In the world of industrial manufacturing and machining, precision and durability are paramount. One component that exemplifies these qualities is the precision-machined hardmetal buttons. These buttons are essential in a variety of applications, from mining and drilling to machinery and tooling. This blog will explore the fascinating world of precision-machined hardmetal buttons, highlighting their design, applications, advantages, and why they are a critical component in modern industry.
Understanding Precision-Machined Hardmetal Buttons
What Are Hardmetal Buttons?
Hardmetal buttons, often referred to as carbide buttons, are small, robust components made from tungsten carbide or similar hard materials. These buttons are renowned for their exceptional hardness, wear resistance, and ability to maintain sharpness under extreme conditions.
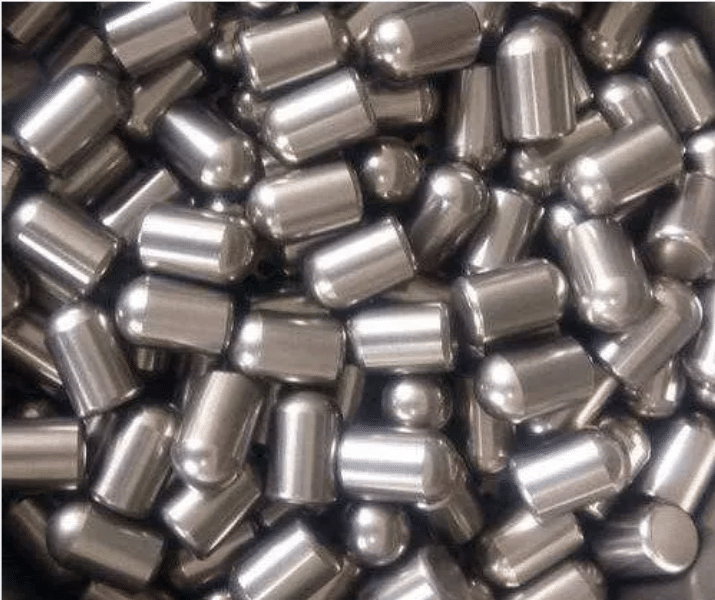
Precision Machining: Why It Matters
Precision machining involves the meticulous shaping and finishing of hardmetal buttons to exact specifications. This process ensures that the buttons meet stringent quality standards and perform reliably in their intended applications.
Key Attributes of Precision-Machined Hardmetal Buttons
- High Hardness: Ensures durability and resistance to deformation.
- Wear Resistance: Extends the operational life of the button.
- Dimensional Accuracy: Guarantees a perfect fit and optimal performance in assemblies.
- Surface Finish: Reduces friction and enhances performance.
Applications of Precision-Machined Hardmetal Buttons
Mining and Drilling
In mining and drilling operations, hardmetal buttons are used in drill bits and cutting tools. Their high hardness and wear resistance allow them to cut through rock, ore, and other tough materials efficiently.
Machinery and Tooling
Precision-machined hardmetal buttons are integral to various machinery and tooling applications. They are used in components that require high precision and durability, such as bearings, valves, and cutting tools.
Aerospace and Automotive
In the aerospace and automotive industries, these buttons are used in components that must withstand extreme conditions and high wear, such as turbine blades and engine parts.
Oil and Gas
In the oil and gas sector, hardmetal buttons are used in drilling equipment and valves that operate under high pressure and abrasive conditions.
Advantages of Precision-Machined Hardmetal Buttons
Choosing precision-machined hardmetal buttons offers several significant advantages:
- Enhanced Performance: The high hardness and wear resistance of hardmetal button ensure superior performance in demanding applications.
- Longevity: These buttons have a longer operational life, reducing the need for frequent replacements.
- Cost-Effectiveness: Despite their higher initial cost, the durability and longevity of hardmetal button make them a more cost-effective choice in the long run.
- Reliability: Precision machining ensures that each button meets exact specifications, providing consistent and reliable performance.
Performance Comparison
To better understand the benefits of precision-machined hardmetal button, let’s compare them with standard steel buttons:
Attribute | Hardmetal Buttons | Standard Steel Buttons |
---|---|---|
Hardness | Very High | Moderate |
Wear Resistance | Excellent | Good |
Operational Life | Long | Short |
Cost | Higher Initial Cost | Lower Initial Cost |
Maintenance Frequency | Low | High |
Dimensional Accuracy | High | Variable |
Key Factors in Choosing Precision-Machined Hardmetal Buttons
When selecting hardmetal button for your application, consider the following factors to ensure optimal performance:
- Material: Choose a hardmetal composition that matches the demands of your application.
- Size and Shape: Ensure the buttons are machined to the precise dimensions and shape required.
- Coating: Consider if a coating is needed to enhance performance, such as reducing friction or increasing wear resistance.
- Application Environment: Take into account the operating conditions, such as temperature, pressure, and abrasive wear.
Selection Checklist
Here’s a quick checklist to help you choose the right precision-machined hardmetal button:
- Material Compatibility: Verify that the button material is suitable for the application.
- Dimensional Accuracy: Ensure the button meets the required size and shape specifications.
- Coating Requirements: Determine if a coating is necessary for enhanced performance.
- Environmental Conditions: Consider the operating conditions the button will be exposed to.
Innovative Manufacturing Techniques for Hardmetal Buttons
Advancements in manufacturing techniques have significantly improved the quality and performance of precision-machined hardmetal buttons. Some of these techniques include:
- Powder Metallurgy: This process involves pressing and sintering powdered materials to create a dense and uniform hardmetal button.
- CNC Machining: Computer Numerical Control (CNC) machining allows for high precision and repeatability in manufacturing hardmetal button.
- Coating Technologies: Advanced coatings, such as PVD (Physical Vapor Deposition) and CVD (Chemical Vapor Deposition), enhance the performance and longevity of hardmetal button.
Benefits of Advanced Manufacturing Techniques
- Higher Precision: Ensures each button is produced to exact specifications.
- Improved Performance: Enhances the hardness, wear resistance, and overall performance of the buttons.
- Consistency: Guarantees uniform quality across large production runs.
Real-World Success Stories
Case Study 1: Mining Industry
A mining company faced frequent tool replacements due to wear and breakage. By switching to precision-machined hardmetal button, they experienced:
- Increased Tool Life: Tools lasted significantly longer, reducing downtime.
- Enhanced Efficiency: Improved cutting performance led to faster drilling speeds.
- Cost Savings: Reduced the frequency of tool replacements, saving on costs.
Case Study 2: Automotive Manufacturing
An automotive manufacturer utilized precision-machined hardmetal button in their engine components. The results included:
- Improved Durability: Components withstood high temperatures and pressures better.
- Consistent Quality: Precision machining ensured uniform performance across all components.
- Reduced Maintenance: Longer-lasting components required less frequent maintenance.
Maximizing the Performance of Precision-Machined Hardmetal Buttons
To get the most out of your precision-machined hardmetal button, follow these expert tips:
- Regular Inspection: Frequently inspect the buttons for signs of wear or damage.
- Proper Use: Use the buttons within their specified operational parameters to avoid premature wear.
- Maintenance: Clean and store the buttons properly to prevent contamination and damage.
Maintenance Checklist
Here’s a quick checklist for maintaining your precision-machined hardmetal button:
- Inspect Regularly: Check for wear or damage after each use.
- Clean Thoroughly: Remove any debris or residue to maintain performance.
- Store Properly: Keep buttons in a clean, dry environment to prevent corrosion.
Frequently Asked Questions (FAQs)
1. What makes precision-machined hardmetal buttons different from standard hardmetal buttons?
Precision-machined hardmetal button undergo rigorous shaping and finishing processes to meet exact specifications. This precision ensures higher performance, reliability, and longer operational life compared to standard hardmetal button, which might not be as meticulously crafted.
2. Can hardmetal buttons be used in high-temperature environments?
Yes, hardmetal button are designed to withstand extreme conditions, including high temperatures. This makes them suitable for use in demanding industries such as aerospace and automotive, where components are exposed to intense heat.
3. How do I choose the right hardmetal button for my application?
When selecting a hardmetal button, consider the material composition, size, shape, coating needs, and the specific operating conditions of your application. Ensuring compatibility with these factors will help you choose the most suitable button.
4. Are there any maintenance requirements for hardmetal buttons?
Regular maintenance can extend the life of hardmetal button. This includes frequent inspections for wear or damage, thorough cleaning to remove debris, and proper storage in a clean, dry environment to prevent corrosion.
5. What advancements in manufacturing techniques have improved hardmetal buttons?
Innovations such as powder metallurgy, CNC machining, and advanced coating technologies have significantly enhanced the precision, performance, and consistency of hardmetal button. These techniques ensure that each button meets exact specifications and performs reliably in demanding applications.
Conclusion
Precision-machined hardmetal button are indispensable components in a variety of industrial applications, offering unmatched performance and longevity. Their high hardness, wear resistance, and precision make them ideal for demanding environments such as mining, drilling, machinery, aerospace, automotive, and oil and gas industries.