Overview
When it comes to precision machining, selecting the right tools can make a world of difference. One such crucial tool is the PVD coated carbide insert. These inserts are pivotal in enhancing the efficiency, precision, and longevity of machining processes. But what makes them so special? How do they compare to other options? And how can you choose the best one for your specific needs? In this extensive guide, we’ll dive deep into everything you need to know about PVD coated carbide inserts, from their composition and properties to applications and selection criteria.
What are PVD Coated Carbide Inserts?
PVD, or Physical Vapor Deposition, coated carbide inserts are cutting tools used in various machining operations. The PVD process involves the deposition of thin, hard coating materials onto carbide substrates. This coating enhances the performance of the inserts by providing superior hardness, wear resistance, and heat resistance, thereby extending the tool’s life and improving the quality of the machined product.
Key Features of PVD Coated Carbide Inserts
- Increased Hardness: The PVD coating significantly increases the surface hardness of the carbide insert, making it more resistant to wear and deformation.
- Enhanced Wear Resistance: The coating reduces the wear rate of the insert, ensuring consistent performance over a longer period.
- Improved Heat Resistance: PVD coatings can withstand high temperatures, making these inserts ideal for high-speed machining.
- Reduced Friction: The smooth, hard coating reduces friction between the insert and the workpiece, improving the quality of the machined surface.
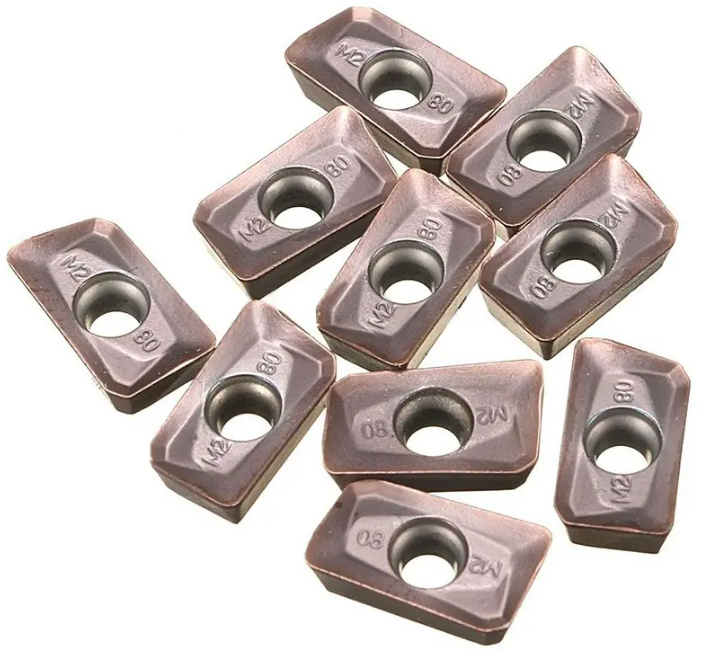
Types of PVD Coated Carbide Inserts
Model | Description |
---|---|
TNMG 160404-PF | General-purpose insert for steel, stainless steel, and cast iron with excellent wear resistance and durability. |
CNMG 120408-MF | Ideal for finishing and semi-finishing of steel and stainless steel, offering high precision and surface quality. |
DNMG 150608-PF | Suitable for high-speed turning of steel and cast iron, providing excellent chip control and wear resistance. |
WNMG 080404-MF | Versatile insert for a wide range of materials, including steel, stainless steel, and high-temperature alloys. |
SNMG 120408-QM | Designed for roughing and finishing operations on stainless steel and steel, ensuring high performance and tool life. |
VNMG 160404-MF | Precision insert for fine finishing of steel and stainless steel, delivering superior surface finish and accuracy. |
CCMT 09T304-PF | Perfect for small component machining, providing excellent edge stability and wear resistance. |
DCMT 11T304-MF | Ideal for high-precision turning of small parts, offering excellent chip control and surface finish. |
SCMT 09T304-PF | Designed for medium to rough turning of steel and stainless steel, providing long tool life and stability. |
RCMT 10T3MO | Used for roughing and semi-finishing of cast iron and non-ferrous metals, offering high wear resistance. |
Applications of PVD Coated Carbide Inserts
Application | Description |
---|---|
Steel Machining | Ideal for high-speed and precision machining of various steel grades. |
Stainless Steel Machining | Offers excellent performance in machining stainless steel with reduced wear and longer tool life. |
Cast Iron Machining | Suitable for roughing and finishing cast iron, providing high durability and wear resistance. |
Non-Ferrous Metal Machining | Excellent for machining aluminum, copper, and other non-ferrous metals with minimal tool wear. |
High-Temperature Alloys | Perfect for machining superalloys, titanium, and other high-temperature materials. |
Material Properties
Property | Description |
---|---|
Hardness | Enhanced surface hardness due to the PVD coating, typically above 2000 HV. |
Toughness | Maintains core toughness of carbide substrate, ensuring resistance to chipping and breaking. |
Wear Resistance | Superior wear resistance compared to uncoated or conventionally coated inserts. |
Heat Resistance | Capable of withstanding high temperatures, making them suitable for high-speed machining. |
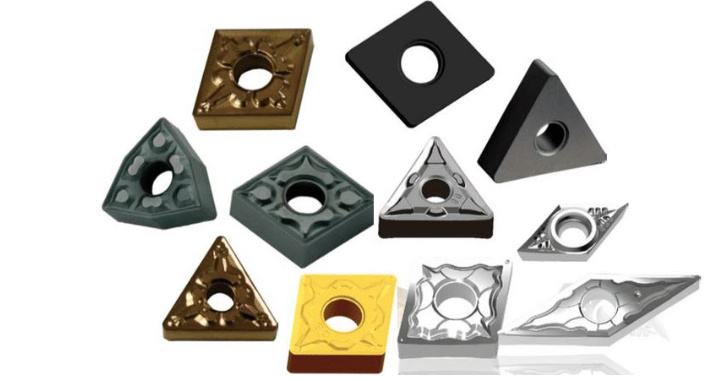
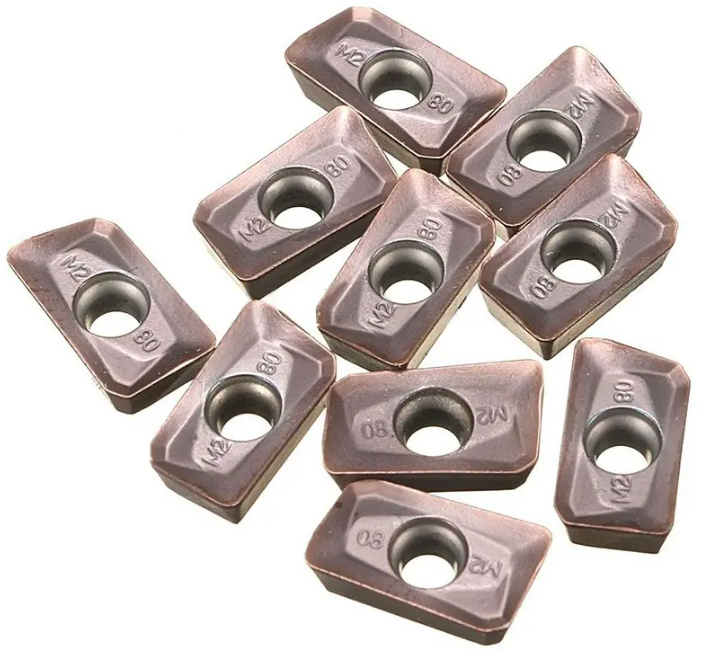
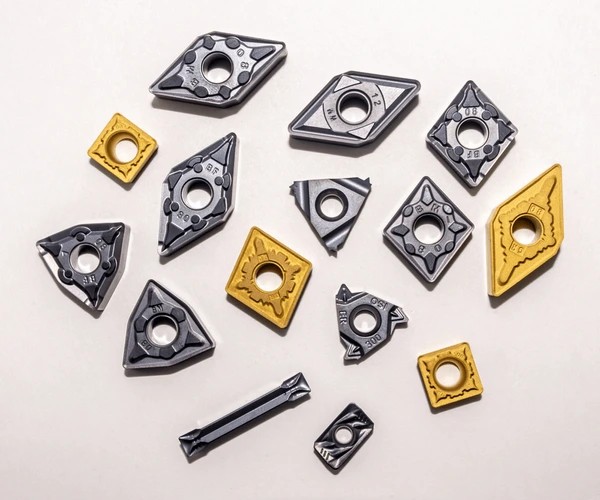
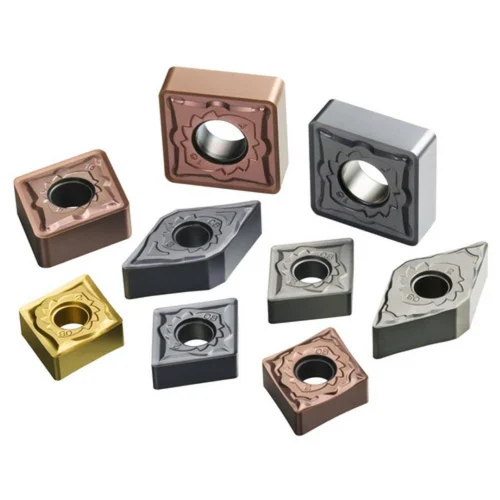
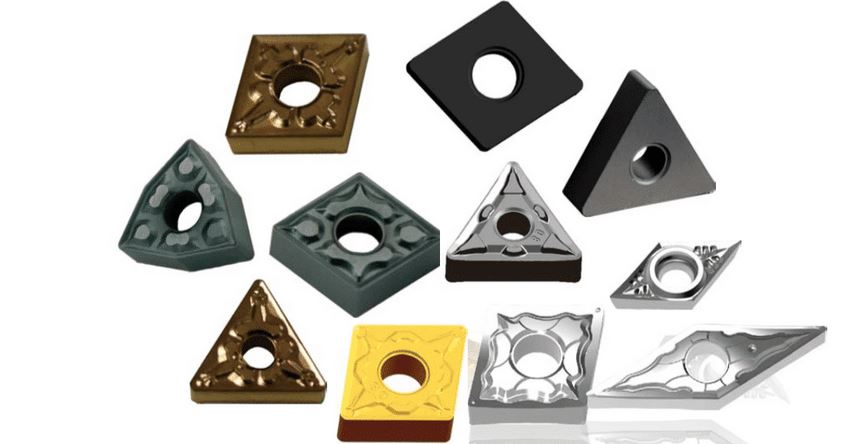
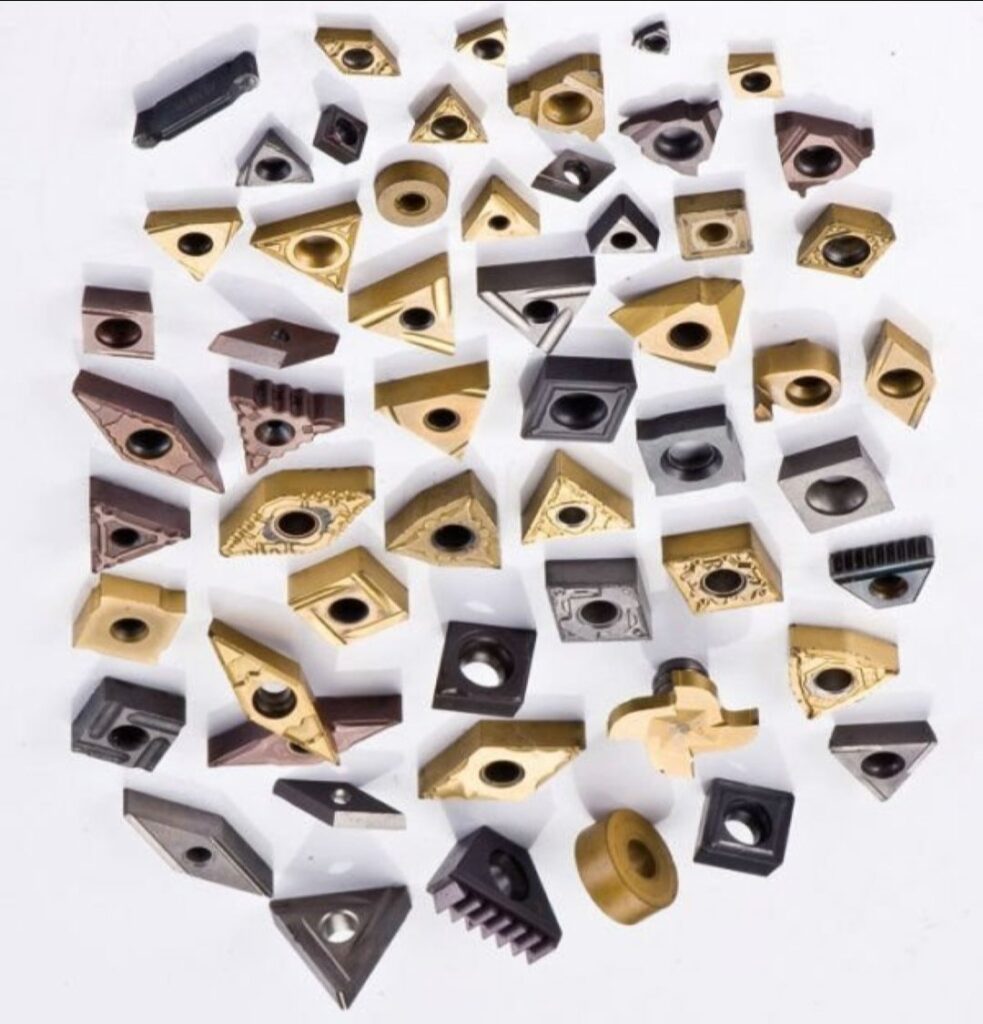
Composition, Properties, and Characteristics
Component | Properties | Characteristics |
---|---|---|
Carbide Substrate | High toughness and hardness, providing a strong base for the PVD coating. | Ensures durability and resistance to mechanical stress. |
PVD Coating | Thin, hard layer of materials like TiN, TiAlN, or AlCrN, offering excellent wear resistance. | Reduces friction, increases wear resistance, and enhances heat resistance. |
Binder Phase | Typically cobalt or nickel, which binds the carbide grains together. | Maintains the toughness and structural integrity of the insert. |
Hardness, Strength, and Wear Resistance
Parameter | Description |
---|---|
Hardness (HV) | Typically ranges from 2000 to 3000 HV, depending on the coating material. |
Flexural Strength | High flexural strength, ensuring the insert can withstand mechanical stresses during machining. |
Wear Resistance | Superior wear resistance, significantly extending tool life compared to uncoated inserts. |
Specifications, Sizes, Shape, and Standards
Specification | Description |
---|---|
ISO Standards | Inserts conform to ISO standards, ensuring compatibility and performance. |
Sizes | Available in various sizes to suit different machining needs and tool holders. |
Shapes | Common shapes include triangular, square, diamond, round, and parallelogram. |
Suppliers and Pricing Details
Supplier | Product Range | Price Range |
---|---|---|
Sandvik Coromant | Wide range of PVD coated carbide inserts for various applications. | $10 – $50 per insert, depending on specifications. |
Kennametal | High-performance inserts with advanced PVD coatings for different materials. | $12 – $55 per insert, depending on specifications. |
Seco Tools | Comprehensive selection of inserts with optimized PVD coatings for different machining tasks. | $11 – $48 per insert, depending on specifications. |
Mitsubishi Materials | Innovative inserts with superior PVD coatings for enhanced performance. | $13 – $60 per insert, depending on specifications. |
Kyocera | Versatile PVD coated inserts for a wide range of materials and applications. | $9 – $45 per insert, depending on specifications. |
How to Select the Right PVD Coated Carbide Inserts
Consideration | Description |
---|---|
Material to be Machined | Choose inserts based on the material you are machining (e.g., steel, stainless steel, cast iron). |
Machining Operation | Determine whether you need inserts for roughing, finishing, or semi-finishing operations. |
Cutting Speed | Select inserts that can withstand the cutting speeds required for your application. |
Tool Holder Compatibility | Ensure the inserts are compatible with your existing tool holders and machinery. |
Cost and Budget | Consider the cost-effectiveness of the inserts, balancing performance with budget constraints. |
Advantages and Limitations of PVD Coated Carbide Inserts
Aspect | Advantages | Limitations |
---|---|---|
Durability | Significantly longer tool life compared to uncoated inserts. | Initial cost may be higher than uncoated or conventionally coated inserts. |
Performance | Superior performance in high-speed and precision machining. | May require specific tool holders or machinery for optimal performance. |
Cost | Cost-effective over time due to reduced tool replacement and downtime. | Higher upfront cost. |
Versatility | Suitable for a wide range of materials and machining operations. | Not all PVD coatings are suitable for all materials; specific coatings needed for specific applications. |
FAQs
Question | Answer |
---|---|
What is the main advantage of PVD coated carbide inserts? | They offer enhanced hardness, wear resistance, and heat resistance, resulting in longer tool life. |
Can PVD coated inserts be used for all materials? | While versatile, specific coatings are optimized for particular materials like steel, stainless steel, or cast iron. |
How do I choose the right insert for my application? | Consider factors like material to be machined, type of operation, cutting speed, and tool holder compatibility. |
Are PVD coated inserts more expensive than uncoated ones? | They have a higher initial cost but are more cost-effective over time due to reduced wear and longer tool life. |
Can PVD coated inserts improve machining quality? | Yes, they reduce friction and wear, leading to better surface finishes and dimensional accuracy. |
Conclusion
Selecting the right PVD coated carbide inserts can significantly impact the efficiency, quality, and cost-effectiveness of your machining operations. By understanding the different types, applications, and properties of these inserts, you can make an informed decision that will enhance your manufacturing processes. Whether you’re machining steel, stainless steel, cast iron, or non-ferrous metals, there’s a PVD coated insert that can meet your needs and exceed your expectations.