Overview of Solid Carbide Drill Blanks
Solid carbide drill blanks are unfinished drill bodies used to manufacture custom drills and other rotary cutting tools. Key details:
- Made from solid bars/rods of sintered tungsten carbide (WC-Co).
- Blanks have standardized shank dimensions but unfinished cutting ends.
- Cutting edges are ground to specified geometries based on application needs.
- Provides optimal hardness, wear resistance, strength at high temperatures.
- Used for tough materials or difficult drilling conditions requiring durability.
- Finished tools used in metals processing, construction, mining, oil/gas, and other industries.
Types of Solid Carbide Drill Blanks
Type | Description |
---|---|
Straight shank | Most common. Used in chucks or collets. |
Taper shank | Used in machine tapers for rigidity. |
Coolant-through | Internal channels provide coolant to cutting edges. |
Core drill | Hollow core design for deep drilling. |
Gun drill | For deep drilling of small diameter holes. |
Various shank types and cutting end designs suit different machining needs.
Applications of Carbide Drill Tools
Industry | Typical Applications |
---|---|
Automotive | Transmission components, engine blocks, drivetrain parts |
Aerospace | Precision holes in turbine blades, airfoils |
Oil/gas | Drilling and tapping holes in pipes, valves |
Construction | Tile, masonry, concrete drilling |
General machining | Drilling metals like steel, titanium, nickel alloys |
Carbide drills used where high hardness or abrasion resistance is required.
Solid Carbide Drill Blank Specifications
Parameter | Details |
---|---|
Diameter | 1-25 mm range |
Length | Up to 12x diameter |
Shank types | Straight, tapered, flatted |
Carbide grade | C1 to C6 based on cobalt content |
Coating | TiAlN, TiCN, etc. for added wear resistance |
Accuracy | Up to ±0.01 mm on dimensions |
Many standard and custom parameters like diameter, carbide grade, coatings, tolerance available.
Typical Suppliers of Solid Carbide Drill Blanks
Supplier | Description |
---|---|
Manufacturer 1 | Leading brand. Wide range of stock blanks. |
Manufacturer 2 | Low-cost imports. Standard styles and sizes. |
Manufacturer 3 | Made-to-order custom blank design. |
Manufacturer 4 | High-precision blanks for aerospace/medical uses. |
Pricing depends on blank dimensions, carbide grade, tolerances, and order quantities.
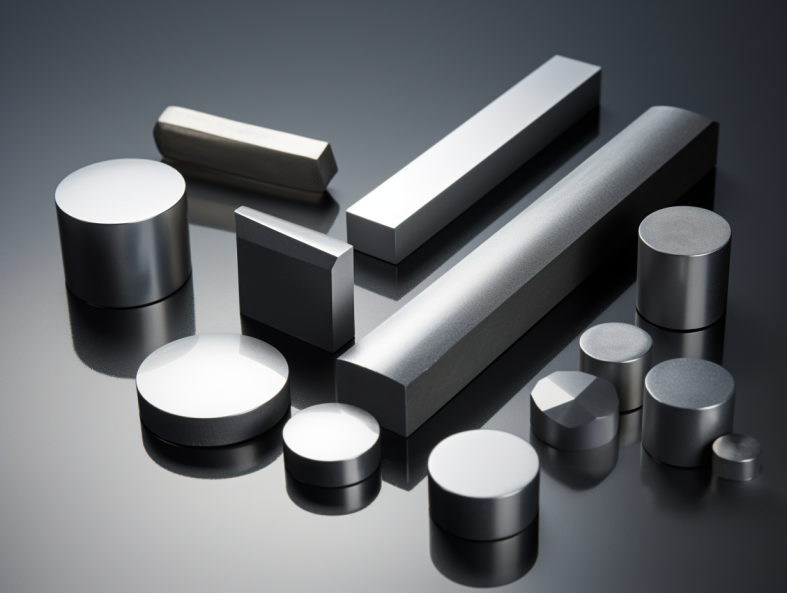
How to Select a Solid Carbide Drill Blank Supplier
Consider the following when choosing a solid carbide drill blank supplier:
- Technical expertise – Look for extensive knowledge of carbide metallurgy and rotary cutting tools. This enables high performance blank design.
- Design capabilities – Supplier should offer standard and custom shank, diameter, length configurations to meet application needs.
- Quality systems – ISO 9001 or AS9100 certification indicates reliability and consistent QC.
- Tolerances – Supplier should be capable of tight tolerances on diameters, straightness, surface finish etc.
- Lead times – Select a supplier able to deliver blanks within your project timeline requirements.
- Services – Some offer additional services like coating, cutting edge grinding, laser marking etc.
- Cost – Weigh cost against factors like quality level, tolerances, lead time, and technical support.
Choose a supplier recognized for carbide blank expertise that understands your drilling application needs.
Design Considerations for Carbide Drill Blanks
- Select carbide grade based on hardness, toughness, and temperature needs – higher cobalt content increases toughness.
- Choose diameter, shank style, and flute length based on hole size, depth, and accessibility.
- Specify appropriate cutting edge geometry – lip relief angle, chisel edge width etc. based on material being drilled.
- Add surface coatings like TiAlN or diamond coating to further improve wear resistance and lubricity if needed.
- Tighter dimensional tolerances and finer surface finishes result in more consistent performance but cost more.
- Coolant-through designs help provide cooling and chip flushing when deep drilling.
- Optimize the blank design to suit your drilling applications through testing and iterations.
Work closely with blank suppliers to identify the optimal drill design configuration for your needs.
Grinding and Machining Carbide Drill Blanks
- Use CNC tool grinders to manufacture the cutting edges to custom geometry.
- Follow cutting tool best practices – proper wheel selection, light passes, appropriate coolant. Carbide is abrasive and hard.
- Precision grinding produces complex geometries not possible with molding/pressing.
- Allows creating specialized profiles like core drills, gun drills, trepanning tools.
- Secondary operations like fluting, grooving, threading, coating can also be done.
- Rigid workholding is critical to achieve tight tolerances during grinding. Air clamping preferred.
- Use diamond or CBN grinding wheels to cut carbide blanks. Conventional abrasives wear too quickly.
- Program precise tool paths based on blank dimensions to generate the required cutter profile.
- Perform in-process inspection of key parameters like diameters, Civ angles, edge sharpness etc.
Carbide tool grinding requires specialized equipment, wheels, and experience to achieve precision blanks.
Quality Control and Inspection of Carbide Blanks
- Measure dimensions like diameter, length, straightness, and finish to confirm they are within tolerance using indicators, micrometers, calipers, etc.
- Verify carbide grade, composition, grain size, and cobalt content through wet chemical analysis and microscopy.
- Ensure concentricity of features using chucks, collets, and dial indicators.
- Examine surface quality under a microscope at high magnifications to detect any porosity or defects.
- Test hardness and transverse rupture strength (TRS) per ISO specifications.
- Apply mag particle or penetrant testing to check for microscopic cracks not visible to the eye.
- Monitor process parameters like grinding wheel speed, feed rate, coolant pressures during manufacturing for statistical control.
Use a proven quality plan and measurement system tailored to your specific component requirements and drawing tolerances.
Inventory Management for Carbide Blanks
- Forecast usage rates and lead times to plan economic order quantities from suppliers.
- Store blanks properly in a clean, dry environment to prevent corrosion during storage.
- Segregate inventory – keep different grades/sizes/coatings separate to avoid mixups.
- Use FIFO inventory management – first in, first out. Turn over stock to keep material fresh.
- Monitor stock levels and reorder points to ensure sufficient supply is on hand to meet production schedules.
- Track inventory in an electronic system for easy viewing of blank availability, orders, lead times, etc.
- Digitize records for each received blank lot – certifications, test results, batch number, date code etc.
- Perform periodic cycle counting and physical validation of actual vs recorded stock.
Effective inventory control reduces costs while ensuring required blanks are available when needed.
Troubleshooting Guide for Carbide Drill Performance
Issue | Potential Causes | Corrective Actions |
---|---|---|
Excessive wear | Wrong grade for material, low quality carbide, inadequate coating | Select optimal grade, improve powder quality, apply wear-resistant coating |
Chipping/fracture | Low cobalt content, poor grinding quality, feed/speed too high | Increase cobalt content for better toughness, improve wheel/parameters, decrease feeds/speeds |
Poor hole size/finish | Incorrect drill diameter or geometry, runout, built-up edge | Measure drill dimensions, improve concentricity, increase surface speeds |
Poor productivity | Low rigidity, incorrect feeds/speeds, inadequate chip removal | Use rigid setup, optimize feeds/speeds, use through-tool coolant |
Work with carbide experts to fine-tune the blank design and resolve any drilling issues.
Pros and Cons of Solid Carbide vs Other Tool Materials
Solid Carbide Advantages
- Hardness maintains sharp cutting edge for longer tool life
- Strength and wear resistance at high speeds and temperatures
- Dimensional stability across operating temperature range
- Range of grades optimizable for toughness or hardness
Solid Carbide Disadvantages
- Brittle – prone to chipping and catastrophic failure if overloaded
- Higher upfront cost compared to high speed or cobalt steel
- Heavier than other tool materials for a given strength
- More abrasive and difficult to grind than steel
- Limited in terms of maximum usable driller diameter
FAQs
Q: What grade of carbide should be used for drilling hardened steel?
A: Carbide grades with 6-8% cobalt like C2-C4 work well for the hardness and toughness needed to drill hardened tool steels up to 45 HRC.
Q: What cutting edge coatings are typically used on carbide drill blanks?
A: TiAlN (titanium aluminum nitride), TiCN (titanium carbon nitride), and diamond coatings are common to provide lubricity and further improve wear resistance.
Q: What causes premature carbide drill failure?
A: Wrong speeds/feeds, poor workholding rigidity allowing vibration, inadequate flute space causing chip welding, poor carbide quality, and operating outside the drill’s designed capacity.
Q: Can you resharpen solid carbide drills?
A: Yes, solid carbide can be resharpened a limited number of times. The cutting edges are re-ground to restore sharpness.
Q: How long do carbide drills last compared to high speed steel?
A: 4-10 times longer tool life is typical if using optimal operating parameters. Carbide’s hardness and wear resistance gives it a longer lifespan under the same conditions.
Q: What tolerances are typical for carbide drill blanks?
A: Blanks can be produced to tolerances around ±0.01 mm for precision applications. Production grades are often ±0.05 mm.
Q: Are solid carbide drills suitable for CNC machining applications?
A: Yes, carbide is commonly used for CNC drilling and boring applications that require tooling to run for prolonged periods without needing changed or sharpened.
Q: Can coolant be used when drilling with solid carbide tools?
A: Yes, through-tool coolant or high pressure flood cooling improves chip removal and carbide tool life when drilling metals.