Welcome to the world of polished carbide inserts! If you’re here, you’re probably looking to dive deep into the nuances of this highly specialized yet essential tool. Whether you’re a seasoned machinist or just getting started, this guide will help you navigate the intricate details of polished carbide inserts, from their types to their applications, properties, and how to select the right one for your needs.
Overview of Polished Carbide Inserts
Polished carbide inserts are a critical component in the manufacturing industry, primarily used in cutting, machining, and drilling operations. These inserts are known for their exceptional hardness, wear resistance, and ability to maintain a sharp edge under extreme conditions. Polished carbide inserts are made from a composite material, mainly tungsten carbide, with other metal powders added to enhance specific properties.
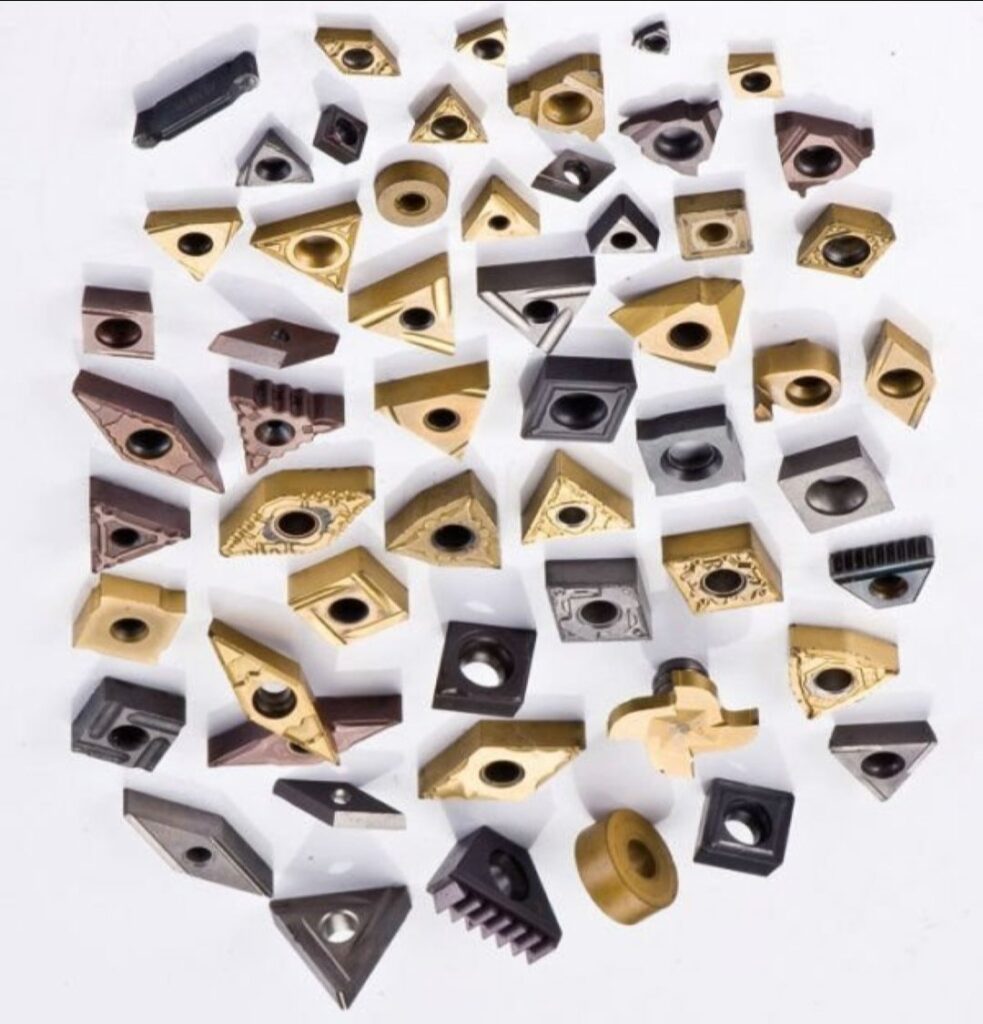
Types of Polished Carbide Inserts
Polished carbide inserts come in various shapes and sizes, each designed for a specific type of machining operation. Let’s take a closer look at the different types and their unique features.
Type | Description |
---|---|
Turning Inserts | Used for turning operations, available in various shapes like square, triangular, and rhomboid. |
Milling Inserts | Designed for milling applications, these inserts come in rectangular and square shapes. |
Drilling Inserts | Specifically made for drilling operations, typically cylindrical or bullet-shaped. |
Grooving Inserts | Used for creating grooves and cut-offs, often in a rectangular or rounded shape. |
Threading Inserts | Designed for threading operations, usually triangular with sharp points. |
Boring Inserts | Made for boring operations, these are often cylindrical or round in shape. |
Parting Inserts | Used for parting or cutting off material, typically narrow and rectangular. |
Profiling Inserts | Designed for contouring and profiling, available in various shapes. |
Face Milling Inserts | Used for face milling operations, often square or round. |
Chamfering Inserts | Specifically designed for chamfering, typically in a diamond or triangular shape. |
Applications of Polished Carbide Inserts
Polished carbide inserts are utilized in a wide range of applications due to their versatility and durability. Here are some common applications:
Application | Description |
---|---|
Automotive Industry | Used for machining engine parts, transmission components, and other critical automotive parts. |
Aerospace Industry | Essential for manufacturing high-precision components like turbine blades and aircraft structures. |
Medical Device Manufacturing | Used in the production of surgical instruments and implants. |
Oil and Gas Industry | Vital for drilling and machining parts used in exploration and extraction equipment. |
Metalworking | Employed in general metal cutting, shaping, and forming processes. |
Tool and Die Making | Crucial for creating molds, dies, and other precision tools. |
Woodworking | Utilized in cutting and shaping wood materials. |
Plastic and Composite Machining | Used for machining plastic and composite materials in various industries. |
Jewelry Making | Employed in the precise cutting and shaping of precious metals and stones. |
Heavy Machinery Manufacturing | Essential for machining large and heavy components for industrial machinery. |
Material Properties of Polished Carbide Inserts
Understanding the material properties of polished carbide inserts is crucial for selecting the right type for your application. Here’s a detailed look at their properties:
Property | Description |
---|---|
Hardness | Exceptional hardness, typically ranging from 85 to 92 HRA. |
Toughness | High toughness, allowing them to withstand significant stress and impact. |
Wear Resistance | Superior wear resistance, extending tool life and maintaining sharpness. |
Thermal Stability | Excellent thermal stability, capable of performing at high temperatures without degrading. |
Chemical Resistance | High resistance to chemical reactions, ensuring longevity in corrosive environments. |
Edge Retention | Outstanding edge retention, maintaining a sharp cutting edge for extended periods. |
Density | High density, typically around 15 g/cm³, contributing to their durability and strength. |
Flexural Strength | High flexural strength, preventing breakage and deformation under load. |
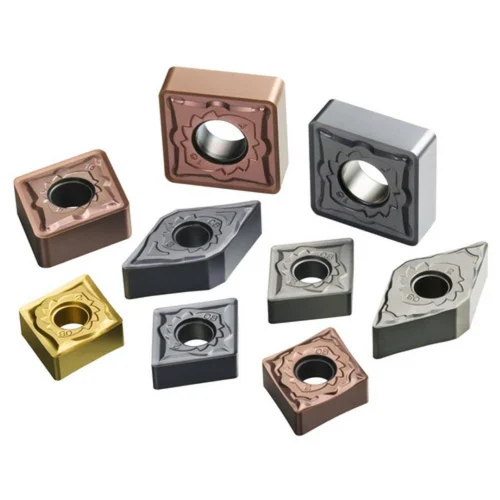
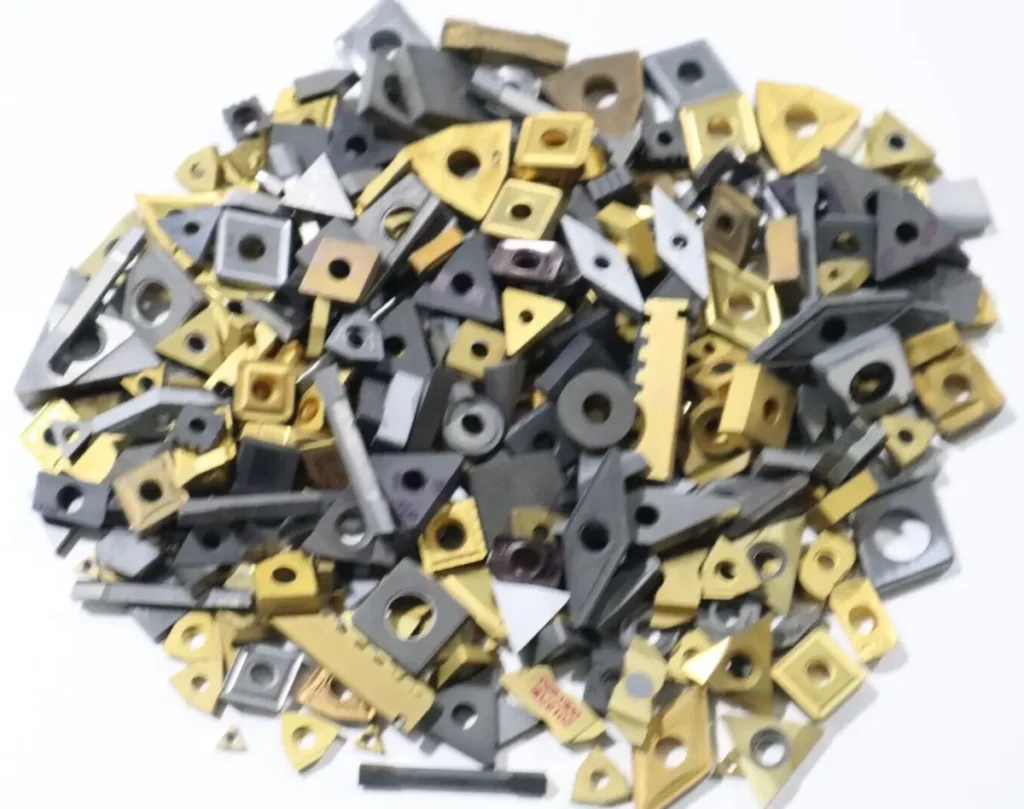
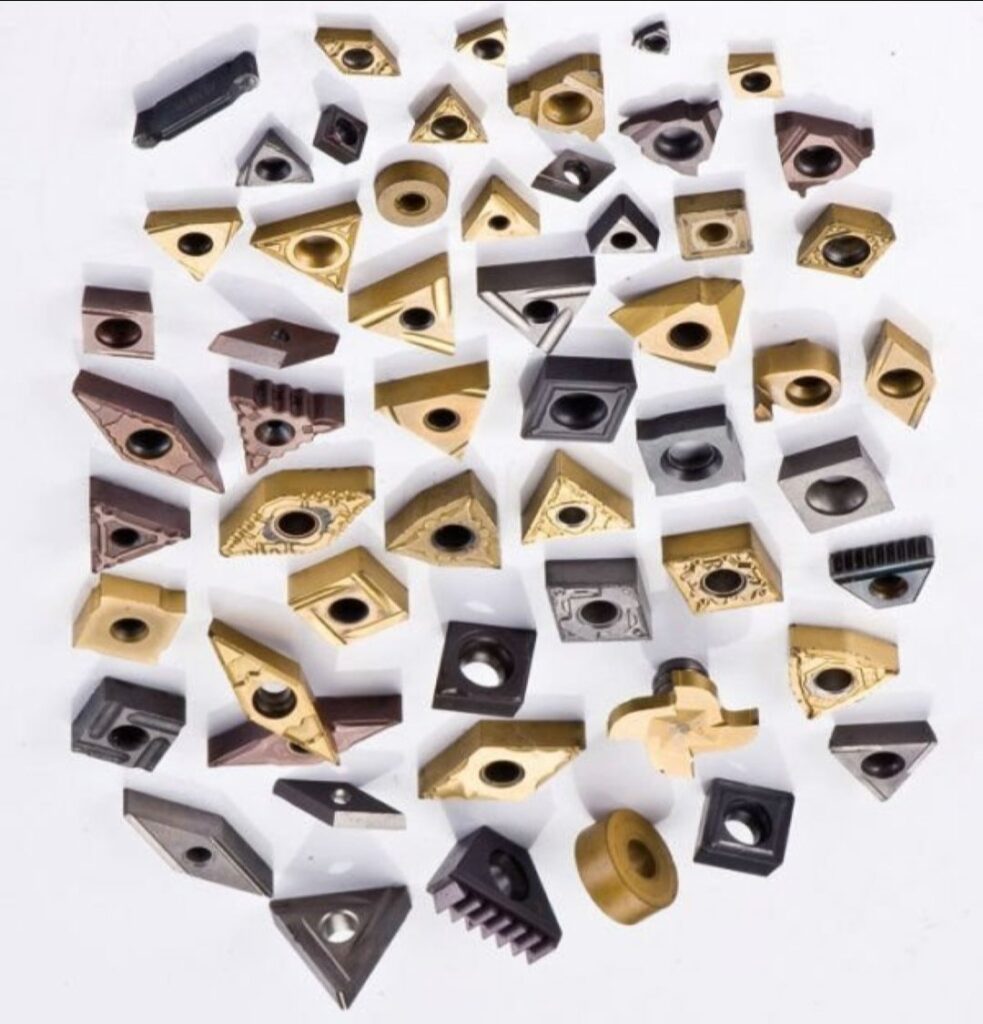
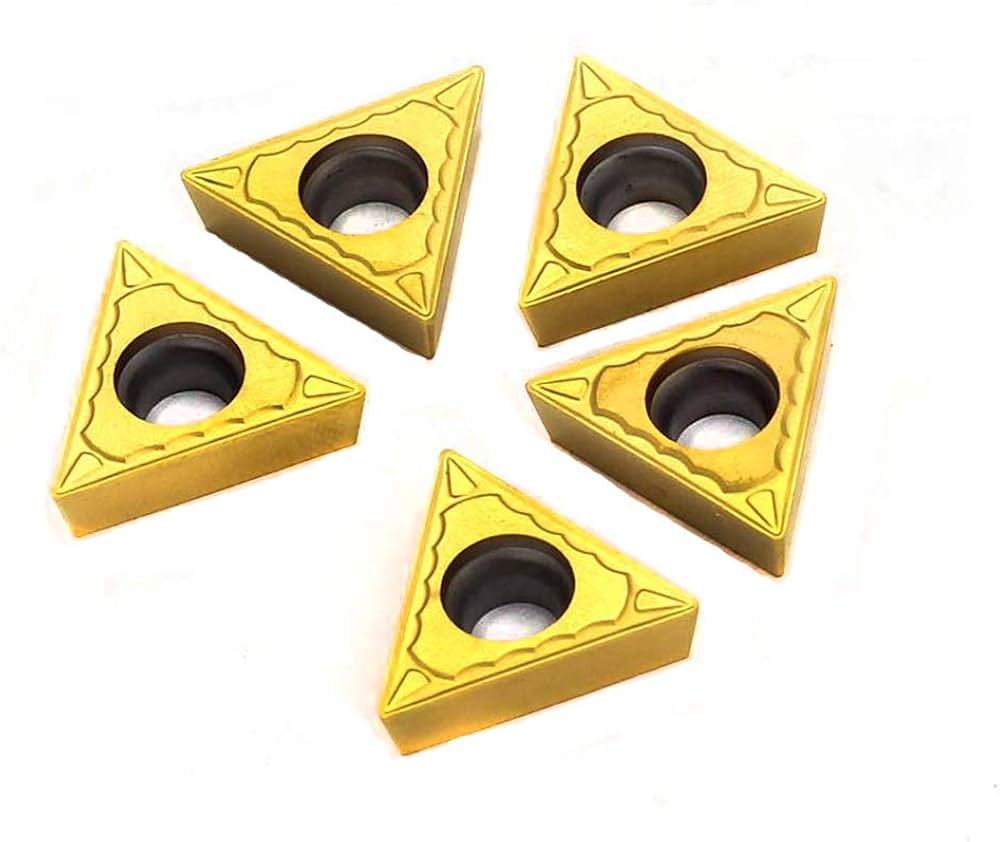
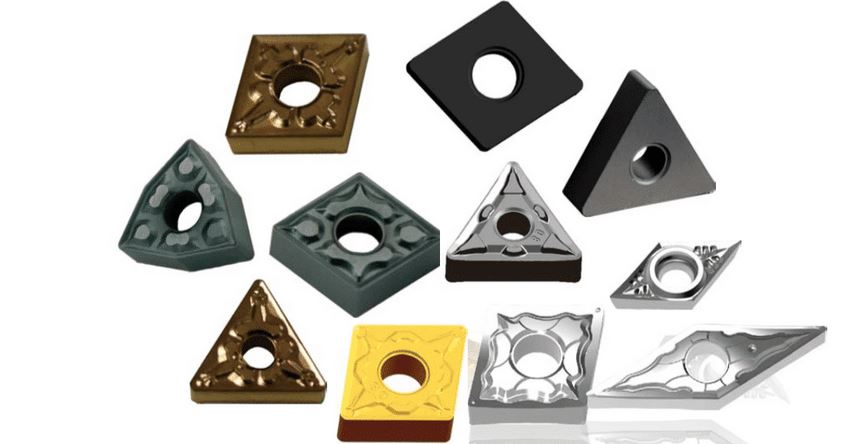
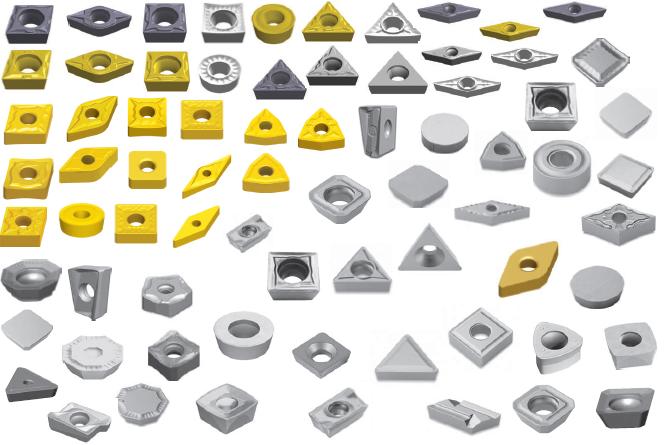
Composition of Polished Carbide Inserts
The composition of polished carbide inserts is what gives them their unique properties. Let’s delve into the specific materials used:
Component | Description |
---|---|
Tungsten Carbide (WC) | The primary component, providing hardness and wear resistance. |
Cobalt (Co) | Used as a binder, adding toughness and strength. |
Titanium Carbide (TiC) | Enhances wear resistance and thermal stability. |
Tantalum Carbide (TaC) | Improves toughness and resistance to thermal shock. |
Niobium Carbide (NbC) | Adds hardness and wear resistance. |
Chromium Carbide (CrC) | Increases corrosion resistance and hardness. |
Nickel (Ni) | Sometimes used as an alternative binder, providing toughness. |
Vanadium Carbide (VC) | Enhances wear resistance and strength. |
Other Additives | Various other elements can be added to tailor specific properties for different applications. |
Hardness, Strength, and Wear Resistance of Polished Carbide Inserts
One of the key reasons for using polished carbide inserts is their exceptional hardness, strength, and wear resistance. Here’s how these properties compare:
Property | Typical Value |
---|---|
Hardness (HRA) | 85-92 |
Flexural Strength (MPa) | 2000-3000 |
Compressive Strength (MPa) | 4000-6000 |
Fracture Toughness (MPa·m^1/2) | 6-10 |
Wear Resistance | Extremely high, with wear rates significantly lower compared to other materials. |
Specifications, Sizes, Shapes, and Standards of Polished Carbide Inserts
Polished carbide inserts are available in a variety of specifications, sizes, shapes, and standards. Here’s a detailed breakdown:
Specification | Description |
---|---|
Sizes | Range from 3mm to 30mm in thickness, various lengths and widths depending on application. |
Shapes | Square, triangular, rhomboid, rectangular, round, cylindrical, diamond, etc. |
Standards | ISO, ANSI, DIN, and JIS standards ensure compatibility and quality. |
Coatings | Available with various coatings like TiN, TiAlN, AlCrN, and DLC for enhanced performance. |
Suppliers and Pricing Details of Polished Carbide Inserts
When it comes to purchasing polished carbide inserts, knowing where to buy and understanding the pricing can help you make an informed decision. Here’s a look at some suppliers and pricing details:
Supplier | Description | Pricing (Approx.) |
---|---|---|
Sandvik Coromant | Leading supplier with a wide range of inserts. | $10 – $50 per insert |
Kennametal | Offers high-quality carbide inserts for various applications. | $15 – $60 per insert |
Iscar | Known for innovative designs and high performance. | $20 – $70 per insert |
Sumitomo Electric | Provides reliable and durable inserts for multiple uses. | $12 – $55 per insert |
Seco Tools | Offers a comprehensive range of carbide inserts. | $18 – $65 per insert |
Walter AG | Known for precision and longevity of their products. | $22 – $75 per insert |
Tungaloy | Supplies high-performance inserts for demanding applications. | $14 – $60 per insert |
Mitsubishi Materials | Offers a variety of carbide inserts for different machining needs. | $15 – $65 per insert |
Korloy | Known for cost-effective and durable inserts. | $10 – $50 per insert |
Ceratizit | Provides premium quality carbide inserts. | $20 – $70 per insert |
How to Select the Right Polished Carbide Inserts
Choosing the right polished carbide inserts involves considering various factors to ensure optimal performance for your specific application. Here’s a guide to help you make the right choice:
Factor | Description |
---|---|
Material Being Machined | The type of material (steel, aluminum, titanium, etc.) significantly impacts the choice of insert. |
Machining Operation | Turning, milling, drilling, etc., each requires a specific type of insert. |
Cutting Conditions | Speed, feed rate, and depth of cut should be considered. |
Insert Geometry | The shape and size of the insert should match the application. |
Coating | Coated inserts offer enhanced performance in specific conditions. |
Tool Holder Compatibility | Ensure the insert is compatible with the tool holder being used. |
Cost | Consider the cost-effectiveness relative to the performance and lifespan of the insert. |
Brand and Supplier | Reputable brands and suppliers often offer higher quality and reliability. |
Comparing Advantages and Limitations of Polished Carbide Inserts
Understanding the pros and cons of polished carbide inserts can help you decide if they are the right choice for your needs:
Aspect | Advantages | Limitations |
---|---|---|
Hardness | Extremely hard, allowing for precise cutting and long tool life. | Can be brittle and prone to chipping under improper use. |
Wear Resistance | Superior wear resistance reduces the need for frequent replacements. | Higher initial cost compared to other materials. |
Thermal Stability | Performs well under high temperatures, maintaining hardness and strength. | Requires proper cooling and lubrication to maximize performance. |
Versatility | Suitable for a wide range of materials and applications. | May require specific coatings or treatments for optimal performance in certain conditions. |
Edge Retention | Maintains a sharp edge for longer periods, improving machining efficiency. | Edge can degrade quickly if used improperly or on unsuitable materials. |
Cost | Cost-effective over the long term due to durability and reduced downtime. | Higher upfront cost compared to other tool materials. |
FAQ
Question | Answer |
---|---|
What are polished carbide inserts? | Polished carbide inserts are cutting tools made from tungsten carbide, used in machining operations. |
Why are carbide inserts polished? | Polishing reduces friction, improves surface finish, and increases tool life. |
How do I choose the right carbide insert? | Consider the material, operation type, cutting conditions, insert geometry, and compatibility with your tool holder. |
What are the benefits of using carbide inserts? | High hardness, wear resistance, thermal stability, and long tool life. |
Can carbide inserts be reused? | Yes, they can often be re-sharpened and reused, depending on the wear and damage. |
What materials can carbide inserts machine? | They can machine a wide range of materials, including steel, aluminum, titanium, and more. |
How are carbide inserts made? | They are made by sintering tungsten carbide powder with a metal binder, often cobalt. |
Are there different grades of carbide inserts? | Yes, different grades are available for various applications and materials. |
What is the typical lifespan of a carbide insert? | It varies depending on usage, but they generally last longer than other tool materials due to their durability. |
How should carbide inserts be stored? | Store them in a dry, cool place to prevent rust and corrosion, ideally in their original packaging. |
Conclusion
Polished carbide inserts are indispensable tools in modern machining, offering unmatched hardness, wear resistance, and versatility. Whether you’re in the automotive, aerospace, or medical device industry, these inserts play a crucial role in achieving precision and efficiency. By understanding their types, applications, material properties, and how to select the right one, you can significantly enhance your machining operations. Remember to always consider the specific requirements of your application and consult with reputable suppliers to ensure you get the best performance out of your polished carbide inserts.