Overview of solid carbide standard tool blank
solid carbide standard tool blanks are unfinished cutting tools made of solid carbide rods that are ground into a specific pre-formed shape. The blanks serve as a starting point to manufacture finished carbide cutting tools.
Key attributes of solid carbide tool blanks:
Attribute | Description |
---|---|
Material | Tungsten carbide or titanium carbide |
Manufacturing | Formed by grinding carbide rods |
Shape | Cylindrical, square, rectangular profiles |
Advantage | Faster to finish tools from preforms |
Finish machining | Coated and machined into final tool |
The blanks provide closer-to-final tool geometries to minimize grinding needed for the finished cutting tool.
Applications of Solid Carbide Tool Blanks
solid carbide standard tool blanks are used to manufacture cutting tools for:
- Turning operations – round inserts, boring bars, grooving tools
- Milling operations – indexable end mills, shell mills, face mills
- Drilling operations – flat drills, twist drills, gun drills
- Threading – thread mills, taps, dies
- Special operations – reamers, burrs, slitting saws
The rigidity and wear resistance of solid carbide makes it ideal for short-run machining of harder materials like stainless steel, titanium alloys, and exotic metals. The preformed blanks minimize production time.
Benefits of Solid Carbide Tool Blanks
Advantages of using solid carbide standard tool blanks:
Benefit | Description |
---|---|
Faster tooling time | Reduces programming and machining vs. stock material |
Closer tolerances | Blanks created to tighter size ranges |
Higher performance | Fully dense carbide enables most demanding applications |
Lower machining costs | Requires much less tool grinding time |
Standardized | Standard blank geometries for common tool types |
The benefits make tooling production from carbide blanks faster and economical for short runs.
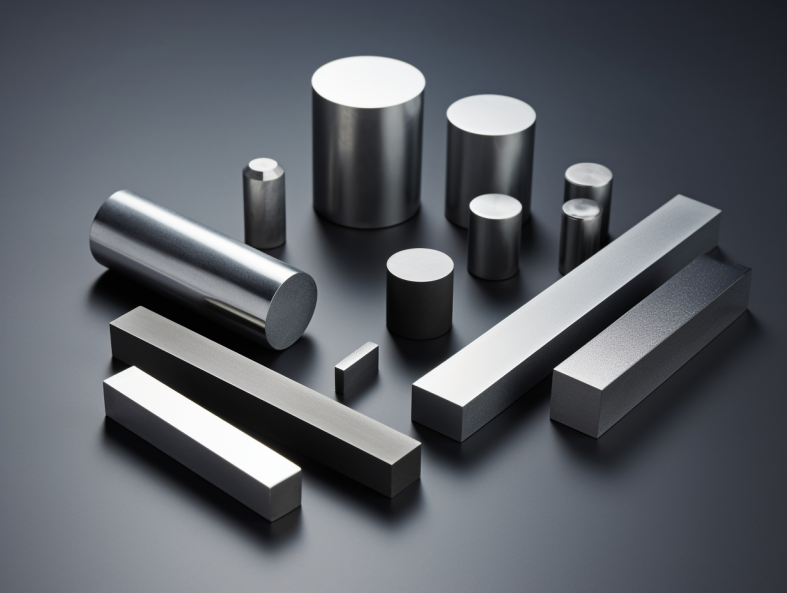
Limitations of Solid Carbide Tool Blanks
Disadvantages of solid carbide tool blanks:
Limitation | Description |
---|---|
Higher material cost | Solid carbide costs more than steel tooling |
Limited geometries | Only standard blank geometries available |
Longer lead times | Need to order standard blanks from suppliers |
Lower stiffness | Small diameters can deflect more |
Brittle material | Carbide is prone to chipping at edges |
For very high production runs, other tooling like carbide inserts or replaceable tip tools may be more cost effective.
Materials for solid carbide standard tool blanks
The most common materials for tool blanks are:
Material | Description |
---|---|
Tungsten carbide | WC-Co alloy, hardest and most wear resistant carbide |
Titanium carbide | TiC-Ni/Mo alloy, high wear resistance and toughness |
Cermet | WC-TiC in nickel/molybdenum binder |
Cubic boron nitride | Second hardest material for specialized applications |
Tungsten carbide grades make up the majority of blanks, offering an optimal balance of hardness, toughness, and cost. Special binder compositions impart specific characteristics like heat resistance or strength.
Solid Carbide Tool Blank Types
Common standard tool blank types include:
Tool | Standard Blank Styles |
---|---|
Round inserts | Cylindrical blanks in various diameters |
Square inserts | Square profile blanks with thickness options |
Drills | Cylindrical blanks in fractional diameters |
End mills | Cylindrical; tapers for flute helix |
Taps | Cylindrical blanks with square or hex ends |
Many other indexable inserts, boring bars, threading tools, and special form tools start from standard carbide blank geometries.
Solid Carbide Tool Blank Specifications
Typical specifications for solid carbide blanks include:
Parameter | Specification Range |
---|---|
Diameter | 0.5 mm to 25 mm diameters |
Length | 25 mm to 150 mm long |
Tolerances | Held to ±0.025 mm to ±0.127 mm |
Perpendicularity | 90° squareness within 0.01 mm to 0.05 mm |
Surface finish | Typically 0.4 to 3.2 μm Ra max |
Tighter geometrical tolerances yield more accurate finished cutting tools.
solid carbide standard tool blanks Suppliers
Leading suppliers of standard solid carbide tool blanks:
Supplier | Country |
---|---|
Kennametal | United States |
Sandvik Coromant | Sweden |
Iscar | Israel |
OSG | Japan |
Walter | Germany |
Sumitomo | Japan |
Komet Group | Germany |
Many smaller regional suppliers also exist worldwide. Blanks may be sold directly or through tooling distributors.
Selecting Solid Carbide Tool Blank Suppliers
Factors to consider when selecting solid carbide tool blank suppliers:
Factor | Criteria |
---|---|
Carbide grade options | Range of material grades available |
Size range | Variety of diameters and lengths in stock |
Geometrical accuracy | Precision ground to tight tolerances |
Coating services | In-house PVD coating capabilities |
Technical support | Expertise in grindable carbide alloys |
Delivery time | Short lead times for standard blanks |
Quality control certifications like ISO 9001 are essential for validating process consistency.
How to Grind Solid Carbide Tool Blanks
The process for grinding solid carbide tool blanks involves:
Step | Description |
---|---|
Mounting | Secure blank in proper workholding fixture |
Rough grinding | Remove excess material to near final shape |
Finishing | Fine grinding to tight tolerances |
Sharpening | Form cutting edges to specified geometry |
Polishing | Smooth out any remaining irregularities |
Coating | Apply wear resistant PVD coating |
CNC tool grinding machines enable fast, automated programming of the finishing routines based on tool geometry. Delicate handling is critical to avoid chipping the hard, brittle carbide edges.
Design Principles for Carbide Cutting Tools
Key design principles when grinding solid carbide tool blanks:
Design Aspect | Guidelines |
---|---|
Flute geometry | Suitable for material removal rate needed |
Helix angles | Proper flute helix for tool diameter and operation |
Chipbreakers | Appropriate groove geometry for chip control |
Edge preps | Small chamfers or hones to strengthen edge |
Tolerances | Grind to tight geometrical tolerances |
The tool geometry directly impacts cutting forces, tool life, chip control, and other performance characteristics.
Applications of Carbide Cutting Tools
Typical applications for carbide cutting tools:
Material | Applications |
---|---|
Hardened steels | Gear machining, die and mold production |
Stainless steels | Medical, aerospace components |
High temperature alloys | Nickel alloys for aerospace, turbine blades |
Titanium alloys | Aerospace and automotive components |
Cast iron | Automotive engine blocks, machinery |
Carbide tools provide the hardness and wear resistance needed for shorter production runs in difficult-to-machine materials.
Recycling and Reuse of Carbide Tooling
Used and worn carbide cutting tools are recycled in the following ways:
Method | Details |
---|---|
Regrinding | Worn tools are reground into modified geometry |
Remanufacturing | Worn areas built up then re-machined |
Coating stripping | Removed PVD coating allows reuse |
Carbide reclamation | Extracting tungsten carbide for reuse |
Recycling reduces waste and the environmental impacts of carbide tooling while realizing additional value from the high-cost materials.
Cost Analysis of Solid Carbide Tool Blanks
Cost factors when using solid carbide tool blanks:
- Carbide tool blank cost – $5 to $50 per blank
- Grinding machine capital investment – $100,000+
- Skilled labor for programming and grinding
- Grinding wheels and tool coating
- Higher carbide tooling costs compared to steel
- Lower total machining costs due to faster cycles
The blanks enable right-sized carbide tooling for short runs where steel tools are inefficient.
Advantages of Solid Carbide vs. Indexable Inserts
Comparison of solid carbide tools made from blanks vs. indexable inserts:
Solid carbide | Indexable inserts | |
---|---|---|
Upfront costs | Higher tooling cost | Lower insert cost |
Tool life | Shorter life per tool | Longer life, easily replaced |
Lead time | Need to order blanks | Off-the-shelf inserts |
Complexity | More complex geometries | Limited insert geometries |
Machining | Faster metal removal | Slower feed rates |
Indexable inserts tend to be a better solution for high production, while solid carbide works well for medium batch sizes and complex toolpaths.
Trends in Solid Carbide Tool Blanks
Emerging trends in solid carbide tool blanks:
- More carbide grade options tailored for specific materials
- Treatments to strengthen carbide grain boundaries
- Composite carbide blanks with harder coatings
- More precise standard blank geometries and tolerances
- Blanks optimized for machining, grinding, or EDM
- Supply chain localization outside China for stability
- Automated laser or waterjet cutting of blanks
- Increased variety of standard blank configurations
- Growth driven by demand for short-run custom tooling
Innovations in solid carbide blanks continue enhancing the performance and manufacturability of carbide cutting tools.
Summary of Solid Carbide Tool Blanks
- Preformed standard blanks for faster carbide cutting tool production
- Made of tungsten or titanium carbide materials
- Cylindrical, square, and rectangular blank geometries
- Minimizes grinding time versus raw stock material
- Enables short-run custom carbide tooling
- Essential for machining hardened steels, titanium, and other hard-to-cut materials
- Leading global suppliers provide a range of precise blank configurations
- Automated tool grinding machines finish blanks into final tools
- Proper tool geometry design principles must be followed
- Recycling reclaims valuable tungsten carbide
- Provides benefits over indexable inserts for small batches
- Advancing blank quality, geometries, and carbide grades
Solid carbide tool blanks will continue as an important platform for agile, short-run production of high performance custom cutting tools.
FAQ
Question | Answer |
---|---|
What tolerances are typical for carbide tool blanks? | Blanks are ground to tight dimensional tolerances around ±0.025 mm. |
What are the main advantage of using carbide blanks? | Faster production of carbide tools compared to starting with raw material. |
What types of cutting tools use carbide blanks? | End mills, drills, inserts, taps, specialty tools are commonly manufactured from carbide blanks. |
How should carbide tool edges be handled? | Careful handling is critical to avoid chipping the brittle carbide cutting edges. |
Can used carbide tools be recycled? | Yes, worn tools can be reground, remanufactured, or recycled through carbide reclamation. |