Overview of Tracker Carbide Inserts
When it comes to precision machining and manufacturing, tracker carbide inserts play a pivotal role. These tiny, yet incredibly robust components are essential in numerous industrial applications, from automotive to aerospace, thanks to their durability and efficiency. But what makes these inserts so special? Let’s dive into the world of tracker carbide inserts, exploring their types, applications, material properties, and much more.
Types of Tracker Carbide Inserts
Understanding the various types of tracker carbide inserts is crucial for selecting the right one for your specific needs. Here’s a detailed breakdown:
Insert Type | Description |
---|---|
Cemented Carbide | A mix of tungsten carbide with a binder metal, typically cobalt, offering excellent hardness. |
Cermet | Combines ceramic and metallic materials for high wear resistance and toughness. |
Coated Carbide | Features a thin coating of titanium carbide or aluminum oxide to enhance cutting performance. |
Ceramic | Made from alumina or silicon nitride, suitable for high-speed machining and hard materials. |
CBN (Cubic Boron Nitride) | Ideal for cutting hardened steels and superalloys, providing superior wear resistance. |
Diamond | Best for non-ferrous materials like aluminum and copper, offering unmatched hardness. |
PVD Coated | Physical Vapor Deposition coating for improved thermal and chemical stability. |
Uncoated Carbide | Plain tungsten carbide, excellent for non-ferrous metals and cast iron. |
Silicon Nitride | Perfect for heavy-duty applications requiring high toughness. |
TiCN Coated | Titanium carbonitride coating for enhanced toughness and wear resistance. |
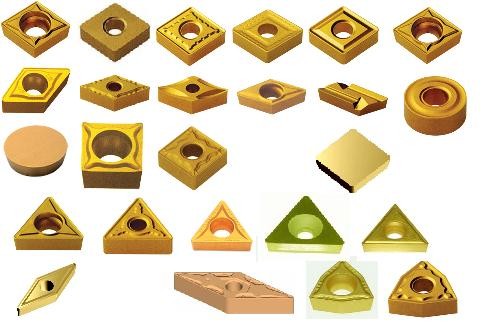
Applications of Tracker Carbide Inserts
The versatility of tracker carbide inserts makes them indispensable in various industries. Here’s how they are applied across different fields:
Industry | Application |
---|---|
Automotive | Engine and transmission components manufacturing. |
Aerospace | Machining of high-strength alloys used in aircraft structures. |
Medical | Production of precise medical instruments and implants. |
Oil & Gas | Drilling and exploration equipment manufacturing. |
Electronics | Precision machining of electronic components and devices. |
Construction | Tools and machinery components requiring high durability. |
Metalworking | General machining and finishing of metal parts. |
Mold & Die | Fabrication of molds and dies for various manufacturing processes. |
Mining | Cutting and drilling tools used in mining operations. |
Marine | Components for ships and offshore structures. |
Material Properties of Tracker Carbide Inserts
Understanding the material properties of tracker carbide inserts is key to selecting the right insert for your application:
Property | Description |
---|---|
Hardness | Measures the resistance to deformation and wear. |
Toughness | Ability to absorb energy and resist fracturing. |
Wear Resistance | Resistance to abrasive wear and erosion. |
Thermal Stability | Ability to retain properties at high temperatures. |
Chemical Resistance | Resistance to corrosion and chemical attacks. |
Thermal Conductivity | Capacity to conduct heat away from the cutting edge. |
Fracture Toughness | Resistance to crack propagation. |
Density | Mass per unit volume, influencing the insert’s strength and stability. |
Elastic Modulus | Measure of the material’s stiffness. |
Thermal Expansion | Rate at which the material expands when heated. |
Composition and Characteristics
Here’s a closer look at the composition, properties, and characteristics of different types of tracker carbide inserts:
Type | Composition | Properties | Characteristics |
---|---|---|---|
Cemented Carbide | WC-Co (Tungsten Carbide-Cobalt) | High hardness and toughness | Excellent for general-purpose machining |
Cermet | TiC + Ni/Co (Titanium Carbide + Nickel/Cobalt) | High wear resistance | Ideal for finishing applications |
Coated Carbide | TiC/Al2O3 (Titanium Carbide/Alumina) | Enhanced cutting performance | Suitable for high-speed machining |
Ceramic | Al2O3/Si3N4 (Alumina/Silicon Nitride) | High temperature resistance | Best for hard materials |
CBN | Cubic Boron Nitride | Superior wear resistance | Perfect for hardened steels |
Diamond | Pure Diamond | Unmatched hardness | Excellent for non-ferrous materials |
PVD Coated | Various metal nitrides or carbides | Improved thermal and chemical stability | Suitable for demanding conditions |
Uncoated Carbide | Pure Tungsten Carbide | Excellent toughness | Great for non-ferrous metals |
Silicon Nitride | Silicon Nitride | High toughness | Ideal for heavy-duty applications |
TiCN Coated | Titanium Carbonitride | Enhanced toughness and wear resistance | Versatile for various applications |
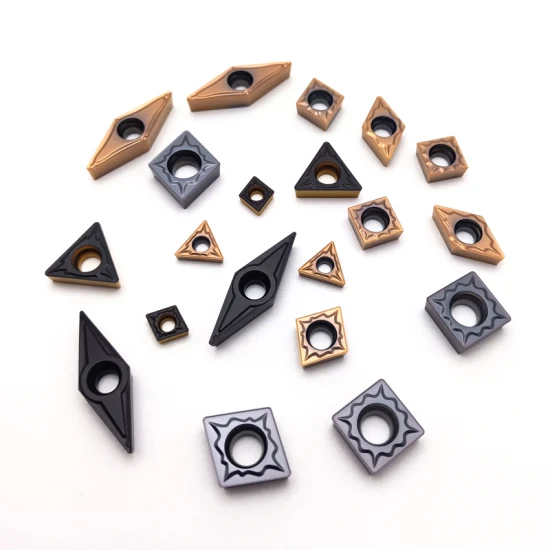
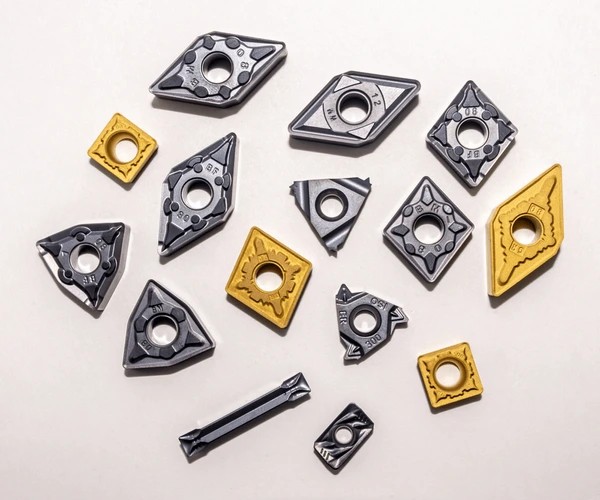
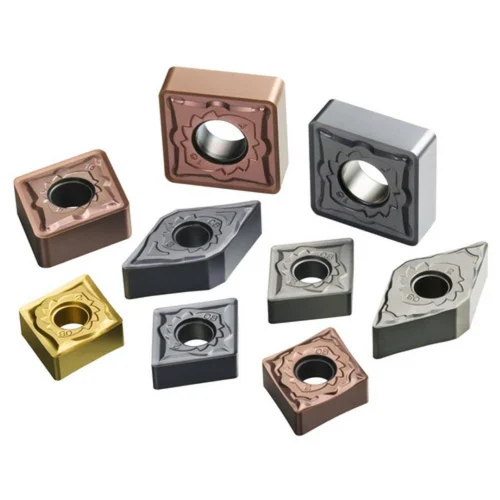
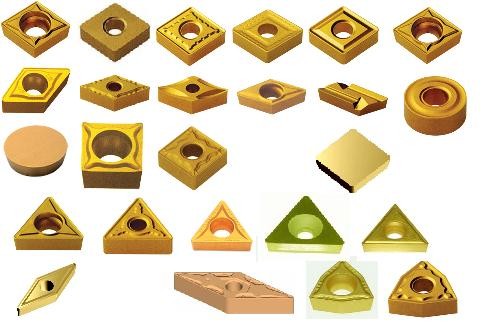
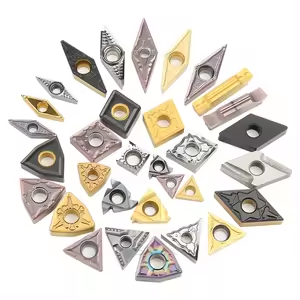
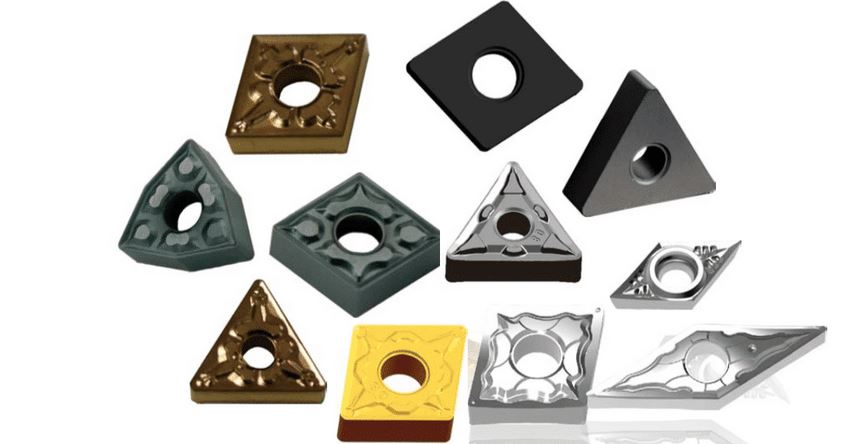
Hardness, Strength, and Wear Resistance
The hardness, strength, and wear resistance of tracker carbide inserts determine their suitability for different applications:
Insert Type | Hardness (HV) | Strength (MPa) | Wear Resistance |
---|---|---|---|
Cemented Carbide | 1500-2000 | 2000-3000 | High |
Cermet | 1700-2200 | 2200-3200 | Very High |
Coated Carbide | 1800-2300 | 2300-3300 | Extremely High |
Ceramic | 2000-2500 | 2500-3500 | High |
CBN | 3000-4000 | 3500-4500 | Extremely High |
Diamond | 5000-7000 | 4000-5000 | Unmatched |
PVD Coated | 2200-2700 | 2700-3700 | Very High |
Uncoated Carbide | 1600-2100 | 2100-3100 | High |
Silicon Nitride | 1800-2300 | 2800-3800 | Very High |
TiCN Coated | 1900-2400 | 2400-3400 | High |
Specifications, Sizes, Shape, Standards
Choosing the right tracker carbide insert involves considering its specifications, sizes, shapes, and compliance with industry standards:
Specification | Details |
---|---|
ISO Standards | ISO 513, ISO 1832, etc. |
Insert Shapes | Square, Triangle, Round, Diamond, Hexagon, etc. |
Sizes | Various, typically denoted by a combination of letters and numbers indicating dimensions. |
Coating Thickness | 1-10 micrometers depending on the application. |
Edge Preparation | Sharp, honed, chamfered, or rounded edges to suit different cutting requirements. |
Tolerance Class | H7, H8, etc., indicating the allowable deviation in dimensions. |
Compatibility | Designed to fit specific tool holders and machines, often indicated by the manufacturer. |
Cooling Methods | Dry, wet, or cryogenic cooling depending on the material and machining process. |
Application-specific Standards | ASTM, ANSI, DIN standards relevant to specific industrial applications. |
Suppliers and Pricing Details
Finding the right supplier for tracker carbide inserts is essential for ensuring quality and reliability:
Supplier | Country | Product Range | Pricing (USD) |
---|---|---|---|
Sandvik Coromant | Sweden | Full range of carbide inserts | $10 – $150 per insert |
Kennametal | USA | Wide variety of carbide and coated inserts | $15 – $200 per insert |
Mitsubishi Materials | Japan | High-performance cutting tools | $12 – $180 per insert |
Seco Tools | Sweden | Comprehensive range of inserts | $14 – $160 per insert |
Iscar | Israel | Innovative carbide solutions | $13 – $175 per insert |
Walter AG | Germany | High-quality precision tools | $11 – $155 per insert |
Sumitomo Electric | Japan | Advanced carbide and CBN inserts | $16 – $190 per insert |
TaeguTec | South Korea | Cost-effective carbide solutions | $9 – $140 per insert |
Kyocera | Japan | Diverse range of ceramic and carbide inserts | $10 – $150 per insert |
Tungaloy | Japan | Specialized carbide and ceramic tools | $14 – $170 per insert |
Selecting the Right Tracker Carbide Inserts
Choosing the right tracker carbide insert involves several considerations. Here’s a guide to help you make an informed decision:
Consideration | Details |
---|---|
Material | Match the insert material to the workpiece material for optimal performance. |
Coating | Choose coated inserts for higher wear resistance and longer tool life. |
Insert Shape | Select the shape based on the type of cut and machine compatibility. |
Cutting Speed | Higher speeds require inserts with better thermal stability. |
Feed Rate | Adjust the feed rate to match the insert’s capabilities and the material being machined. |
Depth of Cut | Ensure the insert can handle the required depth without compromising tool life. |
Machine Compatibility | Verify that the insert is compatible with your machining equipment. |
Application | Consider the specific application, such as roughing or finishing, to select the appropriate insert. |
Cost | Balance the cost of the insert with its expected performance and lifespan. |
Supplier Reputation | Choose reputable suppliers known for quality and consistency. |
Comparing Advantages and Limitations
Different types of tracker carbide inserts offer various advantages and limitations. Here’s a comparison to help you choose the best option:
Insert Type | Advantages | Limitations |
---|---|---|
Cemented Carbide | High hardness and toughness, versatile. | Can be brittle under heavy impact. |
Cermet | Excellent wear resistance and surface finish. | Limited toughness compared to cemented carbide. |
Coated Carbide | Enhanced cutting performance and tool life. | Higher cost due to coating. |
Ceramic | Superior high-temperature performance, ideal for hard materials. | Brittle and can fracture under heavy load. |
CBN | Best for hard and superalloy materials, extremely wear-resistant. | Expensive and not suitable for soft materials. |
Diamond | Unmatched hardness, excellent for non-ferrous materials. | Very costly and unsuitable for ferrous materials. |
PVD Coated | Improved thermal and chemical stability, versatile. | Can be more expensive due to advanced coating processes. |
Uncoated Carbide | Cost-effective and excellent for specific applications. | Limited wear resistance compared to coated inserts. |
Silicon Nitride | High toughness, perfect for heavy-duty applications. | Can be more expensive and harder to source. |
TiCN Coated | Enhanced toughness and wear resistance, versatile for various applications. | Higher cost compared to uncoated or basic carbide inserts. |
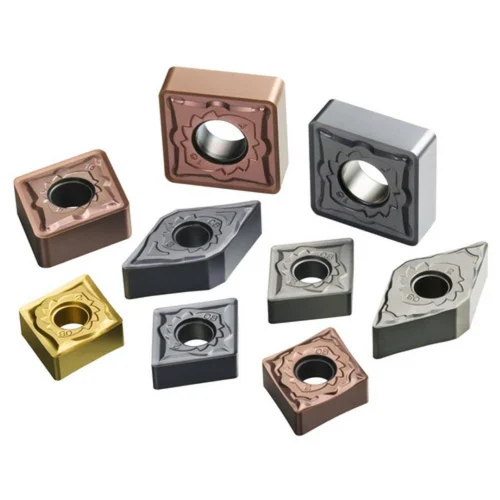
FAQ
What are tracker carbide inserts?
Tracker carbide inserts are cutting tools made from a composite of tungsten carbide and cobalt, used in various machining applications for their durability and efficiency.
How do I choose the right tracker carbide insert?
Consider factors like the material of the workpiece, cutting speed, feed rate, depth of cut, and machine compatibility. Also, consult with reputable suppliers and choose based on your specific application needs.
What are the benefits of using coated carbide inserts?
Coated carbide inserts offer enhanced wear resistance, longer tool life, and improved cutting performance, especially at high speeds and in demanding conditions.
Can I use diamond inserts for steel machining?
No, diamond inserts are not suitable for ferrous materials like steel due to chemical reactions that can degrade the diamond. They are best for non-ferrous materials.
What is the difference between PVD and CVD coatings?
PVD (Physical Vapor Deposition) coatings provide better adhesion and are ideal for sharper cutting edges, while CVD (Chemical Vapor Deposition) coatings are thicker and offer higher wear resistance.
Why are CBN inserts so expensive?
CBN (Cubic Boron Nitride) inserts are expensive because of their superior wear resistance and ability to machine hard and superalloy materials, providing significant performance advantages in specific applications.
How often should I replace my tracker carbide inserts?
The frequency of replacement depends on the application, material being machined, and the specific type of insert used. Monitor for signs of wear and replace as needed to maintain optimal performance.
Are uncoated carbide inserts still useful?
Yes, uncoated carbide inserts are cost-effective and perform well in specific applications, especially when machining non-ferrous metals and cast iron.
What are the best suppliers for tracker carbide inserts?
Reputable suppliers include Sandvik Coromant, Kennametal, Mitsubishi Materials, Seco Tools, Iscar, Walter AG, Sumitomo Electric, TaeguTec, Kyocera, and Tungaloy.
How can I extend the life of my carbide inserts?
Use the correct cutting parameters, ensure proper cooling, avoid excessive cutting speeds and feed rates, and select the appropriate insert for the material and application.
Conclusion
Choosing the right tracker carbide insert is crucial for achieving optimal performance in machining applications. By understanding the types, material properties, applications, and how to select the best insert for your needs, you can ensure efficient and cost-effective operations. Remember to consider reputable suppliers and balance cost with performance to get the most out of your investment in tracker carbide inserts.