- Property of Carbide
Carbide, specifically tungsten carbide, possesses several properties that make it a desirable material in various industrial applications. Here are some key properties of carbide:
Contact us and Explore More About tungsten carbide
- Wear-resistance
Wear resistance is the most important property for cemented carbide. When two surfaces rub against each other, material is removed gradually from both of them. For cemented carbide parts, the wear mechanism is normally is abrasive wear which is defined as the loss of material due to hard particles or hard protuberances. The concept of wear is very complex and depends on many variables. Wear resistance is mainly tested using the ASTM B611 method. For cemented carbide parts, wear resistance increases with finer grain and lower cobalt content, as shown in the right figure.
The concept of wear is very complex and depends on many variables. Wear resistance is mainly tested using the ASTM B611-85 method.As shown pic beside, wear resistance increases with the finer the grain and the lower the cobalt content for cemented carbide parts.
- Hardness
In material science, hardness is a measure of the resistance to localized plastic deformation induced by either mechanical indentation or abrasion. For cemented carbide, the hardness is normally determined based on the Vickers hardness test according to ISO 3878. Another method for determining hardness of cemented carbide is the Rockwell procedure Scale A (ISO 3738). Both of them use a diamond indenter. There is no theoretical formula for a conversion between the two procedures. In order to create a comparison a determinate test must be carried out. Hardness, like wear resistance, also increases with a smaller grain size and lower cobalt content (see below left figure). Wear resistance and hardness show similar behaviour with regard to cobalt content and grain size, so hardness is often used as a reference for wear resistance. Nevertheless the relation of hardness and wear resistance is exponential and also depends on the grain size (see below right figure).
- Toughness
When a material is exposed to external static or dynamic stress, in many cases, particularly with impact loads, both the strength and ductility of the material have to be taken into account. These two properties determine the toughness, which is defined as the capacity to resist fracture or crack propagation. There are numerous methods to define toughness value, such as transverse rupture strength or fracture toughness.
In the case of carbide, the transverse rupture strength frequently is applied to determine the toughness according to the standard ISO 3327. A test material of a certain length is placed on a surface and put under stress in the middle until it breaks (see below figure). The transverse rupture strength (T.R.S.) is then the average value of several tests.
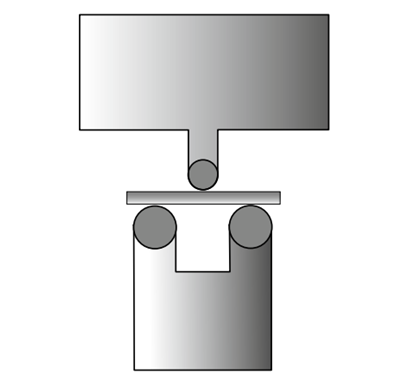
Normally, the maximum value is achieved with a cobalt content around 14 wt% and grain size around 0.2 – 0.8µm. Toughness of cemented carbides increases with the metal binder content and growing grain size. But the transverse rupture strength is decisively influenced by the number and size of defects in the structure or on the surface. Fractures always occur at the weakest point of the structure, which is also where the largest defect is. A high number of defects therefore increases the probability of fracture.
As the quality demands in the field of carbide manufacturing are high, impurities or defects can be minimized and thus the risk of breakage reduced.
Compared to other metal materials, cemented carbide can be considered as the part with lower toughness. For this purpose of the ease, the crack length & size of a Vickers hardness indent is used to deduce the fracture toughness (see below left figure).
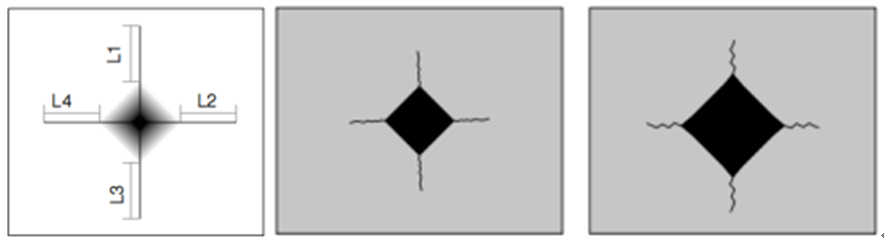
By definition, carbide is to be considered a brittle material as there is basically no plastic deformation prior to fracture. Sometimes we can compare the toughness bymicrostructure examination of surfaces where breakage occurred. Various carbidesshow very big differences in terms of toughness by taking a look at the microstructure, such as showed in below figures. Larger crack propagation means higher fracture toughness, and shorter crack propagation means lower toughness. See below figures.