Rupture Strength (MPa) | Wear Resistance |
---|---|---|---|
C2 | 89.5 | 2500 | High |
C3 | 91.0 | 2300 | Very High |
C4 | 92.5 | 2100 | Extreme |
C5 | 88.0 | 2800 | Medium |
C6 | 90.0 | 2600 | High |
Specifications and Standards
Carbide inserts adhere to specific standards and specifications to ensure compatibility and performance. Here’s a table detailing these aspects:
Standard | Specification | Details |
---|---|---|
ISO | ISO 1832 | International standard for carbide inserts |
ANSI | ANSI B212.4 | American standard for carbide insert shapes and sizes |
DIN | DIN 4987 | German standard for carbide inserts |
JIS | JIS B4125 | Japanese standard for carbide inserts |
Suppliers and Pricing
Understanding the market and sourcing from reliable suppliers is crucial. Here are some well-known suppliers and a general idea of pricing:
Supplier | Location | Price Range (per piece) |
---|---|---|
Sandvik Coromant | Global | $10 – $50 |
Kennametal | Global | $15 – $55 |
Mitsubishi Materials | Global | $12 – $45 |
ISCAR | Global | $20 – $60 |
Sumitomo Electric | Global | $18 – $52 |
Selecting the Right Triangle Carbide Insert Size
Choosing the right insert size involves considering several factors, such as the material being machined, the type of operation, and the desired finish. Here’s a guide to help you select the appropriate insert:
Factor | Consideration | Recommended Size |
---|---|---|
Material Hardness | Hard materials require tougher inserts | C2, C4 grades |
Type of Operation | Roughing vs. Finishing | TNMA for roughing, TCGT for finishing |
Desired Finish | Precision and surface quality | TPMR for precision, TPGH for smooth finishes |
Machine Power | High-power vs. low-power machines | Larger sizes for high power, smaller for low power |
Advantages and Limitations of Triangle Carbide Inserts
When selecting tools, it’s essential to weigh their pros and cons. Here’s a comparison of the advantages and limitations of triangle carbide inserts:
Aspect | Advantages | Limitations |
---|---|---|
Versatility | Suitable for various operations | May require frequent changes for specialized tasks |
Durability | High wear resistance | Expensive initial cost |
Efficiency | Multiple cutting edges | Requires precision setup |
Performance | Consistent high-quality finish | Limited to specific materials and operations |
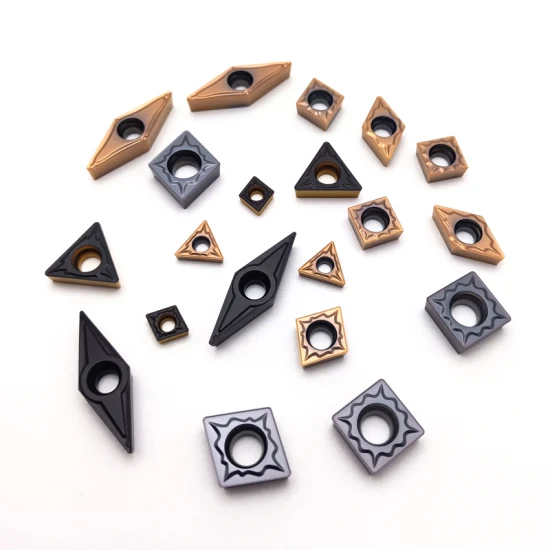
FAQ
Question | Answer |
---|---|
What are triangle carbide inserts used for? | They are used for turning, milling, and precision machining operations. |
Why are carbide inserts preferred? | Due to their high hardness, wear resistance, and ability to maintain a sharp edge. |
How do I choose the right carbide insert? | Consider the material, type of operation, and desired finish. Refer to the selection guide above. |
Are carbide inserts expensive? | They can be more expensive initially but offer longer life and better performance. |
What are the common standards for carbide inserts? | ISO, ANSI, DIN, and JIS standards. |
Conclusion
Understanding triangle carbide insert sizes is crucial for optimizing your machining operations. By selecting the right insert size and type, you can improve efficiency, reduce downtime, and achieve superior results. Whether you’re a seasoned machinist or a beginner, this guide provides the insights needed to make informed decisions about your tooling choices.