Reliable carbide plates are essential in various industries, offering unmatched hardness, strength, and wear resistance. Whether you’re an engineer, manufacturer, or product researcher, understanding the properties, applications, and selection process of carbide plates is crucial.
In this comprehensive guide, we’ll explore everything you need to know about Reliable Carbide Plates, from their raw materials to production processes, properties, applications, and beyond. Let’s dive in!
What is a Reliable Carbide Plate?
A reliable carbide plate is a high-performance material composed primarily of tungsten carbide particles and binder metals like cobalt or nickel. Known for their exceptional durability, carbide plates are widely used for cutting tools, molds, wear parts, and more.
Think of carbide plates as the “superheroes” of engineering materials – they outperform conventional metals in hardness and longevity.
Types of Reliable Carbide Plate
Here’s a detailed table listing the most popular and reliable carbide plate types based on material composition and powder models:
Carbide Plate Model | Composition | Applications | Notable Features |
---|---|---|---|
YG6X | WC + 6% Co | Precision tools, molds | High hardness, wear resistance |
YG8 | WC + 8% Co | Mining tools, mechanical parts | Tougher than YG6X, balanced strength |
YG15 | WC + 15% Co | Heavy-duty tools, wear parts | Higher toughness, reduced hardness |
YN6 | WC + Ni | Corrosion-resistant components | Nickel binder for better resistance |
YC20 | WC + 20% Co | Metal-forming dies | Superior strength for impact loads |
ZP20 | Mixed WC powders | Composite tools, specialty parts | Hybrid performance |
KY10 | WC + Binder | Cutting tools, inserts | Optimized for cutting precision |
T45 | Ultra-fine WC grains | Micro tools, aerospace parts | Extra-fine grains for precision |
KR20 | WC + Rare Metals | Specialty tools | Enhanced wear resistance |
K30 | Cobalt-rich carbide | Tool tips, industrial cutters | Balanced durability and toughness |
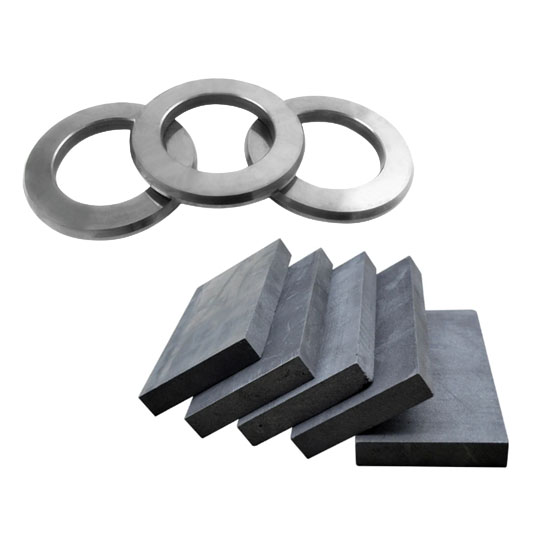
Raw Material and Composition Analysis of Reliable Carbide Plate
Reliable carbide plates are primarily made from tungsten carbide (WC), combined with a binding metal such as cobalt (Co) or nickel (Ni). The key to their outstanding properties lies in this unique combination.
- Tungsten Carbide (WC): Known for its extreme hardness, WC gives carbide plates their wear resistance.
- Cobalt (Co) or Nickel (Ni): These binders provide toughness and impact resistance, balancing the brittleness of WC.
- Micro-Grain Powders: Some advanced models use ultra-fine WC grains to improve precision and performance.
By varying the WC and binder proportions, manufacturers tailor carbide plates to meet specific demands. For instance, plates with higher cobalt content (e.g., YG15) have more toughness, while lower cobalt plates (e.g., YG6X) emphasize hardness.
Applications of Reliable Carbide Plate
Carbide plates are versatile and used across industries where durability and performance are essential. Below is a table outlining their main applications:
Industry | Application | Benefits of Carbide Plate |
---|---|---|
Metalworking | Cutting tools, inserts, molds | High wear resistance, long lifespan |
Mining | Drill bits, wear plates | Durability in abrasive environments |
Aerospace | Precision parts, micro tools | Precision, lightweight applications |
Automotive | Dies, tooling components | High strength and performance |
Oil and Gas | Corrosion-resistant parts | Superior resistance to harsh conditions |
Construction | Cutting tools, saw tips | Toughness for heavy-duty use |
Woodworking | Cutting inserts, blades | Sharpness and long-term reliability |
Electronics | Micro tools, specialty components | Fine-tuned precision |
Imagine a saw blade cutting through metal – carbide plates ensure it stays sharp for longer, reducing downtime and costs.
Production Process Flow of Reliable Carbide Plate
The production of carbide plates involves a meticulous series of steps to ensure their quality and performance:
- Raw Material Selection: High-purity tungsten carbide powder and binder metal are chosen.
- Powder Mixing: WC powder is blended with cobalt or nickel and additives to achieve the desired composition.
- Ball Milling: The mixture is ball-milled to achieve a uniform particle size and distribution.
- Spray Drying: The mixed powder is spray-dried to create granules suitable for pressing.
- Pressing: The granules are pressed into plates using high-pressure dies.
- Sintering: Plates are sintered in a vacuum or hydrogen furnace at temperatures up to 1,400°C to fuse particles.
- Surface Finishing: Plates are ground, polished, and inspected for quality.
The result? A carbide plate that’s tough, hard, and ready for high-performance applications.
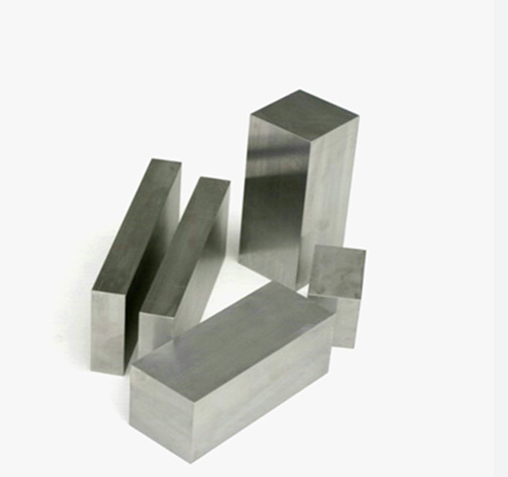
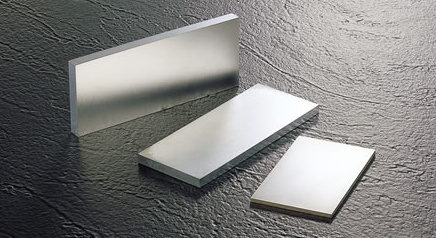
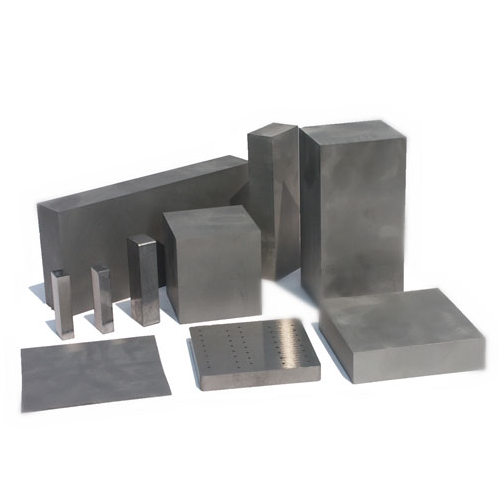
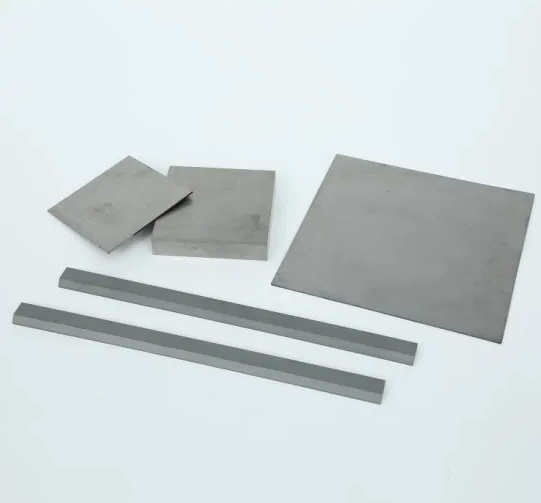
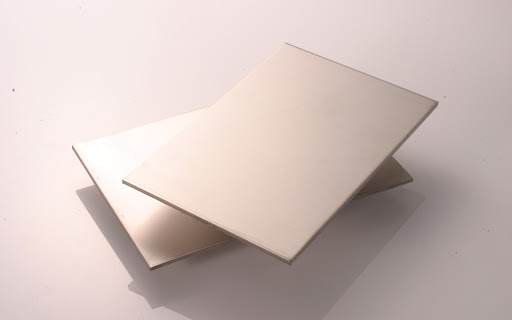
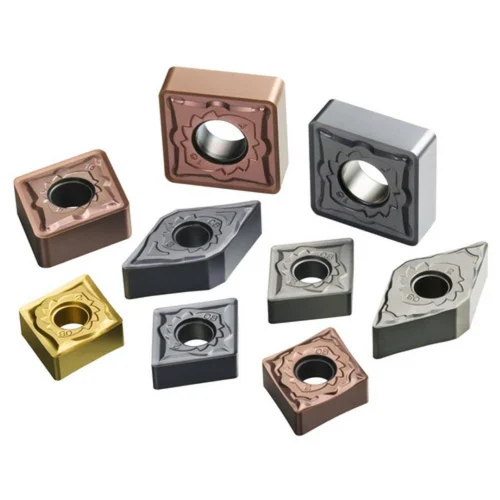
Material Properties of Reliable Carbide Plate
Here are the essential properties that make carbide plates so dependable:
Property | Details |
---|---|
Hardness | HRA 87–92 |
Toughness | Varies based on binder content |
Density | 14.5–15.5 g/cm³ |
Compressive Strength | 4000 MPa – 6000 MPa |
Thermal Conductivity | 70–100 W/m·K |
Wear Resistance | Excellent in abrasive conditions |
Carbide plates are like shields – they endure extreme forces without wearing out.
Composition, Properties, and Characteristics of Reliable Carbide Plate
This table gives an overview of how the composition impacts properties and characteristics:
Model | WC (%) | Binder (%) | Hardness (HRA) | Toughness | Wear Resistance |
---|---|---|---|---|---|
YG6X | 94 | 6 | 91.5 | Moderate | Excellent |
YG8 | 92 | 8 | 89.5 | High | Good |
YG15 | 85 | 15 | 86.5 | Very High | Moderate |
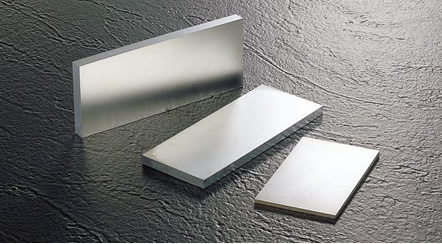
Specifications, Sizes, Shapes, and Standards of Reliable Carbide Plate
Carbide plates are available in a variety of specifications, sizes, and shapes to suit different industrial applications. Manufacturers often adhere to global and regional standards to ensure consistency and performance.
Specification | Details |
---|---|
Sizes | Common sizes range from 50x50mm to 300x300mm. Custom sizes available. |
Thickness | Typically ranges between 1mm and 50mm, depending on the application. |
Shapes | Square, rectangular, circular, or customized to customer specifications. |
Standards | ISO 9001, GB/T 3486-2008, ASTM B777, DIN EN ISO standards. |
Surface Finishing | Ground or unground finish depending on precision needs. |
For instance, rectangular carbide plates are widely used for tooling and wear parts, while circular plates find applications in rotary cutting tools and dies.
Why Standards Matter?
Standards ensure that carbide plates meet performance expectations across industries. For example, plates conforming to ASTM B777 guarantee high-quality sintering and hardness, while those adhering to ISO 9001 ensure consistent manufacturing processes.
Hardness, Strength, and Wear Resistance of Reliable Carbide Plate
Hardness, strength, and wear resistance are the three defining features of carbide plates. Here’s a detailed table to illustrate the key metrics:
Carbide Plate Model | Hardness (HRA) | Compressive Strength (MPa) | Wear Resistance |
---|---|---|---|
YG6X | 91.5 | 5500 | Excellent |
YG8 | 89.5 | 5200 | Very Good |
YG15 | 86.5 | 4800 | Moderate |
YN6 | 90.0 | 5400 | High (corrosion-resistant) |
T45 | 92.0 | 6000 | Exceptional |
- Hardness: Determines resistance to scratching, cutting, and deformation.
- Strength: Defines how well the material can withstand forces without breaking.
- Wear Resistance: Ensures longevity under abrasive or harsh conditions.
For instance, YG6X plates with a hardness of 91.5 HRA are ideal for wear-heavy environments like metalworking tools.
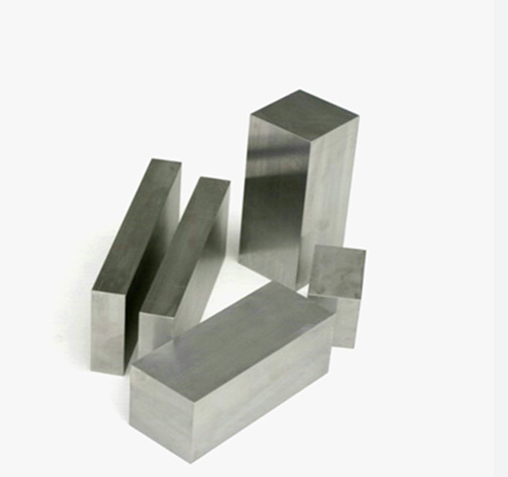
Choosing a Reliable Carbide Plate Supplier and Pricing Details
Selecting the right carbide plate supplier is critical for ensuring performance, consistency, and affordability. Here’s a comprehensive guide to help you make the right choice:
Criteria | Details to Evaluate |
---|---|
Material Quality | Ensure the supplier uses high-purity tungsten carbide and reliable binders. |
Certifications | Look for ISO, ASTM, or DIN certifications to confirm manufacturing standards. |
Customization | Choose suppliers offering customized sizes, shapes, and compositions. |
Delivery Times | Evaluate lead times for orders, especially for custom requirements. |
Pricing | Compare prices, ensuring they align with quality and specifications. |
Customer Support | Assess communication, technical support, and after-sales service. |
Pricing Details of Reliable Carbide Plate
The cost of carbide plates can vary based on composition, size, and quantity. Here’s a rough estimate:
Specification | Price Range (USD per kg) |
---|---|
Standard YG6X Plate | $40–$60 |
High-Cobalt Plate (e.g., YG15) | $50–$70 |
Ultra-Fine Grain Plate | $60–$90 |
Custom Specifications | Varies based on order |
For bulk orders, suppliers often provide discounts or flexible pricing. Always compare quotes and verify quality guarantees before purchasing.
Selecting the Best Reliable Carbide Plate for Your Needs
Choosing the right carbide plate involves matching the product’s properties to your specific application. Follow this table for guidance:
Selection Criteria | Recommended Carbide Plate |
---|---|
High Wear Resistance | YG6X, T45 |
High Toughness | YG15, YC20 |
Corrosion Resistance | YN6, plates with nickel binders |
Precision Applications | T45, KY10, ultra-fine grain carbide plates |
Heavy-Duty Applications | YG8, YC20 |
Cost-Sensitive Applications | Standard YG8 plates for balanced performance |
Pro Tip:
For applications like mining tools, choose high-toughness plates like YG15. For precision cutting tools, go for ultra-fine grain carbide like T45.
Advantages and Limitations of Reliable Carbide Plate
Here’s a comparison of the benefits and drawbacks:
Advantages | Limitations |
---|---|
Exceptional Hardness and Wear Resistance | Can be brittle under high-impact loads |
High Thermal Conductivity | More expensive than conventional steels |
Long Service Life | Requires specialized tools for machining |
Customizable Properties | Heavyweight compared to aluminum or plastics |
Corrosion and Abrasion Resistant | Limited ductility in certain compositions |
Carbide plates are perfect where durability is critical, but in applications requiring flexibility, alternative materials may be considered.
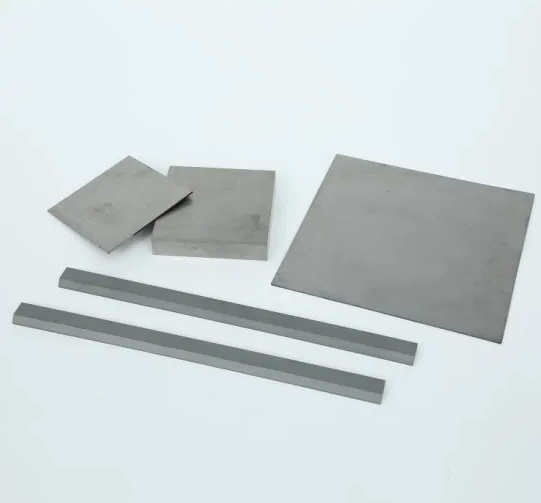
FAQs
Question | Answer |
---|---|
What is the lifespan of carbide plates? | With proper use, carbide plates can last 5–10 times longer than steel in wear conditions. |
Can carbide plates be customized? | Yes, most manufacturers offer customized sizes, shapes, and compositions. |
What industries use carbide plates the most? | Industries like metalworking, mining, construction, and aerospace rely heavily on them. |
How are carbide plates maintained? | Regular cleaning and proper usage prevent premature wear and extend their lifespan. |
Why are carbide plates expensive? | Their high manufacturing cost and premium materials like tungsten carbide increase pricing. |
Conclusion
Reliable carbide plates are indispensable in modern industries due to their unmatched hardness, strength, and wear resistance. Whether you need them for cutting tools, molds, or wear components, choosing the right model, composition, and supplier is essential for optimal results.
By understanding their production process, material properties, and applications, you can make informed decisions tailored to your needs. From YG6X to ultra-fine grain plates, carbide solutions offer unparalleled durability and performance.
When you invest in carbide plates, you’re not just buying a material – you’re ensuring efficiency, productivity, and long-term savings. Now, go ahead and make the smart choice for your industry needs!