In the relentless pursuit of efficiency and precision, modern industries rely on materials that can withstand extreme conditions and deliver unwavering performance. Enter solid carbide rods, the unsung heroes quietly powering countless manufacturing processes, from the smartphones in our pockets to the aircraft soaring overhead.
This comprehensive guide delves into the fascinating world of solid carbide rods, exploring their properties, applications, and the reasons they are indispensable components in today’s technology-driven world.
What are Solid Carbide Rods?
Solid carbide rods, often referred to as tungsten carbide rods, are engineered materials renowned for their exceptional hardness, wear resistance, and ability to maintain their properties at high temperatures. Unlike tools with carbide inserts, these rods are crafted entirely from carbide material, ensuring consistent performance and extended tool life.
They are manufactured through a process called powder metallurgy, where fine particles of tungsten carbide (WC), a ceramic material significantly harder than steel, are bonded together using a metallic binder, typically cobalt (Co). This unique combination of properties makes solid carbide rods ideal for a wide range of demanding applications.
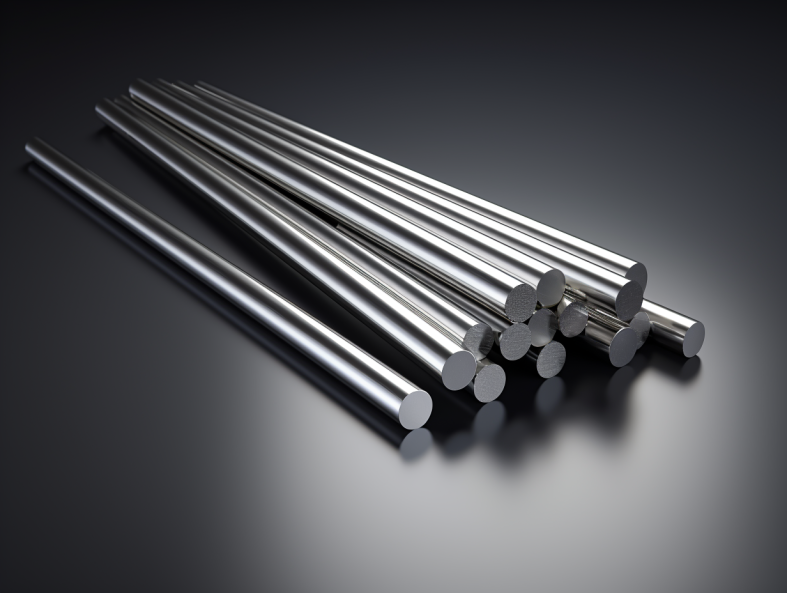
Understanding the Manufacturing Process
The remarkable properties of solid carbide rods are a testament to the precision engineering involved in their creation:
- Powder Preparation: Fine powders of tungsten carbide and cobalt are carefully blended in specific ratios to achieve the desired grade and properties.
- Compaction: The blended powder is then subjected to extremely high pressure, forming a “green” compact with the desired shape and dimensions.
- Sintering: The green compact is heated in a controlled atmosphere furnace to a temperature near the melting point of cobalt. This process, known as sintering, causes the cobalt binder to melt and flow, filling the spaces between the tungsten carbide particles and forming a solid, incredibly dense material.
- Finishing: After sintering, the solid carbide rod undergoes various finishing processes, such as grinding, polishing, or coating, to achieve specific surface finishes, tolerances, and desired properties.
Classifying Carbide Rods: Grades and Their Applications
Solid carbide rods are available in a wide array of grades, each tailored to specific applications and performance requirements. The grade of a carbide rod is primarily determined by:
- Grain Size: Finer grain sizes generally result in higher hardness and wear resistance but may sacrifice some toughness.
- Cobalt Content: Higher cobalt content enhances toughness and impact resistance but may slightly reduce hardness.
Common Carbide Rod Grades and Their Applications:
Grade | Typical Cobalt Content (%) | Grain Size (µm) | Characteristics | Applications |
---|---|---|---|---|
K01 | 4-7 | 0.2-2 | Extremely hard, excellent wear resistance | Micro-drills, engraving tools, precision cutting tools for very hard materials |
K10 | 8-12 | 0.4-5 | Good balance of wear resistance and toughness | Drills, end mills, reamers, drawing dies |
K20 | 10-16 | 0.8-10 | High toughness, good wear resistance | Impact-resistant tools, mining bits, rock drilling tools |
K30 | 16-25 | 1.2-20 | Very high toughness, moderate wear resistance | Heavy-duty impact applications, chisels, shear blades, woodworking tools |
Table 1: A Glimpse into the Diverse World of Carbide Rod Grades
Unleashing the Potential: Applications Across Industries
The exceptional properties of solid carbide rods have propelled them into a wide range of industries and applications, including:
Metalworking and Machining:
- Cutting Tools: Drills, end mills, reamers, and other cutting tools rely on carbide’s hardness and wear resistance for machining a wide range of materials, from aluminum to hardened steel.
- Dies and Punches: Carbide’s ability to withstand high pressures and abrasive forces makes it ideal for forming and shaping metal parts in stamping, drawing, and cold forming operations.
- Wear Parts: Solid carbide rods are used in bearings, bushings, guides, nozzles, and other components subjected to wear and friction, extending their service life significantly.
Construction and Mining:
- Drilling and Boring: Carbide inserts are essential components in drill bits for concrete, rock drilling tools, and tunnel boring machines (TBMs), enabling them to penetrate hard and abrasive materials.
- Road Construction: Road milling machines equipped with carbide-tipped cutting drums efficiently remove old asphalt or concrete, preparing the way for fresh pavement.
Other Notable Applications:
- Aerospace: Carbide rods are used in turbine blades, bearings, and other critical components requiring high-temperature strength and wear resistance.
- Medical Devices: Carbide’s biocompatibility and wear resistance make it suitable for surgical instruments, dental burs, and orthopedic implants.
- Oil and Gas: Carbide rods are used in drilling equipment, downhole tools, and other components for oil and gas exploration and production, where they can withstand harsh environments and abrasive formations.
Comparing Carbide Rod Suppliers: Navigating the Market
Supplier | Location | Price Range (per piece, approximate) | Specialties |
---|---|---|---|
TRUER | China | $10 – $500 | Customized carbide rods, high-precision grinding, wide range of grades, competitive pricing |
Sandvik Coromant | Sweden | $20 – $600 | Cutting tools, wear parts, tooling systems, global presence |
Kennametal | USA | $15 – $550 | Metal cutting tools, wear-resistant solutions, advanced material science expertise |
Kyocera | Japan | $18 – $580 | Cutting tools, ceramic components, industrial tools, focus on precision and quality |
Element Six | UK | $25 – $650 | Synthetic diamond and superabrasive materials, high-performance applications |
Table 2: Carbide Rod Suppliers – A Snapshot of Key Players
Please note: Prices are approximate and can vary significantly based on factors such as grade, dimensions, quantity, and market conditions. It’s always recommended to contact suppliers directly for accurate and up-to-date pricing information.
Weighing the Pros and Cons: A Balanced Perspective
Advantages:
- Exceptional Hardness and Wear Resistance: Unmatched by most other materials, making them ideal for demanding applications involving high friction, abrasion, and extreme temperatures.
- High Strength and Stiffness: Able to withstand high loads and maintain dimensional stability under stress, ensuring precision and accuracy in critical applications.
- Versatility: Available in various grades and forms to suit a wide range of applications, from micro-drilling to heavy-duty machining.
- Long Service Life: Their exceptional durability translates into extended tool life, reduced downtime, and lower maintenance costs over time.
Limitations:
- Brittleness: Susceptible to chipping or fracture under impact or shock loads, requiring careful handling and application within their recommended parameters.
- Cost: Generally more expensive than traditional materials like steel, although their extended lifespan and performance benefits often outweigh the initial cost.
- Machining Challenges: Their extreme hardness requires specialized tooling, expertise, and equipment for machining and processing.
Table 3: Solid Carbide Rods – A Balanced View of Their Strengths and Limitations
Why Choose TRUER as Your Carbide Rod Partner?
TRUER stands out as a premier provider of high-quality solid carbide rods, offering a compelling combination of:
- Customization Expertise: We specialize in tailoring carbide rod solutions to meet your precise specifications, from grade selection and dimensional tolerances to surface finishes and coatings.
- Precision Manufacturing: Our advanced grinding and finishing capabilities ensure exceptional dimensional accuracy and surface quality, meeting the stringent demands of various industries.
- Competitive Pricing: We strive to provide cost-effective solutions without compromising on quality, offering competitive pricing and flexible order quantities.
- Commitment to Customer Satisfaction: Our dedicated team is committed to providing exceptional service and support throughout your carbide rod journey, from initial inquiry to final delivery and beyond.
FAQs: Addressing Your Solid Carbide Rod Queries
1. What is the difference between solid carbide rods and carbide inserts?
Solid carbide rods are crafted entirely from carbide material, while carbide inserts are typically small, indexable pieces of carbide brazed or clamped onto a tool body made of a different material. Solid carbide tools offer greater rigidity and heat resistance, making them suitable for high-speed machining and demanding applications.
2. Can solid carbide rods be coated?
Yes, solid carbide rods can be coated with various materials, such as titanium nitride (TiN), titanium aluminum nitride (TiAlN), or diamond-like carbon (DLC), to further enhance their wear resistance, lubricity, or oxidation resistance.
3. How do I choose the right coolant for machining with solid carbide tools?
Effective cooling and lubrication are crucial when machining with solid carbide tools to dissipate heat and reduce friction. Water-soluble synthetic coolants, often with added lubricity agents, are commonly used. The specific coolant choice depends on the material being machined, cutting speed, and other factors.
4. What are the common causes of premature tool wear in solid carbide rods?
Premature tool wear can result from various factors, including improper tool selection, insufficient cooling and lubrication, excessive cutting speeds or feed rates, and machining of hard or abrasive materials.
5. How should I store solid carbide rods to prevent damage?
Store carbide rods in a clean, dry environment, preferably in a dedicated tool crib or cabinet. Avoid contact with other metal objects to prevent chipping or damage. It’s also advisable to store them vertically to minimize the risk of bending.