Imagine a material so tough, it can shrug off wear and tear like a seasoned warrior. A substance that maintains its razor-sharp edge even after relentlessly carving through unforgiving materials. That’s the essence of a solid carbide plate.
In a nutshell, a solid carbide plate is a sheet of tungsten carbide, an incredibly hard ceramic compound renowned for its exceptional wear resistance, strength, and heat tolerance. Think of it as the superhero of the material world, boasting near-diamond-like hardness and the ability to withstand scorching temperatures that would melt most metals.
Let’s delve deeper into the world of solid carbide plates, exploring their composition, properties, applications, and the nitty-gritty details like specifications, pricing, and trade-offs involved.
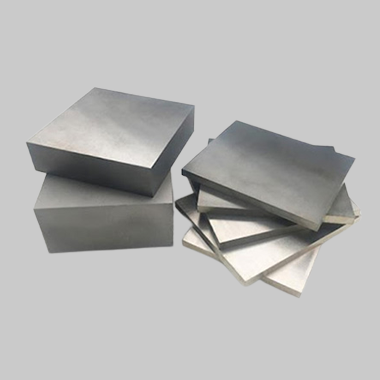
Composition and Key Properties of Solid Carbide Plates
Breaking it down to its core, a solid carbide plate is primarily composed of tungsten carbide (WC) grains. Imagine tiny, microscopic diamonds densely packed together – that’s the essence of the tungsten carbide component. These WC grains are held together by a metallic binder, most commonly cobalt (Co). The exact ratio of WC to Co can be fine-tuned to achieve specific properties tailored for various applications.
Here’s a table summarizing the key characteristics of solid carbide plates:
Property | Description |
---|---|
Primary Composition | Tungsten Carbide (WC) grains and a Cobalt (Co) binder |
Hardness | Extremely high |
Wear Resistance | Exceptional, making them ideal for applications involving abrasive materials |
Strength | High compressive strength, allowing them to handle significant loads |
Heat Resistance | Can withstand high temperatures without losing their properties |
Brittleness | Can be brittle under certain conditions, requiring careful handling |
Corrosion Resistance | Good resistance to many chemicals and corrosive environments |
The unique combination of these properties makes solid carbide plates a highly sought-after material across various industries.
Unveiling the Applications of Solid Carbide Plates: Where They Shine
Solid carbide plates are the ultimate workhorses in industrial settings, tackling some of the toughest jobs imaginable. Here’s a glimpse into their diverse applications:
Application | Description |
---|---|
Metalworking | Used in cutting tools like drill bits, milling inserts, and end mills for machining various metals |
Woodworking | Employed in router bits and planer blades for precise wood cutting and shaping |
Mining and Construction | Utilized in wear parts for equipment like rock drills and crushing machinery |
Oil and Gas Drilling | Used in downhole tools that can withstand the harsh conditions of oil and gas wells |
Electronics | Employed in dies and punches for high-precision stamping and forming of electronic components |
Textiles | Used in spinning nozzles and other wear parts in textile manufacturing equipment |
Aerospace | Found in components that require exceptional wear resistance and heat tolerance |
This list just scratches the surface of the countless applications where solid carbide plates reign supreme. Their versatility and exceptional properties make them a valuable asset in a wide range of industrial processes.
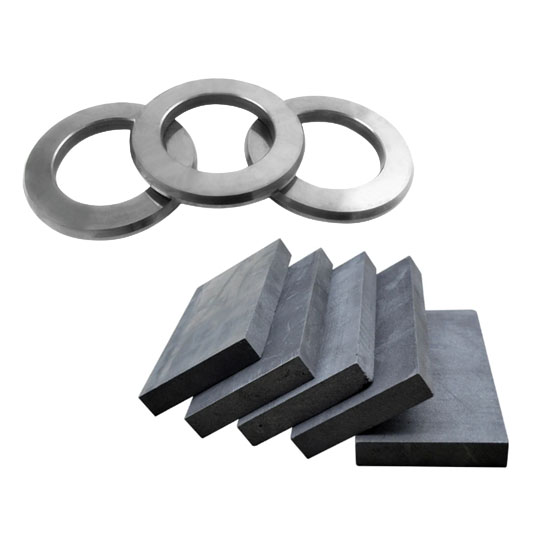
Unveiling the Specifications: Sizes, Grades, and Standards
Solid carbide plates come in a variety of specifications to cater to diverse needs. Here’s a breakdown of some key factors to consider:
Sizes:
- Thickness: Solid carbide plates typically range in thickness from a thin foil-like 0.1 mm to a robust 100 mm, depending on the intended application.
- Length and Width: Dimensions can vary greatly, with standard sizes readily available from suppliers. Custom sizes can also be produced for specific needs.
Grades:
The ratio of tungsten carbide (WC) to cobalt (Co) in the plate determines its grade. A higher WC content translates to increased hardness and wear resistance, but also comes with a trade-off in toughness. Conversely, a higher cobalt content enhances toughness but reduces hardness. Here’s a general breakdown of common grades:
- ISO K Grades: These grades prioritize hardness, ideal for applications involving machining hard and abrasive materials. (e.g., ISO K10, ISO K20)
- ISO P Grades: These grades offer a balance between hardness and toughness, making them suitable for a wider range of machining applications. (e.g., ISO P10, ISO P20)
- ISO H Grades: These grades prioritize toughness, making them a good choice for applications that involve shock and impact resistance. (e.g., ISO H10, ISO H20)
Standards:
Several international standards govern the specifications of solid carbide plates. Here are some prominent examples:
- ISO (International Organization for Standardization): This international standard-setting body publishes various standards for tungsten carbide products, including ISO 513 for dimensions and ISO 4284 for hardness.
- ASTM International (American Society for Testing and Materials): This US-based organization sets standards for various materials, including ASTM B773 for tungsten carbide powder and ASTM B678 for sintered hardmetals.
- JIS (Japanese Industrial Standards): This Japanese standards organization establishes guidelines for industrial products, including JIS B 9002 for tungsten carbide tools.
By understanding these specifications, you can select the most appropriate solid carbide plate for your specific application.
Pricing: Unveiling the Cost of Solid Carbide Plates
The cost of solid carbide plates depends on several factors, including:
- Size: Larger plates naturally command a higher price tag compared to smaller ones.
- Thickness: Thicker plates require more material and will be more expensive.
- Grade: Plates with a higher WC content (harder grades) typically cost more than those with a higher Co content (tougher grades).
- Surface Finish: Plates with a meticulously polished finish may incur additional costs compared to those with a standard finish.
- Supplier: Pricing can vary between different suppliers based on factors like location, production scale, and brand reputation.
As a general estimate, expect to pay anywhere from tens of dollars for small, standard-grade plates to thousands of dollars for large, custom-made plates with a premium finish.
Solid Carbide Plates: A Balancing Act – Pros and Cons
Solid carbide plates offer a multitude of advantages, making them a popular choice in industrial settings. Here’s a breakdown of their key strengths:
- Exceptional Wear Resistance: Their superior hardness allows them to withstand abrasive environments that would quickly wear down other materials.
- High Strength: They can handle significant loads without deforming or breaking.
- Heat Resistance: They maintain their properties at elevated temperatures, making them ideal for hot machining applications.
- Dimensional Stability: They hold their shape well, ensuring precise machining results.
- Long Tool Life: Their exceptional wear resistance translates to longer tool life between replacements, reducing downtime and maintenance costs.
However, there are also some limitations to consider:
- Brittleness: Solid carbide plates can be brittle under certain conditions, especially when subjected to high impact or shock loads. Careful handling and proper machining techniques are crucial to prevent chipping or breakage.
- Higher Cost: Compared to some other materials, solid carbide plates can be more expensive. However, their extended tool life and reduced downtime often offset the initial cost in the long run.
- Limited Machinability: Solid carbide requires specialized tooling and techniques for machining. Improper machining can damage the plate and compromise its performance.
By understanding these pros and cons, you can make an informed decision about whether solid carbide plates are the right choice for your application.
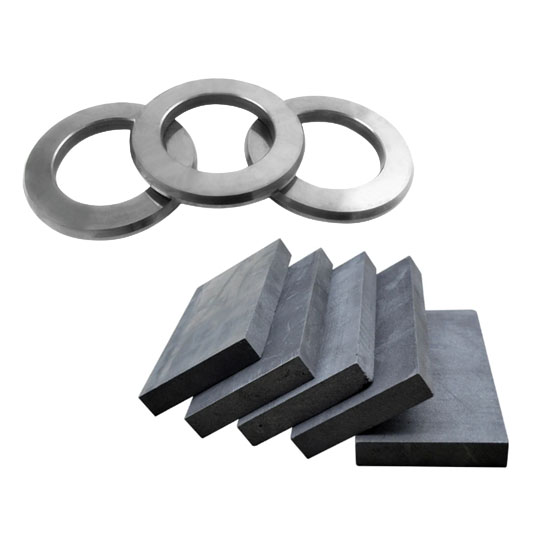
FAQ
Here are some of the most common questions people ask about solid carbide plates, presented in a question-and-answer format for easy reference:
Question | Answer |
---|---|
What is the difference between a solid carbide plate and a solid carbide tool? | A solid carbide plate is the raw material, a sheet of tungsten carbide. A solid carbide tool, like a drill bit or milling insert, is a finished product machined from a solid carbide plate. |
Can solid carbide plates be recycled? | Yes, solid carbide can be recycled and used to manufacture new plates or other tungsten carbide products. |
How long do solid carbide plates last? | The lifespan of a solid carbide plate depends on various factors like the application, workload, and machining conditions. However, they generally offer significantly longer tool life compared to other materials. |
What are some alternatives to solid carbide plates? | Depending on the application, alternatives might include high-speed steel (HSS), tool steel, ceramic, or diamond-coated tools. Each material has its own unique properties and limitations. |
Where can I buy solid carbide plates? | Solid carbide plates can be purchased from a variety of industrial tool suppliers and metalworking distributors. Many manufacturers also sell their products directly online. |