sharpening carbide inserts are essential tools in the machining world, designed for durability and precision. But even the toughest carbide inserts need sharpening to maintain their performance. This comprehensive guide delves into the nitty-gritty of sharpening carbide inserts, from understanding their composition to selecting the right sharpening method. Whether you’re a seasoned machinist or just starting out, this guide will walk you through everything you need to know.
Overview of Sharpening Carbide Inserts
Carbide inserts are tiny but mighty components used in metalworking, offering remarkable hardness and wear resistance. These inserts are crafted from a combination of tungsten carbide and cobalt, making them incredibly durable. However, over time, they can lose their edge, necessitating sharpening to restore their cutting performance.
Why Sharpen Carbide Inserts?
Sharpening carbide inserts is crucial for maintaining their efficiency and extending their lifespan. Dull inserts can lead to poor-quality cuts, increased tool wear, and even damage to the workpiece. Regular sharpening ensures that the inserts remain sharp, providing cleaner cuts and improving overall productivity.
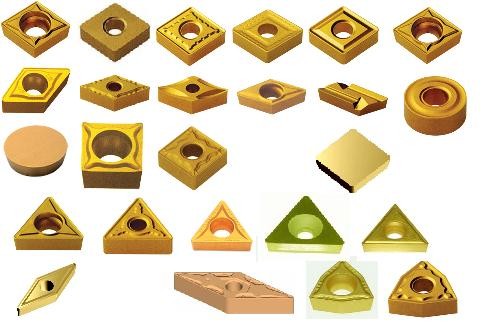
Types of Sharpening Carbide Inserts
Carbide inserts come in various types, each designed for specific applications. Here’s a table summarizing some common types of carbide inserts and their uses:
Insert Type | Description | Application |
---|---|---|
CNMG | Negative rake angle, double-sided | General turning and milling |
TNMG | Triangular, negative rake angle | Roughing and finishing |
SNMG | Square, negative rake angle | Heavy roughing |
DNMG | Diamond-shaped, negative rake angle | Fine finishing |
WNMG | Trigon, negative rake angle | Medium to heavy roughing |
CCMT | Positive rake angle, single-sided | Finishing and light cutting |
DCMT | Diamond-shaped, positive rake angle | Precision finishing |
VBMT | Rhombic, positive rake angle | Fine finishing and profiling |
RCMT | Round, positive rake angle | Contouring and profiling |
APKT | Rectangular, positive rake angle | Milling |
Applications of Sharpening Carbide Inserts
Sharpening carbide inserts is vital for various machining processes. Different applications require different insert types and sharpening techniques:
Application | Insert Type | Sharpening Technique |
---|---|---|
Turning | CNMG, TNMG, DNMG | Honing, grinding |
Milling | APKT, RCMT | Diamond wheel grinding |
Drilling | CCMT, DCMT | Diamond paste honing |
Profiling | VBMT, RCMT | Hand honing with diamond stones |
Roughing | SNMG, WNMG | Grinding with CBN wheels |
Material Properties of Carbide Inserts
Understanding the material properties of carbide inserts is crucial for selecting the right sharpening method. Here’s a breakdown of key properties:
Property | Description |
---|---|
Hardness | Extremely hard, typically 85-92 HRA |
Toughness | High toughness, resistant to breakage |
Wear Resistance | Excellent wear resistance due to carbide composition |
Thermal Stability | Maintains hardness at high temperatures |
Chemical Resistance | Resistant to corrosion and chemical reactions |
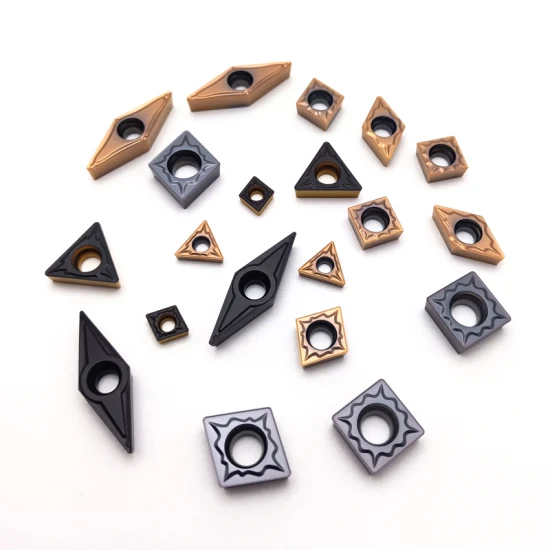
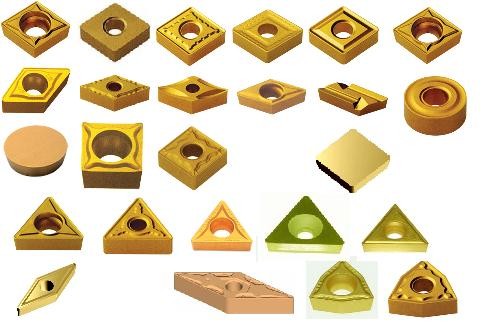
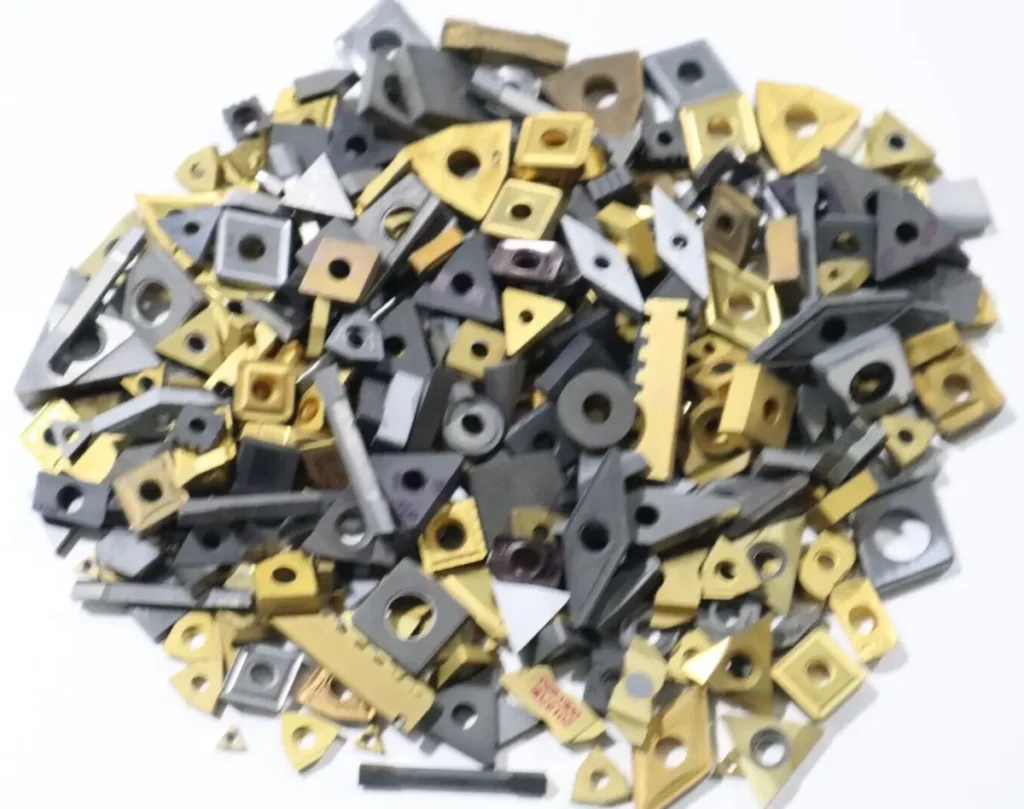
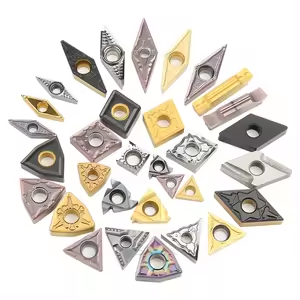
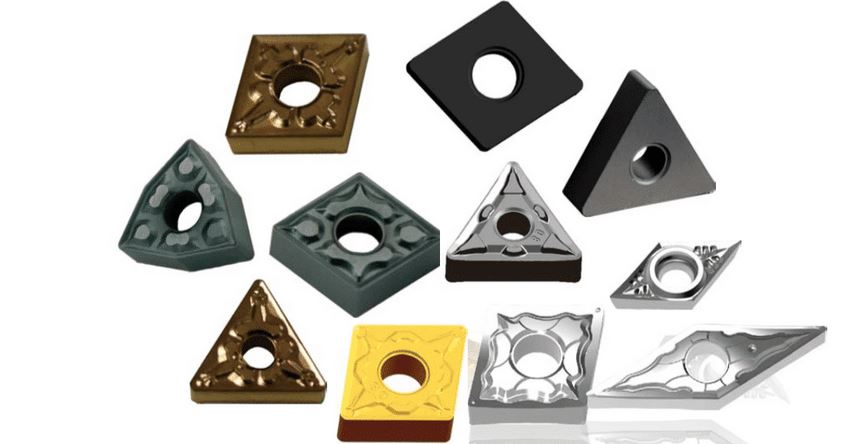
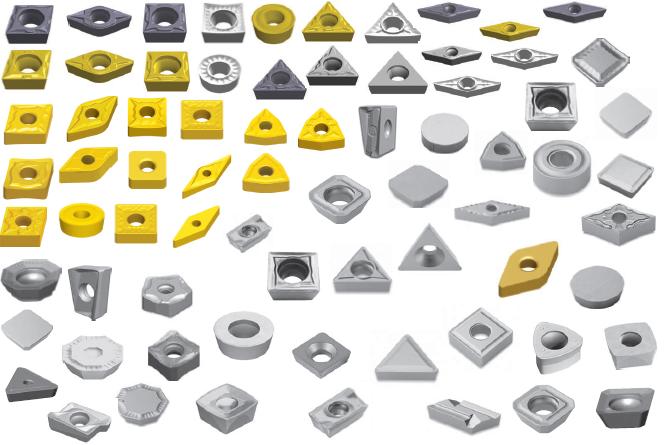
Composition, Properties, and Characteristics
Carbide inserts are primarily composed of tungsten carbide and cobalt, each contributing to their unique characteristics:
Component | Role | Characteristics |
---|---|---|
Tungsten Carbide | Provides hardness | Extremely hard and wear-resistant |
Cobalt | Acts as a binder | Enhances toughness and durability |
Titanium Carbide | Optional addition | Increases hardness and wear resistance |
Tantalum Carbide | Optional addition | Improves toughness and thermal stability |
Hardness, Strength, and Wear Resistance
Carbide inserts are known for their impressive hardness, strength, and wear resistance. Here’s a comparison of these properties:
Property | Description |
---|---|
Hardness | Ranges from 85 to 92 HRA, making them one of the hardest materials available |
Strength | High compressive strength, resistant to deformation |
Wear Resistance | Superior wear resistance, ideal for high-speed machining |
Specifications, Sizes, Shape, and Standards
Carbide inserts come in various shapes and sizes, adhering to industry standards for consistent performance:
Specification | Details |
---|---|
Sizes | Common sizes include 1/4″, 1/2″, 3/4″ inserts |
Shapes | Square, triangular, diamond, round, rhombic |
Standards | ISO, ANSI, and DIN standards ensure compatibility and quality |
Suppliers and Pricing Details
Choosing the right supplier is crucial for obtaining high-quality carbide inserts. Here’s a list of some reputable suppliers and their pricing details:
Supplier | Location | Price Range |
---|---|---|
Sandvik Coromant | Global | $5 – $20 per insert |
Kennametal | Global | $10 – $30 per insert |
ISCAR | Global | $8 – $25 per insert |
Mitsubishi Materials | Global | $12 – $35 per insert |
Sumitomo Electric | Global | $15 – $40 per insert |
Selecting the Right Sharpening Carbide Inserts
Choosing the right sharpening method depends on various factors, including the type of insert, the material being machined, and the desired finish. Here’s a guide to help you select the right sharpening carbide inserts:
Factor | Consideration | Recommended Sharpening Method |
---|---|---|
Insert Type | Positive vs. negative rake | Diamond wheel grinding for negative rake, diamond paste honing for positive rake |
Material | Hardness and toughness | Harder materials require diamond wheels, softer materials can use CBN wheels |
Desired Finish | Roughing vs. finishing | Finishing requires finer honing, roughing can use coarser grinding |
Advantages and Limitations
Understanding the advantages and limitations of sharpening carbide inserts can help you make an informed decision:
Aspect | Advantages | Limitations |
---|---|---|
Performance | Maintains cutting efficiency, extends tool life | Requires precise technique, can be time-consuming |
Cost | Cost-effective compared to replacing inserts | Initial investment in sharpening equipment |
Versatility | Can be used for various machining processes | Limited by the type of sharpening equipment available |
Sharpening Techniques: How to Choose the Right Method
Choosing the right sharpening technique is crucial for maintaining the performance of carbide inserts. Here’s a detailed look at some common sharpening methods and their applications:
Honing with Diamond Stones
Honing with diamond stones is a precise method ideal for finishing and profiling. This technique involves manually honing the insert with a fine-grit diamond stone, ensuring a sharp edge without removing too much material.
Grinding with CBN Wheels
CBN (Cubic Boron Nitride) wheels are excellent for roughing and heavy material removal. This method uses a CBN wheel to grind the insert, providing a sharp edge and maintaining the insert’s geometry.
Diamond Wheel Grinding
Diamond wheel grinding is a versatile method suitable for both roughing and finishing. This technique involves using a diamond wheel to grind the insert, ensuring a sharp and durable edge.
Diamond Paste Honing
Diamond paste honing is a fine-tuning method ideal for achieving a mirror-like finish. This technique involves applying diamond paste to a honing tool and carefully honing the insert, ensuring a razor-sharp edge.
Sharpening Carbide Inserts: Step-by-Step Guide
Sharpening carbide inserts requires precision and the right tools. Here’s a step-by-step guide to help you get started:
- Gather Your Tools: Ensure you have the necessary sharpening tools, including diamond stones, CBN wheels, and honing paste.
- Clean the Insert: Remove any debris or buildup on the insert using a soft brush and cleaning solution.
- Secure the Insert: Place the insert in a secure fixture to prevent movement during sharpening.
- Choose the Sharpening Method: Select the appropriate sharpening method based on the insert type and desired finish.
- Sharpen the Insert: Carefully sharpen the insert, maintaining consistent pressure and angle.
- Inspect the Edge: Check the insert’s edge for sharpness and uniformity. Repeat the process if necessary.
- Clean and Store: Clean the insert again and store it in a safe place to prevent damage.
Comparing Sharpening Methods: Which is Best?
Different sharpening methods offer various advantages and limitations. Here’s a comparison to help you choose the best method for your needs:
Method | Advantages | Limitations |
---|---|---|
Diamond Stones | Precise, ideal for finishing | Time-consuming, requires skill |
CBN Wheels | Efficient, good for roughing | Can remove too much material if not used carefully |
Diamond Wheel Grinding | Versatile, durable edge | Requires specialized equipment |
Diamond Paste Honing | Fine finish, sharp edge | Best for small adjustments, not major sharpening |
Maintenance Tips for Sharpening Carbide Inserts
Proper maintenance is crucial for ensuring the longevity and performance of carbide inserts. Here are some tips to keep your inserts in top shape:
- Regular Cleaning: Clean the inserts regularly to remove debris and buildup.
- Proper Storage: Store inserts in a dry, secure place to prevent damage.
- Timely Sharpening: Sharpen inserts as soon as you notice a decrease in performance to avoid excessive wear.
- Use Quality Tools: Invest in high-quality sharpening tools for the best results.
- Monitor Wear: Keep an eye on the wear patterns of your inserts and adjust your sharpening technique accordingly.
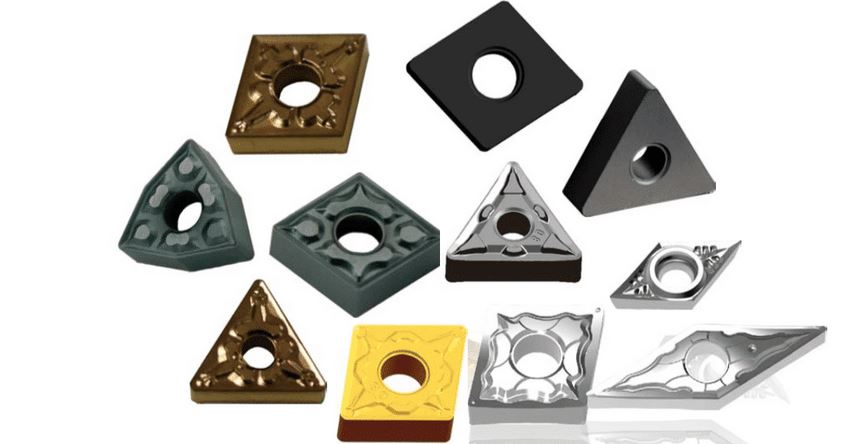
FAQ
Question | Answer |
---|---|
What are carbide inserts used for? | Carbide inserts are used in machining for cutting, turning, milling, and drilling various materials. |
How often should carbide inserts be sharpened? | It depends on the application and material, but generally, when you notice a decline in performance. |
Can I sharpen carbide inserts myself? | Yes, with the right tools and techniques, you can sharpen carbide inserts yourself. |
What is the best method for sharpening carbide inserts? | The best method depends on the insert type and application, but diamond wheel grinding is a versatile and effective option. |
Why do carbide inserts need to be sharpened? | Sharpening maintains their cutting efficiency, extends tool life, and ensures high-quality machining results. |
Conclusion
Sharpening carbide inserts is an essential skill for any machinist. By understanding the different types of inserts, their applications, and the best sharpening techniques, you can ensure your tools remain sharp and efficient. Whether you’re honing with diamond stones or grinding with CBN wheels, the right approach will keep your inserts performing at their best.